Are Spray Foam Contractors Putting Themselves at Risk?
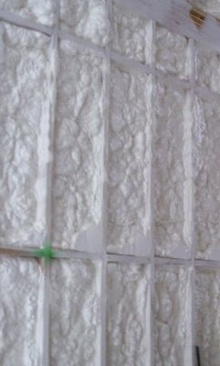
Spray foam insulation is an air barrier. When you use it instead of the fluffy stuff (fiberglass, cellulose, cotton), a house will be more airtight. That’s good.
Spray foam insulation is an air barrier. When you use it instead of the fluffy stuff (fiberglass, cellulose, cotton), a house will be more airtight. That’s good.
When a house is airtight, the nasties in the indoor air tend to stick around. Volatile organic compounds (VOCs), water vapor, odors, radon, and other stuff you don’t want to immerse yourself in make the home’s indoor air quality worse.
How do you solve this problem? Mechanical ventilation. Well, source reduction and separation would come first, but airtight homes need mechanical ventilation.
The role and responsibilities of spray foam contractors
If I were a spray polyurethane foam (SPF) insulation contractor, I’d do like they all do and make sure that every potential client I talked to knew about SPF’s air sealing qualities.
Then I’d do what not nearly enough spray foam contractors do: I’d tell all my clients they need to install a mechanical ventilation system in every new home with spray foam. In fact, I’d include mechanical ventilation as one of the things I sell. (Maybe that’s just because I’d rather be an HVAC contractor, though.)
If a client didn’t want me to do the ventilation, I’d have them sign a liability waiver acknowledging that they understand the importance of mechanical ventilation in airtight homes. Then I’d have that piece of paper so I could pull it out if the homeowner ever came after me for poor indoor air quality.
I’m not the only one saying that ventilation needs to be part of new homes with spray foam insulation. Recently, Mac Sheldon of Demilec emailed me about this issue and wrote, “I’m telling…preaching…admonishing…SPF contractors to never pull the trigger on a spray foam job until there’s a ventilation plan in place.”
I believe spray foam insulation can be an effective product to use in building enclosures. I also know that spray foam can be done poorly. No matter which way it’s done, however, mechanical ventilation is not optional in airtight homes. I wonder how many spray foam contractors will find that out the hard way.
Related Articles
Why Do Airtight Homes Need Mechanical Ventilation?
4 Pitfalls of Spray Foam Insulation
Highlights from Joe Lstiburek’s 2012 Experts’ Session on Spray Foam
This Post Has 10 Comments
Comments are closed.
Great article. I have helped
Great article. I have helped several local companies begin to speak about this over the past couple years. They still are not doing the waiver as I have suggested too.
I would add one more thing to my services and approach if I were a SPF contractor. I would test with the blower door and IR after EVERY install. I just did a test on a new home that were reduced the air leakage by 50% from the touch up we completed. This is when they can get everywhere. Retrofits are more difficult! Just as they aren’t talking about fresh air, removal of old insulation on retrofits, COMBUSTION APPLIANCES in the attic and new thermal envelope, sizing of HVAC issues, etc…they also are not aware they don’t seal the home with every job. That air cannot be seen visually, regardless of what the code says!!
Thanks!!
Another thing to add into the
Another thing to add into the mix as far as polyurethane insulation. I’ not sure if the new is close to the old or not. I have a customer that bought a house with a metal cooregated roof. They sprayed polyu on top as the insulation. They said it takes two years for it to cure and not give off a gas. Where is the gas going? 🙁 most likely in the space. Not good. The roof has large bubbles under the special aluminum reinforced tar sheeting that is on top. the gases and heat caused the sruff to stretch and yes he has leaks.The training i’ve received in the past has taught me that for good breathing air you need (8) complete air changes per day. My sister lives in New Hampshire and they build the house tight for obvious reasons. They also require the energy recovery ventilators in them as a code. 🙂 as for my buddy with the roof issues. Its a large flat roof and has been quoted at 80-100K to replace. Not your normal houae project . Thanks for all your info Allison:
Great Article, I have been
Great Article, I have been involved with training many companies on the cleanliness of the PPE masks,if anyone has some good Power Points, besides OSHA, please inbox me. Thanks.
I certainly understand where
I certainly understand where you are coming from!
Upfront cost is a mitigating factor in the Builder/ Homeowner decision whether or not to use SPF (those who understand Building Science realize the costs are usually recouped in short order). I think many SPF Contractors feel they might lose a job if they require mechanical ventilation or a waiver of liability … the options are either “costly” or “scary”.
There is no question that mechanical ventilation is necessary in a tight building, but I see this as the Builder’s responsibility to relay to the Homeowner … and HIS liability if he chooses to accept the job if the Homeowner declines. This is what he gets paid for.
Any waiver should be between the SPF Contractor and the Builder, acknowledging that the Builder has informed the Homeowner of the perils of non-compliance.
As a matter of course, if I were a SPF Contractor, I would ALWAYS require a waiver of liability when I know that Combustion Appliances are present.
Jamie’s comment that blower door testing should be a requirement is spot-on … even the best applicator misses many spots that compromise both air & thermal barriers and the minimal cost of testing quickly pays for itself.
Thank you, Allison, for encouraging discussion on poignant topics in the field of building science!
As a IECC inspector and hers
As a IECC inspector and hers rater I do a lot of pressure testing in the city of Houston they have required for several years now that house meet a .35 ach I tell all my customers two things if you have a sprayfoam application double check that your hvac contractor has done a correct heatload.. most just do square footage really bad idea no consideration for window Sqft and heatgain
and they need fresh air intake
ashrae 62.2 standard has threshold standards were must induce fresh air and if you do please use a automated control damper
not just a open duct stuck in a wall
city seems to ingnore that some day somebody is going to get sued and it want be mee
I have all customers sign a release
were in it it states that I have notified them of this concern and have been released of all liability as pressure testing service only that was not contracted for code inforcement services
PS if you do a air leakage
PS if you do a air leakage report with Remrate it will give you that warning at bottom and what is need to meet ashrae 62.2 req.
this article useless. Spray
this article useless. Spray foam or any other insulation; understand and use ASHRAE 62.2 to see if the home you are working on requires mechanical ventilation.
this is a battle as an energy
this is a battle as an energy rater that I almost always encounter.
there is a huge disconnect between the spray foam insulator & the hvac contractor.
this is the comment that stood out to me as I am in total agreement:
“PS if you do a air leakage report with Remrate it will give you that warning at bottom and what is need to meet ashrae 62.2 req.”
by Mark Crawford
hvac contactor says ashrae what???
there needs to be communication, accountability and hvac co needs to learn their jobs.
while this may sound harsh..too many hvac companies use rule of thumb sizing instead of hvac load calcs, duct sizing, design & layout. the v in hvac is for venting…duh.
instead of wanting me to do their job..they need to invest in education & learn their jobs!!!
here in the hot humid south oversizing & high RH are all too common. when ashrae standard comes up…they don’t have a clue.
in a perfect world there would be communication between the two companies..but itrw…few companies (foam & hvac) even talk to each other. to hold the bldg contractor accountable..is the same passing the buck because these lines of communication rarely exist.
I’ve been trying for over a decade to get a team together..to establish these discussions. while it works on one or two jobs…it quickly falls apart. maybe it is me???
I sure put a lot of time and effort into it that I make zero dollars on in the time I invest. instead I am the ‘problem child’.
most hvac contractors scratch their heads when ashrae 62.2 is brought up. they don’t know what it is…or crawfish to cya.
I would love a workable performance contractor team. as yet it hasn’t happend, but still I try!
if anyone has a solid way to gather a group, of a team of performance based contractors….please share.
I never cut corners, falsify inputs/reports.
my loyality lies with the homeowner. pride in my work, making a healthy & efficient home for the family who will live in the house…not the builder/insulator/hvac guy that will move on to the next job.
these are my thoughts & ethics…not everyone’s.
thanks for addressing a growing issue Alison..as always..great article.
What? None of you brought up
What? None of you brought up the idea of mandatory moisture control in a spray foam house? In CZ2 we provide a fresh air system and install a dehumidifier as standard equipment in all homes with spray foam.
Thank you, Dave, for bringing
Thank you, Dave, for bringing up moisture control in conjunction with fresh air ventilation. We have seen so many moisture issues in spray foam homes over the last several years. Spray foam does an excellent job of stopping moisture infiltration, as well as exfiltration. Yes, most AC systems do a good job of removing moisture when they are running. But overcooling to control moisture is not the answer. Even in “dehumidification” mode on the newer systems – the HVAC system is cooling to remove humidity. And what about 70 degrees and rainy?