Heat Pumps and Hydronics – A Great Team for High Performance Homes
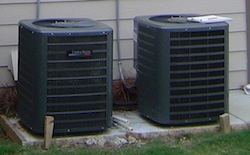
This is the second article of a two-part guest post by David Butler of Optimal Building Systems in Arizona and a frequent commenter in the RESNET BPI group on LinkedIn. I’ve known David for a couple of years now, and I can attest to his expertise in the field of HVAC. When an HVAC question stumps me, I call on David because he’ll most likely know the answer and will explain it in great detail. If you’re a home energy pro, make sure you download and read his paper, The Elephant in the Room.
~~~~~~~~~~~~~~~
In Just Say No to Furnaces, part 1 in this 2-part series, I made the case for why a furnace may not be the best choice for heating a high performance home.
Heat pumps and/or hydronic forced air heat are more appropriate since system capacity can be aligned more closely with the load. This ensures good air mixing at design conditions, an important prerequisite for comfort. Deciding which is best for a given project depends on climate and relative energy costs.
In warm climates with average or better electric rates, the heat pump is hands-down the best heating system. It costs less to operate than a furnace (most markets), and in tight, well insulated homes, a heat pump is actually more comfortable. The lower supply temperature, once considered the bane of heat pumps, is actually preferable in well insulated homes.
Since heat pumps produce less heat as the outdoor temperature drops, supplemental heat is needed in all but the warmest regions. In high a performance home, the need for supplemental heat is dramatically reduced, with a typical balance point (BP) in the mid-twenties. One concept that’s important to understand is that performance doesn’t fall off a cliff below the balance point. At five degrees below the BP, a heat pump will still carry about 75% of the load. If the number of hours below the BP is small, electric supplemental heat is the best option, given its low first-cost.
In moderate to cold climates where a heat pump requires significant supplemental heat, a natural gas-fired hydronic coil is preferable to electric strips. A high-efficiency tankless water heater, such as the Rinnai Ultra, is the ideal heat source for hydronics. The coil, which looks like a radiator, should be sized to handle the full design load. It’s installed between the air handler and the supply plenum (the heat pump coil is on the return side). As with electric strip heat, the hydronic pump is energized when the thermostat senses the heat pump can no longer handle the load.
Most people don’t realize that heat pumps are still relatively efficient at cold temperatures. My 15-SEER Lenox has a COP of 2.8 at 23°F (the BP for my home). But with natural gas prices the lowest it’s been in decades, it’s important to determine the economic balance point for hydronic heat – the temperature where it becomes more economical. Thermostats are available that can lock out the heat pump below a given temperature.
In areas with high electric rates, the economic balance point may be sufficiently high to warrant using straight hydronics. In this case, the air conditioner can be matched with an air handler with a hydronic coil. If there’s no cooling requirement, radiant heat begins to look attractive. Note that baseboard radiators cost much less to install than in-floor tubing, especially in situations where gypcrete is required.
In cold climates without access to natural gas, the choices are more difficult. On a per-btu basis, propane costs about as much as electric resistance heat, and prices tend to be far more volatile. Fuel oil may be more economical, but is decidedly un-green. Ground-source heat pumps may be worth considering in this scenario, but the high initial investment may be better spent on additional insulation. In cold climates without access to natural gas AND high electric rates, you’re up the creek without a paddle. Can you say PassivHaus?
Here’s an interesting fact that surprises many people: Extremely cold climates experience far more hours above than below the BP. For this reason, heat pumps are an excellent choice in markets like Minneapolis, where 75% of the heating hours exceeds 25°F. If you don’t believe me, just check the TMY2 BIN data published by NREL.
When comparing the operating costs for heat pumps vs. hydronics or other types of heat, it’s necessary to estimate how much of the annual load will be carried by the supplemental heat. Unfortunately, annual heat loads are notoriously difficult to model due to the impacts of solar gain and thermal storage. Modeling supplemental heat usage is more dubious. It requires judgment prefaced by a thorough understanding of the numbers. This area is fodder for another article, but one thing I’ll warn you about now: Forget about HSPF when comparing heat pumps with other types of heat. That rating is only marginally useful when comparing one heat pump with another. Rely instead on COP (typically at 47°F), blended with your best estimate of supplemental heat usage.
A final word about heat pumps. The contractor must do the following four things to ensure maximum comfort and economy:
- Locate supply registers so air can be directed away from beds and seating areas.
- Install the air handler and duct system inside the thermal envelope. (I would say this is a prerequisite for calling a house high performance.)
- Provide an override switch for electric supplemental heat (instruct occupants to leave it off until it’s really needed).
- Set the thermostat auto-changeover ‘dead band’ to 8 degrees, or better yet, deactivate that feature in the installer menu (applies to any HVAC system).
Read Part 1:
Just Say No to Furnaces in High Performance Homes
This Post Has 24 Comments
Comments are closed.
David, this is another great
David, this is another great article. Thank you. I think your last two bullet points are really important and the lack of those two steps being done makes many heat pumps much more expensive to operate than they should be.
Unfortunately, I’ve had two people tell me recently that the opposite of step number 3 is happening. When they get a heat pump, the installer tells them to switch to emergency heat whenever it gets down into the mid or low 30s.
Thanks for these last two
Thanks for these last two posts! It puts into perspective when to use either type.
A major key to make either type work is getting the mix of air right in each room. It’s easier to do with a heat pump because the incoming air isn’t overheated to start with. To make heat pumps comfortable, room air mixing is critical. But that’s a Manual D concern . . .
I am in agreement with this
I am in agreement with this article when discussing high efficiency homes. Unfortunately high efficiency homes, I would guess, still only account for less than 1% of all of the homes in the US. So when the leakiness of most homes is considered, other types of comfort conditioning may be more attractive from a comfort perspective.
We also have to be careful in what is determined a “tight” home. Many homes in the south that are considered “tight” would not be considered a code home in Canada. Frequently this has to do with our framing practices in the south. Sometimes the foam insulators do not provide an even coverage of foam so that in the same wall cavity the foam insulation can be as little as 1 inch to as much as 3.5 inches, but the designer based their loads on 3.5 inches.
I don’t disagree with the comment about ground source heat pumps’ upfront costs being an obstacle, therefore the 30% federal tax credit has helped level that playing field.
I don’t agree with the comment about taking the additional money that would be spent on a ground source system and putting it into insulation. An argument can be made that if you built a SIPS home or a structurally insulated concrete home that the additional cost of a ground source heat pump cannot be justified.
From a pure economic standpoint there may be some merit, but that discounts the increased comfort, lower sound, no outdoor unit, and lower carbon footprint that a ground source unit may provide. Not all decisions are based on pure economics.
David,
David,
Thanks for great info! Works great when I get to work with new construction.
How would you designate an existing retrofit as Hi Performance so these principles could be applied?
I especially like the idea of the hydronic forced air with the Rinnai unit. I have one for DHW and it is meeting initial expectations. I am going to check with a HVAC contact in the am to check some pricing.
@anonymous “high
@anonymous “high efficiency homes… account for less than 1% of all homes…”
…and growing. This blog (and my article) is targeted at folks who deal with the “growing” part.
You rightly point out that comfort and safety can’t easily be factored into economic comparisons. Indeed, these types of requirements can sometimes compete with energy efficiency goals. My design approach is to eliminate options that don’t meet comfort, safety and durability requirements, and then consider lifecycle costs.
Regarding ground source, my comment already considers the tax credit. But the notion of investing the difference in insulation was perhaps a bit overstated. I was trying to convey a design approach that seeks optimal use of funds. I would never recommend an insulation budget that even approaches that kind of money 🙂
Thanks for keeping me honest!
@John, appreciate your kind
@John, appreciate your kind words. Actually, it’s not necessary to define high performance to apply these concepts. The comfort issues I described in part 1 result from gross oversizing. If you’re involved in recommending HVAC equipment, you need to become intimate with the various models and capacity match-ups. ACCA and others recommend heating capacity not exceed 50% above the design load.
One nice thing about the heat pump hydronic combo is that it provides a hedge against future energy costs. You can modify the controls to favor one over the other depending on the relative cost of natural gas vs. electricity.
BTW, when specifying a heat pump with electric strips, I have no qualms oversizing 25% above the cooling load (even though Energy Star says 15% for CZ1-4). Whatever is lost in cooling efficiency is more than made up by reducing strip heat. Just gotta make sure the system will handle the latent load.
Great post! It’s on the
Great post! It’s on the opposite end of the spectrum of the post I just published, Basics of Heating your home:
http://blog.mapawatt.com/2011/01/21/basics-of-heating-your-home/
My biggest question, and one I raised on my post “Will an Air Source Heat pump work for you”:
http://blog.mapawatt.com/2010/02/08/heat-pump-will-an-air-source-work-for-you/
..is what defines a moderate climate? Or a cold climate? As I mentioned in my air source post, the DOE talks about these climates, like you do in the above post, but they don’t lay the criteria out to define them.
Could we use start using Climate Zones to define these climates, instead of the less-definitive terms “Hot”, “Warm”, “Cold”.
Great question, Chris. The
Great question, Chris. The truth is, I intentionally avoid defining these terms. There are simply too many variables to use a cookbook-by-CZ approach. For example, I can’t even say that a heat pump is necessarily the best choice in CZ-2. It depends on relative energy and equipment costs. The main point of this series is to try to shake loose the some widely held beliefs and to get folks to look at the numbers.
When it comes to mechanical systems, so much of what’s held up as best practice by the green media is wrongheaded, often encouraged by big marketing budgets rather than careful analysis. For example, I recall an article in Green Builder (Jan 2010) where a builder acknowledged that the $100k mechanical system was a bit pricey, but that it would pay for itself. That’s just BS. The same article claimed that the below-grade ICF walls would increase performance dramatically. Someone apparently didn’t tell him that the earth is an infinite heat sink.
I agree with the problem of
I agree with the problem of oversized furnaces but disagree with the implication that multi stage equipment is unnecessarily expensive. Hybrid heating systems are little more than air source, and offer tremendous output range, the ability to size the heat pump to cooling load, and ability to adjust changeover based upon energy prices. Oversized ac is not addressed, sizing single stage air source to heating generally means oversized cooling even at design temps, and is a big problem.
The goal we will start seeing more and more people talking about is equipment that runs continuously, replacing only the energy lost. This requires output range for varying weather conditions.
I typically recommend equipment with 5stages of heat and 2 cooling. This equipment has the added advantage of being communicating equipment, the benefits of which cannot be effectively touched upon here.
Ted, I agree in theory that
Ted, I agree in theory that fully variable capacity is the ideal in terms of theoretical comfort, but in practical terms, I think we’re arguing about dancing angels.
I’ll readily admit that my focus is on optimized cost-performance. On the other hand, I would never specify a system that cannot meet my client’s expectations in terms of comfort.
While your knowledge is vast
While your knowledge is vast in this subject and the information you pen is would be hard to argue, I find myself wondering why you only touch on the subject of hydronics.
I fully understand the intent of your writing to be a comparison of alternative heat sources in the setting of high performance homes, why only consider forced air as the “chosen” delivery method for comfort?
Maybe the topic of hydronic systems versus forced air is of another thread but, system efficiency and comfort levels can vary greatly when comparing these two types of systems.
I have been installing hydronic systems for years in the far northern reaches of Minnesota with performance and comfort levels unmatched by most forced air systems. Might we expect to hear more about this in future posts?
Eric, from the context of
Eric, from the context of your comment, I believe you’re referring specifically to radiant hydronic systems. I agree, that topic warrants another article. My focus here was on cost-effective alternatives to forced air furnaces (see part 1). If we assume a house will have central AC, the incremental cost of a heat pump or wet coil is small compared to a hydronic radiant system. As I stated in the article, radiant becomes more interesting in homes where AC is not a requirement.
I would be remiss not to mention that radiant systems are more economical to operate than hydronic forced air since the former avoids the blower energy (although ECM motors have greatly reduced the penalty). Whether the savings is enough to offset the first-cost depends on the particulars of the project.
I would argue that radiant slabs offer the greatest comfort advantage in homes that are not so efficient. Homeowners with radiant floors in super efficient homes are sometimes surprised to discover that floors aren’t warm to the touch. After all, “warm floor” is the focus of virtually all radiant floor marketing. I recently worked on an ICF home in central MN that had an average design load of less than 10 btuh/SF, with some rooms less than 3!
What about the cheap economy,
What about the cheap economy, doublewides and modulars, my old neighbor years ago put in a wile-mcclain in a 5×5 room on the back only one single run of three quarter copper. Being a country folk, installed baseboard on ALL outside walls of this small ranch, under door sills I would like to add, hot water coil. Heatcontroler ac unit out front, uses about one tank of 275 gals, at least what he tells me. No formula, alot of baseboard. P.S. Have my own question, live down road from the man I’m talking about, and own a 55′ x 28′ double, because of some dead animals in between black blacked holding original insulation I had to remove. Have Heatcontroller unit also, reinstalled pink insulation. Put silver coat bubble rap insul, around duct work still get ALOT of moisture and drippage. Should I, or could I have the complete under floor joists filled in with spray in and have a duct work encased and the wood frame with cement board attached for skirting. Sorry for no engineering background just my 2cents. Greg
I just installed a large PV
I just installed a large PV array on my home, and of course I have a propane furnace. I’d like to install a dual fuel heat pump / gas furnace to take advantage of the free electricity, but I also have a number of solar water panels and it seems like the heat stored from these panels would be better used to keep the condenser warm so the heat pump is more efficient. The other option is to use the warm water and baseboard radiators for supplemental home heat.
I am currently planning a new
I am currently planning a new home in central Alberta where our climate can be extreme. The envelope will be very efficient. I am leaning toward the use of a dual coil air handler for heating and for a/c if needed. It could also function as a heat pump. Hot water for the heating and domestic use would be supplied by a tankless water heater. Air conditioning could be supplied by the water coil as well if the cost of water is not too high. In this area it normally enters the home at about 40 degrees F. Natural gas is usually inexpensive and electricity is comparably expensive. Heating requirements are estimated at around 30,000 BTU per hour but I will likely grossly oversize the coil as I believe the condensing water heater would be more efficient at larger temperature drops in the circuit. On of the reasons for this method is the ease of adding supplemental heat from sources such as solar or an outdoor wood furnace simply by raising the temperature of the water as it enters the hot water heater. This could be accomplished with a water tank(s) for heat sinks and heat exchangers(probably just coils in the water tank. I would appreciate any comments or ideas.
@Rick, your project sounds
@Rick, your project sounds very interesting. Are you talking about pumping water from your own well or drawing from a municipal water system? Assuming 200 cooling hours annually @ 2.5 gpm, you’re talking 30k gallons. Where I live, that costs about $40.
You mention 40F incoming water. Is it that cold during peak cooling season? You can cool directly with ground water up to about 50F.
But just like an open loop GSHP, you’ll need to discharge in a separate well or pond. Most water requires treatment (you don’t want to pump hard or acidic water through your fan coil), so be sure to check local environmental regs regarding discharge water quality and permitting requirements. Some jurisdictions allow a small amount of chlorine or salt.
You mentioned grossly oversizing your H20 coil. You can manage the return water temperature more effectively by varying the storage temperature, flow rate and airflow.
As for solar thermal tie-in, I’m not sure you’d see a payback unless you do the labor yourself and have access to low cost storage tanks, especially considering the small size of your design load, and the fact that you have access to natural gas.
Let me know if I can be of assistance.
David, thank you for your
David, thank you for your input. It gives me some basis for my calculations. Where I plan on building 30K of water would cost $225. However I expect cooling requirements would be half or less so it still looks attractive compared to installing and maintaining central air. This is municipal water which varies very little in temp because it is delivered through a piping system buried 9 ft. or deeper. We live in a moderately dry climate so the warmed water could often be used for garden or lawn irrigation, essentially lowering the cost to near zero. excess water could simply dumped to the wastewater system. Although I haven’t checked the specific water system it is typical for water in the area to be alkaline (about PH 8) and only moderately hard. Normally there is virtually no scaling except in hot water systems.
I think your comment on on over sizing the heating coil is correct. One of my motives was to reduce airflow and noise. However I am probably biased by exposure to so many over sized hot air systems.
I agree that tie ins of solar or other sources would probably not have a reasonable payback. The reasons for doing it would have to be environmental, conservation of resources or simply to provide a backup source of heat.
It is a little off the subject but I have read an article of yours on HRVs and it has made me question the economies of one even in our climate. I believe mechanical ventilation is a requirement by code in our area for new homes as well as an absolute necessity for humidity control in winter in our super tight houses. Do you know any way to calculate the payback for installing HRV. One problem seems to be that all the units available seem to be vastly over sized for my needs.
Thanks again for your input so far.
Dear David,
Dear David,
I’m a home owner in New Jersey with a recurrent, major problem with my heating system that is driving me nuts. I’m hoping you might be able to shed some light on my problem:
My basic system design is a 4.5 ton heat pump with a hyrdronic heat exchanger, fired by a high efficiency gas boiler. This system was in place when I bought the home, except the I replaced an old cast iron boiler with the high efficiency gas boiler. My heat pump has a stuck reversing valve (A/C works fine), so I have been using the Aux Heat (heat exchanger) as my primary source of heat for these three years. My first winter (3 years ago), the original heat exchanger, mounted in the duct work, ruptured along 2 of the bends in the copper. I assumed the heat exchanger was old and simply wore out. So I replaced it, with a new unit, same size, same btus… and in my second winter, it blew out again.
I assumed it was a faulty exchanger, but the manufacturer guaranteed me it was too much pressure in the line. So, upon replacing it again, my contractor installed a small expansion tank, and a check valve just before the intake of the heat exchanger. Unfortunately, last Friday, the new heat exchanger also blew up. That makes 3 and my contractor can’t think of why this could be happening. I am very frustrated but can’t figure it out either. I have decided to get a new, high efficiency heat pump, and my contractor is suggesting the Aux heat consist of heating strips (electric) instead of the gas fired hydronic heat exchanger…. which I understand are much less efficient. I don’t want to give up on the hot water exchanger as it’s more efficient and they system is already designed that way… but, I don’t want to keep “feeding” it heat exchangers.
The high efficiency boiler also provides heat to several hot water baseboards, an indirect water heater without any problem.
Also, a common thread with each “blow out”, has been that it happens on a mild day, after it has been below freezing at night. This year, it was 29′ at night, and warmed up to near 50′ during the day. I specifically remember this happening on each occurrence, and I’m not sure if it has any bearing on pressure or anything else, just thought I’d mention it.
Any ideas would be greatly appreciated,
Thanks in advance,
Keith White
This is an interesting and
This is an interesting and useful article. In particular, you wrote “But with natural gas prices the lowest it’s been in decades, it’s important to determine the economic balance point for hydronic heat – the temperature where it becomes more economical. Thermostats are available that can lock out the heat pump below a given temperature.” This describes our new Trane system, but how does not calculate the temperature at which the natural gas fired boiler is more economical than the heat pump? Tom
Back in the 80’s I worked as
Back in the 80’s I worked as a designer for a HVAC firm and installed a “dual fuel” air-source heat pump with a LP forced air furnace in a new construction commercial bank building. In the “dual fuel kit” from Trane there was a fairly simple graph that allowed you to plot the economic relationship between the cost of fuels and the temperature that you set the backup furnace to operate. Allison, getting your hands on this graph would probably make for an interesting article and bring some meaningful conclusion to the numerous references to operational economics discussed in the comments above. I think basing the control strategy on the ability of the HP to maintain the requested interior t’sat setting is lame and could cause higher then needed operational costs, especially considering the price of natural gas right now. Also and to answer Tom Cooper’s question, I’ve always wondered from a practical side, who would update these settings over time to accommodate future rate changes. Experience tells us that a high percentage of customers won’t keep up with the manual temperature setting adjustment. Tom, your unit would need to be hooked up to the Web and monitoring fuel market prices to make this adjustment automatic. Tom G
@Tom, great question. The
@Tom, great question. The economic balance point calculation requires that you have energy rate details and the heat pump’s COP data.
First, determine the marginal cost of natural gas. Include all variable costs, but exclude any flat fees that don’t depend on usage. If rate is tiered by volume, use the appropriate marginal rate. Depending on how gas is metered, the rate must be converted to therms (100,000 BTU). For propane, convert the price per gallon to therms by dividing by 0.916. Finally, divide by the seasonal efficiency of the boiler or furnace. For example, if the marginal rate is $0.75/therm and boiler AFUE is 90%, then the cost per therm of heat is $0.83. Add 5 to 10 cents per therm for the blower fan, depending on whether it’s ECM or PSC.
Now take the marginal winter electric rate and multiply by 29.3 to convert to cost per therm. Divide that by the marginal gas cost. That’s the break-even COP for the heat pump. Watch the decimal places. The result should be between 1 and 10.
If you know the heat pump’s COP at 47F and 17F (some mfrs publish this), you can draw a linear COP curve based on the two points. Although that ignores the ‘defrost knee’ at ~35F, it will get you close. For more precision, you can calculate the COP curve from the expanded data table. You just need a couple of points on either side of 35F. COP = BTUH output divided by BTUH input at a given outdoor temperature, so you have to convert watts to BTU’s. Total power is compressor + outdoor & indoor fan watts multiplied by 3.414.
The economic balance point is the temperature at which the heat pump’s COP is equal to the break-even COP, as calculated above.
Given the small incremental cost of a heat pump vs. straight cooling, it may make sense to use a heat pump even if the economic balance point is as high as the 30’s.
Tom G wrote: “Allison,
Tom G wrote: “Allison, getting your hands on this graph would probably make for an interesting article”
If you can locate a copy, please share. I recently removed an old Trane dual fuel kit from a client’s home. The original paperwork was taped to the enclosure, but no graph. BTW, I wrote the article, not Allison.
you wrote:
“I’ve always wondered from a practical side, who would update these settings over time to accommodate future rate changes.”
Well, people like Tom C who are even aware to ask the question. But for inquiring minds, the math is easy once you understand how to do it. What would be helpful would be if manufacturers would publish heat pump COP graphs.
you wrote: “basing the control strategy on the ability of the HP to maintain the requested interior t’sat setting is lame and could cause higher then needed operational costs, especially considering the price of natural gas right now.”
Actually, just the opposite is true if the economic balance point is significantly lower than the thermal balance point, which is usually the case with propane or electric supplemental heat.
But if the economic balance point is above the thermal balance point, I agree that a control strategy based on ODT is the way to go.
David, I am currently having
David, I am currently having a 2K sq/ft home being built in N.Scottsdale. 2×6 walls foam insulation, 2 people & 1 small dog. Any suggestions on my HVAC system?
@Bob, it’s impossible to make
@Bob, it’s impossible to make specific recommendations in a forum like this.
HAVC selection depends on many factors including the design load, room layout, management of peak glazing gains, local utility rates, and last but not least, homeowner preferences & expectations.
Although 3rd party HVAC design is atypical for residential, it makes sense for high performance homes because so few mechanical contractors understand the nuances of designing for better-than-code homes. Plus a 3rd party spec allows homeowner or builder to get competitive apples-to-apples bids on the equipment configuration that’s most appropriate for the home and individual circumstances.