How to Sheathe an Attic Kneewall — And How Not to
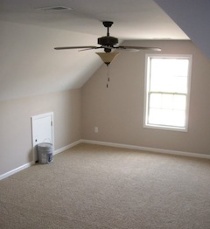
Yesterday I was doing a home energy rating for quality assurance in Augusta, Georgia, and the house I was in had a bonus room. Bonus rooms are often the least comfortable room in a house, and the main reason is that they are the most flawed part of the building envelope, especially the attic kneewalls. In the photo at left, the kneewall is the short wall with the door in it.
The problem with many kneewalls is that they have fiberglass batt insulation with nothing covering them on the attic side, as shown in the photo below. What happens then is that the batts don’t make contact with the air barrier (the drywall), air moves through and around them, and they fall out of the attic kneewall. In other words, they’re pretty much worthless because of poor installation. It doesn’t matter who made the batts.
Georgia recognized this problem about a decade ago and started requiring all attic kneewalls to have sheathing on the attic side and to be insulated to at least R-18. The best way to provide that sheathing is to use a rigid material. I’ve seen OSB (oriented strand board, the flaky plywood), foamboard, and structural or non-structural cardboard sheathing materials like Thermo-ply.
I’ve also seen attic kneewalls sheathed with non-rigid materials, mainly housewrap. The house I was in yesterday had housewrap on the kneewalls, and you can see it above. It’s possible to use housewrap here and do it well. On the left side of that photo, however, notice the opening around the light switch.
On the other side of that bonus room, the kneewall was in much worse shape. It looks like the installers just shoved it in the direction of the kneewall. Notice the batt that has fallen away from the wall in there, too. It’s right above the yellow part of the housewrap. This clearly will lead to extra energy use for heating and cooling and possibly callbacks from the new homeowners who find this room to be the least comfortable place in the house.
I’d prefer to see a rigid material on attic kneewalls. Both can be done poorly, of course, and I’ve seen both done poorly. I think the rigid material will do a better job with air sealing and will stay intact longer. Here are the three keys to sheathing an attic kneewall properly:
- Cover the whole wall.
- Seal all the edges, penetrations, and seams.
- Sheathe the kneewall during framing.
Doing things in the right order is key, no matter what material you use, though. Sheathing the kneewalls should happen during framing, before the electricians, HVAC contractors, and other trades get in there. Then, anyone who cuts a hole in the sheathing is responsible for sealing it. Do that and you avoid the mess you see with the housewrap above and instead end up with something like the kneewall below, which I saw during another HERS rating for quality assurance, this one in Nashville.
Allison Bailes of Atlanta, Georgia, is a speaker, writer, building science consultant, and the founder of Energy Vanguard. He has a PhD in physics and writes the Energy Vanguard Blog. He is also writing a book on building science. You can follow him on Twitter at @EnergyVanguard.
Related Articles
Your Connection to the Blast Furnace – Attic Kneewalls
How to Insulate a Short Attic Kneewall
Does Your Bonus Room Need More Air Conditioning?
Comments are closed.
This Post Has 15 Comments
Comments are closed.
I have always looked at the
I have always looked at the space behinds the knee wall as drawer and closet type storage. LOTS of it. Plan to use the Perma-R behind the other knee wall which will back the storage.
Looks good. In zone 5, we
Looks good. In zone 5, we will run polyiso on the floor as well as any exposed wood that is part of the thermal enclosure.
Out of curiosity, what’s the approach for the sloped ceiling sections above the knee walls?
Another alternative for knee
Another alternative for knee walls conditions is to remove and reinstall the batt insulation to QII standards. Then cover that same area with an R-8 FSK affixing it using cap nails. In tight attics or odd shaped wall conditions (i.e. rake walls), it’s easier to handle than plywood or Thermo-ply and still gives you an R-19 – R121 assembly, depending on the original batt insulation installed.
Allison, is EnergyBrace still
Allison, is EnergyBrace still available?
Also, your link to Thermo-Ply opens the ‘Thermo-Ply Total’ page, which is one of the company’s structural sheathing products. For knee walls, Thermo-Ply Green (non structural) is more appropriate because it costs less and easier to handle. Here’s a better link. Click on Thermo-Ply data sheet from right side menu and look for Thermo-Ply Green.
We also see a lot of trouble
We also see a lot of trouble due to air leakage through the joist cavities beneath the kneewall. These spots should be rigidly sealed as well.
I seen a good bit of home
I seen a good bit of home with kneewall problems in the bonus rooms and livingroom. Because the wall was not seal correctly.
Alison, we call these short
Alison, we call these short attic walls dormers, but the problem is identical here in Australia. I dont normally cover the back of these batts, so I have learnt something from you today.
Several things that I do not
Several things that I do not understand in the posted approaches to treating thee knee-walls!
First, the sealing of the joints of the rigid material or house wrap on the attic side of the knee-wall surface is not NEEDED – if and I strongly state IF, the knee-wall has been throughly air sealed. Air leakage is at the pressure barrier – which is before the thermal barrier.
Second, it should be noted that in cold climate conditions, a vapor retarder should not be applied on the cold side of the installed instulaton. The use of foil faced (even FSK)materials should never be installed after the cavity insulation has been installed.
Third, many side attic (knee-wall) areas are very restrictive in accessiblity and working height. This makes is extremely difficult to install a rigid thermal barrier over the stud framing. I suggest installing horizontally stacked R-19 unfaced fiberglass batt insulation across the back side, anchored to the studs and then covered from roof deck to joist top with house wrap material – this material does NOT have to be air thight! It’s purpose is two fold, one to insure stability of the installed batt and second to lower air movement acorss the batt.
nightwatch
nightwatch: Storage is good, but move the building envelope to the exterior wall and roofline. You don’t want the contents of those drawers to be your R-value.
John Z.: The space behind the kneewalls shown above is unconditioned attic. One approach would be to move the building envelope to that sloped ceiling and exterior wall so that attic space is conditioned. If you don’t do that, you don’t need to do anything about the roofline back there.
Craig L.: That’s a good approach.
David B.: Well, that may explain why I couldn’t find Energy Brace online. Thanks for the better link for Thermo-Ply. I’ll update as soon as I’m done here.
Franklin M.: Absolutely! I addressed that in the article on Bonus Rooms, listed in the Related Articles section.
Franklin O.: I think this is the first time we’ve had two Franklins commenting in the same article! And yes, kneewalls present all kinds of problems.
Marcus T.: Glad to be of service!
Keith W.: (i) What if the drywall is perfectly sealed but attic air comes in the bottom of a kneewall and exits through the top plate (if there is one)? (ii) Thanks for bringing up the topic of vapor retarders and climate zones. Yes, in a cold climate with a vapor retarder on the inside, you definitely don’t want another one on the outside. (iii) I’ve spent my time working in those small spaces behind kneewalls, so I know how difficult it can be. I still don’t like housewrap for that application, though.
Glad to see a nuts and bolts
Glad to see a nuts and bolts Building Science article again! Haven’t read the blog in a while, with all the Metric System, Daylight Savings, ACI and RESNET posts lately. Thanks.
As a follow-up to my previous
As a follow-up to my previous comment, I verified that EnergyBrace is no longer available. The factory that produced it was purchased by Thermo-Ply maker Berry Plastics. Since the two products were essentially the same, the EnergyBrace name went away.
I just found out that Thermo-Ply maker Berry Plastics recently sold its building products line to Ox Paper Tube. Since this just happened 4 weeks ago, Ox Paper does not yet have a web page up for Thermo-Ply.
Hi Allison,
Hi Allison,
I’m a new guy at a fiberglass insulation contractor just up the road from you in Chattanooga. I’ve found your blog to be a great source of background knowledge to help me understand the weatherization industry and overall building performance – so thanks for creating a great resource.
I need to offer an alternative perspective regarding your closing comments about sheathing the knee walls during framing and ensuring that the other sub-trades seal over the penetrations they create. In our experience the other trades cannot, and perhaps should not, be trusted to have a sufficient understanding of insulation (or the equipment/materials) to “cover their tracks,” so to speak, nor can we always expect the builder to enforce such a guideline. And I’m not faulting anybody for that — in their eyes, we’re the insulation guys, so it’s our job to worry about that stuff. In fact, on the occasions where we insulate a home and then another trade comes back to fix something up they may have missed and happens to disturb our work in the process, we get blamed for it and are called in to fix it. We realize the injustice of that scenario, but it’s the reality we face, and arguing about it loses us customers.
So we typically insist on being the last trade to touch an unconditioned area. That way we can make absolutely sure that our installation is top-notch and is least likely to be disrupted by other trades. While our job would be much easier if we didn’t have to work around pipes and wires (and bears – oh my), our builders and homeowners get the best results from us when we come in last and trim the insulation to fit around all those things, and seal around all those penetrations.
Perhaps as building performance guidelines become tougher, more GCs and sub trades will pick up some of that knowledge, but until then, our customers’ homes, the quality of our work, and our reputation are best served by our being the last trade to touch knee walls.
Nathan S:
Nathan S: You make a good point. I think that if you can get your builders to let you be the last one in all the time, that’s great. It would prevent things like what I found recently in Nashville: The Cable Guy Did It! — Attic Insulation Gone Awry.
I think you may have misunderstood my recommendation, though. I said the attic-side sheathing should be done during framing, not the insulation. It would help to get the kneewall completely covered when it’s most accessible. The insulation would still happen later.
Thanks for comment, and I look forward to more comments in the future. We can never have too many educated, conscientious insulation contractors!
Allison, I just noticed this
Allison, I just noticed this entry from just before we met.
We deal with knee walls in 1930s-1950s all the time, 2-3/month at least.
I disagree with you (albeit not that strongly, no Fight Club here) that a really solid air seal is necessary over the stud cavities in knee walls. The only air leakage in the stud cavities is typically the outlets, light switches, and access panels.
Most of the air leakage we tackle is below the sole plate above the floor and in the floor joists directly below the knee wall. We are VERY thorough air sealing these areas with excellent results.
A job we finished last week dropped from 4060 to 2150 cfm50 just with knee wall air sealing (we were able to get 8′ of one wall that had no top plate). 1000-2000 cfm50 reductions are fairly common with this method.
Despite all the bad publicity reflective insulation is getting lately, I like to use it quite a bit on knee walls. We use a perforated variety to avoid the double vapor barrier. We like it because the 4′ rolls that fit most older knee walls are easy to drag in and install. It’s even made by your favorite company, Guardian!
Since it encapsulates the fiberglass batts we often find (or install) it allows them to perform at their full R-value, plus it adds 2-4 (admittedly questionable) to the R-value. Also, of pretty big importance in hot days like we have been having, it reflects a big portion of the heat in the attic back into the attic.
In a bit of heresy, we don’t worry too much about taping the seams or caulking/foaming it on, just staples. The customer feedback has been tremendous, and I’ve been shocked at the transformation on the jobs I’ve been on.
So that’s what I think, what is your take?
I live in Peachtree City, GA
I live in Peachtree City, GA and have a house with 9 of these knee wall areas I need to properly insulate. Of 4 companies I called I finally got a quote andwhat they propose is to install vent baffles on underside of roof OSB and then FG Batt insulation. The house was built in 2001 and now only has batt insulation on backside of drywall of knee walls which is slumping and was poorly installed. What is best solution for this situation? Should a perforated radiant barrier be placed over existing batting or should I proceed with attempting to insulate whole space by insulating underside of roof? Thank you for your great website.