I Use an Air Conditioner Sizing Rule of Thumb!
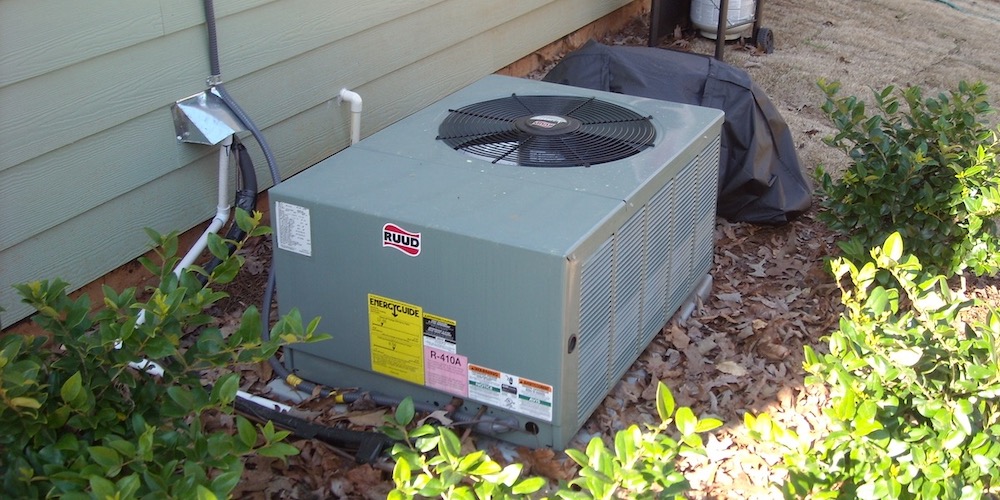
As the Quality Assurance Designee for our HERS rating providership, I do something that isn’t healthful. I know it’s probably driving up my blood pressure and taking years off my life. But I do it because I have to. It’s part of a QAD’s job.
What is it, you ask? I check a lot of Manual J cooling load reports.
It’s already caused my head to explode twice this year, once when I wrote, Why Won’t the HVAC Industry Do Things Right? Then a couple of months ago, what was perhaps the worst Manual J report I’ve ever checked sent me over the edge and Oversized AC, Screwed-up Manual J, ENERGY STAR HVAC Tirade! popped out. Yeah, this has been an ‘issue.’
The reason is that any builder who wants to get their home qualified for the ENERGY STAR label is required to size their air conditioning systems using the results of a cooling load calculation. The rule is that the air conditioner has to be no larger than 115% of the Manual J cooling load. It could be more than that if that number falls between sizes, but you get the idea.
ENERGY STAR Version 2 doesn’t require much in the way of checking Manual J reports, but I go above and beyond when I look at them. One of the first things I do is to apply my rule of thumb. Understand here that the standard practice among HVAC contractors sizing air conditioners for new homes is to use a rule of thumb. It’s often in the neighborhood of 1 ton of air conditioning capacity for each 600 square feet of conditioned floor area, usually abbreviated 600 sf/ton.
So, when I get a Manual J, I find the capacity and the conditioned floor area and calculate that number. I find out what the square feet per ton is for the house. If this is supposed to be an ENERGY STAR home, it shouldn’t be 600 sf/ton. It should be more like 1000 sf/ton or higher. That’s my rule of thumb.
Every time I look at a Manual J report that comes in at around 600 sf/ton, I know that all I have to do is look further into the details, and I can find mistakes that led to their oversizing. Some common ones are:
- Too much window area
- Wrong window types (U-value and Solar Heat Gain Coefficients too high)
- Wrong orientation
- Too many people
- Ducts too leaky or in wrong location
HVAC contractors doing their own load calculations are afraid to come out with a cooling load that’s too low. They’re afraid of call-backs from clients who can’t keep their homes cool. They’re also used to having to oversize cooling systems to overcome the problems of weak building envelopes and crappy duct systems.
If they want to do ENERGY STAR new homes, though, and their Manual J reports are coming to me, they should know that I’ve got my own rule of thumb – 1000 square feet per ton. When that 2000 square foot house comes to me with a 3 ton air conditioner, I have no choice but to look further because they didn’t pass my rule-of-thumb test.
As I said, checking Manual J reports is stressful, but somehow I cope. A few years ago I saw an interesting billboard for a liquor store in a semi-rural Georgia county (actually, the county I used to live in and where I built a high performance home). It said, “If you don’t drink, don’t start. If you do drink, buy your booze at Alcohol Alley.” I was going to try to extend the metaphor to checking Manual J reports, but it’s not worth it. I think I’m just gonna go have a drink.
Allison A. Bailes III, PhD is a speaker, writer, building science consultant, and the founder of Energy Vanguard in Decatur, Georgia. He has a doctorate in physics and writes the Energy Vanguard Blog. He also has a book on building science coming out in the summer of 2022. You can follow him on Twitter at @EnergyVanguard.
Related Articles
How to Cheat on a Manual J Load Calculation
Air Conditioner Sizing Rules of Thumb Must Die
How to Read Manual J Load Calculation Reports
Comments are closed.
This Post Has 17 Comments
Comments are closed.
so true,Allison … around
so true,Allison … around here (Hilton Head, SC), we’re more apt to see a RoT of 450 sq’/ton … I wonder why mold is such a problem here?
Have a customer this past
Have a customer this past week playing with the idea of going for Energy Star. She came to us with a 4000 s.f. super insulated house with great windows. She was concerned that the HVAC contractor was telling her she need 8 1/2 tons to condition the house. When I explained that this was probably excessive and we should request the Manual J she went back to him. He said he would reduce it to 6 1/2 tons but did not want to produce the Manual J. She decided to go for Energy Star and Earthcraft certification just to get him to produce the Manual J. He told her that there is no reason why anyone other than an HVAC contractor should be looking at Manual J’s. Complete insanity. Awaiting his submission with baited breath…..
As much as we (I) rant and
As much as we (I) rant and rave about HVAC contractors and Manual Js, we should equally demand of builders to tighten the envelope. Most Manual Js are done badly by ignorance, but a good chunk is to “counter” building envelope deficiencies. Maybe some day all trades will do their job like it’s supposed to, so contractors can trust each other in their work quality and performance.
Paul: Yep,
Paul: Yep, at 600 sf/ton here in the Atlanta area, we’re at the high end of the range that contractors use. Although I didn’t state it in the article, you alluded to the reason that oversizing is bad – Oversized ACs have short runtimes and don’t dehumidify well.
Elizabeth: I wish I could be properly shocked and horrified by your story because it certainly deserves it. Sadly, it’s pretty much the norm.
Armando: Absolutely! I think building envelopes have improved a lot in the past few decades, and duct systems are the real problem. Of course, there are houses that have huge holes in them as well as poorly installed insulation, and we need to push for improving the whole package. The house is a system.
Lol! I just discovered where
Lol! I just discovered where and when my drinking habit started. It was those pesky mechanical engineers who kept over-sizing and debating me.
We had our first call back on a 1000 sq ft per ton home last week. The living room was hot. When we got there we found that some plumbers had some fun in the attic and smashed up 60% of the duct runs.
Of course some other AC contractors were all set to add in some duct runs and vents.
LOL! We have a decade(s) or more of incompetence to continue to look forward to. I dont really drink but its fun to pretend.
Christopher
Christopher: I think callbacks on right-sized air conditioners will be the result of duct problems most of the time. And that problem’s not insignificant because there’s been a lot of emphasis on right-sizing but not nearly enough on good duct design.
What really sux is when the
What really sux is when the builder gets everything right except for the HVAC. I’ve seen some really egregious oversizing on high performance homes. This can lead to serious comfort and moisture issues.
David B.:
David B.: Unfortunately, getting builders to put right-sized systems on good ducts has been a lot harder than getting them to insulate and air-seal better.
I’m a spray foam guy so you
I’m a spray foam guy so you might ask why I’m commenting on the HVAC stuff. I spent about 20 years in the HVAC industry before the spray foam business and know the pitfalls pretty well. Sadly, I spent much of my HVAC career doing Manual J calcs by hand and over a 15-year period in residential work did about 4000 either by hand or with the software that emerged in the 90’s. I agree with your rule of thumb and like you, found it useful as a “range-finder” before narrowing in on the details.
Two things came to mind while perusing your article; air distribution and insulation “sizing.” As we properly (down) size our HAC systems we need to remember the “V” part of the acronym and we need to be sure we get adequate distribution and rotation of air into the farthest reaches of the structure. This is where good duct sizing is essential but is rarely employed. We also need to use the right materials, and unless you have two linebackers pulling flex duct straight, that product is not appropriate except as a sound absorption measure for no more than 6 ft at the end of the duct run. Very well sealed and insulated ducts located inside the conditioned enclosure are essential…..yes, we still need to be meticulous about air sealing ducts even inside the pressure envelope.
The second item elicited by your article is properly “sized” insulation. When we do our equipment selection, we base the performance on the ASHRAE 2-1/2% Design Temp for cooling and the 1% Winter Design temps yet we continue to use insulation that is “sized” for 75 degree mean temperature. Why are we not asking about the performance of our insulation at the same design temperatures we require of our HVAC equipment? For instance, we now know that some fibrous insulation loses nearly half of its insulating value at 0 degrees F, yet we continue to spec and use it! Anyway, I ask the question rhetorically because right now we have rules and codes to follow that don’t require (or even allow) us to think, but I’m ever hopeful that this will change sometime soon as we introduce code change proposals to the International Code Council. For now, I challenge all the thoughtful people reading your Blog – don’t forget the “V” and think about the efficacy of your insulation package if you have extreme temperatures.
This business about
This business about insulation losing its value due to being cold… I do not think that is generally known. Please consider telling us more about this.
Mark, here’s a
Mark, here’s a report that discusses this effect. It has to do with convective currents that set up in loose-fill fiberglass ceiling insulation as attic temperatures drop below freezing. In homes that have been air sealed, this should not be an issue in wall enclosures since they’re encapsulated on all six sides.
The main take-away for me was that these convective losses don’t kick it until attic-house delta-t exceeds about 38F (corresponds to attic temp of 32F in this study).
Although the negative impact of convection in loose-fill fiberglass can be significant at extreme (cold) temperatures, the seasonal impact in moderate climate zones is probably negligible.
Interestingly, the measured R-value for loose fill fiberglass in this study, especially @ R38, actually *increases* as temperatures drop, until convection currents set up. The chart at PDF page 31 is worth taking a look at.
Mac S.:
Mac S.: Great points about HVAC and insulation.
Mark J.: That’s something I’m in the process of learning more about myself, so expect to see something on that topic here in the blog.
David B.: Thanks for that reference. I hadn’t seen that one.
It’s not a matter of distrust
It’s not a matter of distrust towards HVAC contractor, but simply a given when in new construction there is a disconnect between what the GC intended and what HVAC implemented. For a good end-product, the two better sit down together when producing a manual J report, as well as at least manual D. Prior to breaking ground on the project.
good blog
good blog
There’s even a greater
There’s even a greater disconnect between the architect/designer and the HVAC contractor. The architect will usually draw a rectangle and a circle side-by-side and label them “Furn” and “WH” and that’s as far as he’s thought about arguably the most important systems in the house. They exacerbate the problem by spec’ing joist hangers on beams so ducts can’t pass above them, and are often loathe to allow soffits in their 10′ ceilings. Sad but true.
Work with your architects and help them to understand that even the most beautiful home will be disdained by the homeowner if it is not comfortable. The Taj Mahal is one of the most beautiful buildings on the planet yet it has no windows, doors, HVAC or insulation. Would you want to live there? ….OK it’s a mausoleum so of course you wouldn’t but you get the point….. Comfort and Building Performance must be designed in and built in, they can’t be effectively added on.
Ah yes…………Builders,
Ah yes…………Builders, GC’s and architects Oh MY!
I am but a lowly HVAC contractor with no fancy letters behind my name. I find however that as far as understanding the building as a dynamic system which must function in widely varying conditions, it seems as though the many of the “lettered” people don’t grasp that concept.
I cannot begin to enumerate the number of times I have been on a jobsite and made a suggestion to the builder or architect about the location of a duct or the equipment itself. It seems that function of the HVAC system and performance of the home take a back seat to aesthetic value. Little thought is given to it beyond the “look” of things.
Then they wonder and bitch about duct noise, moisture problems, condensation in walls, (one builder suggested using an exterior wall cavity as a return air duct)astronomical operation costs. ….I am about to throw in the towel unless I can work directly with a homeowner who will listen. Otherwise please spare me the grief.
Oh and BTW, HVAC ducts and equipment belong in the conditioned space. Not in an uninsulated attic or a damp, moldy and slimy crawlspace. Duct sealing and insulating can only do so much before the laws of physics take over and make a mess of your carefully thought out plan.
Paul S.:
Paul S.: Absolutely! If builders would sit down with the architect/designer, plumber, HVAC contractor, framers, and electricians before work began, the end product would be much better.
Jim: Thanks!
Mac S.: Yep, most architects have no idea how to make a complete HVAC system fit into a house. They don’t give the air handlers enough space. They don’t give the ducts enough room to turn properly. They put the systems in places where they shouldn’t go. That’s where we can help. We design homes and HVAC systems and know how to put it all together.
Steve E.: I’m with you 100%, even though I am one of the ‘lettered people.’ If you’re new to our blog, take a look at some of the other articles we’ve written, and you’ll see that we also moan and wail over those same issues you raised.