Should Flex Duct Be Banned by Green Building Programs?
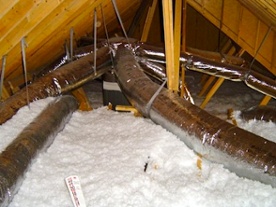
It started on Twitter the other day. I posted the photo you see to the left, and a discussion on flex duct ensued. One person, who’s been known for taking strong stances now and then, saw it and said, “Flex isn’t allowed in any of the green building programs (that are worth a damn that is).”
It started on Twitter the other day. I posted the photo you see to the left, and a discussion on flex duct ensued. One person, who’s been known for taking strong stances now and then, saw it and said, “Flex isn’t allowed in any of the green building programs (that are worth a damn that is).”
His reasons are solid for thinking flex should never be used. Here are some of the things he tweeted: “…easy to damage, easy to fail, and impossible to clean. Also less efficient.” In another tweet, he wrote, “Rodents chew through flex, cable guy kicks it, tape falls apart…”
I’ve posted plenty of photos of bad flex duct installations in this space, and have seen all the problems he mentions and more. Remember Stumpy, the flex duct amputee? This photo (right) has become so popular that it’s showing up in other people’s presentations (with no attribution, of course. Grrrrrrr…).
Flex duct is almost never installed correctly. I’ve been in thousands of houses, both new construction and older homes, and I’ve seen a lot of flex duct. Mostly the installation is pretty bad. In new ENERGY STAR homes or EarthCraft Houses, it’s usually better, but I don’t think I’ve ever seen one that made me step back and say, ‘Now that’s how you install flex duct.’
The most common problems I see with flex are:
- Kinks and sharp turns
- Duct runs that are long and not supported well
- Radial systems (the ‘ductopus’) with too many ducts coming off the plenum and the takeoffs too close together (top photo)
- Extra duct length that should have been cut off (below left)
- Poorly fastened and sealed connections
So, yeah, flex duct has a lot of problems. Should it be banned from green building programs? And which programs allow it? Well, ENERGY STAR (which isn’t a green building program but ducts are well within its purview) allows flex. LEED for Homes allows flex. The NAHB Green Building Standard allows flex. Hmmmmm. I think there might be a program in Minnesota that doesn’t allow it, but I don’t know of any others. (Readers, please let me know of any programs you’re aware of that ban flex duct.)
Well, if we’re not going to use flex, what’s left? There’s duct board, rigid fiberglass with a foil facing, but, in my opinion, that’s worse than flex. If any duct product should be banned, it’s duct board.
That leaves rigid sheet metal, often called hard pipe. I agree absolutely that hard pipe is the best duct to install. Here’s why:
- It must be designed. The installer can’t just show up and throw it in.
- The resistance to air flow is much lower.
- Most of the problems in my list above are irrelevant.
But hard pipe is not without problems. Some of the leakiest ducts I’ve tested have been made of sheet metal, not flex. The photo you see at the right is one that I tested and sealed about six years ago, and it turns out that it was being held together mainly by the duct insulation! When I pulled the insulation off the branch you see here, it collapsed.
Although I’ve been accused of wanting to take away your freedom of choice (because of my articles last week on can lights and McMansions), I do not think that flex duct needs to be banned. I’d just like to see it designed and installed properly. Its best use is for relatively short runs in a trunk-and-branch system, not entire air distribution systems.
The problem here is not the product; it’s the process. It’s also part of the larger issue of the HVAC industry underperforming, to put it nicely. Flex duct, I believe, can have a place in high performance homes. We just need tighter quality control.
This Post Has 30 Comments
Comments are closed.
It all comes back to
It all comes back to following the manufacturers spec. Truely when will the Manufacturers step up and require certifications to actually be allowed and install their products. Heck even Hardi Board at least has a certification class for installation of their product, along with a some others. But the most important machine in your home today and it just goes ignored and uncertified, shame on the industry. THere is a fix though.
You were quick to dismiss
You were quick to dismiss fiberglass duct board. I think it’s the most energy efficient, hermetically sealed acoustic product in the market. With veil there is no glass errosion. I have it in my McMansion and could not be happier. I am so happy my builder specified it.
Buddy:
Buddy: That’s exactly what I’m saying. More education can solve the problem.
Dave: Yes, I was quick to dismiss duct board. If you got a good installation, consider yourself lucky. And keep checking on it because it’ll probably be falling apart before too long.
On the duct board, in my
On the duct board, in my experience as well as falling appart at the seams it does tend to hold more moisture and in many case mildew can grow very easily. Metal and Tight and right Flex works. You just need to know what you are doing.
Here is the problem we run
Here is the problem we run into- cost. Most people just can’t scrape together the extra pennies. Maybe it comes back to a deficiency of our sales guys to up-sell the value of the higher performing systems, but in most cases, no one wants to pay.
Lance: Yes
Lance: Yes, cost is an issue, but the up-front cost is only one part of that. The key is making the case that the operating costs of a bad duct installation can be much higher than the installation costs. When you put a 50% efficient duct system on high efficiency equipment, you’re not getting what you’re paying for.
But going back to my main point, I’m not arguing that flex needs to be banned. I’m saying that it’s OK when designed and installed properly. What should be banned, however, is crappy installation. If all installers would simply follow the manufacturers’ instructions, we’d have much better and more efficient duct systems.
Amen to that one Brother!
Amen to that one Brother!
I agree with everything you
I agree with everything you mentioned about proper installation. Almost any good product in the HVAC industry could be bashed due to improperly installing them. The more houses I inspect the longer my list grows! Your spot on when it comes to selling the importance of using properly trained installers and upgraded materials. I’m not a big fan of flex and thankfully we don’t rely on it but it does have its uses, just not in my projects.
Isaac: I’m
Isaac: I’m with you. If I were building or remodeling houses, I wouldn’t use much flex. As I said above, I believe that it can be done well, but it’s just better to use hard pipe.
When I get the chance to build myself another house, though, my aim is to have no ducts at all! I want to go with ductless heat pumps.
So what I don’t get is if we
So what I don’t get is if we all agree that flex sucks regardless of how well it is installed, why would we keep it around? Yes, Rigid can be installed poorly, but when it is installed properly it performs better than any of the duct alternatives.
Much of the problem stems from inadequate training for HVAC installers combined with hyper lax requirements in residential construction (thank you NAHB). An installer who spends most of their time in the commercial world doesn’t think twice about Manual D, and mastic is standard operating procedure. (there is no cost argument here)
As for foam-board.. A duct system that relies on tape is about is intelligent as a skylight that relies on caulk.
Michael:
Michael: That’s not what I said. (But now that you mention it, I hope that every duct sucks–when it’s on the return side ;~) ) If it’s designed and installed properly, flex can work just fine: Pull it tight. Keep the runs short. No butt joints. Rigid elbows. Good mechanical fasteners. Mastic. Then measure the static pressures and air flow.
Ok Chris you better patten
Ok Chris you better patten that idea.
Again I have no problem with Flex duct use. Being a builder for over quarter century, I started using flex in the late 80’s, I have to admit it was run much better back then also. Another part of the major problem with flex was the building boom of the 90’s and early 2000 era that along with the unskilled workers where anyone that would show up to work with a utility knife and duct tape would become a duct master installer and eat burritos for lunch.Do not discuss anything with them as they ate their burritos because we all spoke a different language.
Shame on us during the Boom, and shame on the industry. Shame on the Home Builders Association for not getting board with the energy codes and supporting the national builders the way they do. But this does not in my opinion put a bad name on the fles product other than they should have done a better job to teach and demostrat proper installation early on with both installers and inspectors and the builders who promoted it.
Flex ducting for bath-fans
Flex ducting for bath-fans makes sense. But given that ductwork belongs inside the thermal envelope, the ‘ease of installation’ argument makes no sense. Hanging flex lines in the basement is an invitation for rips and punctures. running flex through wall cavities is more work and gauranteed to be damaged by drywall installation. And at the end of the day, it is impossible to clean (which should be an annual procedure).
Chris- Metal is hard to work with for the inexperienced, which in my opinion is exactly why homeowners should not be isntalling their own ductwork. Also, tape is not ever a solution. Mastic is the only method that should be used in sealing ductwork and it is quite effective. (Since you asked, there is a company that makes a gasketed ducting system that works quite well. A neoprene gasket at the ends of the duct components makes for a tight seal, and their locking system keeps the lengths of duct secured. It is still a good idea to go over it with mastic however)
“The problem here is not
“The problem here is not the product, it’s the process.” Right on. I’m from the commercial building industry and have seen plenty of examples of terribly performing, award winning green buildings. Awards were handed out because of the stuff they spec’d, not based on actual performance. As an industry we should be focusing our efforts on the bulls eye goal of energy performance. With prescriptive standards actual performance is only implied at best.
I say the high performance
I say the high performance building industry needs to focus on performance rather than products. Test the static pressure, airflow at the coil and room balance. If the system gets the right amount of air to the rooms with minimal leakage, then I don’t give a rat’s ass how they accomplished it. Programs that require Manual D submission are missing the point. Anyone can create a drawing.
Thanks for the great post and
Thanks for the great post and overview of flex duct. I would agree with what is stated in the article, and having seen 500-1,000 duct systems on the West Coast, from 1930’s-2010’s installations, have found the worst of conditions for flex duct and hard metal ducts alike. Quality is key, and there are MANY more of these amputee ducts floating around crawlspaces and attics throughout California, I can attest. However, there are about 200-300 fewer wasteful homes now thanks to our audits/retrofits over the past 5-6 years!
When the total energy use of ten houses after typical retrofit equals the energy use of one wasteful house before retrofit, we have eliminated serious waste and deficiency!
And by the way, getting flex
And by the way, getting flex right adds cost. Contractors will discover they may be able to install metal for less than flex, to achieve the airflow targets. Or at least the difference is much less.
Chris:
Chris: Good points. One of the advantages of flex is that there are few places to seal because, unless the liner gets punctured, the only place flex can leak is at the connections. With hard pipe, you have to seal a lot more connections, the gores in the elbows, and the longitudinal seams.
David: Thanks for raising the point that flex isn’t necessarily cheaper when it’s installed properly.
On the duct board comment,
On the duct board comment, home was built in 1988, I invested in an energy audit last year, did a duct blaster test and it passed with flying colors. I agree that it is all about the proper installation and using the right materials.
The smaller the cooling load
The smaller the cooling load per square foot, the more challenging air distribution becomes. Although there’s less air to distribute in a high performance home, the distances *relative to flow rate* become much greater, especially in a ranch style home.
I’m working on a one-story ‘passive house’ project that will a have ducted mini-split. The problem is that ducted mini-split blowers have very little available static (0.20 IWC is the highest I was able to find). The grilles and filter take up at least half of that, so every foot of ‘equivalent length’ is precious. Flex, even when installed perfectly, simply has too much friction loss. It won’t work.
Interestingly, the Passive House consultant specified a ductless mini-split with one wall unit, and assumed the HRV would circulate the air. However the HRV flow rates per room are simply too small to achive proper balance at peak loads, even as small as they are. This home would require five wall units, which isn’t possible with a one ton compressor.
Amen to what David Butler
Amen to what David Butler said in his first reply.
When will we start to put the focus on verification of the HVAC design instead of only focusing on the design process or material used as a cure all?
I’ve installed a lot of flex duct systems and all metal systems that actually did what they were designed to do. We measured and balanced what we designed and verified its performance instead of assuming the design worked.
The choice of duct materials boils down to a lot of factors with personal preference usually being at the top of the list.
If anything needs to be banned in our industry it’s assumptions.
I just had all the metal
I just had all the metal ducts in my clients 1974 home removed and the entire duct system replaced with flex duct. The original system was gross and leaked more than 25% to the exterior. It would have cost more to clean it, seal it, and properly insulate it, then it would have cost to replace the whole thing.
It has a single unit that services 2 floors and the 14″ return and supply ducts are run upstairs from the crawl space through the exterior chimney chase (with all the returns uninsulated of course).
My HVAC contractor stripped every thing to the plenums, cleaned the plenums, masticed every collar inside and out, used metal fittings at every joint, masticed those before even attaching the inner liner, then attached with zip ties and more mastic. All the ducts are properly hung without kinks and and no weird angles to cut air flow. You can’t even hear the system come on anymore its so quite. I haven’t rerun the duct blaster test yet but I am sure its below current Energy Star specs.
I personally have no problem with flex duct as long as it is installed properly. Without proper installation it doesn’t matter what you use.
Chris – My guys used all
Chris – My guys used all metal fittings on the Y’s. They pre-sealed all the seams before they even took them in the house. It made it a whole lot easier.
That’s funny, unless MN GS
That’s funny, unless MN GS changed the reqs the copy I have states “5C – HVAC DISTRIBUTION STRATEGIES – 5C-PR1_ All new flex duct pulled tight (no pinches)
Requirements: Any flexible ducting must have smooth, even lines, angles must not exceed 90 degrees (no “U” shapes) and must minimize duct runs. There must be no pinching or bunching (extra material), or areas where the airflow is restricted.”
Personally, I like metal ducting, with the last 3 – 5′ section flexible to help cut down on noise
Given all the aforementioned,
Given all the aforementioned, then it would seem only logical to go with oversized HVR’s, inverter mini-splits and forget about the HVAC malaise.
> …it would seem
> …it would seem only logical to go with oversized HVR’s, inverter mini-splits and forget about the HVAC malaise.
I’ve heard this before. Sounds nice in theory, but you still have to distribute the correct cooling airflow to each room. Hard to get around that reality. Ducts are ducts.
Moreover, HVR’s (and EVR’s) are *very* inefficient as blowers, mostly due to high resistance of heat exchanger core. Also an oversized recovery ventilator adds to the load since it can’t recover 100% of the heat.
In the project referenced in my previous post, the Passive House specs called for a wall-mounted mini-split along with an oversized ERV to circulate the air. The ASHRAE 62.2 target for this home is 68 CFM. The ERV is capable of 200 CFM on high, but even with high efficiency ECM motor, it consumes 275 watts (0.7 cfm/watt), and that assumes ducts are properly designed and installed. OTOH, the Lennox ECM blower in my home produces better than 7 cfm per watt (10x better).
The metal duct in my 1950s
The metal duct in my 1950s California ranch house is still in good shape. I just had to add insulation and put mastic on the seams. Insulating the Wyes and Ts was tricky and took forever. I’m adding a second AC system for the other half of the house, and one reason for using flex for the short branches is so that it can hang above in some places. Running it along the attic floor would block access – it’s already hard enough to crawl around in there. The main branch will definitely be metal. My experience with contractors in general is that they want to finish the job fast to make the most money. That’s why I prefer to do my own home projects whenever possible. I can’t believe the corner cutting mickey mouse things contractors have done when I’m not looking. I think there is some benefit to using flex duct for difficult-to-access areas, but combining flex duct with typical residential contractors is asking for a hack job. I bet most contractors think the homeowner will never even look in the attic.
Flexible duct can be a great
Flexible duct can be a great alternative to traditional metal ducts in the rite situation. In the past I have installed insulated and uninsulated duct in a variety of applications including residential and commercial buildings. There are times when I have found it to be appropriate and others where I used a more traditional method of placing insulation sleeves over metal duct or using duct board.
I don’t feel that you can blame a product for poor installations. The overall responsibility lies on the installing contractor and the quality of work that they provide.
We use a product called
We use a product called FlexRight to shape flex ducts into 90 degree long radius bends – they’re inexpensive and one size fits all – you can see them at http://www.flexright.net
I have metal ducts and they
I have metal ducts and they are moist and causing bubbling of paint at vents. I can’t find someone to redo the insulation. Everyone just wants to rip them out. I want to keep them. Any suggestions?