Why Won’t the HVAC Industry Do Things Right?
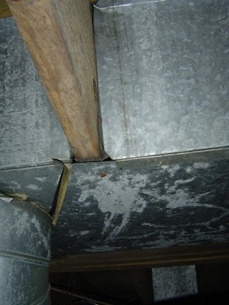
My grandfather, the original Allison Arthur Bailes, was an electrician, plumber, HVAC contractor (‘heating & air man’), and refrigerator repairman. In the ’70s when I was a teenager, I used to spend a couple of months each summer working ‘on the truck’ with him and my uncle in Leesville, Louisiana. My job was mostly to schlep tools and materials between the truck and the job (though, being in Louisiana, I didn’t know the word ‘schlep’ at the time).
On HVAC jobs, what I recall us doing mostly was checking and adjusting the refrigerant charge in cooling systems. Occasionally we’d replace blower motors or diagnose other mechanical failure problems with the equipment, but I don’t recall ever spending a single minute troubleshooting a duct system. If someone called with a comfort complaint, the problem always had to be with the equipment.
Of course, this was the 1970s, and the whole building science thing had barely gotten started. Few people really knew how much duct system problems hurt performance. (We were also discharging the old, bad freon directly into the air then, but that’s another story.)
Now we know how much poor duct system design and installation can reduce performance. We know that oversized systems underperform and fail sooner. We know that not every carbon monoxide problem is cracked heat exchanger.
Yet, the HVAC industry, made up largely of professionals with high integrity like my grandfather, hasn’t grown and adapted. Yes, there are some who know how to do it right, and some of those even put what they know into practice. But overall, the HVAC industry needs an overhaul.
Yesterday I read a great article by John Barba on doing load calculations to size HVAC systems. He’d recently taught a class of 35 HVAC pros, and almost none of them said they do load calc’s. When asked what size heating system they would put in a particular house, given all the parameters necessary to do a heat loss calculation, they came up with numbers ranging from almost double to more than triple the actual load. You really should go read the article because it gives you a great look at how a lot of HVAC pros think.
Unfortunately, this problem is widespread. I wrote last year about some of the problems I’ve found in collecting the Manual J load calculation reports required for ENERGY STAR homes.
Speaking of ENERGY STAR homes, Version 3 of the program is in the pipeline now and set to become mandatory next January. I’ve written several times about the HVAC checklists for the contractor and the rater and how difficult it will be to get them done correctly. It shouldn’t be this way. Everyone who understands how HVAC should be done says that the items on those checklists are things that HVAC contractors should be doing anyway, whether a home is going for the ENERGY STAR label or not.
Yet the reality is that the HVAC industry isn’t ready to do things the right way, and that’s a sad statement. Part of the reason for this is education. I’ve taught a number of HVAC contractors in HERS rater classes over the past few years, and they’re almost always surprised at how much they learn – about HVAC! One told me, “Allison, you’ve taught me stuff about my business that no one’s ever taught me in any of the classes I’ve taken before.”
Another reason is money. In the HVAC industry, you’ve got to get in and get out quickly because in most cases you can’t price jobs to include time and materials necessary to do things the right way. One HVAC contractor told me that they know static pressure in duct systems is important, but they don’t make that simple measurement on each install they do because it takes extra time.
On the latter point, I wrote last year that HVAC contractors should charge by the square foot rather than by the ton of air conditioning capacity. That helps solve the problem of oversizing, but the going rates for HVAC installs in new construction still don’t allow for quality duct design and installation.
Another problem with new home construction is that most of the best HVAC people work on existing homes, where they can make more money. They still don’t do much with duct systems, but they often do a better job with the equipment.
Pretty much everyone I know who works as a home energy rater or building analyst and has to deal with HVAC contractors has lots of frustration around this. The industry is being pushed in the right direction, with everything from more stringent energy codes to programs like ENERGY STAR, but it’s a struggle.
I wish I could wave a magic wand and make everything right. Sometimes it feels like that’s the only thing that can work.
Air conditioner photo from Echiner1 on flickr.com.
This Post Has 40 Comments
Comments are closed.
Allison, when is your next
Allison, when is your next Manual J, S & D class scheduled?
Allison, does your class
Allison, does your class teach Manual T too?
Thank you for this collection of articles, including this post. I’m quickly finding I’m being sought out for HVAC design services. The good news is the HVAC contractors are learning from what I do. Shocked. But, that’s the way it is! See you soon!
Paul, we don’t teach an HVAC
Paul, we don’t teach an HVAC design class. We do have an Advanced HVAC for HERS Raters that covers the basics of HVAC design, but we don’t teach them how to do it. Our next offering of that class is on 27 May.
Sam, see my response to Paul
Sam, see my response to Paul for your question about Manual T. Glad to hear you’re making headway with the California HVAC contractors.
Will you be in Orlando for the RESNET conference next week? Is that what the ‘see you soon’ refers to?
The consumer needs to be
The consumer needs to be educated. Once they learn they’re not getting what they’re paying for, or paying for more than they need (wasting money), the industry will react to the demand. Until then, we’ll probably have to pay extra for the service quality we should already be getting.
HVAC contractors and other industry professionals should also take more pride in their work and educate themselves to improve this situation too. If those in the field doing the work can’t explain it to the homeowner, who will?
Great post. I was in a
Great post. I was in a retirement community doing a HERS rating yesterday. Homeowners were complaining of high bills and comfort issues. They had just installed a new heat pump. We hooked up the duct blaster and could not get pressurized the system. We followed the “can’t reach” guidelines by stepping down the BD, and ended up at 1250cfm25 with 95% to the outside. The maintenance man, who is the resident heating and air expert, could not figure out why. Well, it started with a 14 in return that was completely disconnected, then expanded to the ductboard- 2×4 HYBRID plenum, and went through the entire duct-board trunkline and supply runs. Yet, this was not evident to an industry expert. When we opened his eyes to the problem, it became clear as day. It is incumbent upon us to educate.
Eric, you make a good point
Eric, you make a good point about demand from home buyers and homeowners pushing the industry. I’m doing my part by trying to put out as much good info as I can about how to do things right because I agree that education is a huge piece. Also, I know home energy rating companies that have gotten established by working on the back end to drive demand rather than the front end to put out good products and hope the demand arises.
As a builder, though, you’ve certainly experienced the other focus of home buyers & owners – that is, not wanting to spend extra except on the fancy finishes (granite countertops, hardwood floors…). How have you dealt with that?
Lance, great example! That,
Lance, great example! That, unfortunately, happens way too often. Another thing I’ve found is that when you have an air handler and duct system in an attic or crawl space, the problems are usually on the other side of the air handler. The HVAC guys, like my grandfather, usually just work on the box, the equipment.
There’s nothing wrong with
There’s nothing wrong with pulling yourself up by the boot straps and taking responsibility for those in your industry that provide inferior service.
There’s no crime in not allowing poor workmanship.
The absolute best option for the HVAC industry would be to clean up their act by beefing up their standards and level of proper install protocol.
Is that harder than it sounds?
Thanks for addressing the root of the problem (with respect to poor HVAC performance, bad air quality and wasted energy).
Please, please tell me that
Please, please tell me that array of air conditioners is just a funky piece of artwork….;-)
In the last 15 years, I have
In the last 15 years, I have worked with 9 different HVAC companies, including the perceived “best” in the area. In the past, I’ve had companies question the validity of blower door test, duct sealing and Manual J. Fortunately, I found the right one about 5 years ago. I met him at an NAHB class and he got it. I actually brought him in to finish a job that another HVAC pro was botching–he wouldn’t seal ducts, didn’t do the load calcs, put in unsealed combustion equip (all in the scope of work)–I’ll stop short of listing everything. Anyway, the new guy came in, took care of the problems and have worked together since. He continues his quest, he’s now BPI and a HERS rater.
The biggest question in my
The biggest question in my mind is: “How do you find a good HVAC contractor” followed by “How will you know if he’s good?” I’ll be due for a new heat pump system in the neat future, and I’d like to have a plan in place before it’s an emergency…
Gary, good points! I don’t
Gary, good points! I don’t know all the reasons why, but yes, it does seem to be harder than it sounds.
John Z., I’m happy to hear that, after much suffering, you’ve found a good HVAC contractor who’s been with you for 5 years. As I said above, there are a few who get it – and do it – and the more builders like you reward them by hiring them for your jobs, the more we can help move the industry forward. I think that says loads about him that he’s BPI and HERS certified.
John P., I do believe that
John P., I do believe that wall of ACs is actually a real installation. I believe it’s somewhere in Asia, as I recall from the photographer’s page on flickr.com.
Daniel, one of the first
Daniel, one of the first things you can do when looking for a good HVAC contractor is to find one, as John Zito above did, who’s a certified BPI pro and/or HERS rater. That will ensure they have some training in the house-as-a-system approach and know how to test for duct leakage.
In addition, you can use ACCA’s guide on ‘Choosing the Right Contractor’ to help with your search and ask them to use ACCA’s Quality Installation Checklist, too.
This became such a big
This became such a big problem for us that our only solution was to bring it in-house.
Lance, that’s definitely the
Lance, that’s definitely the best way for builders and home performance contractors to ensure they get the job done right. Hire ’em. Train ’em. Hold ’em to high standards.
Those who want the best
Those who want the best training ACCA has to offer should consider the Residential Epic Training:
http://tinyurl.com/46zpbbp
Unfortunately, you are
Unfortunately, you are correct on most of the issues you address in regards to the HVAC industry. We have trained and educated many of our employees (as you know) but have had a difficult time applying this information to the sales process. What everyone needs to keep in mind is that the HVAC industry, just like any other industry, is in business to turn a profit. As much as we would like to spend hours with a customer trying to dismantle all the “junk” information they have been told by under-informed companies, we still need to get the sale. We install systems to the best of our ability, with honesty and integrity, and never taking advantage of the customer–but, even though we pride ourselves on delivering great value to the customer, we cannot always afford to give the customer more than he is willing to spend. We use our training daily to solve problems and, again, are trying to educate customers as fast as we can, but, keep in mind that the HVAC industry (and I will through the residential contracting industry under the bus with us) has been a mess for a long while and it will take a long while to sort out. We need patience and support—the change is coming but slowly.
David, thanks for the link.
David, thanks for the link. That’s a great training!
Jake, thanks for the great
Jake, thanks for the great comment! I was hoping someone from the HVAC industry would speak up here. Moncrief Heating & Air is one of the companies I was thinking of when I wrote that the best HVAC companies do more work in the existing home market than in new construction, and I know you guys do good work while, of course, being mindful of the balance between good work and reasonable charges. I also know the change that we need won’t happen quickly, but I’m doing what I can to get the word out to help companies like Moncrief push the envelope.
We appreciate your help,
We appreciate your help, Allison.
Allison, I’m permanently
Allison, I’m permanently relocating to Atlanta this Saturday. I’m open for business on Sunday! I’ll see you when you get back for RESNET.
I specify static pressure
I specify static pressure/system airflow testing and load calcs in all my my HVAC replacement scopes of work. I’ve actually had contractors add line item charges to do these because they were included in the scope. The really sad part is that these items, as well as duct sealing/testing are required as part of the ANSI/ACCA 5 QI-2007 Standard. If you have a copy handy, check out sections 3.1 et al, 4.1 et al and 5.1 et al. If you don’t have a copy email me at earthwiseengineeirng@cox.net and I will send you a pdf copy. I also have a pdf for NAIMA Insulation Guidebook. It basically demonstrates that Level 1 QII should be standard practice, not just and Energy Star or HERS credit. So the question is why do some contractors still not get it?
That’s easy, Shawn. It’s
That’s easy, Shawn. It’s because no one requires it of them.
I agree with what Jake said. Change is happening, albeit slowly. What we are experiencing right now is all the more frustrating because a growing number of folks are beginning to understand the issues, while the business side hasn’t had time to catch up.
As individual contractors incrementally improve their processes — within the constraints of the market — others will eventually be forced to follow or they will perish. The growing minority of ‘good guys’ is educating builders. Don’t forget, builders are the key to market transformation because they write the checks for the vast majority of complete HVAC installs.
I completely agree with David
I completely agree with David. If you want to transform HVAC in the new construction and renovation market, the contractor and the architect both have to buy into the process. I can preach all I want to contractors about best practices, but until there is a fundamental shift in the way buildings are built, it is fruitless. Let’s start with building design allowing for adeqaute space for quality ductwork installation–even with “rule of thumb” design, this would improve airflow, and therefore performance, immediately. Shoe-horning 5-ton duct systems into web trusses is not “best practice” but contractors seem to always find someone willing to do it–HVAC system design is constantly sacrificed to the almightly god of basement ceiling height, right? Educate contractors and architects to specify performance in construction documents (as Shawn suggests), the jack-leg contractor will fall by the wayside, and decent contractors will be paid the proper amount to install quality systems. (OK, I’m off my soapbox).
NC licensing boards require
NC licensing boards require that design calcs are done, but no enforcement until customer complains. Informed customers need to state up front they will want a copy of J & D, and a commissioning report that includes performance measurements, including airflow (which would naturally follow if there was any balancing done). And airflow should be checked everytime a system is serviced/re-commissioned, and compared, esp. when adjusting freon (otherwise they’re guessing). Performance numbers should be written down, starting w/ manufacturers’ specs, my design specs, then initial commissioning measurements (w/in a reasonable range of tolerance), re-commisssioning w/in a year (incl opposite season..), then at appropriate intervals thereafter. But customers need to understand that quality comes at a price; they just need to insist on getting it once they pay for it. Written documentation will scare away the timid contractors (but bless them anyway for being there in the heat & snow, etc. all these years…)
Jake, re: putting ducts
Jake, re: putting ducts inside. Lots of lip service but not a lot of compliance in two-story homes and homes on slabs. You know the reason. Attic installs are sooo much easier!
I recall a green architect in NC who was designing her own home. Quite a looker! (referring to the house) She obviously spent a lot of time and thought on duct paths. There was only one small problem. It wouldn’t work. She didn’t allow for duct crosses or min bend radius. She nearly cried when her mechanical contractor arrived on site for his first walk-through.
Architects are simply not trained for this. It’s easier in a one story home on a basement… just use 18″ or 20″ open web floor trusses and watch for solid beams.
Every home designer should make friends with or pay a mechanical contractor to help them learn how to bring HVAC inside. The good news is that with today’s windows and tight shells, it’s no longer necessary to put supplies at the perimeter. Also, systems & ducts are smaller. I can’t remember the last time I specified a 5-ton system, or even 4 tons. Projects I work on typically come in at 1100 to 1400 sf a ton. Homes with loads larger than 3 tons typically require more than one system due to layout or excessive duct run-out distances.
The biggest part of the
The biggest part of the problem as I see it is that general contractors and homeowners (the people who buy HVAC services) aren’t very educated about those services, so they shop on price. The cheapest contractor is never going to be able to give you the best system. Unfortunately, it seems the economy has made this worse by driving prices down. A good HERS rater is someone who can educate everyone else on the job about why upsold HVAC services are worth it.
With that said, sadly, I think HERS raters are often part of the problem. Most HERS raters (unless they have some other job/training as well) have taken a relatively short class on building energy efficiency, and it’s not uncommon to find one that thinks they know a lot more than they really do. The pervasive attitude that the HVAC installer industry doesn’t know what it’s doing is both incorrect and making the problem worse. The HVAC industry knows what it can get its customers to pay for and what it can’t. Some of the things they don’t do seem like small numbers, but if you add up the extra materials, time, and equipment, it’s a big number and they know it. In my experience, at least half would like to do more but know their clients aren’t going to pay for it.
Some of the HERS rater reviews of sizing calculations that I’ve seen are almost scary, and I can understand why the HVAC installers are frustrated by it. Energy Star 3.0 isn’t going to work unless HERS raters and HVAC contractors become full partners who each respect that the other one knows how to do their job. When that doesn’t happen, you might get some contractors that falsify their checklists out of sheer frustration.
We’re not always right. For my own house, I’d take a system sized by an experienced HVAC installer using a ductilator over a Manual D done by a person who just took the class any day.
Two problems already
Two problems already mentioned are cost and education. But I am not sure we understand how serious the problem is.
First of all, the builder cannot pay more for HVAC if the buyer doesn’t demand it. His product will not be completive.
Secondly, I don’t think the HERS community really knows the dramatic cost increase ES 3.0 is demanding.
I recently completed a professional design of a 4400 sq. ft home including two site visits, Manual J, S, T & D with CAD drawings and specs. It took 43 hours. That’s not a RightDraw pix where the HVAC contractor has no clue what you assumed in fitting geometry, boot selection, elbow radius. It’s a full blown layout with details sufficient (sometimes) to convey what was assumed in the design. Then there’s the cost of additional materials i.e. quality diffusers at $25 to $35 each instead of $4. Trunk duct instead of 400 ft of flex, operable balancing dampers in concealed duct systems – $50 each, turning vanes, tapered take offs, concentric transitions etc etc.,,,,, Add a full day for commissioning and air balance. In the end, the guy presents the builder a fair price and the builder cannot stop laughing.
Now the education component -. In over 10 years, I have yet to receive an accurate Manual J from an HVAC contractor. So we do have a huge education challenge. But the idea that the professional design process can be taught in a 2 to 3 day class is not even close to reality. A one day class would just get you started. One week might be more appropriate. Then you have another 2 to 3 weeks on Manual P,S,T,D and B. (soon add Manual Z) Add the necessary knowledge of sheet metal fabrication (fittings), how duct systems fit together and how its installed in the structure. It makes no sense to create an expensive design that cannot be installed, In the words, its hard to install a 4×14 register boot in a joist space 12 inches on center.
How many HVAC contractors can take off two to three weeks to “go to school”? Its a double whammy- the tuition cost wont be cheap. Then the loss of income is a killer to guys who live from week to week.
I think Sam has done a fabulous job with V-3. But I am afraid the crafty HERS and builder community will quickly find the loop holes to game the system. The end result — more complaints and publications like Home Energy Fraud…..Then an honorable mention on 20/20 or our own Chris Matthews segment, right after the duct cleaning frauds.
BUILDER VIEWPOINT
BUILDER VIEWPOINT
Danny, that sounds like a commercial approach to a residential install?
…or…
Should there be a difference in the two building types (with reference to installation)?
As a home builder for many many years and now an energy rater/energy use proponent I remember the chatter I received when in conversation with my HVAC contractors. I would ask them to give me a “more professional approach”, shall we say.
“This ain’t no commercial job, Gary. I can’t do all that work for the money you’re willing to pay”.
There is a separation between the to types of work in the market place. One has a higher standard than the other. Are we “asking” the builder (ultimately the buyer) to pay more? or … are we realizing that for all these years the buyer has been sold “poor quality” and we’re now beginning to bring the two closer in line with one another (you all do realize there are two “worlds” in construction? right? – – Commercial World View and Residential World View)
All comments have contained a
All comments have contained a lot of truth. Five thoughts for what they are worth:
*For too long, many Rating firms passed every house with fifteen minute insulation inspections and a little show with the blower door and duct blast. (How’d we do?) This has given many builders an unrealistic view of building science and the ease in acquiring the Rating. We need to cull these Raters.
* Legacy HVAC firms are likely to slowly fail as mechanical engineers enter the field with more knowledge, stricter adherence to and understanding of building science. Code requirements and stricter enforcement will accelerate this pace.
*When builders start to build, it will not take very long for recent gains in HERS Ratings to fall precipitously as the expense and of proper adherence of V3 HVAC standards become apparent. Their HVAC contractor will buck the changes for as long as possible and the builders will follow the path of least resistance and of least expense.
*Surprisingly, the future of V3 Rating may lie with the production builders who can more easily roll procedures into their business model, use dedicated crews, build the same models repeatedly and have recently expressed a declaration to become 100% Partners.
*It is up to the industry to police our own and to constantly train ourselves, our builders, the HVAC contractors and anyone who wants to hear about the importance of building science.
Danny is one of the sharpest
Danny is one of the sharpest HERS/HVAC guys I know, but think his example overstates the point. No one would argue that it should take 40+ hrs of design/verify time to get good HVAC. In any case, 3rd party design/verify is always going to cost more.
I believe an additional 8-12 hours of design and QA time done in-house would go a LONG way to resolve the types of problems we’re seeing. On a $10k to $15k system, builders would accept a 10% premium if they understood the value it would bring. Custom builders often pay far more than that on high SEER equipment that is ultimately wasted on a poorly designed/installed duct system. The problem is, the HVAC dealers who do good design work only want to sell cadillac equipment (best case, the value of anything over 15 SEER is marginal at best).
Regarding raters checking loads… I argued in a long editorial in Nov 06 Home Energy that ES put the cart before the horse by requiring HERS raters to check loads without proper training. The folks who added that well-intended requirement apparently had no clue what this involved. A short on-line training on this should be developed and made mandatory.
@Amy wrote:
@Amy wrote:
> The pervasive attitude that the HVAC installer industry doesn’t know what it’s doing is both incorrect and making the problem worse…
I don’t disagree with this, but not because it’s not true. You said yourself that “half would like to do more”. What about the other half? That’s pretty much a broken industry in my book.
But I totally agree with you about fostering an attitude of partnership. This requires that HERS raters become *much* more proficient at HVAC, but without pretending to be HVAC designers.
When you get down to it, the
When you get down to it, the home owners or builders are looking to get the job done for the least amount possible. I’ve seen people give the job to the contractor that was less 5% cheaper. I hear questions about this brand or that one. They don’t know what questions to ask or that paying more upfront for proper equipment sizing and duct design will pay them back three fold and offer them more comfort. The only thing the consumers seem to know is the PRICE. Builders know this.
I bid a job for a builder. Selling myself cheap and still getting laughed at. It was a condo job and I was bidding on the rear unit. Walked through the front unit as I left and understood the quality I was selling wasn’t what he was looking for. Slap some flex duct in, drywall the duct chases shut and put a note in the real estate listing High Efficiency Heating an Air Conditioning. Until that changes the hacks and cut throats will run the residential market.
I could not agree more. I
I could not agree more. I will be 32 this summer. I have worked in HVACR installations and service since I was 15. I have always loved to make things with my hands and take pride in being meticulous to a fault. Yesterday my current boss told me my production speed wasn’t up to par with some of the other crews. Well to start off I’m not a crew I am one man. They actually have helpers usually or they don’t take their time and their works suffers or in my opinion from what I have seen it does. I just believe in quality. I am sick of hearing I can’t see it from my house or that should be good enough. I have spent more than half my life damaging my body to make the homes of others as comfortable and healthy as I can. I offer this advice to anyone purchasing anything from a HVACR contractor. Your home comfort system can be a large and complicated task to plan design and actually build and install we have the biggest pipe and the least amount of space to run it and more and more codes governing how it should be done. Don’t let a salesman blind you. Do some research and go in to a decision informed. Be firm about quality and if they don’t like that you don’t want them. Try to see the quality of work they do. Try and meet the installers before hand with the salesman so someone who knows what they are looking at has a hand in the plan for your home. Salesmen usually have no clue what it actually takes to do the job some do but more don’t. Pay close attention to his hands if they look like he has never been cut by a piece of sheet metal don’t be surprised when the installer has to change his design to match the situation. And I know how hard it is to see your hard earned money go down the drain so don’t think the cheapest bid is the best to accept I’m sure they are the cheapest for more than one reason. I would like to add that I more than understand the position of my boss. With what he told me he is simply having a hard time affording me as a lead man because of the amount of time the jobs have taken although there are so many aspects of the jobs and they way the company is run and the way materials are managed and how long you have to wait to get them when you find out you need them. All THINGS AND FACTORS PLAY A PART IN SUCH A PRODUCTION.
I have to agree will most of
I have to agree will most of the comments here. I know that I have been in Robert Graff’s position a few times.
I think the real problem is “perceived value”. People don’t really mind spending more money for something if they feel that they are getting what they pay for. But for right now, at least, they don’t “see” any value to spending a few extra thousand dollars to have it done right. They know that their neighbor had a new system put in for 10k, why should they spend 12k when they have the same size house? And the neighbor has not had any problems (that they know of).
The difficulty in out trade is that the poor duct work takes 3 to 4 years to kill that compressor. But by then it is too late. Then they have to run on electric back up heat for a week at 10°F outside temperature until we can get the new compressor in. So how much did they save? Probably nothing. But they can not see the value up front.
Our main issue is to get the government out of the equation with their SEER nonsense and other ratings and get some real science in the industry that will show (explain) to the customer the REAL value of spending that extra 2k to have it done right.
As a contractor, I would love to be able to offer a customer who allows me to do a proper, by the book install a 10 year parts a labor warrantee to show the value of having it done right.
I think that until we can make that kind of bold statement and offering to customers they will not “see” the difference between the 10k install and the 12k install. They will look at the name brand on the equipment.
But the name brand on the equipment is another hurdle for us as technicians to get over. The manufacturers have much more power to influence the customer buying habits then us contractors. So they are not working for us but against us. The customer’s attention is on the label, not the installer. And we all know which is the most important.
I have the following Amana
I have the following Amana equipment.
AMV9/ACV9 TWO-STAGE VARIABLE SPEED GAS-FIRED WARM AIR FURNACE INSTALLATION INSTRUCTIONS.
XIII. CIRCULATING AIR & FILTERSDUCTWORK – AIR FLOW Page 26
Duct systems and register sizes must be properly designed for the CFM and external static pressure rating of the furnace. Design the ductwork in accordance with the recommended methods of “Air Conditioning Contractors of America” Manual D.
2009 Manual D Residential Duct Systems on page 32 has the following.
“Single blade dampers at outlets and returns are inadquate balancing devices. Use opposed blade dampers that have a gang of blades”
Can someone please explaine why our installer who is an Amana dealer would not follow code?
He only installed single blade dampers.
Why are opposed blade dampers having a gang of blades the choice of Amana and Manual D?
Terry Mishler
@Terry: That particular
@Terry: That particular citation from Manual D is from the section on balancing dampers. The point being made is that supply diffusers should not be used for system balancing.
In the same section Manual D stipulates that balancing dampers should be installed as close to the trunk and as far from supply outlets as possible. Grilles and diffusers are covered in Manual T.
The bigger question is why your contractor didn’t install proper balancing dampers. Of course, he’s in good company as very few residential contractors install balancing dampers, let alone actually balance the duct system. Why you ask? Because one requires them to do so. After all, how many code officials have a clue about the various requirements in Manual D.
I worked in the HVAC industry
I worked in the HVAC industry for only about five years. After my first year the NATE (North American Technician Excellance) program was initiated and backed by many of the equipment manufacturers. My company was a fairly large residential/light commercial company holding both the Trane & Lennox delear brands as well as cheaper equipment. As I recall, our Trane technical rep saying in a class full of local techs- “Trane fully supports the implementation of the NATE certification for 2 year experienced service technicians, and anyone who passes the initial service “Heat Pump” certification should be given a 5 dollar raise!”. Boy I thought I was in for a hard test- It was quite hard and very technically oriented. Out of the four service techs in our company that took the exam, I was the only one who passed. None of our senior techs passed. Needless to say I didnt get a raise. If I remember correctly, the three techs that took the exam failed the next following tests and passed only after they were given the tests at our company offices where they could help each other with the answers.
I am a senior Instrumentation & Electronics tech with 13 years in the offshore Oil & Gas industry now making exactly 4.5 times more yearly gross income than I ever made in the HVAC industry, with vacation, retirement, bonuses, etc,…
I do my own HVAC work in the small rural community where I live in Louisiana when Im not in the Gulf. The money is just not there to attract proficient technical people to that industry. Its hard for a major Oil & Gas company to find those individuals for their industry also.
I wish there was an answer. I just dont think you will find it in our consumer driven society…