An HVAC Company That Thinks Outside the Box, Literally
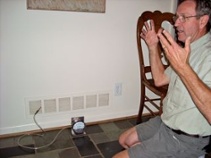
I’ve written a lot about HVAC (Heating, Ventilating, and Air Conditioning) companies in the Energy Vanguard blog, and a lot of what I’ve written is pretty critical. I’ve ruminated about why they won’t do things right, gone on a tirade about a bad Manual J, and beseached them to look at the ducts in addition to the equipment. Those articles have been popular, too, so some might think that I have it in for all HVAC contractors.
I’ve written a lot about HVAC (Heating, Ventilating, and Air Conditioning) companies in the Energy Vanguard blog, and a lot of what I’ve written is pretty critical. I’ve ruminated about why they won’t do things right, gone on a tirade about a bad Manual J, and beseached them to look at the ducts in addition to the equipment. Those articles have been popular, too, so some might think that I have it in for all HVAC contractors.
Today, though, I’m going to tell you about one company that represents a growing trend in the HVAC industry. It’s not as widespread as I’d like to see, but you’ve got to start somewhere, right?
Moncrief Heating and Air Conditioning, an HVAC company with 75 or so employees here in the Atlanta metro area, is on the path to doing things the right way. I first got involved with Moncrief when John Nuesse took the HERS rater class I was teaching in December 2009. The next month, Moncrief put four more of their guys in the class, including Jake Reid, a smart guy with a degree in molecular biology from Vanderbilt University. (Read this interview with him in an article in the Atlanta Journal-Constitution.)
Since those five guys took the HERS rater class, one (Matt Wolski) has gotten certified as a HERS rater with Energy Vanguard Energy Ratings. Also, if you’ve been reading our blog for a while and the name Moncreif seems familiar to you, it’s probably because you’ve read other articles we’ve written about them. Ken Briggs (shown in photo above right), their main air flow guy, has analyzed the air flow problems with my in-laws’ HVAC system and then supervised the retrofit of the ducts to make it work better. He also helped a former EV employee retrofit his mechanical closet to improve air flow in his condo.
Since I was feeling the need to show that good things are happening in HVAC world, I called up Jake yesterday and asked him how he feels they’ve improved. Right off the bat, he told me that they’re now measuring the static pressure and looking at the air flow on every new installation. They’ve realized that the overall efficiency is greatly affected by what happens ‘outside the box’ (i.e., in the duct system).
Moncrief is also one of the rare HVAC companies that looks at the building envelope and takes a house-as-a-system view. They recommend spray foaming rooflines in some cases, as well as looking for infiltration and other building envelope problems when they address comfort issues. On another job, Jake told me he found that the large attic fan in a gable end in one house was causing high humidity, so they shut it down and helped reduce the humidity.
With several guys in the company now trained in building science, air flow, and home energy ratings, Moncrief is an HVAC company that’s definitely on the right path. This, I believe, is a trend that we’re going to see accelerate, and my hope is that in a few years, doing things right will be standard practice in the HVAC industry. Let’s make it happen!
This Post Has 6 Comments
Comments are closed.
For awhile I have held the
For awhile I have held the opinion that HVAC is really an engineering process and not the mechanic’s job many make it out to be. I would love to see companies in my area which could be as methodical as Moncrief. The tragedy seems to be customer demand is lacking, and HVAC contractors feel ever-present need to be cheap and cut corners. Three cheers for companies like Moncrief!
In addition, let us talk
In addition, let us talk about the dark side. I talked with a company in the Houston area which had great expectations, I think fed by NCI (National Comfort Institute). They were talking about measuring airflow and doing everything up to ACCA methods: Manual J, Manual D, etc. A year later I finally saw them operating out of a Home Depot store, and HD does not think that way. It is my belief they failed to find enough revenue to support the high road, then decided to take the low road. Another company had great expectations, this time with the Comfort Institute (not same as NCI). They had the CI president to my house showing the HVAC guy about airflow measurement. Sadly I think they grossly mismeasured my airflow, and got way off from focusing on my cold-bedroom problem which was my #1 concern. They said they balanced my airflow, only much later did I learn you usually need a room-by-room Manual J (heat load model) first. Without Manual J how can you possibly know what airflow is appropriate? They told me my total airflow was barely over 700 CFM for a 3-ton system, I was greatly disappointed to learn the blower was on 2nd speed out of 3. They never figured that out.
Discussing the downside, and what goes wrong, can be a very useful complement to the complete optimism scenario. I wish Moncrief had been the one to visit my house.
As a former building
As a former building inspector for an Atlanta area city, I came to appreciate Moncrief as a contractor who ALWAYS made the extra effort to do things right. First, they always pull permits and have the work inspected, this puts them out front of most of the area contractors. The work was done correctly, and code violations from the previous installation were corrected. Never was the standard complaint used,”It was already like that, we did not do that.” My hat is off to one of the area’s most consistant perfomer.
It is a start and more and
It is a start and more and more companies will take the high road.
I believe that once the installers know how to do it, it will not cost very much more than typical to do it right.
On the contrary, I usually turn my findings into up-sales for the homeowners. This is as it should be.
The better we can train installers, and also train them into making these kinds of up-sales, then the more and more it will get done right.
If they cant do it or sell it, then all will just go back to default.
We have a long way to go.
M. Johnson
M. Johnson: Yes, HVAC is more than just a mechanical job. The HVAC companies that do it right have to look at the whole house as a system, not just the HVAC, and certainly not just the box. And yes, when companies feel like they can’t compete against the low-bidders, it turns into a race to the bottom and everyone suffers.
On your technical issue, when first installed, fixed speed blowers are normally set on the middle speed so that if they need to make adjustments later, they can go either up or down. If your system was moving only 700 cfm instead of ~1200, changing the dip switch wouldn’t have solved your problem. It was probably running too high a static pressure because of restrictions in the ducts.
Paul: It’s nice to hear that Moncrief’s work has impressed building inspectors, too. Knowing the guys there, I’m not surprised.
Christopher: Up-selling is exactly what good HVAC contractors should be doing because they’re looking for – and finding – more problems. It’s not selling them stuff they don’t need, though – it’s selling them what others have ignored, like air-sealing, duct retrofits, insulation. In the end, you have a much happier customer because they’re more comfortable, they’re saving money, their house is more healthful, and everything lasts longer. It’s a win-win situation.
Allison: I did not anticipate
Allison: I did not anticipate getting into analyzing my “700 CFM for 3.0 tons” allegation, but there are some other facts:
>>If your system was moving only 700 cfm instead of ~1200,
>>changing the dip switch wouldn’t have solved your problem.
>>It was probably running too high a static pressure because of restrictions in the ducts.
>>when first installed, fixed speed blowers are normally set on the middle speed
>>so that if they need to make adjustments later, they can go either up or down.
Initially the measurement was 723 CFM, adding up 14 supplies. After finding the high fan speed via another tech, a second measurement was 1456 CFM and static pressure was measured at 0.7 inches water column.
My personal opinion is that I identified the 1st tech as not doing his job, despite having a flow hood and the coaching of the Comfort Institute (the WA one). In the face of available data, perhaps the 1st flow measurement was badly mistaken — when using hi-tech anything, a measurement can be off by a mile.
In a separate argument, why did tech #1 not even think to raise the fan speed? Even I could find that in the manual.
What I have learned is not to be overly judgemental about anyone making a mistake, what matters more is how they recognize it and how they act to remedy it. But in this case we were simply faced with a baffling set of data, until tech #2 came along.
I think we should put more of these measurements in the hands of the homeowners. They will be misunderstood at times and misused, but I believe no worse than the status quo. I wish every homeowner knew the static pressure of his system, and that more knew the CFM delivered. I’m beginning to think that having superheat and subcool numbers are fair insurance against common types of maladjustment — you don’t have to understand their theory to know when a number is not in bounds. SOMETHING has to change to fix this profession, I think it is broken as it stands.