Can an Exhaust Fan Control Humidity in a Spray Foam Attic?
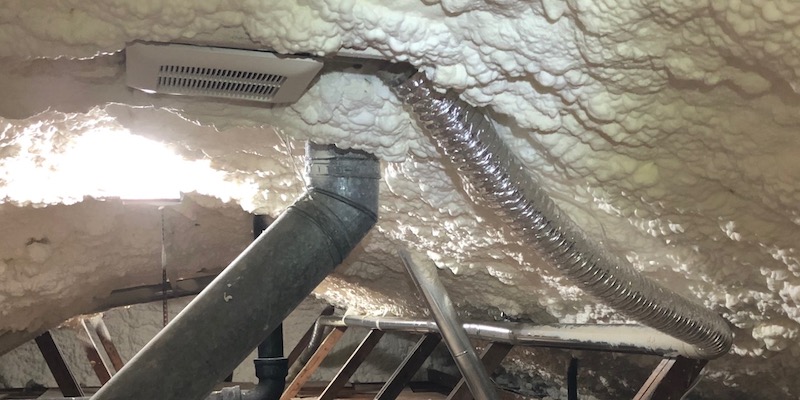
Here in the South, we love our humidity. It makes us glisten in the summer. But we also love our air conditioning and low humidity inside our homes. To save on air conditioning costs, more and more homes have attics encapsulated with spray foam insulation to bring the HVAC systems and ductwork inside the conditioned space. But there’s a problem.
High humidity in a spray foam attic
A few years ago I wrote about the topic of high humidity in spray foam attics. When you encapsulate the attic with spray foam insulation and don’t do anything to condition the air in the attic, the humidity can get very high. It also stratifies, with the highest relative humidity near the ridge. The 2016 article I wrote on this topic shows the data for a house here in Atlanta.
With closed-cell spray foam on the roof deck, you have humidity in the attic but it doesn’t get to the OSB decking. With open-cell spray foam, however, the moisture goes into and out of the roof decking every day. During the daylight hours, especially when the sun hits the roof, moisture is driven out of the decking, through the foam, and into the attic air. At night, the moisture makes its way back through the vapor permeable spray foam and soaks into the OSB again. Do this long enough and you can damage the roof.
Using an exhaust fan in the encapsulated attic
Since that time, we’ve been experimenting with ways to keep the attic humidity low. One of the methods we’ve tried is using a small fan to exhaust air from the attic. If the attic is properly sealed to the outdoors (and many spray foam attics aren’t), the replacement air comes from the conditioned space below the attic and is cool and dry. (Caution: I’m talking about a fan that moves a small amount of air, maybe 100 cubic feet per minute, not a powered attic ventilator, many of which move more than 1,000 cfm.)
One of the houses we’ve tried this with is my own house in Atlanta. When I bought it, the attic had poorly installed spray foam insulation. In the fall of 2019, I had Woodman Insulation* come put a lot more spray foam up there for me using SES open-cell spray foam.* Before they arrived, though, I did a lot of prep work in the attic.
One part of that prep was installing an exhaust fan. I used a Panasonic FV-0511VQ1 WhisperCeiling fan.** It’s efficient, quiet, and operates at either 50, 80, or 110 cubic feet per minute (cfm) of air flow.
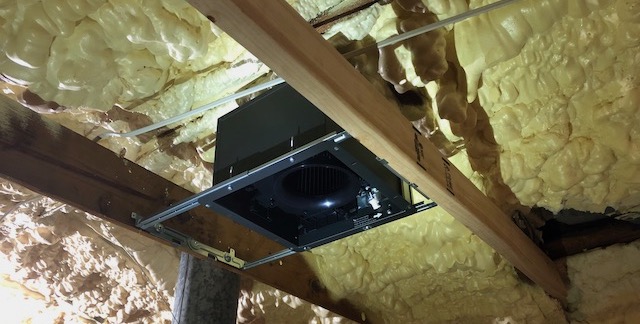
I also set up a HOBO data logger near the ridge. It has magnets on the back so I stuck it to the remainder of my furnace flue. (After installing mini-split heat pumps, I had the furnace and gas meter removed.) The white box to the right of the data logger is a remote sensor for the temperature and relative humidity monitor** that I keep an eye on in the den below. You can see the exhaust fan in the background of the photo.
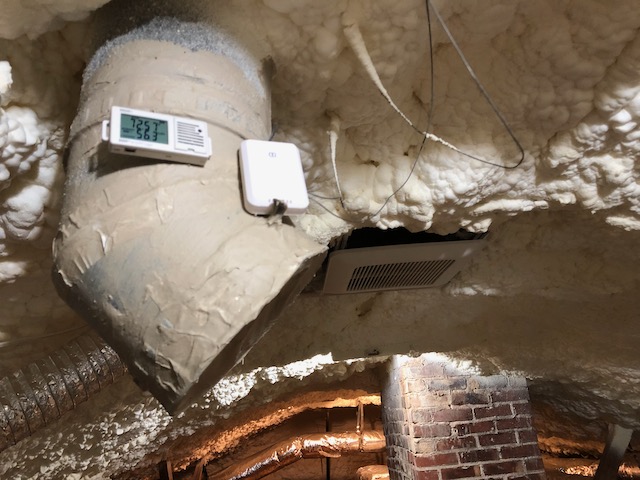
Humidity data from summer 2020
The graph below shows some of the data I recorded last July and August. The upper yellow dots are the outdoor high temperature for each day, the blue curve is the attic temperature, and the orange curve is the attic relative humidity.
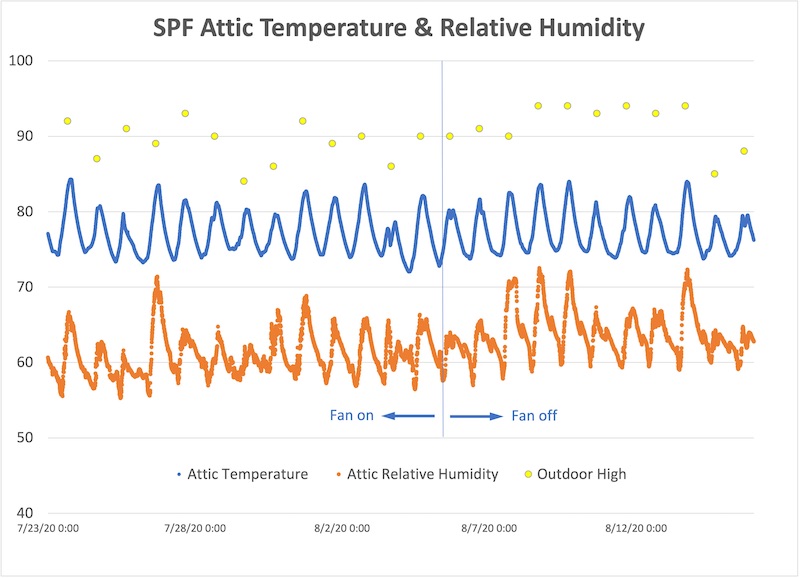
The first thing to notice is that the relative humidity didn’t get as high as the house I wrote about in my 2016 article. The relative humidity at the ridge of that other house got up over 80% on five of the seven days we monitored it in June 2014. It even hit 90% on one of those days. In contrast, my attic’s relative humidity got into the low to mid 70 percent range at worst and stayed in the 60s during the hot part of most days.
The graph above shows relative humidity. Below I’ve posted the graph with dew point temperature. Interestingly, they both fall pretty much at the same place on the chart even though one is a percentage and the other a temperature.
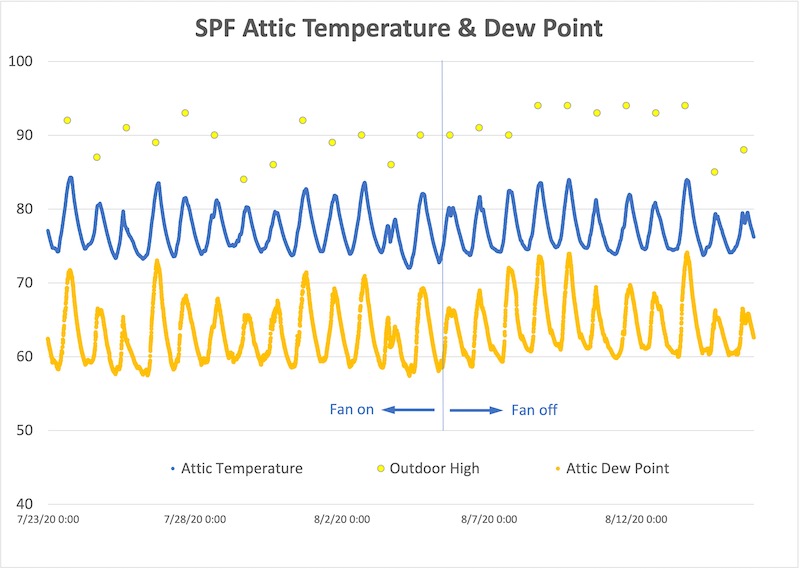
The second thing to notice is that the first part of the graph shows the data with the exhaust fan running continuously at 50 cfm. At 1 pm on 5 August, I turned it off. The first couple of days after I turned off the fan were the same as the preceding days. Then the relative humidity went up. Instead of dropping into the 50s at night, the relative humidity went down to only about 60%. The maximum humidity went over 70% on four of the days with the fan off.
Does it work?
The short answer is that I need more data. There does seem to be higher attic humidity with the fan turned off, but the outdoor temperature also got higher during that time. The good news is that in my house, the humidity is mostly reasonable even with the fan turned off. I don’t like the spikes over 70%, but the attic doesn’t spend much time there.
My data logger is still up there recording data, so I just need some heat and humidity to see how it performs this year. As I mentioned above, I had the exhaust fan set for 50 cfm when I ran it last summer. The building code doesn’t require any conditioning of the air in a spray foam attic. For rooflines insulated with air permeable insulation (the fluffy stuff – fiberglass, cellulose, rock wool), the International Residential Code requires 50 cfm of supply air per 1,000 square feet of attic floor area. With 2,300 square feet for my attic, I’d need 115 cfm, which is conveniently close to my fan’s maximum rate of 110 cfm. I’ll do that experiment this summer and get back to you.
The big drawback with exhaust ventilation (literally!) in a humid climate is that an equal amount of outdoor air is pulled into the house through the building enclosure. Using it in an encapsulated attic helps the attic by exhausting humid air near the ridge and replacing it with conditioned house air. Then the house has to do with a little extra humidity. It’s possible it could also grow mold inside your walls. A better way to exhaust from the attic would be to do it through an energy recovery ventilator (ERV), which is what I’ll do once I get my new Zehnder ERV installed.
Let me issue a word of caution to anyone considering this. This technique will work only if the attic is sealed tight. Many spray foam attics aren’t as airtight as they should be, so running an exhaust fan in them could make a humidity problem worse, not better.
The exhaust fan definitely works for one thing, though. It’s not bad in my house, but I do notice a smell sometimes when the fan’s not running. With the fan running, there’s no odor in the house at all, even when it’s on the lowest setting of 50 cfm.
Allison Bailes of Atlanta, Georgia, is a speaker, writer, building science consultant, and founder of Energy Vanguard. He is also the author of the Energy Vanguard Blog and is writing a book. You can follow him on Twitter at @EnergyVanguard.
* In full disclosure, Woodman Insulation and SES provided their spray foam and the installation at no cost.
** This is an Amazon Associate link. You pay the same price you would pay normally, but Energy Vanguard makes a small commission if you buy after using the link.
Related Articles
Humidity in a Spray Foam Attic
Make Dew Point Your Friend for Humidity
Spray Foam Insulation at the Edge – A Forensic Analysis
NOTE: Comments are moderated. Your comment will not appear below until approved.
This Post Has 84 Comments
Comments are closed.
I have a comparable setup in FL — an open-cell SPF attic, a WhisperValue DC, and a temp/humidity logger. Both are near the attic ridge. The fan went up to deal with residual SPF odor. My sloppy HVAC duct connections have been purging the attic’s humidity just fine. Looking over my data logs, I have pretty much the same results that you’ve seen… The vent fan hasn’t had a huge impact.
One thing I do notice is the post-fan daily humidity spikes don’t peak as high as before. I had been seeing sharp, brief spikes to ~70% like clockwork at 4PM. Post-fan, these spikes peak at 58-62%. The 30-day mean humidity, however, is unchanged at 52%.
Right after the fan went up I fired up the poor man’s blower door (i.e. engaged every possible negative pressure source such as bath fans, range hood, etc) and went to work with my finely calibrated air-movement detectors (ten sweaty fingers).
Two cans of Great Stuff later (1.5 cans toward the house and the other 0.5 in my hair, stuck to my arm, and embedded in my clothing) I’d sealed-up many leaks including a long run of leakage at the base of the gable and one softball-sized leak near the master bedroom.
So it’s possible the fan had nothing to do with the diminished humidity peaks and the sealing effort should get the credit. At some point this month I’ll shut the fan off entirely, see what happens, and report back.
Richard, your results are good. If you’re seeing only brief spikes to 70% RH, your roof should be in good shape.
Allison-
Hoping you can help answer my question. I have read 100’s of articles and want to do the right thing here….
We are doing a whole house remodel to our ranch home in Annapolis, Maryland roughly 2,300 sqft.
We are spraying our entire home with closed-cell spray foam and are planning to close up the gables on both ends of the house. No Ridge vent and no soffits either. We do not have any mechanical in our attic and no HVAC up there so speak of.
Our contractor insists that we keep the gables open and install an attic fan. This goes against almost everything I have read.
Could you lend your expertise?
David: If you’re encapsulating the attic, you absolutely do NOT want to have gable vents (or any other type) or powered attic ventilators. Your contractor has no idea what he’s talking about. You do need to do something to condition the air in the attic. You could put a little bit of supply air in it. You could use a dehumidifier. Or you could use a small exhaust fan. I do the latter with my spray foam attic, and you can read about it here:
Can an Exhaust Fan Control Humidity in a Spray Foam Attic?
Thank you for the response and followup, all.
I would not that at this point, the roof has just been finished and is sealed up. No ridge vent or soffit vents. We do currently have gables vents at the peak of the roof on either side that have yet to be closed.
The home is a ranch. Half the home has vaulted ceiling ( looks like the shape of an A) the other half is not vaulted and resembles the shape of a Triangle.
I would prefer not to go back and add a ridge vent or soffits.
Could we in theory leave the gables open and not spray foam the roof decking, instead using blow in insulation? …not sure how that would work in the Vaulted section (A).
If we do decide to go with an encapsulated attic, we close the gables and introduce supply air, do we also need a return vent?
Thank you all in advance!!!
Thanks Allison.
I believe we are going to close everything off and run electricity and plumbing for a dehumidifier should we have an issue – which we will monitor with a temperature and humidity monitor.
I did have an additional thought…a lot of the articles talk about the attic being conditioned because of duct leakage from HVAC systems in the attics. My thought pertains to homes without HVAC in the attic and no supply in that space either…
In theory, couldn’t you use a similar philosophy as exterior soffit vents as an interior solution to get air to pass freely between rooms into the unconditioned space?
Say for example you put a few of those vents covers in a hallway or bedroom(s) to allow air to get into the attic. Wouldn’t that with the already obvious leakage points (can lights, drywall seams, etc) provide sufficient air to condition the space…
@David Stockum, since there are no ducts in the attic, I would argue there’s little if any economic rationale for insulating the roof deck with closed cell foam. I suggest instead consider fully venting the attic with soffit and ridge or gable vents. Perhaps that’s what the contractor is advocating? Except no attic/roof fan!
In that case, you want to ensure the ceiling is tight and insulate the ceiling with blown-in fiberglass. All wall top plates should be sealed with spray foam, not just the holes. A tight ceiling and R-49 or higher ceiling insulation will get the you the same or better performance than insulating the roof deck. Lastly, avoid ceiling light cans. With many LED options, those will hopefully go the way of the dinosaurs!
Good points, David. In addition to a vented attic being more cost effective with no mechanicals in the attic, it’s also the safest. Here’s an article I wrote last summer based on a conversation I had with Kohta Ueno of Building Science Corporation:
The 3 Safest Ways to Insulate the Top of the House
Thanks for your response Dave. I just saw this after responding to Allison’s initial response.
I think I’m asking many followup questions that you touched on here in my response to him.
We have, unfortunate already added to canned lights (LED).
We do have the option of modifying our insulations plans as that works is still a few weeks away.
If I’m reading this correctly you are suggesting we leave the gables open, no attic/roof fan….but would you add a gable fan or no?
Then we would ensure the ceiling is tight and insulate the ceiling with blown-in fiberglass. All wall top plates should be sealed with spray foam.
Am I missing anything?
Sorry for all the questions. Trying to do the right thing and it seems everyone has an opinion.
Hard to do this without reviewing your plans, but I can answer a couple of your questions.
First, when I recommended against attic/roof fan, I’m referring to ANY powered fan that is designed to ‘cool’ a vented attic. They have been proven to cause more problems than any benefits.
Second, gable vents (at the top of the gable) are effective in lieu of ridge vents (but hip roofs do need ridge vents). However, without soffit vents, I’m not sure if your home would pass code. Depending on your home’s soffit design, it may or may not be practicable to add those vents. If not, you may be locked into an encapsulated attic. That’s not a bad thing, especially if you have a lot of light cans (which are hard, but not impossible to seal). But encapsulation is more costly than vented, all else being equal.
How you would vent the A vaulted ceilings depends on whether you have scissors trusses (i.e., ceilings are at a different angle than roof) vs a sandwich vault where joists and rafters are the same members.
We have a cross gable roof. The A section is a sandwich vault where joists and rafters are the same members.
If at this point we are locked into a spray attic ceiling, I’m wondering which path to take forward. Dehumidifier or introduce supply air. If we do introduce supply air, how much, and does it need a return vent or not?
@David Stockum wrote:
>If at this point we are locked into a spray attic ceiling…
Assume you meant spray attic roof deck…?
> Dehumidifier or introduce supply air
You definitely won’t need a dehumidifier with closed cell foam on the roof deck. The code does not require supply air in unvented attics where the roof deck is insulated with air impermeable insulation, and in any case, you definitely DON’T want a return vent in unfinished space.
If you seal potential ceiling leakage paths from bathrooms with a shower and any other high moisture areas, the attic shouldn’t need any supply air. If the attic has a walkable storage area, you may want to run a supply duct to that area for comfort. I can’t say how much supply air without knowing a lot more about the house, but you don’t need to heat or cool the area to the same temps as conditioned space. You can always add a damper or close the duct off if you find that you don’t need it.
Did the fan deal with the residual odor?? I have an spray odor issue in my living space at the moment….
Yes, although in my case, I don’t smell it anymore even when the fan is off in the winter and spring.
The plots are interesting. I am assuming that the yellow dots (high temperatures for each day) are from a local weather station. Those temperatures do not correlate well with the attic temperature or RH. I am guessing that solar radiation has a lot to do with it too.
I would sure like to see the time scale expanded so that we can see the time of day that the attic temperature and humidity typically peak (high and low). It would also be interesting to see the temperature and RH data converted to dewpoint to see that daily profile.
Roy, yes, I grabbed the outdoor highs from Weather Underground. I’d say the outdoor temperatures mostly correlate pretty well with just a couple of exceptions.
You got your wish, or part of it anyway. I added a graph with dew point.
The dewpoint information is interesting. Can you give me a rough idea of the time-of-day when the dewpoint and drybulb temperature peaks and valleys occur?
Sorry, I meant to tell you the peak times before. I looked at the graph and they usually peak around 5 pm and are heading down by about 7 pm, although once or twice the humidity and temperature were still high at close to 9 pm. The dry bulb attic temperature bottoms out at about 7:30 am and the RH at 10 to 11 am.
Nice article and very timely. Maybe you could ‘link’ the article I wrote for you back in 2012 where you make the comment about those foamed attics not being sealed well…and all those new big holes! Haha! We have done thousands of those predrywall tests since then…and not much has changed. From the touch-up we complete at predrywall, with an average of 6 cans of foam, we normally improve the ACH50 by 30-50%! Those holes to outside (infiltration points) are hiding in those ‘sealed’ attics!
The smell issue is real, but we have only dealt with it in open-cell attics and it only seems bad when the humidity is high. If it weren’t for the smells…you could simply pull air from the home and dump it back into the occupied space in a non-offensive location as to not bring in that wetter outside air and create the ‘negative pressure’ on the home. At 50-100cfm, its likely a non-issue, but better safe than sorry since physics doesn’t care about your health, your home’s health or its durability….its our responsibility to learn and believe the BS (Building Science).
When the home has a sealed attic and sealed crawlspace, we have set up transfer (exhaust) fans to pull air from the sealed crawlspaces and dump that colder, drier into the sealed attics with an additional fan in the attic sending that air back down into the crawlspace on the opposite side via a duplicate fan and duct. These fans are balanced which seems to work well!
We have also seen great improvements by dumping supply air into the attics (without an active return in the attic)…thinking “Cool Hand Luke Meets Attics”! This conditions them better, provides some circulation/mixing and brings those dewpoints down! We like to see one installed on each side of the attics to aid in circulation…or some circulation fans to help the air mixing if its a large attic that is ‘chopped up’ architecturally (I just thought about Joe Lstiburek crumbling up a piece of paper to show us how architects design roofs plans these days…haha)!
Is the “smell” coming from the spray foam?
Craig, some of it may be, yes. But when you encapsulate an attic, you’re encapsulating air that otherwise might be vented to the outside. In an older house, there could be dirt, dead animals, and nasty stuff that’s been stored up there for decades. In a new house, you have lots of materials that are still off-gassing. In short, it’s hard to say what all the odor is from.
Any chance the smell is moisture trapped (or slow to leave) the open cell/sheathing and it’s maybe not moldy but “damp” smelling?
Troy, yes, it’s possible, but the odors appear shortly after encapsulating an attic, which is long before damp sheathing could be a problem.
I had a similar issues albeit in a crawl space where my heat/AC ducts runs. My duct like everyone else’s is not leak proof, so during heating operations the crawl space was being heated and when the A/C was running the space was being cooled. This wasted energy in both cases.
Initially I thought the moisture around the foundation due to poor drainage design during the initial construction was the issue. I revised all the downspout discharging and directional flow of the rain water flow with drainage boxes and discharge piping away from the foundation . This did reduce the humidity a bit but did little to eliminate humidity in the crawl space. My next option was to seal the crawl space so outside air would not enter the crawls space. I caulked all the sill boards, insulated and blocked off all the outside vents. This effort Improved the humidity during some conditions but stood could not maintain my humidity requirements of around 50%.
Three years ago I finally bit the bullet and installed a crawl space dehumidifier in the center of the crawl space, WOW! Problem solved. The dehumidifier has a remote control panel that displays temperature and humidity. I also installed a temperature and humidity monitoring device near the access door that is also the lowest elevation of the crawl space. Both the remote control panel located in my living space and the monitoring device at the access door read consistently 48-52% humidity and 60-65 degrees year round.
Understood this is a different application but sealing the attics and installing this type of dehumidifier with an external drain should maintain a 50% humidity level all the time. These types of humidors have a blower that operates all the time and keeps air circulation while removing any unwanted moisture. The desired humidity can be set and monitored on the controller. My hardwood floors are no longer cold during the winter as well. We also see out living space humidity is much more stable without the humidity being transferred from the crawl space by seeping into the duct when no positive pressure is present from the heat/AC blowing.
We also get a lot of comments on how clean the house smells from friends and family.
Sorry if I have wasted anyone’s time if you do not feel this so a relative post.
FYI, this type of humidifier is not cheap. Costa around $1,400, but for me it is well worth it. Crawl space dehumidifiers are built much more robust than any normal dehumidifier.
LOL
Frank, thanks for your comment. It’s certainly relevant to this discussion because encapsulated attics and crawl spaces are both buffer spaces in which the air needs to be conditioned in some way to control humidity and odors.
Two questions for you: Where are you located? You don’t say, but it must be somewhere in the humid parts. Which dehumidifier did you install?
Interesting topic and glad that you mentioned the possible negative pressure in the home that could result. I’m and HVAC contractor and just did training this morning with my techs and as we talked about house pressure I said a slight positive house pressure is better then slight negative to keep the humidity out in the summer here in Birmingham, AL.
I sprayed foamed (open cell) the attic in my last house and my current house. In my last house I added a 4″ collar with damper to both supply and return in the attic and it keep the humidity down but I was uneasy about the possible VOCs in the attic. I have not addressed the new attic but I do have temp/RH/VOC monitor in the attic to see how it does this summer before I do anyting. My first option was to cut in two transfer grilles to let it balance to the living area.
Is there a way to “seal” the spray foam so that it does not emit the odor? I had read about intumescent paint used to seal it for hire ratings and wondered if that would help the smell.
Thanks!
Tyler
Tyler, I don’t know of a way to seal the VOCs and odor in, but that doesn’t mean there isn’t a way. Maybe someone with experience in that area will comment.
On the supply and return in an SPF attic, I agree with what Curt said below. In addition, putting a return in means you pull in attic air and send it into the house. Putting only a supply in also sends attic air into the house because of the positive pressure. That’s why I like the exhaust fan or, ideally, using the exhaust from an ERV.
I’ve contemplated this as well. I reckon a coating that keeps VOCs inside would also be a vapor barrier. If there’s a synthetic membrane roof underlayment, now we have a second vapor barrier. Roof deck is now the meat in a mildew sandwich? Just spitballing here…
While adding a small supply and / or return (If odor not an issue) might seem a no brainer to control attic humidity there can be a code / safety issue in terms of the attic then being directly conditioned space…in some jurisdictions inspector may demand that the foam get an ignition barrier…possibly even be covered with drywall!
Did you consider a vapor diffusion port at the ridge? Gather you didn’t do that prior to upgrading the spray foam, could it be done from outside? That would be an alternative, right?
James, no, I didn’t consider that. I trust Joe Lstiburek that they work when done properly but chose to control the humidity mechanically. Also, our roof deck is 1×6 solid wood and not as susceptible to moisture damage as OSB.
Great article. One of the first things I did after purchasing my first home about 5 years ago was to vacuum out all of the nasty old insulation and spray the roof deck with open cell foam. This made an enormous difference to the comfort and efficiency of the 1960s home, but in retrospect, I would have gone about things differently had I known better at the time. I noticed very high humidity soon after installation – so much so that the ridge foam was soaking up humidity like a sponge. I opened a couple of ducts into the attic and that seems to have solved the issue, although I have yet to install data loggers to confirm. However, the ducts into the attic did transfer the attic smell into the home which was unpleasant and probably unhealthy! Fortunately, after a few years the smell is virtually gone.
Funny how the insulation contractors tell you all the wonders of spray foam and totally ignore its pitfalls. I wonder how many rotted roofs we’ll be seeing in the coming years due to insulation contractors lack of knowledge or attention the important issue of attic humidity. I imagine very few homeowners ever go up into their attic after the spray foam is installed.
If I could do it again, I might still vacuum out the nasty 1960s insulation and seal the attic, but instead of spray foam, do a new roof with insulation boards on top of the roof decking. That would allow a higher r-value and avoid some of the issues that come with spray foam. One issue that I still need to address is sealing holes that the insulation contractor did not. But frustratingly, the globby nature of spray foam makes it very difficult to visually inspect for obvious holes in confined spaces. I think it would actually be easier to start with a bare attic and use canned foam and insulation board to seal up all the obvious holes.
Ken, yeah, encapsulating the attic with spray foam and then walking away, especially in a humid climate, is a recipe for disaster. Putting supply air in the attic is definitely one way to control humidity, but as you noticed, it pushes odors into the house. Here’s a nice article from Joe Lstiburek on this topic:
Cool Hand Luke Meets Attics
Ken, one way to locate holes or leaks is a thermal camera, they have become rather cheap over the past several years. I purchase a FLIR thermal imaging camera, premium cost supplier, that attaches to a mobile phone for $325 three years ago. It will make locating heat and cold escaping from your all areas or components of your home. Lots of uses for this device. You can get cheaper thermal cameras from other manufacturers.
Frank Hancock
302-547-7712
Ken: regarding the data logger, if you don’t already have one, I like this guy: https://www.amazon.com/Govee-Thermometer-Hygrometer-Bluetooth-Temperature/dp/B07R586J37/ref=sr_1_1_sspa — I have one that lives permanently at the attic ridge and I can take a reading via Bluetooth from anywhere in the house.
Thanks, Richard! The hygrometer you linked to is on an Amazon “lightning deal” right now for $12.50. I purchased one and will give it a try! If it works well for me I’ll buy several more for other locations in the attic and crawlspace.
Ken, let me know how you like it. I was leery about their accuracy but they both agree with every other temp/humidity measuring device I have at my disposal.
Richard, thanks for recommending these monitors. I have installed two in my attic and another two in my crawlspace. I have uploaded an image showing my current readings below:
https://ibb.co/vJNLfSL
Since installing the monitors, I learned that RH briefly spikes at as high as 80% or even 85% for 15-30 minutes at around noon and then spends 2-3 hours above 60% before retreating to about 50% for the night. This is with an AC supply duct opened into the attic and providing about 40 – 50 cfm. This is obviously too high.
After a bit more reading, I decided to take an alternate approach to the one described in Allison’s above article. Dr. Joe suggested a similar approach using an exhaust fan to move air from the conditioned space into the attic. In my case, I’m testing this by temporarily removing the ducting from a powder room exhaust fan at 50cfm. I also closed the attic’s AC supply duct so that I could isolate the effect of the exhaust fan.
I’ve now conducted this test for just 5 days (since 8/8) and the daily RH spikes appear to be on a downward trend (between 70-75%) even though the attic temperatures have been fairly consistent. The RH is also clearly reaching new lows during the night (about 5-7% lower than before).
There is not enough data yet to confirm that the fan has had the desired effect – and I would like to see the attic RH spiking no higher than 70% – but it appears this may be a viable solution to my years long problem of high attic humidity.
However, I wonder whether my strategy is having negative effects on the home’s indoor air quality as attic air gets pushed below the ceiling and into the main living space. I have not noticed a marked increase in attic smell (although I have caught a couple whiffs in a certain place in the home that I know has leakage between the ceiling and attic)
Allison: do you have any opinions on the strategy of exhausting the homes’ air into the attic compared to exhausting the attic air to the exterior?
We automatically include the cost of blower door directed spray foam quality control (2 guys; 3-8 hours) on all new construction and deep remodels for which we provide HVAC equipment or ductwork. We have the equipment and experience in house using it to locate, identify and seal (small gaps) in spray foam. Big gaps get outlined in embarrassingly prominent neon spray paint for the foam sub to remediate.
We carry three different embarrassingly prominent neon spray paint colors for those jobs needing multiple iterations of test – seal – retest – seal – reretest – seal.
If anyone balks (owner, builder, foam sub) we simply inform the team that without confirming the foam is substantially airtight, we are unable to guarantee ideal humidity control, comfort performance and moisture damage resilience of the project.
Our customers “get it”. Our best builder clients are those that have been burned in the past by costly moisture control failures and highly value the additional layer of protection our procedures provide. I regard it is such an important step that we would withdraw from a project if someone was dumb enough not to test and confirm infiltration performance.
Every now and then for extra credit we sub to mold remediation contractors in either or both of forensic and corrective roles.
Curt, thanks for showing the way to do things right! It sounds like it’s gotten easier for you to do all this because of something Joe Lstiburek told me years ago: “The gap between stupid and hurt is narrowing.“
Speaking of which… Your guys left a can of orange Krylon in my attic. I’ll make sure they take it home next time I call for service. 😁
I got inspired by this article and put z-wave temp + humidity sensors (logged wirelessly via SmartThings) in various places around our 3 year old custom build (that’s when I started reading this blog – learned so much and I drove our custom builder nuts … )
I was shocked to find out that in our open web trusses (between first and second floor) the humidity is 75-80 % at 76 degrees. I live in Houston, and dew points outside are around 75 right now and it has been windy the past days. Our house was insulated with BIBS (AC is in conditioned closet on second floor thanks to this website) and there are some tricky transitions at the rim joists where first floor roof lines hit second floor walls, but I made sure they were all closed (no big holes per Lstiburek) and the blower door results were about 2250cfm for 3800 sf at 10 ft height (I believe around 3-4 ACH50 which passed code here in Houston.
Do I have a problem (mold growth for instance)? Should I be concerned about dew points of 80% rH @ 77F in the truss cavity when the living areas below and above it are at 55 % rH @ 76 F?
@Robert, given the information you provided, I would question the accuracy of the RH logger located in the floor truss cavity. I suggest putting the logger that’s reading 55% beside the floor truss logger for comparison. Accuracy is a concern with low cost RH sensors.
If your truss cavities do have substantially higher RH readings (80% @ 77F = 70 degree dew point!), you need to hire someone who knows how to locate and seal those leakage paths! If you have any ceiling supplies mounted in the floor truss cavity, mold may be growing on the back the drywall surrounding the boots and on the backside of the boots themselves.
I have enjoyed very much reading your articles. I am a building a new home and want to make it as energy efficient as possible. We have planned to condition the crawl space and ventilate the house with an ERV. I was also looking at the attic being conditioned. No duct work in the attic. My HVAC guy is discouraging this because we live in zone 4A. Any thoughts on what we should do. Thanks.
Tom Lowry
@Tom, congratulations on banning ducts from your attic! Given that, I generally advise against directly conditioned attics. This not only adds considerable first-cost, but increases heating and cooling costs due to the increased exposed surface area and conditioned volume. An indirectly conditioned attic (insulated roof deck, no direct supply air) would have a lower lifecycle cost. In this case, the attic acts as a thermal buffer. This configuration makes the most sense when there’s no other way to get ducts out of the attic.
Vented attics generally have the lowest lifecycle cost, assuming the ceiling plane is field-verified tight. A lot depends on roof and ceiling complexity and roof pitch (i.e., surface area). If the ceiling is tight, a properly vented attic with a well insulated ceiling will outperform an encapsulated attic. It doesn’t cost a lot extra to exceed code-mandated minimum R-values when using blown-in ceiling insulation. One exception would be flat roofs, which inherently have poor ventilation characteristics.
Thank you very much. This solves my attic problem and concerns. Our crawl space will be very adequate. We plan to encapsulate and insulate the walls. All duct work will be located there. What would be the best way to ventilate and control the humidity? We were thinking about an ERV. Any better way? Roof is standing seam metal.
David, do you combine a wiring chase below these vented attics? I ask as someone who just added and (hopefully) sealed a bunch of Lessco boxes over slimline recessed lighting (and quite a few “regular” light boxes with all the attendant switch wires etc). As I crawled, swore and bruised, my mind returned to the decision not to create a conditioned attic (with insulation under a new metal roof), when we looked at the budget and said, “Ok, so we’ll establish the air barrier at the ceiling” …. So as I write I have a visceral appreciation of the effort needed to maintain the air barrier at the ceiling 🙂
So only chance I’d ever pursue a vented attic with blown in insulation again would be if there were both no ducts and no wiring in with the blown in insulation. So are you using a “plenum truss” for ducts, bathvents/vent hoods, with a wiring/lighting chase below the air barrier (ie sort of two ceilings), or are the ducts and wiring in a conditioned crawl space?
@James, as noted in my prior reply, an indirectly conditioned attic may be warranted if there’s no way to get ducts out of the attic. But I always try to find a way to bring ducts into conditioned space. For single floor slab-on-grade homes, I’ve specified drop-chases and built-up chases. Every house is different. Whenever possible, I specify ductless returns (i.e., no direct return ducts). This offers several advantages over fully ducted returns, not the least of which is that it makes it a lot easier to bring ducts inside.
Thanks for pointing out some of the challenges involved in air sealing a ceiling! I think most folks prefer to hire an experienced air sealing crew for that, but sometimes you just gotta do it yourself! And as I said, the decision to encapsulate depends among other things on ceiling complexity — i.e., how difficult/expensive it will be to get a tight ceiling.
Regarding recessed lights… I advise clients to use surface-mount fixtures wherever possible (LEDs offer many new options for that), but traditional ceiling cans (even AT rated ones) need to be covered and sealed with an air-tight cap (e.g., CanCap, Tenmat Recessed Light Cover, diy XPS box, etc.). OTOH, I don’t see why you’d want to run lateral wiring chases in the context of this discussion.
BTW, an important yet often overlooked detail is to seal the gaps between ceiling drywall and top plates (including interior wall plates). As the house settles, these gaps can become a major leakage path from the attic to the wall cavities.
David & Tom, an indirectly conditioned attic in climate zone 4A can create moisture problems. If you encapsulate the attic by putting the insulation and air barrier at the roofline, you have to do something with the air in the attic. That’s the whole reason for this article. As I showed in my previous article, the humidity in some encapsulated attics can be much worse than it is in mine. See Humidity in a Spray Foam Attic. The life cycle cost goes out the window if you have rip off your roof and replace it.
As David says, if you don’t have ducts in the attic, your best option is to insulate and air seal the attic floor.
@Tom wrote: “We plan to encapsulate and insulate the walls. All duct work will be located there. What would be the best way to ventilate and control the humidity?”
Not sure if you’re referring to house or crawl… Whole-house ventilation is beyond this discussion, but the ERV is a reasonable strategy. BTW, I strongly advise against relying on ERV as primary exhaust for showers or other high moisture areas.
Humidity control in a sealed crawl space is dictated by IRC Section R408.3 (unless trumped by state/local code). The IRC provides several options.
In reality, the need for humidity control in a sealed crawl varies greatly depending on site & foundation drainage, and how well the crawl is sealed (see note below). Keeping moisture out in the first place is always the best strategy. I recommend going with the easiest, least expensive option: adding a crawl space supply vent sized to deliver 1 cfm per 50 ft2 of under-floor area and a return air path to conditioned space (transfer grille or jump duct). Then monitor crawl RH and adjust the supply as needed ($5 balancing damper). In any case, you don’t want to use an ERV for a crawl as it will add moisture when the dew point is higher outside than in the crawl!
NOTE: Sealed crawlspace subcontractors love to sell dehumidifiers — they either don’t respect the client’s wallet or don’t have much confidence in their product. I advise clients to hire someone who will guarantee “leakage-to-the-outside” (typically verified by a 3rd party; requires 2 blower doors — one to test crawl and one to null leakage between house & crawl).
Your information was very helpful. I was referring to the crawl space which we are going to encapsulate. The house will be tight so we will need some kind of ventilation. Thank you very much.
Tom
I agree completely with David! The crawlspace on my 1960s home was professionally encapsulated shortly before I purchased the home. They did a pretty good job of the encapsulation, but it appears that they oversold the product to the widowed, elderly homeowner. They did NOT replace the rickety old (original?) crawlspace door which had a rotten frame and leaked like a sieve. Instead, they installed an expensive dehumidifier and sump pump. Additionally, they totally ignored the source of the problem: water infiltration due to poor landscape drainage.
After purchasing the home I spent quite a bit of effort improving the landscape drainage. Had this been done first, the urgent need for crawlspace encapsulation may have been mitigated. Additionally, I installed a well-sealed crawlspace door. I then unplugged the vastly oversized dehumidifier and the sump pump has not run since. I’ve monitored the crawlspace humidity levels with a cheap hygrometer and it constantly stays between 50 and 60%. I have not needed to supply conditioned air or install a return in the crawlspace.
The crawl space will be 2800 sq ft. Average height 5 ft. We will have geothermal HVAC will all duct work in the crawl space along with a tankless hot water heater. The house will be tight in the crawl space, out side walls of living space and ceiling of the living area. my majoer concern is ventilation in the living area and in the crawl space. Would a Ultra-Aire ventilating dehumidifier work in the crawl space.
@Tom, you do NOT want to introduce outside air into to a closed crawl space! Ventilation is for people!
One of the building code options for managing RH in a closed crawl is to install an exhaust fan with return pathway from the house. In that case, the fan “ventilates” the crawl with drier air from the house (see R408.3.2.1 @ IRC link in my previous comment). I recommend that option in retrofit situations where crawl has some residual nastiness from before it was closed.
In new construction, I recommend the supply air vent option because it costs less and is easy to adjust. The contractor may need to use a dehumidifier temporarily for the initial dry-out during construction, but as I stated in my previous comment, you shouldn’t need a permanent dehumidifier if everything is done properly. If the “supply air vent” option doesn’t keep RH under control, you can close the supply vent and install an exhaust fan. (Depending on how your stem walls are built, you may want to box out for an exhaust duct in case you later decide to switch to that option.) Permanent dehumidifiers should only be considered as a last resort!
Ideally, you want to keep RH in the crawl below about 60%, noting that short-term excursions as high as 70% are NOT a problem (since crawl is generally cooler than house). Folks who install humidifiers and set them at 55% or lower are just wasting energy!
BTW, if you have residual odors from construction (e.g., spray foam in rim bands), you can purge the odors with a high capacity window or floor fan. Ditto for the house itself. Run it several hours a day for a few weeks as needed. Pick and choose when to run the fan based on outside conditions.
Tom,
David covered what to do about crawl space air very well. Here’s an article I wrote in 2013 on this topic, with lots of good info in the comments there, too:
What Is the Best Way to Deal with Crawl Space Air?
Regarding dehumidifiers, Ultra-Aire is one possibility, but Therma-Stor, the company that makes Ultra-Aire, makes the Santa Fe line as well, and that’s probably what you’d want for the crawl space. Here are the links to the Sylvane pages for the two different lines:
Santa Fe dehumidifiers
Ultra-Aire dehumidifiers
These are affiliate links. You pay the same price you would pay normally, but Energy Vanguard gets a small commission if you buy after using the link. Here are the regular links:
https://www.sylvane.com/santa-fe-dehumidifiers.html
https://www.sylvane.com/ultra-aire-dehumidifiers.html
Thanks Allison. I have already read you article several months ago. With this fresh perceptive I am going to read it again including the comments. My HVAC seems very knowledgeable. I better understand the path I need to go and because of you and David, I now know the right questions to ask.
Thank you very much.
Tom
Thank you David. As you have probably surmised I am a novice at this. However after reading your notes and studying the IRC section R408.3 I am beginning to get a grasp of what I need to do. You have been very helpful and I really appreciate the advice.
Tom
I have a V2.0 for this concept. I put the return for my ERV at the ridge beam in my sealed attic. Yes I am now using the hottest wetest air in my house to precondition the incoming hot humid summer air from outside so I am minimizing my energy recapture in the enthalapic core, but I am pulling that hot humid air out of my attic while making the attic negative pressure relative to my house so more cool dry air is drawn through my can lights and sucked into my attic maximizing my goal of drying the attic out. Also, any concern about the attic air being “dirty” (weather that be from long dead possums or off-gassing spray foam) is addressed by putting it under vacuum and keeping that attic air out of my living space. You could do the same thing in a conditioned crawl and get more energy recapture since the crawl tends to stay cool. I like having these spaces negatively pressured relative to the living space.
@Russell, you could accomplish precisely the same thing with a low-cost ventilation fan and use your expensive ERV to much greater effect by exhausting from the house.
I might need to walk back my comment about the attic fan not increasing humidity in the house. With the weather warming and dew points rising, I’m watching the humidity plots rise a little faster than I’d like when the HVAC cycles off. I’ve disconnected the attic fan around 10AM and already seeing modest improvement.
Tonight I’ll put a WiFi-controlled switch on the fan and set up a daily program. To start, I’m thinking to run it during the hottest eight hours of the day and adjust downward if I can…
@David but then I would be putting the attic and entire house under net negative pressure rather than maintaining an overall balanced pressure like I am now
@ Russell, I understand your rationale but what strikes me is that you’re literally wasting the energy exchange core in this configuration. You already acknowledge this setup minimizes energy recapture, but you may actually end up with negative recapture at night when exhaust air may be warmer than outside air (note that Allison’s graph doesn’t show overnight lows).
OTOH, pulling exhaust from the attic in winter should yield a small recovery boost. So a lot depends on the climate zone. Either way, the additional cost of an ERV over non-recovery ventilation options doesn’t seem justified. (Allison: I’m looking at you buddy, and your pricey Zehnder.)
As for putting the house under negative pressure… a lot depends on relative size and tightness of house vs attic, and how much air your ERV moves vs minimum exhaust rate needed to maintain a reasonable attic RH. But if negative house pressure is truly an issue, methinks there are less expensive alternatives to accomplish the desired result.
In new construction or re-roof situations, I think a vapor diffusion port is the obvious solution. The 2021 IRC provides for this option, whereby one can use low-cost fiberglass instead of SPF to insulate the roof deck.
David, you make a good point about the heat recovery going in the wrong direction at night. In my case, the nighttime lows are usually around 70° F and the attic drops to about 75° F at night, so yes, we’d be keeping some of that heat in the house during the nighttime exchange. The daily balance should still be positive. The winter exchange would definitely be positive as the attic temperatures are often in the 70s. Also, we do more heating than cooling here in Atlanta.
My plan for the ERV is to have most of the exhaust come from the living space, but now you’ve got me rethinking that. I might still put some ERV exhaust in the attic but have a backup plan that makes it easy to move it to the living space. Also, my shingles have about 5 years left in them, so maybe I’ll install a vapor diffusion port when the time comes for a new roof.
David, I guess we really need data to sort this out. I can say that with my T-stat set to 70 and a high today of 94 my attic temp peaked at 80 so I’m not loosing all my hard won temperature differential. I had not thought of the ERV working against me at night, interesting thought but the low tonight will be 74 so that would not happen tonight anyhow. I am not familiar with a vapor diffuser port, but it seems to me that would work against me with the humidity here. Am I missing something? wouldn’t it let humidity in as easily as it lets it out? If my attic humidity matched the outdoor humidity I’d have a serious mold problem!
@Russell wrote: ” I guess we really need data to sort this out”
It doesn’t really matter if you end up with a somewhat positive or somewhat negative recovery efficiency over time. My point was specifically regarding cost-benefit. There are better (i.e., lower cost) alternatives to address high humidity in encapsulated attics.
I’ve done enough modeling of ERV’s to know that even if one assumes rated efficiency numbers, cost-benefit is often marginal in warmer climate zones, especially for higher-end models like the one Allison referred to. Keep in mind that HVI certified ratings only apply at the rated conditions. I’ve attempted to model SEASONAL recovery efficiency using TMY bin data and it’s not pretty. (I say ‘attempted’ because manufacturers are reticent to disclose efficiency data beyond a couple of operating points. This is especially a problematic for warm-humid climates where performance is a function of absolute humidity differentials in addition to just temperature.)
You’ve already invested in the ERV but I wouldn’t recommend this approach to those considering their options.
Allison,
Apologies if someone has already said this – I did a quick scan and may have missed it. But it seems like the better (or at least another) way to look at the relationship of indoor RH and outdoor conditions would be to plot the relationship of average humidity (or daily peak, or both) against outdoor humidity (and maybe also outdoor temperature) in an x/y scatter plot. It might reveal more (or less) of a relationship than is visible with the time-axis plots you have. Also (and I haven’t thought this through) – when it’s hotter in the attic the same RH represents more moisture – maybe instead of RH or even dewpoint it might be worth looking at the attic air humidity ratio. All this is also complicated by the fact that the indoor air conditions may affect what’s happening, since the attic is better connected to indoors than out (and the makeup air from the exhaust is presumably mostly from indoors) – though presumably indoor conditions are fairly steady.
Hmmm….does anyone just put a dehumidifier in a sealed attic?
John, yes, using a dehumidifier is the safest way to control humidity in an encapsulated attic.
Allison, I’m glad to see this comment!
First, thanks for your great work and articles.
Your 2016 article on humidity in spray foamed encapsulated (I have a bone to pick with the term conditioned) attics deals mostly open cell foam, and moisture from the outside. I’d like to see you readdress the issue re: closed cell.
We had our 1967 house crawl space and attic encapsulated with closed cell and air sealing work done and replaced the second-story attic-installed gas furnace/AC with a heat pump in 2014-5. I’m now (long overdue) resolving trapped humidity problems; boundary layer pushed below the ceiling into the second story and the AC not adequately handling the humidity (wife NOT HAPPY about how the encapsulation just made things worse!), insulation on supply ducts saturated with condensate and dripping and puddling on the sheetrock.
We had also had an inline (“whole house”) dehumidifier installed on the main HVAC unit in the basement, with explanation that “like the smell of burnt toast”, moisture will be evenly distributed throughout the house. Nice theory. But the evidence does not bear it out.
Here’s my bone. A encapsulated attic will condition the temperature, but not the humidity, so it does not fulfill my definition of conditioned.
We are in the process of having another in-line dehumidifier installed in the attic (with fresh air supply this time, though it’s a poor solution for make up air), and will condition the space with 4” return and supply on either end of the attic. Fingers crossed and knocking on wood that it works, or y’all might have come visit me at the morgue.
My friends are also laughing at my efforts to be more environmentally conscious, as I suck up more and more electrons.
Kind regards,
Lander, a fellow Atlantan
Lander, I agree, the term ‘conditioned attic’ is problematic. Encapsulated attics aren’t ‘conditioned’ without thermostatic control with at least one supply and one return. But before sucking up even more electrons chasing symptoms with expensive mechanical solutions, you should first try to identify the moisture source and go after that!
> insulation on supply ducts saturated with condensate and dripping and puddling on the sheetrock.
Sounds like a LOT of moisture! I agree with Curt… A blower door test (along with zonal pressure diagnostics) would likely to reveal that all that moisture is coming from the outside. You seem to be throwing encapsulation under the bus when it may simply be a poor implementation. Did your spray foam contractor QA their work with a blower door? Even the best crews miss stuff! Foam insulators who test their work as a matter of course quickly learn from their mistakes and don’t unknowingly leave customers with a botched job. Those that don’t have no clue.
Interior generated moisture (baths, cooking, laundry) shouldn’t be a problem if spot ventilation is used to good effect, and working properly. When you arrange for that blower door test, ask the technician check your upstairs bath exhaust fan(s) and verify that the exhaust ducts are leak free.
Lastly, I definitely would not add outside air to the attic. In summer, that would just add fuel to the fire. If all else fails, you might consider installing a low volume exhaust fan in the attic with a passive make-up air path to the upstairs conditioned space.
I get the objection to calling a foamed attic “conditioned space”. Florida code calls it “indirectly conditioned” space…it is considered conditioned because it is within the pressure and thermal envelopes, but it is indirect since it is not actively conditioned.
Given your reports, I wonder just how air tight your foamed attic really is – I often encounter condensation / dewpoint fails on ductwork in foamed attics where the foam was never tested / controlled for air tightness.
If you can’t get the foam substantially air tight, such as by blower door-directed testing, then yes it is likely you may need not a whole home dehumidifier but one dedicated to the attic space. As our climate relentlessly becomes more humid, I’m seeing need for this more and more often.
It may also be worthwhile to check amount and integrity of your ductwork and whether it is adequately sized as well as system-developed temperature split – target is for supply air to be ~20 degrees cooler than return air. Temp split much below 20 won’t dehumidify properly in the course of cooling, and temp splits higher than 20 risk dewpoint fails and inefficient operation.
Curt and David,
Thank you for your thoughtful replies!
I’m still very much a proponent of encapsulated attics (and an evangelist for encapsulated crawls). It’s just been a frustrating journey (plus the angry spouse thing…)
We’ve had several blower door tests; pre- and post work. But it’s worth having it done again with IR camera expressly focused on eaves.
Can’t look at the upstairs bath exhaust ducts as they were, though they have been visually inspected several times. Both fans (one the original small builder grade with screeching bearings) were replaced today and new hard ducts installed.
Heat pump’s temp split measured today – I was told it was in spec.
We are not adding outside air to attic directly; it comes through the in-line dehumidifier first.
Pretty sure you are right about infiltration air as primary source of humidity. I stated 1967 to give a clue of general construction practices of the era. Also, when we first moved in we were told this was the builder’s house. We thought that sounded good, but quickly learned that was code for – the construction is crap. built quick for them to live in for 2 years before they move on.
Last week we discovered water leakage in a first floor ceiling/wall. I called in a water/mold remediation specialist. (Turns out master bath wax ring had failed.) After they pulled off the sheetrock and insulation, it was worse than I feared. I had long suspected the 1st/2nd story joist band was a sieve; there is a balcony across the front of the house. There is not even blocking b/t the joists; sheathing -> interstitial space. I hope there is a way I can share pictures. This part of the conversation should be cross posted to the latest article about where to put the air boundary!
L
Upper story floor support systems (what you called “the 1st/2nd story joist band”) are notorious for being poorly sealed as to outside air infiltration and thus become a large source of uncontrolled hot/cold/humid outdoor air leakage problems. In hot humid climates they become even more problematic since the air sealing fails put very high dewpoint air in contact with HVAC ductwork whose installation is often compromised by floor support system structural conflicts…and such ductwork is difficult to access and correct after construction.
For more on this Google “windwashed floor systems”
@Lander, still unsure why you’re adding outside air to the attic. You’ll end up spending more energy running the dehumidifier (than without outside air). In my mind, the only reason to introduce outside air into an unoccupied space would be for drying purposes.
The outside air is fed into the dehumidifier, which feeds into the house supply.
Also, because the attic is part of the house’s interior enclosure it is no longer “unoccupied”.
Allison,
I’m looking to build a cabin in Pinetop, Arizona (IECC Zone 5, Köppen zone Csa, elevation 6,900 feet) using Perfect Wall / Perfect Roof principles with Everlog concrete siding furred out from ZIP R-12 sheathing.
Can I do open-cell foam between the 2x6s on the interior side? If so, can I spray against the polyiso, or do I need something between as a substrate? I couldn’t glean whether I could from Joe Lstiburek’s Clever Wall section. I appreciate your input.
@Jason, yes, the foam can be sprayed on the polyiso, but I would ask this: Since the ZIP system is an air barrier, there’s no benefit to using open-cell foam in the cavities. Why not use cellulose or blown-in fiberglass (i.e., BIBs)? 5.5 inches of blown-in fiberglass yields around R-23 in the cavity, a bit higher than open cell foam, and costs less.
I came across this post after I had the thought to install a bath vent fan in one of my 5 different attic spaces (3rd floor finished attic), specifically the SW corner isolated attic (no HVAC or duct work). The SW and NW attics get the most continuous sun exposure and the humidity is problematic (reaching above 85% in the SW attic). I found that in February here in Houston TX on the weeks that were clear and sunny the problem would become very noticeable (solar vapor drive ping-pong effect is real for me). My home only has R21 open-cell but I’m pushing to get that up above R30 with my builder now.
I found an 80CFM .8 sones humidity sensing bath fan with internal timer at costco and decided to install it. I tied into an existing bath exhaust duct via a T (with backdraft dampers) to minimize holes in my exterior. I spent some time tuning the humidity threshold and run timer but the results have been profound. Where in February the attic would reach over 85% on really sunny days (I had readings above 90% last year), post fan install and tuning it is peaking at 65% and dropping below 50% at night (on roughly the same exterior conditions).
I still have some more tuning to do with the threshold and I need a good high outdoor humidity day (been cool and dry this past month) to be sure it is pulling air indirectly from the interior. I’m optimistic it will be the solution and I will likely reproduce the setup in the NW and SE attics.
Stephen, I agree with Curt on this. I’m in the same climate zone with R21 open cell under the roof deck. I have a wireless hygrometer up at the ridge and I have never seen it read anywhere near 80% RH. I might get a spike to 70% on occasion but it’s normally under 60%. I reckon you have a leak somewhere…
Has your attic foam been checked for airtightness?
Every new construction, addition and deep remodel project for which we provide HVAC services includes mandatory blower door assisted envelope airtightness verification with particular attention paid to foam – We do this in house – our duct guys enjoy time off from ductwork.
Once foam crews get used to their work being tested, they tighten up!
My home did have a blower door test done and passed quiet well. I actually believe the issue with the SW attic’s high humidity is residual moisture present in the roof decking post construction due to the tightness of the home. I know it is solar vapor drive causing the humidity to rise and fall as it aligns to when the sun is hitting that side of the home.
The SW attic is also right above a full bath and laundry room and I could see some additional load occurring due to that. I have since put in a whole-home dehumidification system to manage interior humidity. I believe the initial venting of the humidity at startup of the fan has addressed the egregiously high humidity in the attic.
The above said, the spray foam job could use some work (few low/high spots but all above 4”) but I don’t believe there is actual infiltration into the space.
Two houses ago we had an attic storage area with closed cell foam – despite humid north Florida locale we did not have moisture problems up there. It ran maybe 5-10 degrees above indoor temp in summer and maybe a few degrees cooler during what passes for winter in our area.
The foam was so effective that we were quite lazy about closing the attic access folding stair assembly – we often left it down / open for weeks at a time.
As a precaution, I specified a smoke detector for that space.
Ok, so here are my thoughts on this. Once sprayfoamed, the attic becomes part of the interior envelope. If there are ducts and HVAC equipment in the attic, they generally become more efficient. We typically see HVAC companies specify less tonnage for a sprayfoamed house. A logical alternative would be to install a small positive air vent and a small return in the attic from what may now be a slightly oversized HVAC unit. Somebody else mentioned how leaky ducts reduce the humidity. By adding a small vent and return, you are accomplishing the same thing. You just need to make sure that the additions do not divert too much air from the house. I’m not an HVAC expert, but a couple of turns a day should be sufficient to keep the humidity the same as it is in the house.
Another important point is that sprayfoamed attics are cooler than traditional attics. Much cooler. So if an attic is sprayfoamed in the summer, the temperature will drop, but relative humidity will stay high because the cooler air can’t hold as much moisture. Once enclosed, the moisture is trapped and can only escape through aspiration into the home. This process can be accelerated greatly by putting a dehumidifier into the attic temporarily until the humidity in the attic is close to the humidity in the house. Once the humidity level drops, it will not return in a properly sprayfoamed attic.
In my experience the issue is a bit more complicated than that:
1) Closed and open cell foam respond differently to humidity – There’s a doc at Joe Lstiburek’s building science website that discusses sheathing rot attributed to foam moisture retention.
2) Actively conditioning a foamed attic may trigger additional fire protection code scrutiny…such as having to install drywall over the foam
3) No foam job is perfectly air tight – some outside air leakage is inevitable, especially in the case of retrofits
4) We are more and more often having to retrofit dehumidifiers into foamed attics, open cell in particular, especially in beachfront houses – they experience significantly higher average wind speeds.