Does Spray Foam in the Attic Make It a High-Performance Home?

Ten years ago, Georgia led the United States in adopting a new energy code. Perhaps the biggest advance was that it required all new homes to meet a threshold for airtightness (7 ACH50). Now most states require blower door tests and the threshold is generally in the 3 to 5 ACH50 range. Unfortunately, Georgia has fallen behind. It took us seven years to update the energy code. When we did, we increased the airtightness requirement, but not as much as the International Energy Conservation Code (IECC), and we opted out of better insulated walls. Yes, we still allow R-13 2×4 walls in new homes.
We did improve the attic insulation, though. The new state energy code requires R-38 attic insulation statewide. Further, because the code also requires better windows, home builders can’t get homes to meet the code with R-20 spray foam insulation on the roof deck without demonstrating compliance through what’s called the performance path (section 405 in the IECC). They had been getting this lower level of attic insulation approved with a simpler method called the total UA alternative. In other words, they could get a lower insulation level for the attic to comply by using better-than-code windows, which builders were doing already anyway.
Georgia’s R-20 spray foam amendment
Fast-forward a couple of years, and now builders want to go back to the simpler days of getting R-20 spray foam insulated rooflines to pass automatically. To do so, they’ve got an amendment up for adoption that would automatically allow R-20 impermeable insulation (i.e., spray foam) if they meet three other stipulations:
- Increase airtightness from <5 ACH50 to <3 ACH50
- Install whole-house mechanical ventilation that’s not exhaust-only
- Cover the rafters with a minimum of R-3 insulation
This amendment would make it a prescriptive requirement to put R-20 spray foam insulation on the underside of the roof deck. That’s the easiest way to pass code. Check the four boxes (the three above plus R-20) and you pass.
Does spray foam equate to high performance?
In talking about the amendment with supporters, I heard people say that encapsulating an attic with R-20 spray foam makes it a high-performance home. Fifteen years ago, I would have agreed with that statement. Now, not so much.
Does spray foam in the attic make the house more airtight? Maybe. Does spray foam in the attic lower the heating and cooling load of ducts in the attic? Probably. Is R-20 enough? No.
We’ve done some modeling on what it takes to get R-20 spray foam encapsulated attics to pass the current code, and they just barely make it…sometimes. Here’s what I wrote about that in my letter opposing the amendment:
The performance path in the energy code, section 405, may allow some homes to pass, but based on our examination of this method, it’s very close. We modeled two house plans of a local builder. One passed, and one failed at 2.99 ACH50. The one that passed came in at 0.3% less than the required threshold. (The floor plans modeled are 3,200 sf with R-20 insulated roofline, 14.5 SEER air conditioner, 96.1 AFUE furnace, and ducts in the attic.) Those same house plans with an air leakage rate of 4.99 ACH50 miss the threshold by more than 10%.
If R-20 spray foam attics are that close to the line of a barely-legal—uh, I mean, code minimum, you’ve gotta really stretch to call that a high performance home. Yeah, they’ll have a bit more airtightness, get mechanical ventilation, and have a bit of insulation on the rafters. They’d be doing the first two of those things anyway if Georgia hadn’t weakened the IECC requirements in those areas.
But come on. High performance? No way!
Spray foam isn’t a miracle product
I like spray foam insulation. I have it in my house. My attic is encapsulated with open-cell spray foam. My crawl space is encapsulated with closed-cell spray foam on the band joists. When it’s done properly, it definitely helps with airtightness and makes it easy to reduce the loads on ducts in attics.
Not all spray foam is done well, however. We get a lot of calls from people who had spray foam insulation installed in their attics and have problems with odors, humidity, or heat. The most popular article I’ve written here in the Energy Vanguard Blog is 4 Pitfalls of Spray Foam Insulation. It’s been viewed 14 thousand times this year already and millions of times since I wrote in 2010. If people weren’t having trouble with spray foam insulation, this article wouldn’t be so popular.
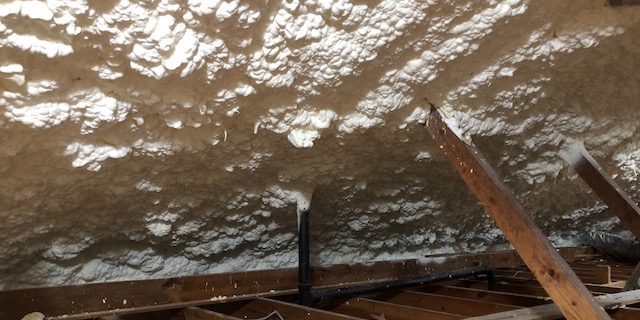
Take my house, for example. My wife and I bought it from my father-in-law two years ago. He’d had the attic encapsulated with open-cell spray foam insulation in 2012. A couple of years later, he had to hire another contractor to deal with the moisture and mold problem that resulted from the very bad spray foam job. When I moved in, I had a lot more spray foam installed to bring the attic up to R-40+, and it reduced the air leakage of the house by 22%. (Stay tuned for articles on the before and after conditions.*)
Spray foam insulation isn’t a miracle product. In fact, it often suffers the same problem for which spray foam contractors bash fiberglass: poor installation. Worse, bad spray foam installers can create more serious problems for homeowners than bad fiberglass installers.
Is R-20 in the attic ever enough?
When it comes to new homes, my answer is no for almost everyone. My one exception would be homes in mild climates that need little heating or air conditioning. I’m thinking of places like Santa Monica, California, but even then, I’d have to look at the data.
Where an R-20 encapsulated attic does sometimes make sense is for existing homes. If a homeowner has a set budget for improvements, using some of that to do R-20 spray foam on the roofline can provide a lot of benefit if ducts are in the attic and if it reduces air leakage significantly. I was a home performance contractor from 2004 to 2007, and that was one of the things we did.
But no house with an R-20 attic should ever be called a high-performance home. You’ve got to be at R-30 minimum just to be in that conversation. R-20 should be the minimum for walls. (I need a cartoon here based on the old Trix cereal commercial that says, “Silly rabbit, R-20 is for walls!”)
The case against an R-20 attic also includes what we learned from Texas this winter. A home with only R-20 will become unlivable much faster in the case of a power outage than would a house with a fully insulated attic. With more and stronger effects of climate change showing up every year, we should be requiring new homes to be more resilient, not less.
The sum and substance of this issue is that spray foam insulation was allowed to have a lower R-value 20 years ago because of two things: It made a significant difference in airtightness and it could bring ducts inside the building enclosure. Now, all new homes have to be airtight (well, OK, not in Mississippi) so spray foam insulation shouldn’t get this pass anymore.
Allison Bailes of Atlanta, Georgia, is a speaker, writer, building science consultant, and founder of Energy Vanguard. He is also the author of the Energy Vanguard Blog and is writing a book. You can follow him on Twitter at @EnergyVanguard.
* We had the additional open-cell spray foam installed by Woodman Insulation using SES open-cell spray polyurethane foam, and they did a great job. In full disclosure, they did provide this to me at no cost.
Related Articles
4 Pitfalls of Spray Foam Insulation
Spray Foam Insulation at the Edge – A Forensic Analysis
Humidity in a Spray Foam Attic
NOTE: Comments are moderated. Your comment will not appear below until approved.
This Post Has 22 Comments
Comments are closed.
I can relate to this article after living in my home for seven years. The home has R-22 blown in cellulose into Insulweb netting under the roof. I live in Arizona, a Pulte built home in a Del Webb community. The home on paper is supposed to be Energy Star and a HERS rating of 60. During the late spring early summer, when outdoor temperatures are between 70 and 100, the thermal performance is OK. But during the high summer heat from June thru August, the insulation underperforms. I wish the builder had used spray foam to at least an R-40, covering the truss cords to lessen thermal bridging. The one downsides to cellulose, inconsistencies in dense packing the cellulose in each truss bays and overall sloppy work by the insulation contractor, leads to performance issues too. Given my high summer cooling bills, my home is anything but high performance. While my home is more comfortable and certainly much more air tight when compared to my previous 1996 home in northern California, we need better building codes and better workmanship by contractors employed by production home builders.
Scott, poorly installed R-22 cellulose under the roof deck would be worse than properly installed R-20 spray foam. If the cellulose doesn’t completely fill the cavity and air is able to move from the space below to empty pockets at the roof deck, convection can transfer heat from the roof deck to the attic. From what you describe, it sounds like that may be what’s happening in your house.
As you noted, it’s important to differentiate between the question of whether R-20 on roof is ‘high performance’ (I’m dumbfounded that anyone would actually say that!) and the question of whether it makes sense to treat this assembly differently than ceilings + vented attic. Clearly these assemblies are different animals in terms of the impact on thermal loads.
I would support an amendment to the IECC that adds encapsulated attics to the prescriptive R-value table for hot CZ’s with somewhat reduced R-values for air impermeable insulation on the roof deck. Given Georgia’s R-38 prescriptive code for ceilings, I would support R-28 as the legal minimum for insulated roofs.
You wrote: “no house with an R-20 attic should ever be called a high-performance home. You’ve got to be at R-40 minimum just to be in that conversation.”
I’m not sure I agree with that, at least for CZ-3. Case in point… I live in CZ-3B (SE Arizona) and I’m *very* happy with the performance of my own recently built high performance home with R-34 ocSPF on my unvented flat roof. The walls are R-26 (5.5″ BIBS + 1″ EPS).
The house has 3,300 ft2 conditioned floor area including finished basement, and has a single 1-ton heat pump (4 zones), straight electric DHW, and 3.84 kW PV that works out to about 125% net positive (7600 kWh/yr produced, 6100 consumed, based on 2 yrs of data). The only fossil fuel I use is for a propane backyard grill. I haven’t installed a circuit level monitoring system (yet), but I estimate heating & cooling consumption is roughly 1800 kWh/yr.
David, because I know you and your maniacal attention to detail, I certainly have no argument with you calling your house a high-performance home. I can see even an R-30 insulated roof deck being considered a high-performance home if, as in your case, the walls have significantly more insulation and the total UA is low. But R-30 SPF on the roof deck and R-13 walls wouldn’t cut it in my opinion.
David, after thinking more about it, I changed the part of the article you quoted. I now say R-30 should be the lower limit if you want to call it a high-performance home.
David, just for clarification you have a 1 ton unit serving your entire 3300sqft or 4-1 ton units? Even the latter is commendable… Also did you have a blower test done?
@LeeH, yes, just a single 1-ton system for the entire house. It’s a Carrier 18VS 5-stage heat pump. To answer your other question, the house tested out at 0.52 ACH50.
BACKGROUND: Professionally I design mechanical systems and envelope specs for high performance homes, so 2000 to 2500 ft2 per ton are routine for my projects. But 3300 ft2/ton was a record even for me. I designed this house specifically to work with the 1-ton 18VS — it’s the only non-mini-split inverter based heat pump available under 2 tons.
Although my load calc modeling and all of my experience said this would work, admittedly I was a bit nervous. But I had a fall-back in case it didn’t work: I can cut the roof load in half by applying a high reflectivity coating to the flat roof. Fortunately that won’t be necessary (it would cost ~$2k). The first summer we were in the house, it hit 104 degrees two days in a row. The main level slipped 1 degree above the 77F setpoint, pretty much what I expected.
We live in rural SE Arizona at 4400 MSL. Because of the higher elevation, we’re not as hot as Tucson but we typically see 100 several times each year. As it turns out, the system will maintain 77 degrees at 100 outside. Since I let our bedroom zone float during the day, it takes 2 to 3 hours in the evening to reach our preferred nighttime setpoint of 73. In winter, the heat pump alone can hold 69 or 70 when the ODT drops into the mid-20’s. I installed a 3kW strip kit as it occasionally drops into the low 20’s and teens.
The simple conduction analysis for insulated roof decks vs. ceilings is interesting. The roof area is higher than the ceiling area below it so you need a higher R-value for an insulated roof than you do for an insulated ceiling for equivalent conduction heat transfer, all else being equal. So if you want the equivalent of an R40 ceiling on a house with a 9/12 pitch roof, you need R50 on the roof deck. So how does one get away with R20 or even R30 for the roof deck when R38 is required for the ceiling? As mentioned in the article, when you insulate and “seal” the roof deck with spray foam, you don’t have to worry about sealing all of the ceiling penetrations like plumbing, wiring, can lights, access holes, etc, so it is easier to make a “tight” house. As also mentioned, if the ducts are in the attic, their losses will be significantly reduced with an insulated roof deck compared to a ventilated attic, so that helps. What about the temperature in the attic being different than outdoors with an insulated ceiling? It depends on how well the attic is ventilated, but it probably hurts in the summer but maybe helps in the winter since a vented attic is typically warmer than outdoors during the summer and winter? So has anyone tried to quantify these secondary, but probably significant effects to see what insulation level for the roof deck is really needed to be equivalent to the level required for an insulated ceiling?
I do have an insulated roof deck and I love it. I don’t know why anyone would do anything else. Some of the other advantages are that it is easier to service air handlers in the attic and run new wiring to the rooms below when needed. It also gives me a lot of extra storage space without the risk of melting my Christmas ornaments in the summer.
@Roy, if you move the ceiling R-value to the roof, the thermal impact on conditioned space will be less, even though the surface area is greater. This is because the indirectly conditioned attic acts as a thermal buffer.
The heat flux through the ceiling depends on the delta-T across the ceiling plane and the u-value of the ceiling assembly. In summer, a vented attic will obviously have a MUCH higher delta-T across the ceiling than with an encapsulated attic. If you do the heat transfer calculations (assembly u-value * delta-T), you’ll find that the heat transfer through an uninsulated ceiling with, say, an 8 degree delta-T is lower than with the same R-value applied to the ceiling under with the typical delta-T for vented attics. This is why it may not make sense to apply the prescriptive R-value for ceilings to the roof.
If you directly condition the attic so that the temperature is equal (or close) to the rooms below, the ceiling heat flux disappears but the overall load on the AC will be larger.
From an energy cost-benefit perspective, the rationale for an encapsulated attic depends largely on roof pitch and ceiling design (i.e., difficulty of achieve a tight ceiling), and whether attic-located HVAC can otherwise be avoided. When the house is specifically designed to accommodate interior HVAC, it becomes difficult to justify the additional cost of foaming the roof deck compared to a vented attic with a high R-value, tight ceiling.
David, it sounds like you are agreeing with me, but using different words to say it 😉
Thermally, I agree that if you get the ductwork out of the attic and can make the ceiling air tight and can provide sufficient ventilation to the attic, then insulating the roof deck instead of the ceiling might not make sense, mainly because it is cheaper to pile loose insulation on the ceiling compared to spraying “tight” insulation under the roof deck. But there are still the other benefits to an encapsulated attic like useable storage space, access to wiring and plumbing, less severe temperature and humidity swings on the attic framing, etc.
@Roy, agreed there can be reasons other than economics for why someone might want to pay extra to move the thermal boundary to the roof. I was just answering your rhetorical question: “I don’t know why anyone would do anything else.”
Roy, I’ve spent many hours over the past two years in my encapsulated attic. I’ve also deployed HOBO data loggers and will have an article soon showing my data. As I mentioned in the article, my attic was nominally R-20 when I moved in and now it’s R-40+. The difference in attic temperature between those two levels is significant. That means less cooling load on the ceiling below and less load on the ducts that are in the attic.
I don’t know of any formal studies showing the effects of different R-values, but that would be valuable research.
I was wondering if I might ask a somewhat off-topic question. For an existing home with HVAC and ducts in a vented attic in Allison’s neck of the woods, any thoughts on spray foam on the roofline vs. putting spray foam on the ducts to provide both sealing and better insulation? I’ve seen this latter service offered locally and mentioned on a Dept of Energy blog. I believe the cost for each would be similar. Current ceiling insulation is cellulose to code as of 2000. Ductwork is fairly leaky. (And I don’t really need attic storage space)
No need for an answer to my specific situation, but spray foaming attic ducts might be an interesting blog post (unless already covered)
Just curious…. At what roof slope does an insulated roof become an insulated wall? Would you put R40 in a wall in your CZ?
The high performance homes I work on in the PNW tend to have R-49 flat attic insulation w/ some builders moving up to R-60. R-38 floors and R23 walls are also common. Our new code that kicks in this Oct will require .27 U windows and a version of “ducts inside” that allows for “partially buried ducts under attic insulation” which they borrowed from the 2017 DOE ZERH program. For insulated vaults our code requires R-38. If a builder wants to do an unvented assembly our code requires R-20 of impermeable insulation at the roof deck which can be sprayed from below (most common) or rigid foam board on top (which hardly anyone does). In my opinion, this code aligns nicely with the building science that says this a good way to avoid condensation, but I’m glad we require additional R value to meet energy efficiency goals as well. I’ve always thought the best place to increase R values is the weakest point of a given envelope. In almost any climate / state building code that’s the windows.
Here in California, we have Title 24 energy requirements updated as of Jan. 1, 2020. There are two spec’d-out options. Here is a good reference from Johns Manville: https://www.jm.com/content/dam/jm/global/en/building-insulation/Files/BI%20Toolbox/102219_BI_BID_285_CA_Title24_SingleFamily.pdf
(1) Prescriptive Path –Vented Attic : R19 min below roof deck. R38 min ceiling.
(2) Performance Path – Unvented Attic: R22 min below roof deck.
The discussion above seems to be an either/or choice: either you insulate the roof deck on a unvented/conditioned attic or you insulate the ceiling only for a vented attic.
For a vented attic (I am considering using a whole house fan in our area), I would be interested to know your thoughts on insulating both the ceiling and the roof deck vs. a high R-value (e.g. R50+) ceiling only (assuming the house passes the Title 24 calculations). One other consideration – my understanding is that radiant barrier roof sheathing will not work either with either spray foam roof deck insulation or fiberglass since the insulation provides a conductive heat path into the attic.
@Kent: to respond to your questions, please post your CZ, whether this is new construction and whether ducts will be in the attic…?
You wrote: “The discussion above seems to be an either/or choice: either you insulate the roof deck on a unvented/conditioned attic or you insulate the ceiling only for a vented attic.”
That’s not correct. Vented attics in CZ 4, 8-16 must have insulation on the roof deck AND ceiling if ducts are in the attic (or follow performance path). If you don’t live in these CZ’s then I agree with what you wrote. (I’m guessing you live in CZ 4, 8-16 since the prescriptive path requirements you quoted only apply to those climate zones.)
BTW, although unrelated to your question, the JM pdf has an error of omission…
JM’s Prescriptive table omits the following requirement to qualify for ducts in conditioned space (Option C) : duct leakage to the outside must be verified at <15 cfm. Otherwise the JM table is a very good representation of the 'uglier' Figure 3-23 in the 2019 Title 24 Compliance Manual.
Thank you David for this information.
This is new single story construction in CA CZ 4 – a semi-arid/Mediterranean low humidity climate. In July and August, it is not unusual to experience a 40 deg F temperature swing from high to low. Hence the reason for using a whole house fan in a vented attic to draw in cool outside air starting around 8 pm and exhaust it through the attic. In winter, this cycle can be reversed in the morning.
CZ 4 is also ideal for a heat pump, either ducted or ductless or some combination. The refrigerant lines can be run to attic air exchangers, then ducts into the rooms or the lines run straight into ceiling or wall-mounted units. Any ducts would be R8 and meeting the leakage requirement.
Option B is the data that I have been looking at, but I do not understand why a radiant barrier roof sheathing will work with a fiberglass shingle roof. To reflect heat back out of the attic, there needs to be an air gap to break conduction heat transfer. If SFI is tight up against the decking, the heat will conduct through.
The other consideration is cost – there is a significant labor cost to insulate both the roof deck and the ceiling (especially with SFI). I thought that as long as the Title 24 energy CBECC-RES calculations (and perhaps Manual J) passed CA requirements, you could insulate a vented attic without following a prescribed option – which for me would be radiant barrier decking with all of the insulation in the ceiling (R50+).
If you go with prescriptive Option B (high performance vented attic), you must install R-19 on the underside of the roof deck (to dampen duct gains). In my opinion, it would be silly to use SFI in that case. Option B also requires an air gap between shingles and roof deck. That’s easy to do with tiles or metal roofing but I think a second roof deck would be necessary to support shingles. Ouch.
BTW, I’m not sure why you questioned the benefit of a radiant barrier in the context of Option B since it’s not required (see JM table). As you noted, radiant barriers provide no benefit if covered with insulation.
You can ignore the prescriptive requirements and instead demonstrate compliance via CBECC-RES software modeling (i.e., performance path). In that case you can install the shingles directly on the roof deck, omit the R-19 roof insulation and go heavy on the ceiling insulation. I’m not convinced a radiant barrier would be cost effective in your climate, but if you insist, go with TechShield roof sheathing, which has an integral radiant barrier. Separately installed radiant barriers are never cost effective.
All of that being said, it’s always best to to accommodate HVAC inside the thermal envelope (Option C). Depending on the home’s design, it’s usually possible to accomplish that without resorting to an unvented (encapsulated) attic, which adds unnecessary cost. But if that’s the only way to bring the ducts and air handlers “inside”, you can still have a whole house fan. For example, Tamarack manufacturers a line of ducted whole-house fans.
Thank you David for all of this valuable information!
You’re welcome! If you intend to go with Performance Path ( CBECC-RES software modeling), be sure to have a HERS rater to run the model early in the process so you can change directions if necessary. For example, due to diminishing returns, you may discover that simply doubling up on ceiling insulation may not be sufficient to get you below the Title 24 whole-house energy budget.
Also, regardless of what the HERS energy model says, if you go with a vented attic, make sure the ceiling is properly air sealed. It’s not just a matter of sealing all the penetrations — the joints between the ceiling drywall and interior wall top plates need to be sealed with spray foam or other suitable sealant such as Knauf Ecoseal Plus.
Hey Allison, great article. I actually came across your blog from your popular article “4 Pitfalls of Spray Foam Insulation.”
I just want to reiterate what you said “Spray foam insulation isn’t a miracle product. In fact, it often suffers the same problem for which spray foam contractors bash fiberglass: poor installation. Worse, bad spray foam installers can create more serious problems for homeowners than bad fiberglass installers.”
I never would have thought that bad spray foam installers could create more problems down the road than bad fiberglass installers because you would think that spraying would be an “easier” job.
We actually started our own insulation company and have our website in the works. I will definitely use your articles as a resource for information to let our customers know an “outside perspective.”