How to Get the Best Possible New Tract Home
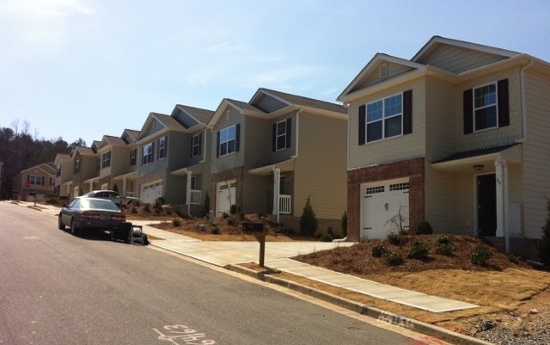
Let’s say you’ve bought a lot in a new development and are having a tract home built. You want the home to be as energy efficient, comfortable, and green as possible. Your builder offers only a few options, like high-efficiency heating and air conditioning systems, but you want more. That’s the question I got from Kerry in North Carolina. Let’s see what you can do to get the best possible result.
Before you buy the lot
This isn’t Kerry’s situation, but it may be for you. If you’re still searching for the right place to live, you have more options available. Here’s what I suggest.
1. Find a development that offers green homes. Depending on where you live, you may be able to find a place that builds all ENERGY STAR homes or certifies all their homes in a green building program.
2. Find a builder who can build a green home in a regular development. Ask for their experience with green building. How many homes have they had certified in a national program like ENERGY STAR or LEED? How many in regional or local programs like EarthCraft House or Austin Energy Green Building Program?
3. Find an architect or building designer with green building credentials. This won’t work in every development, but if you know you’re going to buy a lot in neighborhood where you can use your own plans, get started early. Find a good design professional with green building experience and start working on the details.
4. Find a third-party verifier. A certified home energy rater or other building science professional can advise you on tricky details to watch out for as well as do the inspections and testing during construction. If you find a really good design professional, as advised in step 3, you may have this covered already.
5. Have a design review with representatives from the various trades. Going over the plans with the designer, builder, framer, plumber, HVAC company, and insulator can help you avoid pain during construction.
Once you’ve got the lot
Not everyone will be in a position to do the above items, so let’s see what you can do if you already have a lot and a builder. Kerry is in this boat and asked:
- What can I do before drywall to make my home greener but not ‘impose’ too much on the job site?
- What can I do (affordably!) to the crawl AND the attic space to add energy efficiency and waste less valuable gas/electric resources? Preferably some steps we can “DIY”?
In this situation, you have to make some compromises. You’re not going for a zero energy LEED Platinum Passive House. You just want to get the most you can out of the situation. A good starting point is my list of 10 steps to building a pretty good house. Here are a few other ideas.
1. Get the builder on your side. Talk to the builder about your goals for the home. Do your best to enlist them to your side. Antagonizing them early in the process is likely to be counterproductive. There’s plenty of time for antagonism later, when you’re further into the process and you really need it. Some builders are less amenable to homeowner involvement than others, so try to get a feel for where yours stands.
2. Nix the no-nos. There are a few items that you should tell you builder NOT to install in the conditioned space of the home:
- Unvented combustion appliances. Ventless gas fireplaces don’t belong in buildings. Period. Under the best conditions, they add a lot of carbon dioxide and water vapor. Insist on venting for all fireplaces.
- Natural draft water heaters. A gas water heater is fine. Just make sure it’s a direct vent or power vented model. Natural draft water heaters can put carbon monoxide in your home.
- Powered attic ventilators. These devices are banned in Georgia (except solar-powered models) because they can create health and safety problems by backdrafting combustion appliances. They also waste energy. If you’ll have an unconditioned attic, passive vents are fine.
3. Seal the air leaks. Air leakage affects indoor air quality, comfort, energy efficiency, durability, and noise. For something so inexpensive with so many positive consequences, air sealing is a no-brainer. Some air leaks can be fixed later, but all are more easily and inexpensively sealed during construction. Pay special attention to air sealing around the windows and doors. In the attic, make sure the chases, penetrations for wires and pipes, and top plates are sealed. In the basement, look for unsealed penetrations to the outdoors. In the photo below, light helps you find the holes.
4. Ask for a blower door test. Verify the air sealing with a blower door test. Your builder may already have to do this if your code requires it. If not, insist on it. A reasonable goal for the test would be 5 air changes per hour at 50 Pascals (referred to as 5 ACH50), with lower numbers being better. If you get to this level, you’ll want to have a mechanical ventilation system installed.
5. Make sure all parts of the building enclosure are insulated. It’s true. A lot of insulated houses have areas that are uninsulated. Bathtubs and showers on exterior walls often have this problem, but it can happen in other places, too. Do a thorough inspection before drywall goes up and in all parts of the attic.
6. Focus on HVAC distribution, not equipment efficiency. Get the best duct system you can for your heating and air conditioning system. This is a lot easier said than done, especially in a tract home. You’ll almost certainly need to do number 9 below to get this done.
7. Encapsulate the crawl space. A lot of moisture problems originate at the home’s foundation. Vented crawl spaces in humid climates often create indoor air quality problems. Encapsulating the crawl space is the way to go. It also reduces the overall air leakage. The builder may not be comfortable doing this, but it’s not hard to do it later. In either case, you probably want to do a lot of homework or hire an experienced professional to help or both.
8. Encapsulate the attic. This is only for homes with heating and cooling systems and their ductwork in the attic. Encapsulating the attic, typically done with spray foam insulation, brings the HVAC inside the building enclosure. As with encapsulating a crawl space, do your homework and hire a pro.
9. Hire a third party verifier. An experienced pro will help you get the best house you can. Their work will pay for itself, in peace of mind certainly and probably in mistakes caught and fixed. Look for someone with certifications as a home energy rater, Building Performance Institute (BPI) Building Analyst, National Association of Home Builders (NAHB) Green Verifier, LEED Green Rater, or similar.
Getting the most out of your new tract home
If you do the things above, you should end up with a pretty good house. I haven’t covered everything here, but that’s why I recommend hiring a third party verifier who can help you understand the process and get the home you deserve.
One thing you may have noticed about my advice is that I didn’t recommend going with a high-efficiency HVAC system or getting more insulation. Those things certainly can be good, but I’d rather see a home with minimum efficiency equipment and a great duct system. I’d rather see code-required levels of insulation and an airtight enclosure. An airtight house with good ducts will outperform the leaky house with poor ducts every time.
Have you already gone through the process of getting a tract home built? Are you going through it now? What have you experienced? What’s your advice?
Related Articles
10 Essential Steps to Building a Pretty Good House
The #1 Question to Ask before Putting Spray Foam in Your Attic
The Top 10 Mistakes I Made in Building a Green Home
NOTE: Comments are moderated. Your comment will not appear below until approved.
This Post Has 25 Comments
Comments are closed.
In my experience, a power
In my experience, a power-vent gas furnace is just an atmospheric one + a fan and air inlets to draw in enough air to cool the exhaust to temperatures safe for PVC. That is a lot of extra air beyond stoichiometric. If If this is installed in the interior, I wonder if it could contribute even more to depressurization than the atmospheric ones. Of course, this doesn’t apply to condensing gas water heaters, which use the extended heat exchanger to cool the flue gas to temperatures at which PVC remains happy – or have sealed combustion (outside air) for some models. Am I right to be concerned?
Good point, Harvey. I was
Good point, Harvey. I was going to mention getting all sealed combustion equipment but didn’t do so in the end. Since we’re talking about tract homes, my first concern was to get the worst offenders out of the house. The tighter the house becomes, the more important it is to eliminate all atmospheric combustion, not just natural draft water heaters and ventless gas fireplaces.
Other than #1 are there any
Other than #1 are there any tract builders that would allow any of this? Living in the Southeast I understand that we’re at the mercy of the large production builder. I cringe just thinking of the John Wieland upcharges.
Tract builders are the bain of my existence.
Kris, there are some good
Kris, there are some good tract builders who not only allow this but also offer an array of green options.
It would be really cool if a
It would be really cool if a builder offered an “Energy Star” or “Earthcraft” upgrade on his/her list of other upgrades but I understand that the economies of scale probably make it cost prohibitive.
More of your customarily
More of your customarily excellent advice, Allison!
12 years ago, before our tract home was under construction, I approached the builder and told him I wanted to contract with another respected, retired builder who would periodically visit the site and monitor all phases of construction.
“Well, until you close escrow, the house belongs to us and anyone on site besides our employees would be considered a trespasser. You may of course have the home inspected when it become yours and we will discuss any perceived shortcomings then.” !!!
I probably rolled over too soon, but was able to visit myself after hours and sent notes to the sales rep who was cooperative in passing along my observations to the site supervisor. Air sealing was being done by the builder, but wish I could have had the attic (and all the minimally insulated ductwork) enclosed as you suggest. I enclosed the crawl space later myself. No doubt a more practiced eye would have seen other issues.
Btw, the retired guy felt uncomfortable going on site without approval, so that didn’t happen.
Perhaps builders have become more cooperative, what with Yelp and all…
Your experience doesn’t
Your experience doesn’t surprise me, Steve. No one likes to be told how to do their job, but in the case of many builders, that’s the only way to make it right.
I think by the time a
I think by the time a potential buyer adds all of your suggestions the cost of the home will either be prohibitive or they might as well just build a custom home on their own lot. For the most part buyers in tract housing are in a specific price range and the add-ons you suggest will push them out of that range.
I totally agree with all your suggestions and maybe if they get one or two of them they are still ahead of the game (sealing air leaks should cost anything more to the owner- its should be standard business practice).
I think sometimes we are setting up potential homeowners to think these things don’t come at a price.
Something has to change in the way we build things. I just hope we don’t out price the “typical” buyer trying to fix everything.
I enjoy your articles- keep them coming.
Good points, Tad. Yes, these
Good points, Tad. Yes, these things do have costs associated with them, but so do extra square footage, granite countertops, and whirlpool tubs. If they’re able to do some tradeoffs upfront, they can get a better house.
Agree,
Agree,
From my own experience they use price as a disincentive or just say no.
16yrs ago I asked for the following:
House wrap : “No, and we won’t put it up if you buy it.”
Inspect insulation (Ex, I wanted to foam the gaps around our leaky windows) : “Sorry, they came early and drywall guys were ready.”
Foam under slab: “No, and we won’t do it because all the units in building must be on same grade.”
They scared me into not asking anymore when a neighbor was refunded his deposit because he complained so much.
In addition to your excellent
In addition to your excellent list, I also advise clients to buy a lot that allows optimal solar orientation. Orientation matters even for homes that aren’t specifically designed to be passive solar. Even more important is to bring ducts inside the envelope. Depending on the home’s design, this is often possible without the expense of encapsulating the attic.
Two great points, David.
Two great points, David. Thanks for bringing them up.
If it were my list I would
If it were my list I would have started with
1) find a lot that has natural gas service.
2) get a half pound natural gas meter, and say no to CSST, make sure there are no subordinate gas regulators in your home.
Hi Adam, my apologies, but
Hi Adam, my apologies, but can you translate to home-buyer-speak? I have a feeling that most of what you mention is not something I can choose/change with my builder until after closing, I get whatever they normally install…..can you offer some insight of what I can look for now (before drywall) and what you recommend after closing I change (affordable)(it looks like all gas lines in the home are copper?). Thank you so much for your advice!
What do these things mean? )
What do these things mean? ) get a half pound natural gas meter, and say no to CSST, make sure there are no subordinate gas regulators in your home.
Thank you SO much Allison!
Thank you SO much Allison!
We have been lucky I suppose, but this is our 2nd tract home built in the last 10 years and BOTH the site mgr’s have been fantastic. I do agree with many comments about BEING NICE to them from the get-go! While I may have to wait until after closing to encapsulate attic & crawl, I’ve been able to add extra studs, add soundproofing & extra insulation, “unauthorized” extra outlets and move a few air ducts (just a few inches) for better flow.
Our builder does NOTHING extra, the “options” were about 1-page long in huge font. It’s amazing what a little “niceness” can do in getting cooperation before all the drywall goes in (a few cups of coffee in hand didn’t hurt either)!
We will have to encapsulate after closing, but having some of Allison’s advice has been very helpful – in addition to your reader responses! I’ve gone to the trouble to seal all gaps and leaks, add extra HVAC tape to duct work, add insulation behind tubs against exterior walls (really, there was NO insulation there!!!!) and a host of other small things that don’t set off any alarm bells with the builder. Even if he had been uncooperative, I would have been able to do some of this on Sundays when crews are scarce or non-existent. None of my fixes harm ‘passing code inspection’ and I daresay nobody even notices most of my work.
I agree that most people are in a tract home due to cost, but please keep in mind that many tract homes are now $400+, and many folks DO have the funds to spend $10-30k to encapsulate. Also, the minor things that cost me under a few-hundred bucks (plus personal elbow grease) will make my home a LOT better (just thinking of no insulation behind the 2 exterior wall tubs and some sealing of ‘little holes’ everywhere!). Even in my previous house, a good $150k less and back when I could not spend even an extra $1000, it would have been within my power to fix some of the small things and greatly enhance the efficiency of our last home.
I would love a custom house and a custom builder, or even a greener builder, but school districts, land availability/pricing, custom home prices (with lot prep) and job location limit a lot of these for middle-income folks (even folks in the $500-600 range).
Thanks to everyone for all your advice, I still have work to do before drywall next week (based on all the great advice obtained here)!
Best to all!
You’re welcome, Kerry. Thanks
You’re welcome, Kerry. Thanks for jumping in here and sharing your experience, both with the current tract home you’re having built and your previous one.
NG is 60PSI throughout the
NG is 60PSI throughout the region.
Your meter only reduces the pressure to 2PSI if the face on the meter is red.
Your meter reduces the pressure to 1/2 PSI if the face on your meter is white.
If you have a red faced meter, then every appliance will have a crappy, likely MAXITROL brand NG regulator allowing NG to potentially leak into your home. CSST is corrugated stainless steel steel tubing and you can puncture it with a picture hanging nail. Is this the kind of gas piping you want in your home?
https://youtu.be/lQxTmSfxEFg
I just inspected a new home, and found that every room in the house was filled with quite a bit of combustible gas due to this one regulator in the basement.
Adam Stetten – thank you for
Adam Stetten – thank you for the clear explanation of your previous comment.
Just out of curiosity, what
Just out of curiosity, what is the minimum ACH50 that does not require a ventilation system?
Followup: how do I go about getting a blower door test done? Does Alabama Power do them?
@Blake, that’s an interesting
@Blake, that’s an interesting question. Older versions of ASHRAE 62.2 (low rise residential ventilation standard) and BPI’s Building Airflow Standard, which was based on the 1989 version of ASHRAE 62, stipulated that a home required ventilation if it tested out below 0.35 ACH at natural air pressure, or 15 CFM per occupant (# of bedrooms + 1), whichever was greater. This was widely interpreted to mean that you either stop air sealing when you reach the limit, or add mechanical ventilation.
Other than the obvious “cliff” this method imposed, a big problem is that ACH-nat cannot be directly measured. The conversion to ACH-nat from ACH50 (as measured by the blower door) were based on an ‘n-factor’ contour map. Very imprecise. So much so that ASHRAE (and the home performance industry in general) have largely abandoned the ACH-nat metric.
Since the 2007 version, ASHRAE 62.2 has instead stipulated a target ventilation rate (CFM) based on floor area and number of bedrooms, along with a formula to take credit for measured infiltration.
To answer your question, the ACH level that fully trades off with mechanical ventilation depends on a number of factors. In my own practice, I begin to think about ventilation below about 3 ACH50, but you’ll find no consensus among home performance practitioners on that (an understatement).
Here’s a handy online calculator that implements the latest ASHRAE 62.2 calculations (2013), making it simple to answer your question for a particular home. If you know the volume, you can back into the ACH50 that fully offsets the need for mechanical ventilation: http://bit.ly/1zjcnpi
Location location location!
Location location location! As always, great technical comments. I know the focus here is building energy use, but I would start the list with a location that does not require a lot of time and gas to get to anywhere else (groceries, work, school, etc).
Thanks for this article and
Thanks for this article and conversation. I’m an architect in the Raleigh-Durham, North Carolina area and have witnessed first hand the results of our several decades long local building boom. Whenever demand is so high, there’s little incentive for contractors to build quality. It’s just too easy to cut corners and make more profit. I’ve lived in two different houses from this era and it is shocking what gets passed through inspections. This trend just won’t stop.
I always council home buyers to look for contractors with a longstanding good reputation because it’s about the only market force working in the buyer’s favor. Check at least three recent references! Seriously, go find a few contractors that have been around for 10+ years under the same name. If you find someone with a reputation to conserve, they’ll either charge what it costs to do it right or decline the job.
Good contractors are reasonable. Steer clear of any situation where construction quality seems obvious problem and no one seems to care. Run whenever poor quality is forced on the customer!
Obviously, I subscribe to the view that good construction drawings from an architect are a fair start on quality. But it takes follow through to make those happen.
Good energy efficient construction is difficult even in high end houses because there is not enough training on the construction side. Even on the commercial side, it usually takes several conversations and emailing tidy research summaries to begin to climb up the hill toward achieving useful envelope design concepts in reality. (I usually start off with a test to see if “air barrier” is understood beyond good ol’ house wrap and then ramp up to moisture barrier positioning within insulation and its impact on condensation.)
For residential construction, it is nearly impossible to find a contractor that knows or cares about actual building science. Pricing is too competitive. Good contractors head toward commercial construction or architecturally designed residential where they can survive.
Which brings me to my point: Builder/market housing is cheap for a reason. It is created as a commodity and it is disposable. Rather than “invest” in such a home, why not reduce your required square feet by about 20% and build something with real quality? It is mind-blowing how large houses are around here and yet, they are all made of paper. They are the Emperor’s New Clothes and it is absurd! Build better than bigger.
“Which brings me to my
“Which brings me to my point: Builder/market housing is cheap for a reason. It is created as a commodity and it is disposable. Rather than “invest” in such a home, why not reduce your required square feet by about 20% and build something with real quality? It is mind-blowing how large houses are around here and yet, they are all made of paper. They are the Emperor’s New Clothes and it is absurd! Build better than bigger”.
An owner/builder is at a disadvantage because as you know it’s all about the price of land, the value of surrounding housing stock and economies of scale with regards to materials/labor.
The only way to make it happen as an owner/builder is to invest a significant amount of money into the property under the premise that you would ‘break even’ when it came time to sell.
Through Building America and
Through Building America and other programs, production builders have demonstrated time and again that it’s possible to design and build high performance homes and succeed, even thrive, in a competitive marketplace.
Building high performance homes is *much* more about training, process, and QA than adding more insulation and selecting high efficiency products. The learning curve can be a bit steep, but over time, it doesn’t have to add that much to the cost.