HVAC Therapy for Energy Code Flunkees – “It’s Not Your Fault”
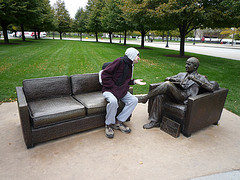
[Guest post by certified HERS Rater Jeffrey Sauls about his experience with the new Georgia energy code requirements for duct tightness testing.]
[Guest post by certified HERS Rater Jeffrey Sauls about his experience with the new Georgia energy code requirements for duct tightness testing.]
“Seriously. I want you to hear this. It’s not your fault.”
In a couple of month’s time, many HVAC contractors across Georgia will be hearing these words from their therapists…and the therapists will be correct. It’s really not the HVAC contractors’ fault.
The issue that will have these contractors flocking to therapy is the enforcement (beginning 1 July) of the duct tightness requirements adopted this year by the state of Georgia. Along with the building envelope leakage (infiltration) requirement of less than 7 ACH50 (7 air changes per hour measured at 50 Pascals), all new homes are required to have duct leakage* less than 8 CFM25 (cubic feet per minute measured at 25 Pascals) per 100 square feet of conditioned floor area (often referred to as 8%, although it’s not a true percentage).
I’ve had the opportunity to spend the last few months working with a couple of proactive builders in the metro Atlanta area that want to ensure they can meet the new tightness requirements once enforced. The glaring conclusion from these tests is the duct leakage requirement is going to give builders fits if they don’t develop a remedy for it. Most builders will achieve the envelope tightness without much problem. Don’t get me wrong, I’m excited that Georgia’s code is making the industry measure it, but it’s not that big of a challenge for builders to hit 7 ACH50.
The duct leakage is where the real problems are. For the most part, the ductwork and units are pretty well sealed. There are often small holes in the cabinet that could be sealed better and the filter doors continue to be a disaster (aside from the 4” media filters), but these are small potatoes. The big issue is at the boots. Practically no sealing takes place here at the present, and it’s easily the largest source of duct leakage in a new home. It’s also not just a single issue at the boots, it’s two specific locations: between the boot and the metal frame and more importantly, between the ceiling drywall (or subfloor) and the metal frame.
Why this is not the HVAC contractors fault is the timing of construction activities. The time to perform this sealing usually doesn’t align with their typical site visits. Should it be the painters? Drywallers? Insulators? Site supervisors? Punch out specialists? I think the answers will vary, and it will be up to the individual builders to decide when this sealing should take place given their particular build process.
In no way am I saying the HVAC contractors are doing things perfectly. Most have a long way to go on proper unit sizing (decoupling your profit/pricing from the size of the installed unit is a good start to helping them accept Manual J results), and all the penniless mastic salesmen is a bad thing. Mastic on the plenums and cabinets is prevalent but few contractors are using it on all the connectors. Aluminum foil tape is the popular answer that usually meets the initial duct testing requirements, but will it hold up after multiple years in a scorching Georgia attic? (Regardless, mastic is required – see Section 403.2.4 of Georgia’s Supplements to the IECC)
Tight duct systems are the ultimate goal here, but the hidden lesson in all of this for HVAC contractors is don’t start promising low duct leakage rates to your builders unless you plan on making an additional trip to the jobsite to seal around the boots. For those of you with HVAC contractor friends and acquaintances, remember to show support and remind them, “It’s not your fault.”
To those of you who are putting the ductwork out of the attic and inside the building envelope or using ductless systems, bless you. You obviously get it already.
* Code actually allows three duct leakage testing options: 1) 6% total leakage measured at rough-in with air handler installed. 2) 8% leakage to the outside measured at final. 3) 12% total leakage measured at final.)
Jeffrey Sauls, the owner of D2D Sustainability is a certified HERS rater and Duct and Envelope Tightness (DET) Verifier for the Georgia energy code. His background is engineering, and he has a degree in Industrial Engineering from Georgia Institute of Technology.
Top photo by Ambernectar 13 from flickr.com, used under a Creative Commons license.
This Post Has 10 Comments
Comments are closed.
Good article Jeffrey. Your
Good article Jeffrey. Your observations are concurrent with mine. However, I remember when I read the new Georgia standards a few months ago I was surprised at how loose they are. Give me a break! 7ACH50 and 12% total duct leakage is almost no standard at all. When are people going to get serious about this?
Anyhow, keep up the good work.
This standard sets a low bar
This standard sets a low bar for a passing grade. While it is good to chop off the worst offenders, the hazard here is everybody will settle for “the worst house that is legal”. I certainly hope builders can get mileage out of posting far better numbers than the minimum, and that customers pay attention to this.
1) Use duct mastic on every
1) Use duct mastic on every connection of flex duct and start collar to plenum, before making the connections – especially between the flex duct and collar. THIS IS A MUST TO GET THE RESULTS NEEDED – INSTALLERS PRACTICALLY HATE DOING THIS AND WILL MAKE ALL KINDS OF EXCUSES AND ALTERNATE BUT UNWORKABLE SOLUTIONS.
2) Avoid tape period except: Use butyl tape on any service panels that separate the air stream. This can be removed and re-applied when needed.
3) Test the tightness before you call it good.
4) After a couple of systems you can get it to under 2% leakage to outside. Yes, that was 2%. When you get better at it you can get it to under 2% absolute.
5) There is a way to practice in the shop to get perfect at duct tightness. Maybe I will develop a routine for it on my course.
5) It is like welding with nitrogen bleed, or using a vacuum pump – just do it and it will come out alright.
6) Save the money on the counselor and do the above. 🙂 IT IS MORE COST EFFECTIVE.
John R.:
John R.: Yes, it’s a low bar, but it’s higher than we had before – nothing! I think the main goal right now is to get builders & HVAC contractors used to the idea of having their work tested. As they find out that it’s not really that hard to meet the requirements, then the bar can be raised.
M. Johnson: I think that will happen. Those builders who have tighter houses and duct systems will use that in their marketing. With actual test results attached to the envelope and duct tightness requirements in the code, builders have a way to distinguish themselves from the pack.
Christopher C.: Thanks for the tips! HVAC installers who follow your advice shouldn’t have trouble passing, even if they don’t get all the way to 2%.
Boots are indeed a big
Boots are indeed a big problem (although I take issue that cabinet leaks are ‘small potatoes’, given the high static levels). However, I don’t buy the argument that site visit timing is an issue. Boot-to-drywall (or boot-to-floor) sealing should be done when grilles/diffusers are installed.
That being said, when dealing with HVAC contractors, I go out of my way to avoid attacking their work. The reality is that the market has forced the industry toward the lowest common denominator. The culprit is lack of accountability. Neither the builder, homeowner, nor building inspector check duct leakage. If everyone is held to the same standard, albeit a low standard to start with, at least those who ‘get it’ will not get beat up on price by someone who could care less. That’s the magic in transforming the market. Belly-aching is to be expected.
David B.:
David B.:
Great point on the cabinet leaks being at high static pressure during system operation. They definitely need to be sealed to reduce “real world” leakage. Given the current duct testing methods though, my experiences have been that they’re still very minor when compared to boot leakage.
RE: timing. The argument I’ve heard (and somewhat buy) is that the sealing products need time to cure before attaching grilles. This is definitely true with foam. The grille becomes a permanent part of the ceiling if it’s put on too soon after foam has been applied. In the grand scheme, I would also imagine it’s cheaper to pay a painter to caulk the boots than it is to absorb an HVAC tech’s rate to do so.
Agreed. I do not envy the business position HVAC contractors are in. The education of everyone in the process HAS to continue. As you mentioned, it is unfortunate that the HVAC companies that try to correctly size the unit and install ducts properly still get beat up on price because their $/ton is too high.
Jeffrey, I know some people
Jeffrey, I know some people have no use for tape, but I’ve been using (and recommending) high quality UL-181 foil tape for this application for more than 15 years with excellent durability. No curing time. No messing with trying to bridge those big gaps with caulk.
Although the builder might save a few nickles by having another sub do the work, we simply can’t let the HVAC guy off the hook for being end-to-end responsible for leakage. I can just see the finger pointing. In any case, larger HVAC companies usually have a low wage tech do final trim-out. But the reality is, it’s not going to happen unless codes require it.
Great discussion, the bar is
Great discussion, the bar is low but now we have a bar. The process is slow but it has begun. Savvy homebuyers are demanding more and educating themselves. I think that they are becoming real drivers in this process, especially when they are represented by Agents who “get it.”
I agree that something is
I agree that something is better than nothing.
I don’t have it out for HVAC contractors, but if you can schedule to go in a person’s house every six months to check and service the system(s) you should be able to schedule a time to seal the boots. I would think as a contractor that to hold say 25% of the HVAC contract until testing is complete and passed the set requirements would help any scheduling problems. The policy is you do it, or pay me to do it.
Owners retain a percentage of the entire contract from me until all the subs get around to scheduling their punch work.
Money is the great motivator, hold it and they will come, or schedule as needed.
I agree with the money thing.
I agree with the money thing. AC contractors just don’t get paid to have good duct systems. They do get paid to use bigger equipment.
Builders usually like to take the lowest bidder with the best insurance policies. That bidder does not include a perfect system as part of the scope. Just a safe system.
Manufacturers don’t enforce static pressure limits on warranties. I wonder why. They would not sell systems.
Now we are getting at the real heart of the problems. Follow the money.
You get what you reward. Rewarding the lowest bidder, despite hidden deficiencies, is what you get. Imagine if the ac contractors were forced to only bid nothing larger than 3 ton units. They would go broke on tract homes with the way it gets sold and scheduled up till today.
Just some opinions of mine. Maybe not facts.