Mechanical Room Duct Obstructions
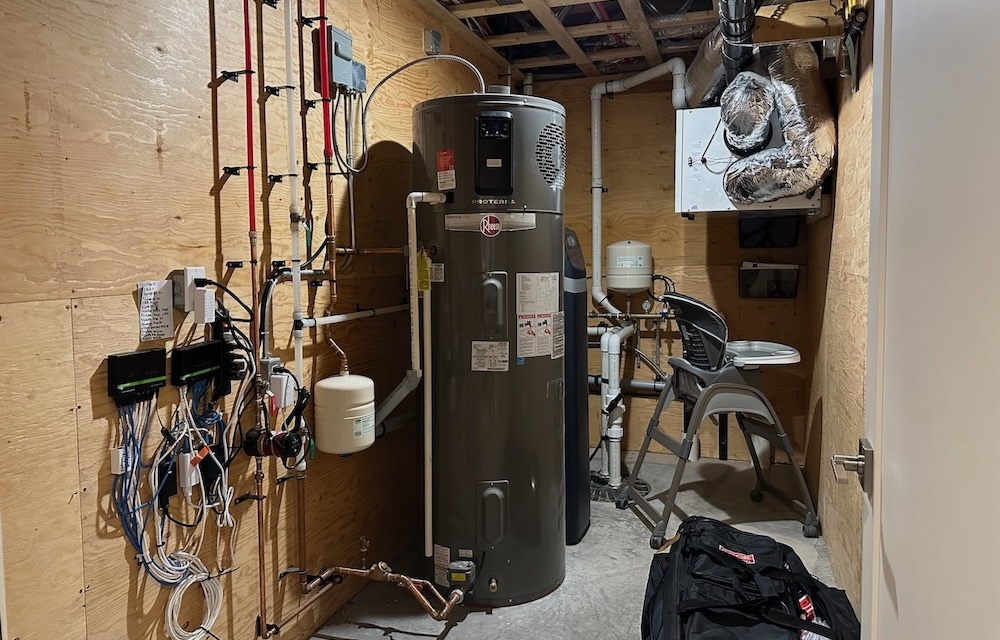
Recently I wrote about how bad it is when architects give HVAC designers a little closet to put the mechanical equipment and ductwork in. Make it a mechanical room, I said. But here’s the thing. Size isn’t the only thing that matters. We have to find space for air handlers, ductwork, mechanical ventilation systems, and dehumidifiers. And the ducts attached to those pieces of equipment need to be able to get past any obstructions and deliver their air where it needs to go. So, let’s take a quick look at the issue of mechanical room duct obstructions.
Watch out for stairs
Here’s a snippet from a project we worked on a while back. Notice the nice big mechanical room in the basement. Hooray! We love seeing one that big.
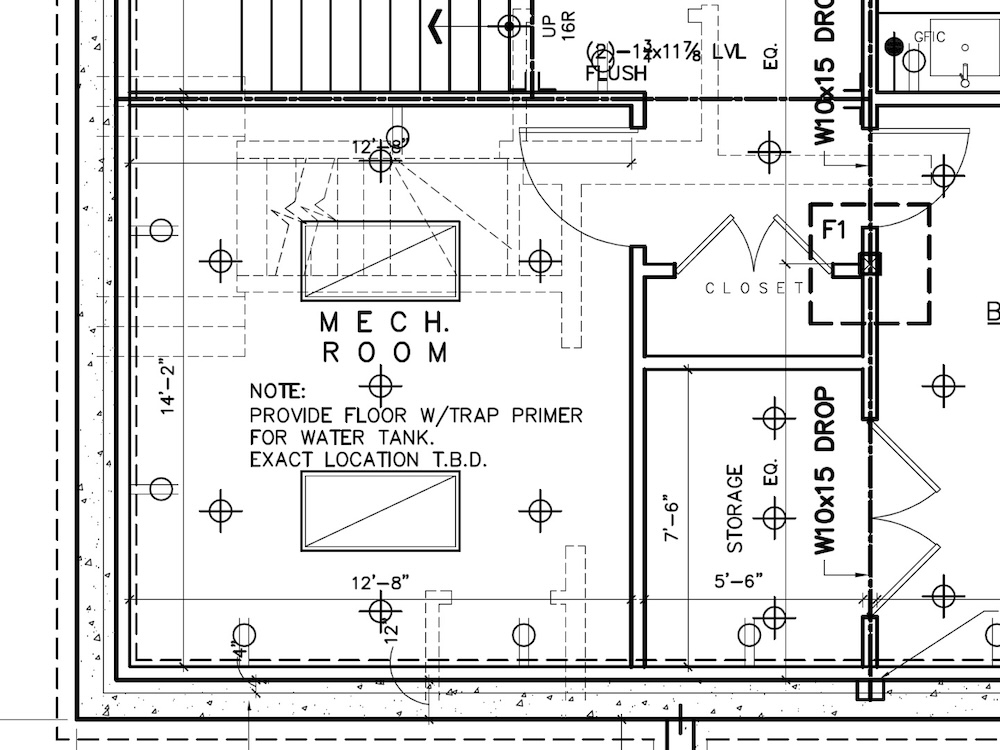
Now, take a closer look. The first thing that might jump out at you is the stairs at the top of the floor plan. That’s obstruction number one. Now we’re limited to taking all the ducts out through the right side of the mechanical room.
Beware of beams
But wait! Look a little closer and you see obstruction number two. It’s a flush beam (i.e., at the same level as the ceiling joists around it), shown by the horizontal red line below. That limits the vertical space available to move ducts through that area to the right of the stairs.

And finally, obstruction number three is the clincher. The vertical red line to the right of mechanical room is another beam, but this one is dropped below the ceiling joists above. To get any ducts across it, you either have to go up through the first floor and find pathways there. Or you have to go under the flush beam, which means dropped soffits that take away ceiling height.
Visualize ducts
Structural elements, like the beams mentioned above, are the most common mechanical room obstructions, but there are others, too. Plumbing drain or supply lines can ruin a perfectly good duct design. So can several other things. Here’s a good list of obstructions we have to look out for when we’re doing the HVAC design for a home:
- Stairs
- Beams
- Plumbing drain and supply lines
- Plumbing fixtures (toilets, showers…)
- Electrical panels and wiring
- Skylights
- Vaulted ceilings
- Open-to-below or open-to-above rooms
- Range hoods
Duct design is hard enough already when we have a nice big open space for everything. Throw in some mechanical room duct obstructions, and it gets even harder. When you’re designing a house (or having one designed), please take a moment to visualize where the ducts might go…and how they’re going to get there. Better yet, get the relevant trades together to figure it out in advance.
Allison A. Bailes III, PhD is a speaker, writer, building science consultant, and the founder of Energy Vanguard in Decatur, Georgia. He has a doctorate in physics and is the author of a bestselling book on building science. He also writes the Energy Vanguard Blog. For more updates, you can subscribe to Energy Vanguard’s weekly newsletter and follow him on LinkedIn.
Related Articles
Make It a Mechanical Room, Not Just a Closet
The Basic Principles of Duct Design, Part 1
My Duct Systems on Low-Static Mini-Split Air Handlers
Comments are welcome and moderated. Your comment will appear below after approval.
This Post Has 21 Comments
Comments are closed.
My father was the general contractor and carpenter for new home construction while I was a kid. I was his crew during the summers. Even though he was the general contractor, getting the “trades” to work together was tough, especially because they usually weren’t on site at the same time. We would usually let the sheet metal guys be the first to do their rough-in, followed by the plumbers and then the electricians. It usually worked pretty well. We had to keep an eye on them to make sure that they didn’t too much structural damage.
I agree that beams get in the way, but another related component is bridging between the floor joists. The sheet metal guys would just tear out any bridging that got in their way. We would try to work with them to put in a section of solid bridging with a hole in it to accommodate round ducts.
Allison, have you or anyone on this blog tried using “rheia” ductwork (rheiacomfort.com)? It looks like an interesting concept to me. I have never tried it nor do I have any financial stake in it. It just looks like a step in the right direction if the cost isn’t prohibitive.
Hello RoyC
I just looked at rheia ductwork. I am familiar with “high velocity” HVAC design and thought it evolves to retrofit older homes to AC. Hard to see “high velocity” as a feature otherwise.
I never thought that the HVAC industry took it that seriously as they have other ways of doing things.
As a hydronics professional, I see some primordial need to go ahead and move the heat or cool with pipes using water instead. You can move heat or cool with out moving air.
Hi Dale: I don’t think Rheia is necessarily promoting “high velocity” ductwork like Unico, at least I don’t see that in their literature. I believe that they are saying that you can use more small ducts rather than fewer large ducts to make installation easier. I hope they are not promoting the high static pressures required by Unico systems.
Dale, maybe you can heat and cool without moving air, but it is hard to dehumidify, ventilate, or filter without moving air. Thus, I am not a fan of hydronic radiant or baseboard systems.
Roy
I don’t know what the flow rate is for the very small diameter ductwork they are showing but the duct size alone would dictate that the velocity in the duct be somewhat high. They do show an awful lot of such small diameter ductwork so maybe they are just dividing a larger flow into many parallel streams that converge at the register. Providing the registers with the appropriate flow to provide the correct throw and spread with low noise is the objective.
Dale, I understand the need for “throw” in commercial systems serving large spaces, but is it really necessary for residential applications? Even if it is important, it is the velocity at the register that determines throw, not the velocity in the duct.
As you tighten and insulate the envelope (beyond code minimums), the “correct” throw diminishes in value.
Roy,
Yes handling air is necessary for dehumidification and for ventilation which is the proper job of dedicated ventilation and de-humidification systems.
Dehumidification is something that traditional hvac systems provide only as an side effect that is often at odds with sensible cooling. Ventilation is a function that conventional hvac systems don’t address at all. Or they do Mickey Mouse things like putting a duct from a furnace or heat pump return to the outside and call it ventilation. Pretty pathetic.
Neither application has a lot to do with heating and cooling. The real trick is to find ways of decoupling these otherwise disparate functions. That is what is done in commercial HVAC systems and what I practice in my work.
Dale, you addressed ventilation and dehumidification, but what about filtration? I am just saying that a good forced-air system can provide all of these HVAC functions at a lower installed cost and better operating efficiency than having separate hydronic and forced-air systems for these functions.
RoyC
I have designed several Rheia systems over the last few years working closely with the Rheia Team. Some of the things I like about the Rheia system is the consistent temperatures from floor to floor, everything is in conditioned space and every Rheia install is balanced. As a designer I appreciate the thorough process of a Rheia design.
Mike, thanks for the feedback. How does the cost compare?
I don’t see a problem… You have a basement AND a mechanical room. Yes you have some obstacles but again you have a basement and a mechanical room. You are 200% better off than everyone else in the country. Come to TX where we have no basements and no mechanical rooms. Well unless you consider the attic a mechanical room as that’s where the HVAC units, ducts often waterheater are located.
I was being jealous above… I would really like to see a house designed by the group of tradesman that are building it and see what the end result is. I can tell you that when I done commercial construction enemy number 1 is the architect then sometimes the engineer as they both draw up pretty stuff that has no ability to be reality. Fortunately we had good architects that would change their plans for the next build of the same or similar building. They learn but they learn slowly since they rarely show up on site and have no experience in the field. Architects and engineers should be required to have 5 years of hands on site experience before getting their license.
When it comes to houses please make them square and stop the silliness of having rooms jut out from here and there. Not only is it a waste of material which ends up costing more per sqft but you also end up with more surfaces to insulate. And you end up with all kinds of hips and valleys that vastly increase the cost of roof framing and roofing and increases the likelihood of roof leaks.
Amen to the hands-on experience requirement for architects and P.E.’s.
Amen to home floor plans not being modeled after the coast of Maine.
More self-respecting commercial design firms have been working with BIM tools, and BIM is trickling down to single-family design.
Allison’s article is saying, “make the structure work with systems, not against them”. A basement mechanical room where the internet router is chilling with the HP water heater is a luxury, but similar systems can be accomplished with a much more modest floor plan by distributing the individual system components to more than just one centralized location, at design stage.
Robert, as an senior architect helping other architects, I agree we should have required time in the field… not just transporting pay apps, but actually getting into how the soup is made. I think we need more science as well, a little more physics would go along way to making sure folks can distinguish between an air barrier and a vapor barrier not to mention why they are needed when… However, as frustrating as all those roof angles and other “silliness” – barring sky cranes, lol – there needs to be folks out there that push us to reach beyond the practical – to reach for beauty… understanding that not everyone will agree on what that looks like… just remember the next time you have to “help” the architect, they are juggling the interface between you and other tradesmen (and women) as well as a client – who is often even further disconnected with reality – years ago I overheard a client “Arthur, Arthur, I finally got it!” (offering at least the 5th version of a basement plan) and my boss, “They poured the slab today…” (expectant that the posed question would be dropped) followed by, “Is that hard to change?”… lol… We all have to deal with moments where we arrive at what seems obvious before the next guy… the trick is to gracefully help them see without “shoving their nose in it”… :)… so they’ll be willing to come back again for a scritch and a pat on the head on a better day…
Robert, I have been involved in residential construction in Texas and Oklahoma and believe that a conditioned attic (foam insulated roof deck) is the way to go. This is even better than a basement for HVAC since you can easily supply air to the ceilings rather than the floor. Just be sure to provide stairway access rather than a scuttle hole.
Hello Allison,
Many thanks for the article. I’ve spent much of my career designing and building mechanical rooms. Thought I specialize in hydronics the headaches and limitations placed on us by top down designers who treat mechanical design and equipment as afterthoughts even as they place enormous responsibility on trades people to work miracles. Especially if the client has money, then the architect is free to have others create a monument to his own ego
Sorry…
That said, you might consider the advantages of hydronic distribution systems using hot or chilled water. An Air to Water heat pump can be piped into a buffer tank in that mechanical room and heated or chilled water can be distributed from there to remote distribution in the building to address different loads. The piping saves considerable space.
Even if one is operating fan coils, dhu coils etc. (exchanging to air) the air handlers can be remotely located in the building, even if they are ducted from there.
This also opens the door to sensible cooling using radiant panels and providing dehumidification via a dedicated air exchange system, erv coupled with chilled water coil.
This is a description of a system design that I am currently peddling :-). Dedicated Outdoor Air System residential scale.
RoyC
I have designed several Rheia systems over the last few years working closely with the Rheia Team. Some of the things I like about the Rheia system is the consistent temperatures from floor to floor, everything is in conditioned space and every Rheia install is balanced. As a designer I appreciate the thorough process of a Rheia design.
Mike,
So the Rheia system is basically a high velocity duct system like Unico. Is that correct?
Re: Allison’s stairway/beam conundrum, perhaps you could go with two smaller zones, one on each side of the stairway which would require two mechanical rooms.