More on Air Conditioner Sizing Rules of Thumb
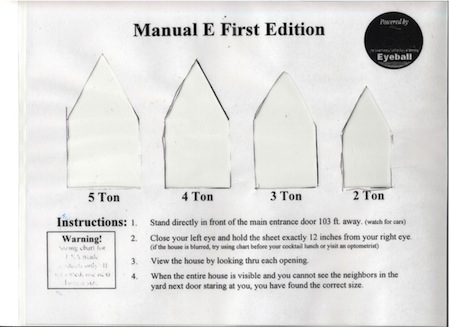
Air conditioner sizing rules of thumb must die. That’s what I wrote in my last article. The most common rule of thumb is to use 500 square feet per ton to determine the size of air conditioner needhttps://www.energyvanguard.com/blog/more-on-air-conditioner-sizing-rules-of-thumbed. Or 400 or 600 or some other number in that general vicinity. In my article, I showed a graph of air conditioner sizes, given in square feet per ton, for 40 homes that we did load calculations for. The average of the 40 was 1,431 sf/ton. Now, let me say a bit more about that.
Here are a few points that came up in the comments to the article and on LinkedIn and Facebook as well as some takeaways that I feel need to be emphasized.
1. No matter the number, you can’t use square feet per ton to size air conditioners. I posted the square feet per ton results we got from 40 Manual J load calculations in hot and mixed climates. The average was 1,431, but you can’t use that to size air conditioners. You have to do an actual load calculation. Those 40 results ranged from a low of 624 to a high of 3,325 sf/ton.
2. If you tell me your load calculations average 400-600 square feet per ton, I assume you’re not doing them correctly. Is it possible that homes meeting current building and energy codes need that much air conditioning? Yes. If they have a lot of window area, they face west, and are in states with weak codes. My friend Mike MacFarland of Energy Docs in California gets 1,500 sf/ton for retrofits and achieved 3,350 sf/ton for a new zero energy home. And their design temperature is 102° F so don’t tell me this doesn’t apply in Florida or Arizona.
3. You need room-by-room load calculations to get the air flow right. Contractors who use whole-house rules of thumb often don’t get the right amount of conditioned air for individual rooms.
4. The square feet per ton you get from Manual J still gives you an oversized system, even when you do it correctly. Mike MacFarland says he finds it 20-40% too much capacity. David Butler says 15%. In my own condo, for which I’ve measured AC runtimes for the past two years, I’m seeing about 75%. (I’ll write more about my condo soon.)
5. It’s easy to get whatever load you want when you do a Manual J load calculation. I’ve written about this before. Putting in the wrong values for windows is an easy way to add load, as is putting in too many people, using exaggerated design temperatures, and the wrong orientation. If you want 500 sf/ton, it’s not hard to produce a Manual J load calculation that gives you that number.
Designing an HVAC system starts with proper sizing. Look at the square feet per ton number you get to see if you’re in the ballpark. If the number is less than 1,000 sf/ton, there’s a good chance the number is wrong.
Allison A. Bailes III, PhD is a speaker, writer, building science consultant, and the founder of Energy Vanguard in Decatur, Georgia. He has a doctorate in physics and writes the Energy Vanguard Blog. He also has a book on building science coming out in the fall of 2022. You can follow him on Twitter at @EnergyVanguard.
Related Articles
Air Conditioner Sizing Rules of Thumb Must Die
Got Manual J? Don’t Assume It’s Correct
The 3 Types of Heating and Cooling Loads
NOTE: Comments are closed.
This Post Has 51 Comments
Comments are closed.
If you really, REALLY want to
If you really, REALLY want to get it right, do at least a single point whole house blower door test and plug that number into the Man J calculation in lieu of “Loose, Kinda Loose, Sorta Loose, Kinda Tight, Sorta Tight, Tight, Very Tight” selections.
Even better, USE the blower door test, ideally conducted in the presence of the astonished homeowner, to effect reductions in infiltration to move the needle a notch or two in the tightward direction.
We tell clients that while we furnish and install some of the best and properly sized HVAC systems, we can’t heat, cool and dehumidify the neighborhood, just the houses i it.
Yep. Putting in an
Yep. Putting in an infiltration rate that’s too high is one of the many ways to cheat on Manual J. With new homes, though, you can’t do a blower door test. That’s where good energy codes and enforcement can help. If there’s a limit on the maximum infiltration rate, you can put that in. If the builder has had blower door tests done before and has a record, you can use that. But as you say, Curt, using a simplified input for infiltration probably won’t be very accurate.
So if i understand you
So if i understand you correctly infiltration is one of the values that gets guessed at with manual J
Last fall I had a builder
Last fall I had a builder approach us to do their building permit estimated energy calculations (in FL, you need a Manual J and Manual S submitted based on plans as part of the building permit process). When he sent me a list of their plans, there was a column for square footage and AC size. I knew there was going to be a challenge once he told me the AC size based on the size of the house.
He told me they use 650 sq ft/ton. I did five calcs and showed him they were actually between 1150 – 1300 sq ft/ton. He wasn’t buying it. I pointed out how just in the last six months, they had changed from R30 to R38 in the attic, went to radiant barrier roof sheathing and changed from aluminum windows to a vinyl double-pane Low-E2, so any size ACs they had in the past would be reduced as they had less heat to remove from the building.
He said I had to adjust my numbers. I tried several ways to show him they didn’t need the sizes he specified, but he wasn’t budging.
Neither was I.
Needless to say, we are not doing their energy calculations.
But why is it some builders can’t put two and two together? This builder had recently made significant changes to their building envelope, yet he couldn’t equate that to reducing the AC required. And the savings in AC size that could pay for part of, if not all, the envelope upgrades they had made?
Sometimes I just don’t get it.
Tim,
Tim,
I feel your pain. We do our own Florida permitting calcs for our new construction clients. Every now and then we meet a builder or existing homeowner wanting way too much tonnage. Painful though it is, if we can’t bring them around to enlightened thinking, we walk.
With new construction we pretty much insist that air handler and ductwork all be located within conditioned envelope. That nearly always calls for spray foaming the attic since none of our builders work out ways to bring the ductwork in below the ceiling plane.
With foam we pretty much insist on our testing the foam with our blower door rig. Our agile duct guys are also well suited for foam quality control…it is one of the few times in their young lives they are both supplied and paid to apply bright colored spray paint to buildings…
The QC process tends to be somewhat to highly embarrassing to the foam sub, especially if they haven’t been through the BD test routine.
Reply to Emre – yes we sometimes guess at infiltration numbers for new and existing buildings (not everyone can or will pay for the blower door rig) but it is an educated guess.
We routinely (90+% of the time) downsize systems in the course of replacement, and we have yet to undersize a system.
In our environment of upper 70s wetbulb temps / mid 70s dew points, it is better to walk / run away from projects demanding oversized equipment in leaky buildings rather than “own” the inevitable discomfort and elevated mold risk.
My problem is when it gets to
My problem is when it gets to Manual S. Most of our houses are 4-6K sqft, with great bldg envelops at 1ACH50, all metal ducts in conditioned space, top windows and systems. Our Manual Js are around 1300-1500 sf/ton, but when it gets to the Manual S, the high efficient equipment becomes 800-1000 sf/ton; not the 10-15% oversize per code. Reasons given:
1. As equipment efficiency goes up, the rating goes down.
2. Unit size is not equivalent to promise “output”. A 3 ton, 2 stage unit delivers 26K sensible, 31K total. A 4 to unit delivers 41K sensible, 44K total.
3. Units come in full ton units, so if your sizing calls for a 3.2 tons, we have to go to 4 tons.
A rigged system… it sSeems like no-win even if we try our best to do the right thing.
Thanks for helping us keep
Thanks for helping us keep our “cool” with our clients. Here in dryer climates (Denver CO) evaporative cooling, helps cool neighborhoods too! AIr Conditioning compressors heat up our local neighborhoods, using 4 to 5 times more electricity, than Evaporative Cooling. We are lucky to be in a dry climate, our dry sense of humor is also more acceptable here!
Could it possibly be that
Could it possibly be that builders look at tonnage in the same way car companies/salesmen look at horsepower. You never know when you’ll need that extra horsepower!
It appears as if State Codes are written to upsize rather than pick the closest size because they feel that if the temperature should ever rise a degree or two above the 72F set point that every one will expire. In fact, when it’s hotter outside, it is wise to let the indoor temperature move up a bit to reduce the shock when you go outdoors.
Yes, Emre, you understand
Yes, Emre, you understand correctly. Sometimes you have to guess because there’s not a house to test yet. There’s just a set of plans and specifications.
Ugh! That’s a sad but all too
Ugh! That’s a sad but all too common story, Tim. Maybe they think they need more capacity because they’re getting the typical, bad duct installation.
Kudos to you, Curt, for
Kudos to you, Curt, for insisting the spray foam be done the way it should be!
Armando, thank you for
Armando, thank you for raising the Manual S issue. I mentioned it briefly in my article on Friday, and you’re right. When you do equipment selection (Manual S), you do end up with a bigger system than you would just from the Manual J. I wrote about that a few years ago in this article:
3 Reasons Your 3 Ton Air Conditioner Isn’t Really 3 Tons
http://www.energyvanguard.com/blog-building-science-HERS-BPI/bid/59745/3-Reasons-Your-3-Ton-Air-Conditioner-Isn-t-Really-3-Tons
No sweat, Dennis!
No sweat, Dennis!
Yes, evaporative coolers (a.k.a. swamp coolers) are a lower energy way to keep homes cool in dry climates. Whole-house fans are another way.
Colin, that may well be part
Colin, that may well be part of their thinking. As I mentioned to another commenter here, it could also be that their duct systems are so bad they need the extra equipment capacity to make up for what’s lost in distribution.
I think it should be said
I think it should be said very clearly here that there is absolutely no direct relationship between square footage and heating or cooling load. We should probably try to stop using the term square feet per ton altogether. It’s not even a very good number for defining the efficiency of a building envelope. I guess what I’m saying is we should be trying to improve the language we use in the field if we’re going to improve the way things are being done.
“My problem is when it gets
“My problem is when it gets to Manual S. Most of our houses are 4-6K sqft, with great bldg envelops at 1ACH50, all metal ducts in conditioned space, top windows and systems. Our Manual Js are around 1300-1500 sf/ton, but when it gets to the Manual S, the high efficient equipment becomes 800-1000 sf/ton; not the 10-15% oversize per code. Reasons given:
1. As equipment efficiency goes up, the rating goes down.
2. Unit size is not equivalent to promise “output”. A 3 ton, 2 stage unit delivers 26K sensible, 31K total. A 4 to unit delivers 41K sensible, 44K total.
3. Units come in full ton units, so if your sizing calls for a 3.2 tons, we have to go to 4 tons.
A rigged system… it sSeems like no-win even if we try our best to do the right thing.”
Armando –
1) Are you in a hot climate whose outdoor design temperature is significantly above the AHRI cooling capacity ambient temperature of 95*F? If so, valid point – you must use extended capacity tables in manufacturer product info guides to determine actual available capacity at design conditions.
2)I disagree with the statement that increased efficiency costs capacity. The AHRI directory is your friend. I structure all our price books straight out of the AHRI directory that lists ALL certified equipment combinations, not just the random / popular ones manufacturers list for my “benefit” some combinations actually exceed nominal tonnage, and in many cases those high-achieving combos are at the upper end of the efficiency spectrum, as well.
3a)1.5, 2.5 and 3.5 ton systems are all routinely available, albeit rarely in 2 stage equipment.
3b) Confronted with a legitimate “3.2” ton load? Work with client to seek and destroy those two tenths (or more)…find some low hanging fruit such as air infiltration tightening, extra attic insulation, duct sealing, internal gain reduction, window solar filming / screening. There is nearly always some on every project. Failing that, a frank conversation about the oversizing / safety factors already built in to Man J is in order.
3c) Off ratio (Net ton / recommended tonnage) A newly minted mechanical engineer explained to me that off ratio capacity can be taken back at 50%. (I need to look that up) In other words, if the equipment is rated 2.25 tons sensible and 3.0 tons total (standard 75% sensible heat ratio), but the load is, for example, 2.5 tons sensible 2.8 tons total (90 % SHR) you’ll be OK – the SHR can be increased at a slight reduction in total capacity. A competent HVAC installer gets this by tweaking CFM / ton upward.
Rigged? Nope, but one has to be willing to do the math and own the data and the science.
Good point, Andy. Although I
Good point, Andy. Although I used different words, I think I did make that point in number 1 above: “No matter the number, you can’t use square feet per ton to size air conditioners.” I do think it’s a useful number to be aware of, though. It gives you an idea of how efficient the house will be.
now how do you use plans to
now how do you use plans to do a manual J on a new construction
“..That nearly always calls
“..That nearly always calls for spray foaming the attic since none of our builders work out ways to bring the ductwork in below the ceiling plane…”
I guess homeowners need to accept less interior square footage and architects need to place the mechanicals in a well-insulated (for sound) room that’s large enough to accommodate the system. Mini-splits are another option I suppose.
From BSC:
http://buildingscience.com/documents/building-science-insights/bsi-006-no-good-deed-shall-go-unpunished
We think minisplits are not a
We think minisplits are not a good option in most cases.
As you begin tracking air quality you will realize you want high quality filtration, distributed fresh air, and in wet climates you will often want supplemental dehumidification.
…and most people want those things affordably and with as little complexity as possible.
I love seeing Curt’s thinking
I love seeing Curt’s thinking.
I hate new build. In retrofit, they know their home is a piece of crap, that’s why you are there, and it’s not your fault. You fix the house like they never belied was possible, and they are happy.
New build – they pay for Big Mac, cut every corner they can, and expect a perfect fillet Mignon. No win.
That said, we were involved with a 5000 sf new build last winter. 80,000 furnace is oversized as we said it would be. Runs on the 3 ton Greenspeed heat pump most of the time.
This summer for cooling the 3ton hardly ever ran at 100% output, and maintained 72 at thermostat even when 5° above design. When we last looked they’d bumped their set point to 74. When you get equipment sized so it operates continuously we often see RH below 45%. At that level we see setpoint going up over time. 76-79f setpoints are not uncommon.
Iirc, even on hottest days cooling cost never broke $3.
Standard 2×4 construction. Regular fiberglass in the walls.
Builder did get it quite tight – 1600 cfm50.
Can you put up a working link
Can you put up a working link to the article about the 3 ton system not being 3 tons? I am enjoying your blog so much! Thank you, Kellie
Thanks, Kellie! I’ve added a
Thanks, Kellie! I’ve added a live link of that article to the list of related articles at the bottom of my article above.
GreenSpeed is an excellent
GreenSpeed is an excellent choice for heating dominated climates. It’s a bit overkill in my area, but the next Carrier system down from it, 25VNA8, has horrid EER.
Your numbers demonstrate, once again, the importance of a fairly well sealed house; though no need to go all PassivHaus nutty about it.
We spend pretty much all summer at 77*F / 45%RH. That’s a sweet spot.
$3 / day datum needs $ / kWh for relevance.
Look for new build clients that “get it” They are out there, though most are smart enough to avoid falling into the clutches of production builders to whom “custom home” means owner gets to select paint colors as long as they are amoung 50 shades of grayish beige.
@Emre, that is indeed a
@Emre, that is indeed a problem on new construction. My solution is to advise clients to establish a CFM50 target based on builder’s experience and other criteria and incorporate that into the contract, whereby someone is on the hook to bring the house into compliance if it fails, within some percentage.
Excellent comment, Curt.
Excellent comment, Curt.
The biggest reason why Manual S leads to 44k total capacity for 4-ton nominal system, etc., is because the AHRI test procedure for rated capacity stipulates 80F dry bulb and 67F wet bulb indoors, not the conditions anyone designs for. More like 75F/63F. So for me, the expanded tables are an essential part of the Manual S procedure even if outdoor design is right on the 95F rated temp. Manual S essentially looks at the equipment’s capacity at design conditions — including design airflow, which virtually always means referring to the expanded data tables.
@Allison, re: David Butler
@Allison, re: David Butler says 15%. (referring to MJ overstatement of cooling loads)
Indeed, MJ8 is at least 15% over for cooling loads in my experience (more than that for heating).
To the point that you can make a load calc come out to any number you want… there’s of course truth to that, but if you start out with the assumption that you ^WANT^ MJ to come out to the lowest defensible load based on full knowledge of envelope and and QA, the scatter among those of us who truly understand the procedure (not just the software) is surprisingly small.
I agree that MJ overstates more than 15% on super insulated homes and homes with lots of thermal mass. It takes experience and a a good feedback loop to make those judgements.
You’re right, Curt. ACCA
You’re right, Curt. ACCA Manual S procedure calls for 50% of excess latent capacity to be added back to sensible capacity (the other 50% excess is “wasted” dehumidification…as far as the calcs go anyway)
Ted wrote: “We think
Ted wrote: “We think minisplits are not a good option in most cases. As you begin tracking air quality you will realize you want high quality filtration, distributed fresh air…”
How does this exclude mini-splits? Or did you mean to say ductless mini-splits?
We typically specify ducted mini-split heat pumps with MERV 13 filters and ERVs with dedicated supply and exhaust ductwork for ventilation. Typical prices from our HVAC installer partners are in the ballpark of $5/ft2.
“
”
Ted Kidd
8/29/2016 4:01:13 PM
We think minisplits are not a good option in most cases.
As you begin tracking air quality you will realize you want high quality filtration, distributed fresh air, and in wet climates you will often want supplemental dehumidification.
…and most people want those things affordably and with as little complexity as possible.”
I imagine mini-splits with an ERV/HRV would be adequate with regards to filtration. Btw..mini-splits can dehumidify (When vacationing in Central America the apt I stayed at had a mini-split which had a dehumidification setting and it performed very well)
I agree that proper sizing is
I agree that proper sizing is important, full knowledge of all the sizing variables is important and of course full knowledge on how to use the software is important. But I do not think a proper sized AC system is the panacea that everyone thinks it is. For real home comfort and moisture control, I think there is a much larger beast to slay.
Think about it. Most of our discussions are based on proper sizing… when? At design conditions. Is it fair to say that in part load conditions even a perfectly sized AC will not perform as well as we would like? So let’s assume two things: 1) you calculate and install the exact Manual J/S system and 2) it will perform as we claim whenever the load is at least 75% of the capacity. (I know it’s a gradual performance decline but let’s just say 75%) How many hours are you fighting for the perfect match?
I live near Indianapolis and I track the weather for some training sessions I present. This summer, June 1 to August 22, what percent of the hours were within 25% of the design temperature? (Assumptions: design = 91d, set point = 75d that’s a 16d TD, 25% = 4 degrees, what percent of hours were 88 degrees or higher?) While you are guessing at the answer, I will take this opportunity to defend the 91d design (ACCA 99.6%) instead of the 89d design (ACCA 99%). “89 degrees! Are you kidding?” my affluent homebuilders would challenge. (I have many stories, but not that much room here.)
Here are the results of my tracking 1989 hours this summer: 1376 hrs, 69% at 79 degrees or below meaning you only need 25% of your capacity, 284 hrs, 14% between 79 and 83, 212 hrs between 83 and 87, and only 113 hrs, 6% between 87 and 91 when you finally see 75% or more of your AC capacity. ( 4 hrs over 91d.)
Now just to get you thinking, what percent of the Indy hours were near design conditions for the latent load? (Assumptions: 75d WB design = 69d dew point, “no latent load” dew point would be 55, difference = 14d dew point, so what percent of hours had a dew point of 65.5 or more?) Of 1989 total hours, 366 hrs, 18% had dew points 58.5d or below, 272 hrs, 14% had dew points between 58.5 and 62, 253 hrs, 13% had dew points between 62 and 65.5, 523 hrs, 26% had dew points between 65.5 and 69, and 575 hrs, 29% had dew points greater than design conditions of 69d dew point.
WHAT IS MY POINT!? Proper AC sizing won’t make it run. Only 6% of our summer hours are near the design conditions that make an AC run the way we crow about. Comfort depends on dealing with both sensible and latent load. In contrast, 45% of all hours are near or greater than the design conditions for latent load.
Does Manual S address run time over an entire summer or just design conditions? Are we spending too much time micro slicing all the design variables when the discomfort gorilla in the room is actually a discussion about seasonal latent loads, latent capacities, infiltration, ventilation and other devices being added to the air conditioning system? Our sensible loads are getting too low to depend on the air conditioner to do it all.
And then once you acknowledge that we do need some additional devices, do you need to keep micro thin slicing the AC sizing procedures since the latent load might actually be better addressed by a machine that is running?
@Kris, a conventional
@Kris, a conventional recovery ventilation system (ERV/HRV) only dehumidifies/filters outside air. It has no way to remove moisture or contaminants from indoor air.
Interesting points Dan. I
Interesting points Dan. I look forward to responses from people that have thought about these issues way more than me. Do your observations about handling humidity with low sensible loads steer you toward something like a Minotair (http://www.minotair.com)?
Reid, I agree with Allison
Reid, I agree with Allison when he suggests an ERV is not a dehumidifier. http://energyvanguard.com/blog-building-science-HERS-BPI/bid/76792/An-Energy-Recovery-Ventilator-Is-NOT-a-Dehumidifier
A very popular name brand ERV I researched removes about one part moisture for every three parts ventilated into the home. I propose that trying to control excessive humidity in a home with an ERV is like trying to control your weight with the triple scoop ice cream cone diet. You simply order more and more triple scoop cones, always being sure to give one scoop to the dog from each cone, and continue until your weight is under control. But I understand why so many people are confused about this. I have read much of the ERV marketing and they are not quite telling the entire story.
@Dan wrote: …the design
@Dan wrote: …the design conditions that make an AC run the way we crow about… spending too much time micro slicing all the design variables…
Not sure what you mean here. No one said proper sizing is a panacea. It’s just one aspect of good design — a step in the design process worth writing about.
And I disagree with your generalizations about seasonal latent loads and capacities in homes with low sensible loads. A good designer can manage part-load latent conditions, often without resorting to additional equipment. Hint: the house is a system.
Oh I agree. The ERV/HRV
Oh I agree. The ERV/HRV would filter outside air and then mini-splits (ducted I suppose) would filter and dehumidify the interior air.
Dan, Note that the Minotair,
Dan, Note that the Minotair, unlike most ERVs, does not transfer moisture from the more humid stream to the less humid stream. Instead, it is a heat pump and removes moisture the same way an air conditioner does. I am not saying that this is the answer. I am asking the question because I honestly don’t know whether it is a good direction and this forum includes smart people that have thought a lot about these kinds of things.
Reid, …and I hope some of
Reid, …and I hope some of those smart people will contribute some insight and opinions on this device. Sorry I did not research the Minotair better before responding. It is obviously not a generic ERV as I assumed.
After reading everything the Minotair site offers, I am encouraged that we are still pushing technology to find a better way. But it looks too small for me and for the majority of the new homes I see in the Indianapolis area. I deal with energy efficient homes that still legitimately call for two to ten tons of cooling. Then my eventual conflict for some of these homes in certain conditions is when the AC does not run enough to deal with the latent load. This is especially true as mechanical ventilation becomes more prevalent. So when I refer to low sensible loads, I do not necessarily mean at design conditions, I mean, August 13 to August 18 this year in Indianapolis. During this period at my house, I did not need my 2.5 ton geothermal system very much, but I ran the dickens out of my whole house dehumidifier. We stayed wonderfully comfortable.
Dan, sorry for not being
Dan, sorry for not being clear regarding how a Minotair could be part of the solution to the problem you outlined. I wasn’t suggesting that it would replace the AC, but rather that it replaces the conventional ventilation system. Since the heat pump in the Minotair is small, it would still run enough on low load days to be effective in removing humidity. I don’t know whether it would be sufficiently effective for a large house. At least it wouldn’t contribute to the humidity problem like a conventional ventilation system does. On the other hand, it might be better to have a separate device whose only job is dehumidification rather than trying to do two jobs with one machine.
Reid, cool device! I was
Reid, cool device! I was wondering when we’d start seeing something like that on the marketplace.
Dan, I’m with you. As homes get better, and we bring sensible load down, latent doesn’t stay the same it goes UP! Ventilation needs don’t go away, and under worst case load the latent problem goes through the roof.
We recommend AGAINST recovery. I’m suspicious there isn’t much juice to squeeze on the recovery side, and now we are beginning to see the only way to effectively resolve iaq with confidence is through pressurization.
We also like the drying potential pressurized dehumidification offers.
A side benefit of keeping homes in the 45rh range is 76-79 setpoint are comfortable. A lot of good things start happening when you done need to keep homes so cold.
Reid, as I mentioned above, I
Reid, as I mentioned above, I’ve been waiting for a device like this for a long time. 2-300% efficiency on the energy recovery and dehumidification – fantastic.
The problem we are seeing now is we are finding, at least in retrofit, we do NOT want balanced ventilation for IAQ control.
We want pressurization. Unless you have a perfectly sealed house, controlled fresh air requires pressurization.
Let me restate – If you have an existing home with IAQ issues, we strongly recommend pressurization. In fact, we are seeing that extended use of exhaust fans may make homes go from positive to negative long enough that air quality backslides.
@Ted, re: positive pressure..
@Ted, re: positive pressure…
To the extent that IAQ issues are internally generated (odor, moisture, pet dander, dust, smoke, cooking, voc’s, etc.), exhaust/negative p is a good thing, no?
Also, maintaining a positive pressure balance in a cold climate is generally a bad idea. I hope the homes where you recommend a positive pressure balance have continuous insulation outboard of the sheathing.
John/Chris, I love mini’s for
John/Chris, I love mini’s for specific locations (Ie: an attic) and we are open to considering ducted mini splits as whole house solutions – we just haven’t seen a well formed argument for them except where regular ductwork Isn’t feasible.
The barriers for us are: Finding experienced installers, our lack of experience, lack of local resources, and lack of evidence there is any beneficial reason to use them.
Do either of you have case studies on how your installs have worked out, including why they were a better option than a standard high quality split systems?
David,
David,
We seem to be running across a lot of homes with air quality problems. Since most homeowners can’t completely gut and abate their homes, our approach has been to design solutions that fit client problems and budget. This means abate where feasible, tighten the snot out of the house, and pressurize. We really like to pressurize with a ventilating dehumidifier as it allows warmer comfort temperatures which in turn means *warmer surface temperatures* (and, of less import, nice energy savings).
In tracking relative humidity to health events, there appears to be correlation to adverse events when humidity levels above 50%, even when pressurizing.
We like the idea of pressurizing with dehumidified air as we suspect this increases drying potential to building components that these houses may never have previously seen. This is quite possibly due to oversized air conditioning and wintertime humidification.
Yes, spot ventilation is critically important. The observation about extended exhaust I thought might be helpful as it is one most people are unlikely to run across. After all, how many people here are continuously monitoring client home temperature, rh, indoor air quality, and health events?
🙂 –
Regarding your hypothetical “generally bad idea” – If you let every project become a science project, the search for perfection can become enemy of “great,” and nothing ever gets done.
Rule of thumb prescriptive hypotheticals from a building science book are good to understand so you don’t make catastrophically dumb mistakes, but you simply can’t remove 100% of all risk, unless all you do is armchair hypotheses. I know retrofit sales and design are not your wheelhouse, so you may have to just take my word on this.
And since we’ve started tracking indoor metrics, it’s become obvious these houses are too wet. Lots of them, too wet. Full Stop.
And even properly sizing the air conditioning, tightening the houses, and blocking moisture in the basements doesn’t solve the problem a lot of the time for some, and all of the time for any. Humid climates often have latent load with no sensible load, they even sometimes have latent cooling needs and heating load!
And in one recent situation the health problems had the client worried they were on the path to financial ruin. Those problems appear to be solved. They are ecstatic.
So it’s becoming clear that having an operating dashboard with logging is crucial. The technology is available so we no longer have to operate our homes accidentally, it’s time to take the blindfolds off.
Ted wrote: “science project”.
Ted wrote: “science project”… “perfection can become the enemy of great”…
Not even close. My comment (re: pressurizing in a cold climate) is basic building science. I would say your approach would is more akin to a science experiment. Good luck with that. See caveat noted in my previous comment.
Great info. Questions:
Great info. Questions:
1. With the increase in awareness, will we start to see smaller systems? It is currently almost impossible to buy a traditional split system under 1.5 tons, and if you need something “off the shelf” 2 tons is the smallest in stock.
2. Is the area of the unvented attic included in the calculation of your rule of thumb square footage?
Humidity is DEFINITELY a huge factor. Installed a new, smaller sized split system in a semi leaky house, and immediately noticed that a) my condensate water collection has about doubled; b) indoor air temp is very comfortable at 77 vs 72-73 with the old system; c) the house must be drying out as after 20 years there are nail pops in places they never were, which I don’t quite understand because I would think the low winter humidity would be lower than the summer conditioned humidity…
My impression is that the
My impression is that the increase in awareness if from a miniscule fraction of homeowners to a tiny fraction of homeowners. When it increases further from a tiny fraction to a small fraction of maybe even a medium fraction, then manufacturers might respond.
Availability of small enough equipment is mainly a problem for super-insulated homes and multi-unit buildings. For typical homes in most of the country, 1.5-2 tons is not grossly oversized.
There is a company in Canada, Dettson, that sells smaller split systems. I don’t know why they don’t get more attention. I didn’t choose them due to concerns about availability of local contractors to service them. Do contractors that participate on this forum have reasons for not offering them?
The curmudgeon in me says “no
The curmudgeon in me says “no way!”. The savings would have to come from the tract builders because it will have to be cheaper to spend $ on a properly sized/designed system vs. using guess work and oversizing.
What’s the cost difference? I have no idea.
Kris wrote: “It will have to
Kris wrote: “It will have to be cheaper to spend $ on a properly sized/designed system vs. using guess work and oversizing. What’s the cost difference?”
The cost difference between sizes is relatively small, and to truly get it right, the duct system may need to cost more. But system cost isn’t the only consideration driving this…
There’s a perception among builders, reinforced by hvac contractors, that bigger is better, and the corollary fear that smaller may lead to comfort complaints. The reality is that comfort complaints are rarely due to under-sizing, and in fact, comfort is enhanced by proper design.
There’s also the perception that design costs associated with right-sizing exceeds equipment savings. While that’s often true in the narrowest sense, there are larger economies to be had from proper design when the entire system (i.e., the house) is on the table. My clients nearly always spend less on their homes than what they would have spent had they followed the status quo approach.
@Reid, miniscule -> tiny? I
@Reid, miniscule -> tiny? I think you’re seriously underestimating the impact of above-code programs at a national level as well as better enforcement of code-mandated load calcs (despite the prevalence of BS loads in many markets). Moreover, I believe homeowners today are a lot more savvy about hvac than just 10 years ago.
I would hazard a guess than 20% of systems in new homes are within 25% on cooling capacity. That’s impressive progress since Energy Star first starting pushing proper sizing to builders in 2006. And distributors in some markets are telling me they’ve experienced and responded to increased demand for smaller equipment compared to 10 years ago.
Indeed, demand for mini-splits has skyrocketed over the last decade and US manufacturers are scrambling to participate through branding partnerships and even acquisition (Daikin/Goodman). That said, US manufacturers have been reticent to compete with Asian mini-split mfrs in product development in sizes less than 2 tons.
But where the equipment is being developed and manufactured isn’t what’s constraining the high performance home market. It’s the difficulty of getting hvac contractors on board with proper design, and/or getting home buyers & builders to see the value of 3rd party design. That’s is why we’re still seeing markets where smaller equipment isn’t stocked.
Change is hard…. which is why I see the progress that HAS been made as a glass half full rather than half empty.
There’s still one area where manufacturers could do better. We need smaller furnaces! I believe Dettson is the only manufacturer that offers furnaces with less than 40k capacity (it’s smallest model modulates from 6k to 15k). I don’t think many contractors are even aware of Dettson, but more than that, it’s difficult to get folks to break out of what they’ve always done.
Sorry for my late reply; I
Sorry for my late reply; I was out of town. Thanks for your insightful comments. I work primarily in TX, so design temps are 98 & 24.
I like using 2 stage or variable speed units, 16SEER and 96%AFUE. I believe the higher the rating the efficiency goes down.
If I was bldg. my house, I would use a 3 ton vs. 4 ton, because the 15-20% MJ oversizing. I’ve been working with the best HVAC contractor in DFW area, and yet there is still a lot of room for improvement in “higher-performing” systems, and we are already bldg. high-performing envelopes, so there is no low hanging fruit left out. Spending money to lower tonnage is not always effective.