Mr. Bean Proposes a Radical Change to Energy Codes
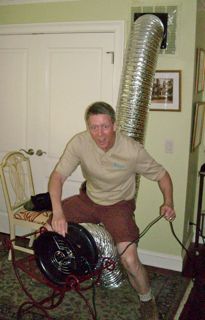
Evidently, I’m an oddball. We published a guest post by engineer Robert Bean on comfort and ASHRAE Standard 55 a few weeks ago, and when I first read the article, one sentence jumped off the screen, grabbed me by the collar, and yelled in my face, “Allison, you ignorant nut! Mr. Bean’s suggestion is radical! It’s revolutionary! It can help naked people all over the world.”
Now, you may think what he wrote wasn’t so radical. Maybe you didn’t even think it was particularly important. Perhaps you just have difficulty believing anyone who pretends that his duct leakage test equipment is a giant sandworm.
I guess most or all of the people who read the article felt underwhelmed as well because, even though I wrote in my introduction to the article, “Pay attention, because he makes a statement toward the end that, I believe, could lead to a great shift in our thinking about buildings,” no one commented on the part that I thought was so radical.
So, what did Mr. Bean actually say?
“If building codes dropped the reference to controlling air temperatures and switched the requirements to controlling mean radiant temperature, building performance specifications would have to change overnight.”
Whoa! Radical!
Why, you ask? It’s because even though home energy pros and building science geeks talk about the importance of mean radiant temperature (MRT), a lot of our building codes and practices focus on controlling air temperature rather than mean radiant temperature. I explained MRT a few months ago in an article that will be the title of the book I’m putting together now: Naked People Need Building Science. For a good technical description of MRT and operative temperature, which is a combination of the air temperature and MRT, see the Healthy Heating page on mean radiant temperature.
Here’s my personal experience with MRT and operative temperature. Ten years ago I built a high performance home out of structural insulated panels. It had little air leakage and was well-insulated, and I was more comfortable in that house than in any other I’ve lived in.
Because it had such a good building envelope, the MRT inside the house was high enough in winter that I could reduce the thermostat setpoint by several degrees Fahrenheit. An air temperature of 65° F, for example, was more comfortable than other homes I’ve been in with the air temperature of 72° F.
As Robert Bean explained it to me on the phone last week, the air and mean radiant temperatures behave like a teeter totter, with those two temperatures on opposite sides and the operative temperature at the fulcrum. As the MRT goes down, the air temperature needs to come up. When the the MRT goes up, as in the green home I built, the air temperature must go down.
So, what do you think would have to change in our building practices to control mean radiant temperature? How would energy codes have to change? If you’re a builder, have you recognized this issue, and how have you addressed it? Let’s hear it!
Related Articles
Thermal Comfort: Everyone Wants It but Few Know the ASHRAE Standard
Naked People Need Building Science
This Post Has 23 Comments
Comments are closed.
How do you measure the MRT
How do you measure the MRT though?
If you cannot measure it easily, how do you make the change that Robert Bean suggests?
I like complicated solutions,
I like complicated solutions, because they require more intentional thought and action. 🙂
MRT may or may not be a fun achor to tether our energy codes to. It reminds me of the comments from glass manufacturers to the energy obsessed DOE Build America Teams who were pointing fingers at the glass industry and making bold statements about what they should be doing. The Glass rep pointed out that windows serve multiple masters. They must resist the elements, be durable, allow light to flow in, allow the occupant to view the world, and have a degree of comfort. He didn’t include efficiency in the list. He took great pains to talk about percieved comfort of an occupant and how much more important it was to design spaces that were comfortable depending on their use and the clothing requirements for each space (bedrooms for example require less heat because the occupant is typically under multiple layers of insulation). Designing around the comfort index (for which there is an easy to follow guide) is a far superior approach and makes things like PH looks border line retarded. 😉
No Fair — I was expecting
No Fair — I was expecting something funny by the Real Mr. Bean, Rowan Atkinson!!
Not often you can fit a Kevin
Not often you can fit a Kevin Bacon reference into a building science article – Kudos
Paul P.:
Paul P.: If the building codes started using MRT, I don’t think there would be much or any requirement to measure it as part of the verification process. It would go into helping create prescriptive requirements to keep the MRT from tracking outside temperatures quite as much as they do now.
Michael A.: Complicated solutions are good. Simple solutions are good. I think Einstein put it best: “Everything should be made as simple as possible, but not simpler.”
Lorna F.: Ah, my plan worked to perfection! Just kidding (sort of), but I hope you got something out of the article anyway.
Gunther P.: Dang! I know I put a Dan Akroyd/Jane Curtin reference in there and a Frank Herbert reference, but I can’t really take credit for any Kevin Bacon references. In fact, I can’t even find one.
What prescriptive
What prescriptive requirements would you or Mr Bean suggest that would keep the MRT from tracking the outside temperatures?
Is it just more insulation and less thermal bridging as with all good envelopes and your SIP house? Or is it something more?
So Allison, what do you think would have to change in our building practices to control mean radiant temperature??
Paul. P.: MRT can be
Paul. P.: MRT can be calculated several ways as per ASHRAE Handbooks; can be specified and simulated as per various programs and measured in-situ with a matrix of embedded sensors or hand held devices along with a weighting calculation; or it can be measured using field instruments such as those made by LumaSense (aka Innova aka B& K )…
There are also commercially available “operative temperature” thermostats which integrate the dry bulb and mean radiant for control purposes. For a history lesson, a patent was filed in 1981 for an operative thermostat by ASHRAE member Morris Markel based on the work of researchers Berglund and Rascati. Others using different technologies are currently being developed by various control companies.
As a side note: The challenge (ultimately) with MRT is how it is calculated with more precise methods integrating a “where is it calculated” which incorporates angle factors and a level of calculation sophistication beyond most practitioners. Fortunately there is an ASHRAE Research project almost completed which is to, “Develop a radiant/convective system module for the simulation and analysis of spaces and systems” This contract was awarded to Wrightsoft and when done it will become part of the ASHRAE Thermal Comfort Tool which is the sister software to ANSI/ASHRAE Standard 55. That mew tool will allow users to build a 3D room around an occupant for predicting thermal comfort based on MRT and dry bulb.
For a starting point of further discussions here is where I’m coming from; like other codes, the National Building Code of Canada v2010 states in Section 9.33.3.1. Indoor Design Temperatures: “At the outside winter design temperature, required heating facilities shall be capable of maintaining an indoor air temperature of not less than …22°C in all living spaces,…”, however in Section A-5.3.1.2.(1) Use of Thermal Insulation or Mechanical Systems for Environmental Control, it states, “In addition to controlling condensation, interior surface temperatures must be warm enough to avoid occupant discomfort due to excessive heat loss by radiation.”
From my perspective, by including a specific value for air temperature but excluding specific values for surface temperatures, building codes segregate and “float” on one of the most powerful tools available in addressing thermal comfort, energy conservation and energy policy.
Thermal comfort validation of which MRT and operative temperature are included; is present in current programs such as LEED NC, but absent in residential construction programs….stand by on this as we have initiated preliminary discussions with program managers.
Paul, Your questions get right to the heart of the matter…and would get fleshed out in subsequent discussions….for now:
Re: What prescriptive requirements…one way…by simplified calculation (assumes a homogenous environment with a centrally located measuring point) an MRT within a degree or two of air temp is often found in high performance buildings; in my experience that being buildings with floor surface fluxes less than 10 Btu/hr/sf. Others? Sure…open for discussion.
Re: Is it just more insulation and less thermal bridging…yes and lower window to wall ratios or tradeoffs which include higher performing windows…and external shading…and tighter envelopes and and and….since all of these elements combined eventually get consolidated down to a surface flux.
Re: So Allison, what do you think would have to change in our building practices to control mean radiant temperature?? I can’t answer for Allison, but in my world, it begins by working backwards from maximum plant efficiency and indoor climate engineering specifications. In other words if it was code required that boilers, furnaces, heat pumps etc. had to operate at maximum engineered performance with systems designed to exchange the greatest Btu for the lowest kW whilst conditioning the occupants to meet indoor climate engineering specifications, building system would have to change in order to become an enabler of environmental systems (see below).
M.A.: re: “Designing around the comfort index”…I call this the inside out approach where indoor climate engineering specifications (and energy allowances) beget architectural specifications as opposed to the outside in approach where architectural specifications beget indoor climate engineering specifications. In the latter approach the architect hands the engineers the plans and says ok now make my building work; whereas the former has the engineers handing the architect the indoor climate engineering specifications and energy allowance and says ok now Mrs./Mr. Architect design a building which enables our systems to operate at maximum performance.
Lorna F.: Too funny…fyi – Rowan Atkinson was an electrical engineer by trade, no shock he makes more money acting (pun intended).
Gunther: Tremors, K. Bacon and the giant sand snakes…
One of his finest
One of his finest performances Tremors 2009
http://www.imdb.com/title/tt0100814/
I’d be happy if somebody
I’d be happy if somebody would come up with some sort of “empathy control” instead of a standard thermostat for cooling. Automatically lower setpoint when humidity levels are high.
It has always occurred to me,
It has always occurred to me, that with forced air heat, that radiant heat must be the factor that allows the furnace to turn off. Otherwise the furnace should be on all the time. If I measure the heat in the walls, ceiling etc it seems to be the factor that dictates comfort rather than the dry bulb setting.Measuring the BTUs needed is a direct relation to the MRT which is directly related to the comfort. The end sum is if you insulate well then the MRT, dry bulb temperature and heating cost are intimately entwined.Am I all screwed up?Cheers Mike
Robert: B. Thanks for the
Robert: B. Thanks for the detailed reply, still digesting but I am getting it better now. Measuring it a problem, but a human-friendly MRT internal envelope surface is a good thing.
Bob : I really like the idea of an “empathy control” a lot of people do seem to need that dial turned up.
Allison: any MRT thoughts? Good post.
Mike L
Mike L.: Re: It has always occurred to me…
Yes and sorta…what allows the furnace to turn off is reaching the set point of the thermostat which is supposed to represent conditions deemed “comfortable” but even when the conditions to satisfy the thermostat are such that it turns the furnace off it doesn’t “stop” the radiant exchange between the occupants and the space. Frankly you would never want to “stop” the radiant exchange since its necessary for cooling or said another way if the room was so warm that radiant exchange was destroyed the body would over heat.
When the furnace is on it does a couple of things: it reduces the convective/conductive losses from the body and it raises the surface temperatures in the space which also reduces the radiant losses from the body – both enable the body to retain heat. The problem with all but high performance buildings in cold climates is the rate of building heat loss exceeds the rate at which hot air can compensate for the cooling rate of the surfaces which exceeds the internal heat generated by the body…so the net result is heat is drawn out of the body at a rate faster than it can be replenished so you experience a cooling sensation. We expect the thermostat to emulate that experience but it can’t unless it actually sensed what you sensed.
With radiant heating systems the air is warm only because the surfaces are warm…warm surfaces reduce body heat loss or said another way radiant heating enables the body to retain heat in a cooler air temperature environment…this is also true for high performance buildings without radiant heating systems in moderate climates as already testified by those living in good buildings.
Re: If I measure the heat in the walls, ceiling etc.
It is “a” factor and very powerful one…see the article on the ASHRAE Standard and the ten factors of thermal comfort. Dry bulb represents only 1 of 10. Building performance and thus the radiant exchange matters – always has – always will – it cannot be ignored.
Re: Measuring the BTUs needed….
Yes.
Re: The end sum is if you insulate well then the MRT, dry bulb temperature and heating cost are intimately entwined.
Yes.
Re: Am I all screwed up?
No.
What is needed is a radical
What is needed is a radical change on what home designs are truly practical, long-term. This is a behaviour change as the technology exists today to create it (if it were socially acceptable). Human culture seems (in my observation) to follow the path of the wealthy. Wealthy individuals do not really care about residential building costs, energy costs, transportation costs, etc. as their disposable income is so high they have no trouble maintaining that spending level. Less-wealthy individuals (of varying economic “classes”) see what lifestyles the wealthy afford and emulate them to the degree they can afford (because their disposable income levels are not as high).
So instead of 4000 sq.ft., cathedral ceiling, turreted-windowed grand homes, the lesser-economic classes have no windows on the sides (that others rarely see) and lots of windows on the front (for public display) and rear (to watch the backyard).
[BTW – I believe this analogy
also works for automobiles, hence the proliferation of older luxury brand vehicles in inner-city settings.]
Designing for each room’s MRT is technically achievable today – it’s just that the majority of home buyers don’t want it because wealthy individuals didn’t want it before them (nor did they want super-insulated, passive-solar, or Passive House homes).
Now if Architectural Digest emphasized MRT-regulated homes in all their issues…
Bob wrote:
Bob wrote:
> I’d be happy if somebody would come up with some sort of “empathy control” … Automatically lower setpoint when humidity levels are high.
That would be a bad idea. What is needed is already available — humidity control. This can be accomplished with a humidity sensing thermostat (or separate humidistat) and one of several methods to increase an AC’s latent capacity (reduce fan speed, add hot gas re-heat for low cost off-cycle dehumidification, or a dehumidifier as last resort.
Simply reducing the setpoint would actually increase the RH in the short term, and perhaps even in the long run depending on the particulars of the hvac system, thus imposing a significant energy penalty. I can provide a short lesson in psychrometrics if required.
In many cases, high RH can be traced to one or more sources that can then be mitigated. Always best to attack moisture at the the source whenever possible.
Agreed, eliminating the
Agreed, eliminating the source(s) of moisture is the best option. Running the blower on lower speed to reduce humidity is also a great option IF there is enough of a sensible load to trigger A/C operation.
Hot gas reheat is an expensive retrofit for most installations, not practical for residential unless a new system is being installed in a high humidity climate.
Here in Oklahoma there are times when it’s wet outside but not warm enough to trigger to operation of a conventional thermostat. Current humidity sensing thermostats won’t trigger the system since it’s not warm enough (at least the White Rodgers line doesn’t).
Most people simply hit the “cooler” button on their thermostat when it “feels muggy” in the house. Having a thermostat that would lower the temperature about 1 degree for every 4% the space was over the humidity setpoint would help a lot IMHO. The stat could also raise the setting 1 degree for every 4% under the humidity setpoint, saving energy on days when the system runs a lot and humidity is low.
For example if the stat was set at 75 degrees @ 50% humidity and the space was 74 @ 60% humidity the stat would run the A/C until the house got to 73 @ 58% (humidity would go down because system would be running). Another example is if the house was 75 @ 40% the thermostat could raise the temperature to 77.
This thermostat is something that would be easy for HVAC contractor to install, even handy homeowners could do it. The stat could even have a “dehumid” terminal for use with Variable Speed furnaces or a Hi/Low relay on PSC blowers. This would help to get to the actual setpoint of 75/50% instead of overshooting for comfort. Installation of the dehumid feature would be optional, few homeowners would know how to wire up a PSC blower relay. PSC systems are 90% of what is in homes, although VS is slowly catching on.
White Rodgers has a “cool savings” feature that takes raises the temperature when the system runs a lot, and while fairly effective doesn’t take into account the actual humidity in the space. “Cool savings” also does not lower the temperature in cases of high humidity.
Bob wrote: “Most people
Bob wrote: “Most people simply hit the “cooler” button on their thermostat when it “feels muggy” in the house.”
Agreed. Not good. But your enthalpy thermostat would simply automate what we agree is bad behavior! The fact that the stat does it more precisely than the HO does not make it good.
“The stat could also raise the setting 1 degree for every 4% under the humidity setpoint”
It doesn’t work like that. Reducing the RH below about 55% will have little if any benefit in terms of dry-bulb comfort. This will just lead to comfort complaints.
In my previous home in Charlotte, RH generally stayed below 55% with ocassional excursions into the high 50’s (even low 60’s when there was no sensible load). I moved to SE Arizona about 5 years ago and we’ve only been able to raise the setpoint by 1 degree, even with indoor RH at 30%. During monsoon when RH ocassionally climbs into the low 50’s, we find we don’t need to reduce the temeprature to maintain comfort. So I would say that there’s about 1 degree of impact below 60%.
Above 60%, the impact of RH on comfort is greater, but maintaining comfort under these circumstances isn’t necessarily accomplished by reducing dry bulb temperature. For example, many areas of the country can have extended periods of damp weather in the fall and spring when there’s no sensible load (as you pointed out). In that case, the indoor temperature may be in the low 70’s, so the body senses cool and wet. That’s different from warm and wet, which is what your enthalpy stat is attempting to address. In particular, it makes no sense to reduce the temperature further when it’s already at the low end of the comfort range. This will just lead to comfort issues AND higher energy bills. When there’s a latent load and no sensible load, there are but two choices: dehumidify or stop the source.
A properly sized AC will prevent “warm and wet” in most cases, and as we agree, fan control will improve a system’s latent capacity. But if that’s not enough, there may be a narrow range of conditions in which lowering the stat one degree might (eventually) help. However, using your example of 74F/60%, lowering the temperature to 73 would initially *raise* RH to 62% (humidity ratio hasn’t changed yet). Depending on how quickly the AC satisfies the new setting, there’s likely to be no reduction in RH during first several cycles. Keep in mind it typically takes the evap coil at least 10 minutes to begin condensing moisture. More likely, it would take several days to see a significant reduction in RH, depending on sensible loads and whether the system is properly sized. Moreoever, because of the long lag times involved, again, this strategy would expend energy while creating even more comfort issues. One more thing, if your enthalpy stat were installed on a home with a grossly oversized AC (e.g., zero latent capacity), you’d end up with very cold occupants and very high energy bills.
I just know when humidity is
I just know when humidity is high in my own home 74 feels warm and I’ll bump it to 72. Agreed, above 55% is when it has the most effect, I normally won’t bump the stat if RH is already below 50%.
I do have my own “redneck variable speed control” on my furnace that runs the blower on low for the first 7 minutes then switches to high speed. It’s a simple SPDT relay controlled by a delay on make timer set to 7 minutes. Red (low) blower speed goes on NC relay contacts, Black (high) goes on NO contacts. Common of relay goes to “cool speed” on furnace control board. On the 24V side one terminal of relay goes to common, the other goes to delay on make timer. Delay on make is wired between “Y” and relay coil.
Works well considering it costs less than $20 in parts. Helps with coil getting colder quicker and starting the dehumidification process. During low load conditions, the cycle is rarely over the 7 minutes required to engage the relay. Under high load conditions the A/C spends most of its time on high speed.
re: “redneck variable
re: “redneck variable speed control”
I’m impressed, from one redneck to another.
I wasn’t the first to come up
I wasn’t the first to come up with the idea, this webpage explains it a bit better:
An alternative to changing the thermostat or adding a dehumidistat is to use a Delay-On-Make timer. Since we know the majority of cooling operating hours are at less than outdoor design conditions, we can operate the blower at a reduced cfm for the first 5 to 10 minutes of thermostat demand in anticipation of humidity complaints.
Install a Delay-On-Make timer in series with “Y” and the dehumidification relay coil. So a “Y” output from the thermostat will energize the outdoor unit contactor and the added timer, which will energize the added dehumidification relay after the selected time delay period.
Connect the normally open blower relay contact to the dehumidification relay SPDT common terminal.
Connect the slower blower motor speed tap to the dehumidification relay normally closed contact.
Connect the faster blower motor speed tap to the dehumidification relay normally open contact.
On each cooling demand, the blower operates at reduced cfm until the timer period has ended, at which time the blower will operate at higher cfm to finish out the cooling cycle.
http://www.fluke.com/Fluke/usen/community/fluke-news-plus/ArticleCategories/HVAC/Battling+High+Humidity.htm
There are a lot more things
There are a lot more things to consider than simply reducing the air speed of the blower. By reducing the air speed you can cause system performance issues,distribution problems,sweating duct due to lower temps, flash point of the refrigerant (fixed metering device)and discomfort due to lower output temps of the system.
I am very cynical of the dehu controls that simply lower the air speed to drop the coil temp.
P.S. Great article/discussion Allison !
James Jackson wrote: &
James Jackson wrote:
“By reducing the air speed you can cause system performance issues, distribution problems, sweating duct due to lower temps, flash point of the refrigerant (fixed metering device) and discomfort due to lower output temps of the system.”
You forgot one – icing the evap coil. All all these outcomes are indeed possible, but only if the person designing the system doesn’t know what they’re doing.
Commercial (and residential dehumidification systems operate every day in this manner. To the extent that high RH is coincident with a sensible load, it’s a lot more efficient to use a 13 SEER (or higher) air conditioner to manage RH than one of those stand-alone dehumidifiers with toy compressor.
David Butler wrote: ”You
David Butler wrote: ”You forgot one – icing the evap coil. All all these outcomes are indeed possible, but only if the person designing the system doesn’t know what they’re doing.”
I didn’t forget icing the coil, Its just unlikely the coil would actually ice in the 7 min low speed delay. Frost maybe but the other issues would be present with exception of the duct sweating, that takes a little more time. I completely agree with your comment about only the person designing the system doesn’t know what they’re doing.
I am of the opinion that the only way to properly control humidity is to slow or remove the source, then design the system according to manual J then select the proper unit using Manual S for the sensible/latent load.
My point was mainly to know the equipment you are altering. If you changed the air speed permanently or temporarily with a time delay on a system with a TXV and a accumulator its not that big of a deal. The bigger problems are present when you drastically lower the air speed on a unit with a fixed metering device.
I get calls quite often from contractors that have installed a new HVAC system with new sealed and R8 insulated ducts that are sweating like crazy. The majority of the time I find the unit is a single stage system in Dehu mode allowing the air to spend too much time on the coil, dropping the temp in the ducts well below DP. The fix is simple increase the air speed to close to 400 CFM per ton durring the regular cooling cycle then set it to drop to around 350 per ton for temporary dehumidification.
If you are going to install a relay to slow the air speed across the coil just make sure you look at the engineering specs on what the fan can produce at certain speeds and static pressure readings and try not to lower the CFM more than 50-60 CFM per ton. High to Medium or Medium-High is probably closer to a safe range.
This whole discussion makes a
This whole discussion makes a huge assumption, i.e. that anyone has done a heat load of any kind before starting construction of a new house.
Unfortunately modulation has not improved the situation as it gives the average contractor, 99% or so, more “perceived” latitude in over-sizing HVAC equipment.
While we consider MRT standards (brilliant Mr. Bean), the industry slogs along in the 19th century.
Though the installing HVAC contractor is responsible for installation, and sometimes maintenance, the builder rarely hires the forward thinking HVAC contractor. Ultimately we have to advocate for the homeowner to seek out and insist on contracting for mechanical systems directly with a qualified HVAC contractor.
Of course we could get Architects to consider HVAC systems and creature comfort as the first order of business but you would have to start with taking their window away…good luck with that!