R-Value vs. Thermal Resistance
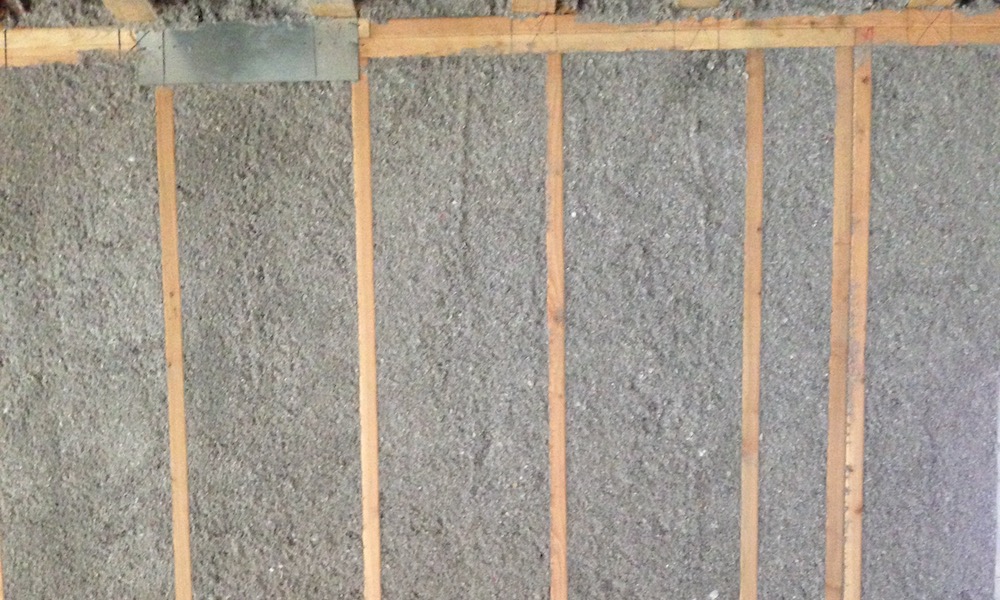
I’ve been known to argue for using building science terms correctly. I’ve written articles about how we shouldn’t use the word “breathe” in relation to houses and that air doesn’t have any capacity for holding water vapor. I’ve even written a book (coming out this summer!) whose title is related to breathing houses. Today I have another terminology issue: R-value vs. thermal resistance. But this time, I’m just here to educate. I’m not going to try to persuade you to change your ways because I’m probably not changing mine.
The true meaning of R-value
The term R-value has a specific, legal definition. Because of scams in the 1970s, the US Federal Trade Commission (FTC) created the R-Value Rule to regulate the use of that term. I wrote in a 2013 article:
“The R-value Rule requires testing insulation using one of four American Society of Test Methods (ASTM) standards. The basic requirement is that the mean temperature must be 75° F (24° C) with a temperature difference of 50° F (28° C) across the insulation. According to Building Science Corporation, most R-value testing is done with a temperature of 50° F (10° C) on the cold side and 100° F (38° C) on the hot side.”
From that, you can tell that R-value isn’t the correct term for what we get by averaging the heat transfer effects of combinations of insulation, wood, drywall, sheathing, and all the other components in building assemblies. Why? Because that’s not what gets tested. Individual materials get tested using one of those ASTM tests. Not assemblies.
And it’s not all materials either. It’s pretty much only materials intended to be used as insulation. The FTC’s R-value applies to products marketed and sold with an R-value. That prevents companies from doing things like claiming their miracle product (e.g., insulating paint) has an R-value of 100 in a mere one millimeter of thickness.
Even a thick shag carpet sitting on a foam pad doesn’t have an R-value. It certainly could be tested and labeled with one. But carpet companies don’t get their products tested, and thus carpet does not have an R-value.
The term that really applies most of the time
So if R-value is the wrong term when we talk about heat flow through wood or carpet or walls, what is the right term? Of course, you already know because it’s in the title of this article: thermal resistance. When heat flows through any material, it encounters resistance. In some materials, it encounters significant resistance, and those are the things we use for insulation. In other materials, the resistance is smaller, as in wood or glass.
Now, let’s take it a step further. R-value isn’t always correct even for insulation that has been through the ASTM testing. The title of that 2013 article I quoted from above is Big News: The R-Value of Insulation Is Not a Constant. According to what I’ve written here, that title is wrong. If we’re using the term R-value correctly, it IS a constant. It’s just the result of the test. The thing that changes with temperature (the subject of that article) is thermal resistance.
To summarize, R-value vs. thermal resistance is an important distinction to understand mainly for anyone selling something labeled with an R-value. But I suppose you should be careful of someone trying to sell you something by claiming it has a “thermal resistance of 100” or some other crazy high value.
R-value has a specific meaning to protect anyone who buys products intended to reduce heat transfer. In building science discussions here and elsewhere, you’ll see talk of whole-wall R-value or average R-value. Most of that kind of talk really is about thermal resistance, though.
Hat tip to Marcus Bianchi, PhD, of the National Renewable Energy Lab. He helped me understand this issue better when he gave me feedback on part of my upcoming book.
Allison A. Bailes III, PhD is a speaker, writer, building science consultant, and the founder of Energy Vanguard in Decatur, Georgia. He has a doctorate in physics and writes the Energy Vanguard Blog. He also has a book on building science coming out in the summer of 2022. You can follow him on Twitter at @EnergyVanguard.
Related Articles
Big News: The R-Value of Insulation Is Not a Constant
Does Poor Installation of Insulation Hurt R-Value?
The Layers and Pathways of Heat Flow in Buildings
Comments are moderated. Your comment will not appear below until approved.
This Post Has 12 Comments
Comments are closed.
This was a helpful review of the (limited) role of R-Value, but time / resources / enthusiasm permitting, could do with being fleshed out a bit with some examples of how R-value is combined with thermal resistance of non-R-Value rated components (such as wall framing components and , yes, foam backed shag carpet) to give us U-factors for use in building science / load calcs, etc.
Well as long as we are nitpicking . . . .
Thermal resistance was developed from an electrical analogy where electrical resistance, R, is defined by V=IR where V is voltage difference and I is current (amps). Thus, R has units of V/I or volt/amp which is defined as ohm. For the thermal analogy using thermal resistance (Rt), Q=T/Rt or T=QRt, where T is temperature difference (analogous to V) and Q = heat transfer rate (analogous to I). Thus Rt has units of T/Q or F-h/Btu. However, R-value has units of ft2-F-h/Btu. So it is not a thermal resistance at any condition. Perhaps it is a thermal resistivity? Electrical resistivity (rho) is a material electrical property and is defined by the equation, R=(rho)L/A where L is the length (thickness) of the material in the direction of electrical flow and A is the cross-sectional area of the material across the electrical flow. It has units of ohm-ft or volt-ft/amp. So by analogy, thermal resistivity would have units of ft-F-h/Btu which is not the units for R-value. So what is R-value? It is the the thermal resistance of a square-foot of material with a fixed thickness. Or you could you say that it is the thermal resistivity times the thickness of the insulating material. Note that the thermal conductivity of an insulating material is the inverse of its thermal resistivity and has units of Btu-in/h-ft2-F.
If you have read this far, you have probably wasted your time, but I had nothing better to do during lunch today!
Thanks for the technical definition of R-value vs thermal resistance. My comment is actually related to your article: I am familiar with the terms and have read the method instructions for determining R-value (about 35 years ago). My question is a bit farther reaching as regards to the thermal resistance of wood; specifically logs. I have tried to read and understand much of “The Wood Handbook” written and published by the US Forest Service. I am particularly interested in the chapters on drying wood and the meanings of the terms “Green”, “Air Dried” with an emphasis on “Kiln-Dried”. I use only Fully Kiln Dried EWP (as determined by the procedures in “The Wood Handbook”) when building a log home. (I prefer to build using Metal SIPs with log siding). All of this is leading to the question or observation that many in the industry claim “8” log walls are equivalent to a 6″ fiberglass insulated stud wall in performance due to Thermal Mass” (without regard to the moisture % at the center of a log). The biggest problem I have experienced is the term “Kiln-Dried” is VERY loosely used and there is NO governing authority to require testing to claim the term “Kiln-Dried” like the testing that was required to establish the R-value Rule because of so much abuse of the term and false claims. When is a governing authority going to require proper testing for a log supplier to perform testing as described in “The Wood Handbook”? Dr. Bailes and All readers: Please feel free to tear my comments apart or give good observations or explain who I can write to in order to explain my experience and dismay that there aren’t any regulations re: the above. (I am looking forward to receiving my copy of your new book!)
I think what you are getting at is U-Factor, the reciprocal of R-Value. U-Factor is usable for all assemblies, even those not tested for R-Value, such as foam backed shag carpet.
I enjoy articles like this, but at the end of the day I find myself asking “so what questions need to be asked and answered so that the rest of us can make use of it?”. In the case of residential housing, I am interested in the effect of the ‘assembly’ on heat retention, and a comparison of various materials, methods or such that make it better or worse. I suppose one might say that is the role of engineers, but there ought to be some easier way to take, for example, 6 common building methods and materials and tell all of us how well it retains heat.
That’s my point in the post immediately above – Assembly U-factors give us the info we need to assess, calculate, and model real world performance of actual buildings.
Thanks. I have only seen U-factors for Windows, but not assemblies. Have you found such a thing? For example, if I have R-48 SIP walls (no transfer) and Pella triple pane windows, can I get close to an assembly U-factor? I suppose you have to add in raised floor, underfloor insulation and a number of other things, but at this point I am so far away I can’t find much use for it.
Actually, I think what you get in the NFRC label for windows and doors are in fact “Assembly” figures – they incorporate the frame, mullions, muntins, etc.
I have long wondered about the relationship of a material resisting the heat transfer vs retaining the heat itself. In a cooling situation , it seems advantageous that my wall assembly not let the outside heat transfer into my house quickly, but that same night I don’t want the heat my wall assembly absorbed during the day to radiate into my house either. So in a way I am looking for the total effect of the insulation over a 24 hour period.
If anyone can point me to the math on this I would appreciate it. Otherwise I might cover my house inside and out in tin foil with a 2 inch air gap.
The ability to “retain” heat is thermal capacitance (some call it thermal mass) which is a different property than thermal resistance. Its impact is much more difficult to predict because it depends on where those materials are located in the wall assembly and how the indoor and outdoor temperatures vary with time. The ASHRAE Handbook of Fundamentals is a good reference if you want to learn more about it.
Some say that you want high thermal capacitance on the indoor air side of the envelope. I disagree. To get enough indoor air temperature variation for this capacitance to have an impact, you would probably be uncomfortable. It should be on the outdoor air side of the envelope (e.g., brick or concrete block) to dampen the impact of outdoor air temperature and solar heat gain fluctuations.
Roy – you make an interesting point, but I’d like to add some comments having lived in both heating and cooling dominated climates about roles of thermal mass
1) In a heating dominated climate, it can be acceptable, even desirable for a thermal mass within the envelope be intermittently heated, such as by sun or a woodstove or similar, and then release its heat late at night when outdoor temps are at their lowest. Proponents of this approach may be satisfied by the central core / daytime use rooms of a home being kept warmer by thermal mass while outlying bedrooms are allowed to get a bit cooler – curl up with each other or extra blamkets.
2) In a cooling dominated climate, I personally enjoyed an ICF (Insulated Concrete Forms) home – that variant puts the thermal mass in the middle – split between two layers of insulation. The benefit of thermal mass in a hot humid climate is in the delay of solar gain – the hot afternoon peak is reduced. There is also benefit in the thermal mass releasing some heat into the home well after dark – that delayed sensible gain “gives the HVAC system something to do” well after dark; indeed all night long. In other words, the slow release of some stored heat into the home all night long causes the HVAC to operate, at least intermittently, all night long. This improves comfort by reducing humidity since conventional HVAC systems manage latent gain only indirectly, in other words only when there is some sensible heat gain to activate the system thermostat.
A conventional light frame home won’t carry enough sensible heat long enough into the dead of a hot muggy night to create enough load for the HVAC to manage humidity.
Hi Curt:
I am not a fan of indoor temperature swings so I don’t have much use for internal thermal capacitance. This is just personal comfort preference.
Since I can’t stop outdoor temperatures swings, I am OK with thermal capacitance in the outdoor building layers, especially brick exteriors. Flattening the diurnal heating or cooling load on a building is generally a good thing. Keep in mind that this load dampening is not only a function of the thermal capacitance of the building material. When you do the detailed transient heat conduction analysis, the dampening effect is a function of the thermal resistance times the thermal capacitance. This becomes evident when you look at the units of thermal RxC which is F-h/Btu multiplied by Btu/F which gives units of time (hours). So increasing the thermal resistance of the building envelope also helps it dampen diurnal load profiles. In addition, increased thermal resistance also reduces overall (average) heat loads whereas thermal capacitance does not. So I am making the case that increased thermal resistance always helps with thermal loads whereas increased thermal capacitance only has limited benefits.
The real reason that I like brick exteriors is that I don’t have to paint it in the future, although for some strange reason around here, people are painting brick, even on new homes. I don’t get it.