This Lack of Building Enclosure Design Makes Extra Work
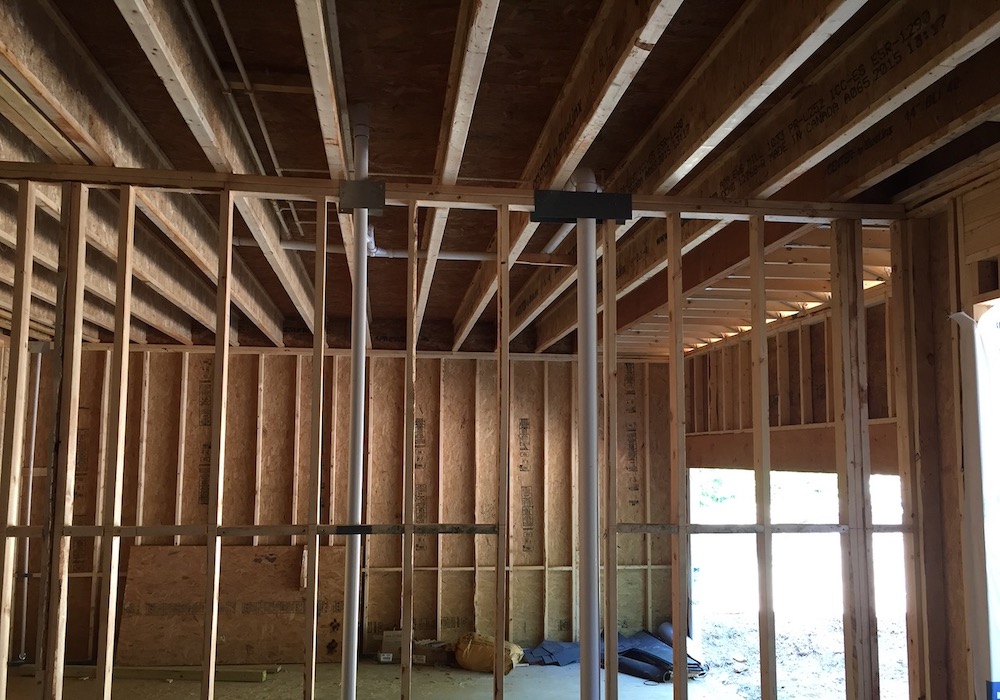
Take a look at the photo above. See anything missing? If you don’t see it yet, look at the big opening at the bottom right of the photo and you should be able to deduce what that room is. It’s a garage. Now look at the framed wall between the garage and the inside of what will be the living space, which is where I was standing when I took the picture. You see it, right?
This house is in Georgia. We were the first state to require all new homes to pass a blower door test. Unless they fill the big holes between the floor joists, this house will not pass the blower door test. It won’t.
Because the ceiling framing there is done with I-joists, it’s not a simple matter to do the blocking and air sealing required here. Yes, it can be done, but it’s going to be extra work.
Also, when I visited the house, they didn’t have the ducts installed yet. If they make the mistake of running flex duct through those joist cavities, their air-sealing job just became magnitudes more difficult. Yeah, you can sort of do it, but it’s not gonna do a great job.
But the thing that gets me when I see this is that it could have been avoided. If instead of having joists running right across that wall they had run the framing the other way, they could have a solid piece of wood there. Seal the edges and penetrations and you’re done. They also could have kept the joists running the same direction but not made them continuous. Just butt them into a perpendicular joist on top of that wall.
Unfortunately, few homes have detailed framing plans, and many of those that do have them don’t get reviewed for this type of problem. This failure of design makes extra work for the builder.
Allison A. Bailes III, PhD is a speaker, writer, building science consultant, and the founder of Energy Vanguard in Decatur, Georgia. He has a doctorate in physics and writes the Energy Vanguard Blog. He also has a book on building science coming out in the fall of 2022. You can follow him on Twitter at @EnergyVanguard.
Related Articles
Building Enclosure Blunder in the Basement
Are You Making These Mistakes with Your Garage?
I-Joists, Attached Garages, and the Air Leaks That Poison
NOTE: Comments are closed.
This Post Has 24 Comments
Comments are closed.
My first thought would be,
My first thought would be, well they screwed up, BUT if they block/install a gypsum ceiling (which is required for fire separation) This would separate the garage from the conditioned/sealed space. would that provide the sealing needed to pass a blower door test?
<b>Doug K</b>: I
<b>Doug K</b>: I’ve tested houses with drywall ceilings in the garage, and if they joists are wide open, a lot of air still gets through. Blocking would reduce it, but since they used I-joists, there would still be plenty of bypasses. They’d have to seal all those gaps in the indentation between the I-joist flanges, too. <br /> <br />
We strongly encourage,
We strongly encourage, borderline demand, that new homes into which we install HVAC get blower door tested before drywall goes up. <br /> <br />We smoke test most attic foam retrofits using reversed blower door fan. <br /> <br />We have begun to add a required blower door test result near the top of page one of new home HVAC proposals. Of course we can’t and don’t compel compliance, but it serves to concentrate minds on the issue and gives us some leeway on future comfort / humidity complaints. <br /> <br />We recently had a new foam contractor bow up a bit, demanding our certification to perform the test, but his tune changed about 10 minutes later when the wind began to whistle through gaps in his foam. <br /> <br />
HEY Curt … been there/ done
HEY Curt … been there/ done that! <br />A Builder who brags about using foam insulation but who fails to test… that’s the one blowing smoke ! 😉
Many States do not enforce
Many States do not enforce their duct and/or blower door Code requirements, ensuring that designers and builders never learn how badly their houses perform.
Spray foam to the rescue!&
Spray foam to the rescue! <br /> <br />Even rudimentary blocking in the joist spaces above the partition wall to fill the big voids and a healthy squirt of 1/2 lb spray foam and they’re golden…air-sealed and insulated. The spray foam won’t shrink, settle, or delaminate over the 100 plus years we hope this house is in service, and if they continue the foam across the ceiling of the garage to the leakiest place in every house, the rim joist, they’ll have a warm floor in the room above the garage. <br /> <br />Low-density spray foam got its start in Toronto back in the 80s in exactly this application, where the bonus room above a garage was impossible to heat using fibrous, air-permeable insulation. One year 80% of construction defect claims in Toronto were from cold floors in these bonus rooms. <br /> <br />The other challenge in this house is the cantilever above the garage door. Foam will fill it, air-seal it and insulate it, but I doubt any other type of insulation and air sealing system could effectively solve this problem. Of course all responsible contractors combine the spray foam with a simple caulking package to address the air leak zones where we’re not spraying foam like the juncture between the bottom plate and the floor deck. With a little common sense and use of modern materials, it’s easy to get a very well sealed, high performance home. <br /> <br />We know we have a solution to effectively air-seal this home, and regardless of the method and materials used, we know we’re going to build it tight, so who’s going to ventilate it right?
My first thought would be,
My first thought would be, well they screwed up, BUT if they block/install a gypsum ceiling (which is required for fire separation) This would separate the garage from the conditioned/sealed space. would that provide the sealing needed to pass a blower door test?
Doug K: I
Doug K: I’ve tested houses with drywall ceilings in the garage, and if they joists are wide open, a lot of air still gets through. Blocking would reduce it, but since they used I-joists, there would still be plenty of bypasses. They’d have to seal all those gaps in the indentation between the I-joist flanges, too.
This detail is doubly
This detail is doubly important because it’s not just a question of efficiency. It’s a health and safety concern and has been a long-standing item on our Northwest ENERGY STAR checklists. A perpendicular joist on top of the wall plate is the easiest behavior change for the builder/subs. Bottom line, though: tackle these issues pre-construction through an integrated design process with subs. Put some coffee and donuts out on a table and get these guys talking to each other. they’re problem solvers.
We strongly encourage,
We strongly encourage, borderline demand, that new homes into which we install HVAC get blower door tested before drywall goes up.
We smoke test most attic foam retrofits using reversed blower door fan.
We have begun to add a required blower door test result near the top of page one of new home HVAC proposals. Of course we can’t and don’t compel compliance, but it serves to concentrate minds on the issue and gives us some leeway on future comfort / humidity complaints.
We recently had a new foam contractor bow up a bit, demanding our certification to perform the test, but his tune changed about 10 minutes later when the wind began to whistle through gaps in his foam.
HEY Curt … been there/ done
HEY Curt … been there/ done that!
A Builder who brags about using foam insulation but who fails to test… that’s the one blowing smoke ! 😉
Many States do not enforce
Many States do not enforce their duct and/or blower door Code requirements, ensuring that designers and builders never learn how badly their houses perform.
Spray foam to the rescue!&
Spray foam to the rescue!
Even rudimentary blocking in the joist spaces above the partition wall to fill the big voids and a healthy squirt of 1/2 lb spray foam and they’re golden…air-sealed and insulated. The spray foam won’t shrink, settle, or delaminate over the 100 plus years we hope this house is in service, and if they continue the foam across the ceiling of the garage to the leakiest place in every house, the rim joist, they’ll have a warm floor in the room above the garage.
Low-density spray foam got its start in Toronto back in the 80s in exactly this application, where the bonus room above a garage was impossible to heat using fibrous, air-permeable insulation. One year 80% of construction defect claims in Toronto were from cold floors in these bonus rooms.
The other challenge in this house is the cantilever above the garage door. Foam will fill it, air-seal it and insulate it, but I doubt any other type of insulation and air sealing system could effectively solve this problem. Of course all responsible contractors combine the spray foam with a simple caulking package to address the air leak zones where we’re not spraying foam like the juncture between the bottom plate and the floor deck. With a little common sense and use of modern materials, it’s easy to get a very well sealed, high performance home.
We know we have a solution to effectively air-seal this home, and regardless of the method and materials used, we know we’re going to build it tight, so who’s going to ventilate it right?
This detail is doubly
This detail is doubly important because it’s not just a question of efficiency. It’s a health and safety concern and has been a long-standing item on our Northwest ENERGY STAR checklists. A perpendicular joist on top of the wall plate is the easiest behavior change for the builder/subs. Bottom line, though: tackle these issues pre-construction through an integrated design process with subs. Put some coffee and donuts out on a table and get these guys talking to each other. they’re problem solvers.
I tend to go along with Doug
I tend to go along with Doug K. on this one. How is it possible to blower door test a house with an integrated garage space within the envelope? That floor above the garage should be considered conditioned space unless the entire first level is garage/basement like we have with elevated homes in a flood plain. Now if the walls between the garage and living space are shear walls and sheathed with OSB or plywood, you can address this in a different manner.
I tend to go along with Doug
I tend to go along with Doug K. on this one. How is it possible to blower door test a house with an integrated garage space within the envelope? That floor above the garage should be considered conditioned space unless the entire first level is garage/basement like we have with elevated homes in a flood plain. Now if the walls between the garage and living space are shear walls and sheathed with OSB or plywood, you can address this in a different manner.
The first thing that came to
The first thing that came to mind is how will they prevent CO infiltration?
The first thing that came to
The first thing that came to mind is how will they prevent CO infiltration?
Yes, that was my first
Yes, that was my first thought as well. This can’t be that common? Really?
Not quite related to this
Not quite related to this particular detail, but I am trying to get my builders to get away from using a plastic vapor barrier behind the drywall and move over to air sealing the attic floor with foam packs after the drywall goes up. No plastic = proper adhesion to drywall and top plates. It’s easy to foam ALL penetrations (and potential leaks) from above, then use a vapor barrier paint or primer on the drywall. <br /> <br />Presently, many leaks are missed, especially electrical boxes/drywall intersections as electricians only air seal from inside the boxes, before the drywall goes up. Unfortunately the contractor mantra tends to be "we fear change". <br /> <br />If our cars leaked like our homes there would be anarchy in the streets. Mandatory blower door testing!!
Not quite related to this
Not quite related to this particular detail, but I am trying to get my builders to get away from using a plastic vapor barrier behind the drywall and move over to air sealing the attic floor with foam packs after the drywall goes up. No plastic = proper adhesion to drywall and top plates. It’s easy to foam ALL penetrations (and potential leaks) from above, then use a vapor barrier paint or primer on the drywall.
Presently, many leaks are missed, especially electrical boxes/drywall intersections as electricians only air seal from inside the boxes, before the drywall goes up. Unfortunately the contractor mantra tends to be “we fear change”.
If our cars leaked like our homes there would be anarchy in the streets. Mandatory blower door testing!!
Yes, that was my first
Yes, that was my first thought as well. This can’t be that common? Really?
I DON’T NEED TO REPLY TO
I DON’T NEED TO REPLY TO ANYONE’S STATEMENT. I HAVE A QUESTION I HOPE SOMEONE CAN ANSWER. IT IS 85 DEGREES OUTSIDE AND MY HEAT PUMP IS RUNNING COLD AIR AND ALL OF A SUDDEN IT STARTS BLOWING HOT AIR. I JUST HAD A NEW A-COIL INSTALLED ON 9-1-15 ON TOP OF MY FURNACE BECAUSE IT WAS BLOWING HOT AIR. CAN SOMEONE THAT KNOWS WHAT THEY ARE TALKING ABOUT TELL ME WHAT THE PROBLEM IS.
I DON’T NEED TO REPLY TO
I DON’T NEED TO REPLY TO ANYONE’S STATEMENT. I HAVE A QUESTION I HOPE SOMEONE CAN ANSWER. IT IS 85 DEGREES OUTSIDE AND MY HEAT PUMP IS RUNNING COLD AIR AND ALL OF A SUDDEN IT STARTS BLOWING HOT AIR. I JUST HAD A NEW A-COIL INSTALLED ON 9-1-15 ON TOP OF MY FURNACE BECAUSE IT WAS BLOWING HOT AIR. CAN SOMEONE THAT KNOWS WHAT THEY ARE TALKING ABOUT TELL ME WHAT THE PROBLEM IS.