Unicorns and Good Home Performance Retrofits: Two Elusive Critters
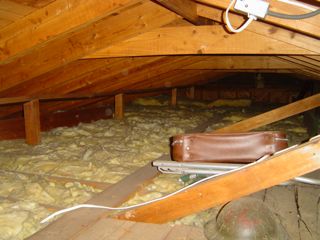
Guest post by Ed Voytovich of Building Efficiency Resources (The BER). I know Ed mainly through our interactions in the LinkedIn RESNET BPI group, where he’s a frequent and knowledgeable contributor, though we also met IRL (in real life) at the RESNET conference last year. He’s one of the most experienced and forthright people in the industry, and, like me, he’s a guy with a PhD who found himself working on houses. ~ ab3
Guest post by Ed Voytovich of Building Efficiency Resources (The BER). I know Ed mainly through our interactions in the LinkedIn RESNET BPI group, where he’s a frequent and knowledgeable contributor, though we also met IRL (in real life) at the RESNET conference last year. He’s one of the most experienced and forthright people in the industry, and, like me, he’s a guy with a PhD who found himself working on houses. ~ ab3
~~~~~~~~~~~~~~~
I’ve been in probably 2,000 attics over the years. I always tend toward underestimation in cases like this, so that I don’t sound like my late mother. I’ve also sold and created specs in the past for a fair number of retrofits (although usually without being able to check them when they were done).
“Out of all those inspections and projects,” you ask, “how many were clearly top-quality jobs, fully consistent with best practice, BPI standards, and common sense?” A reasonable estimate in my climate can be based even without testing upon two criteria. Evidence of serious snowmelt on roofs is a pretty good one, but valid customer complaints are even better.
A personal favorite was a 900-square-foot Cape Cod in Syracuse with an unfinished second floor and occupied solely by a retired lady librarian. I was called in via the grapevine as an independent adviser because she was no more comfortable after the work than she was before. She got out her audit report as provided by her contractor, and it said she would save $1,300 in energy costs the first year the work was done. I swear on the head of my late dog Dinger: I saw this with my own eyes.
Why is this amazing? Her previous year’s total cost for natural gas to heat, cook, dry her clothes, and make hot water was $800. Ladies and gentlemen, this kind of absurdity shoots the home performance industry squarely in the metatarsals.
My estimate of the number of top-quality retrofit building performance jobs that I have seen on the retrofit side is somewhere between darned few and pretty darned few. The rest ranged from flawed to downright miserable.
Maybe my experience is unusual, or maybe I’m too critical, but I think there is a good reason why there’s so little excellent work. Forget the testing that we love to discuss in minute detail. Air sealing and insulating are hard, physically challenging, uncomfortable, repetitive, dirty jobs that don’t usually pay very well.
It’s hot up there in the summer and cold in the winter. There’s mouse poop in the improperly installed pink stuff. Every time you want to get started blowing the walls, it’s raining, snowing, or hotter than the hinges of Hades. You are constantly in peril of stepping through the ceiling, drilling through a wire, popping off the sheetrock, or letting the indoor cat out. Spray foam doesn’t come out of your hair, and cleanup never ends. Nobody drops out of medical school to pursue a career working in the field as a building performance improvement installer.
Then, when the crew is all done, there is rarely anything the homeowner can look at and say, “Isn’t that just beautiful.” There’s no immediate positive feedback. Even the HVAC guys can show off a shiny new piece of equipment (although they do have to live with the old complaint that the duct mastic looks untidy).
You’re probably thinking to yourself, “OK, Ed, so what’s the answer?” I’ve been thinking about this for at least ten years. I haven’t got a clue.
Please join the discussion and share your thoughts in the comments section. We’ve got to think of something.
This Post Has 18 Comments
Comments are closed.
I think you’re on to a new
I think you’re on to a new marketing breakthrough: “Income generating energy retrofit!”
I think the answer is simply hiring lower wage employees to do the hard work, and have the experts supervise. Take home building for example, the architects and civil engineers are not driving nails, and I’m sure they couldnt do it near as well as the experts (who normally are from spanish speaking countries).
When a home down the street from mine was being built, I saw a team laying bricks, and one guy was throwing stacks, like 10 bricks at a time, to another guy 10 feet away…and it was the middle of an Atlanta summer. You think this is easier than insulating?
Of course everyone can’t have a crew under them, but in that case, home performance pros have to be diligent about doing the job 100%, and call out the ones who arent. Let’s face it, the barrier to entry to calling yourself a home professional isn’t that high, which is why we need places like this blog to continue to push for excellence.
HUMAN FACTOR :: When work is
HUMAN FACTOR :: When work is too hard, hot, cold, wet, or just plain-ole no fun, it usually means there’s high turn over, opportunity for fraud, sloppy-ish-nesh and a host of other challenges.
Want to stop the out right lairs from out right lying? Good Luck With That!!!
Create a better system! Currently, there is absolutely nothing to prevent new work from being installed crappy. We’re repairing yesterday’s new homes today. Unless we change the way we address new construction today, we’ll be performing (and lying about) the same tasks tomorrow. There is no answer to this question because there are no measures in place today that help prevent the kind of absolute CRAP that’s being “allowed” in new homes.
“Doc, it hurts when I do this!” and Doc says, “Don’t do that.”
As with most government
As with most government programs, the EnergyStar program started out with the greatest of intentions, then sunk like a brick in the sea when contractors were permitted to use a “free energy audit” as a means to get in the door. All this did was allow shady contractors to sell “whatever-is-in-the-back-of-their-truck” to unsuspecting customers. As I understand it, at the onset, this service was never meant be be utilized in that fashion, but instead as a separate fee-paid service. We allowed the fox to guard the henhouse, and are now wondering why this program has had such questionable results. Contractors will be contractors, and the same “can’t see it from my house” approach is still being used by far too many of the BP guys.
I will go on to say that it is not the guys in the trench that are allowing this to happen. There always has, and will always be, low men on the totem pole who will be tasked with the dirty end of the stick. Oversight and follow up are the real problems here as I see it. I also believe in order for programs such as this to succeed, there needs to be an independent third party to perform the initial testing and writing of the work scope, followed by that same contractor in the building after the work is finished for retesting. And if the expectations are not met during the after-eval, the final check shouldn’t be cut. For some reason, we do not appear to be smart enough to grasp this concept. Some of these clowns have taken all this technology, and because the average layperson doesn’t understand it, are taking advantage of the general public.
Lastly, why is it that once a house is “rated” EnergyStar…why can that set of prints be submitted to construct multiple houses that earn the same rating, with a rater never setting foot inside? And why are raters allow to be on the payroll of builders? Terrible, terrible conflicts of interest abound. That’s the best reason I can come up with.
Once the ARRA funds dry up
Once the ARRA funds dry up there will be hard-working, trained workers from the low-income weatherization program looking for jobs. Those are the guys I would hire if I were a BP contractor.
Hi Ed(and Allison)! Thanks
Hi Ed(and Allison)! Thanks for another great and thought provoking post.
A couple of points I’d like to address:
1. The idea that somehow third part oversight will stop shoddy workmanship. In no other residential construction arena do we expect some governmental, or worse a subcontractor for a quasi-governmental agency to actually create better quality construction. Not gonna happen. Every building requires a building permit and inspections, right? We’ve all seen good electrical work, and not-so-good electrical work and it all got inspected, right? The oversight only increases the cost and timeline for the homeowner. One of the biggest hurdles already in place is the bureaucracy attached to residential retrofits. If you have to pay someone (through incentives and rebates) to buy BP, then we’re not offering a competitive product.
2. “The number of top-quality retrofit building performance jobs that I have seen on the retrofit side is somewhere between darned few and pretty darned few. The rest ranged from flawed to downright miserable.” Yep. But I’d say that’s right in line with the percentage of top-quality construction in both new homes and major remodels. The modular home industry has, in my opinion, ruined the new construction market. I am generalizing, of course, and that is always dangerous, but the vast majority of new modulars going up are inferior when it comes to BP. Speed Kills. You can build it FAST, or you can build it with QUALIY, but you can’t have both. Same with BP. The margins are so small, and depend so much on Rebates, Incentives, and Red Tape to be profitable, that you have to get in and get out to earn a living. Take too long, even with trained ex-WAP installers @Amanda Evans (who require higher pay, mind you), and you’ll not be in business for long.
3. “Create a better system!” Um, we don’t need a better system. We have a better system – it’s called Market Driven Capitalism. What we need is to actually USE the system we have. How about eliminating existing fossil fuel subsidies, for one. If we reflect the true cost of energy, BP contractors will be busier than a one legged man in a but kicking contest.
So to me, like most things in this world, it is really all about the money. BP has to make financial sense – on it’s own merits. When the end result justifies the means, the crooks and crap-slingers will still be around, but the top-notch companies will do just fine – without some low-level bureaucrat looking over their shoulder.
Ed, I love your writing – please keep it up. It inspires me to engage. And I have to make one final comment about your “cost savings” example that pulls back the curtain on a much deeper societal problem – math and science education. Specifically our failure at it. Everyone, and I mean e-v-e-r-y-o-n-e who has had a basic education in this country should be able to recognize that you can’t save $1,300/year on an $800/year energy bill. It’s disgraceful. And in part it is to blame for the housing, real estate, and financial crisis’ that have lead to this re-depress-cession or whatever it is we’re in. When the vast majority of Americans can’t calculate simple interest, or realize that $800 – $1300 is a negative number, then we have a real problem.
And, I’m afraid “Houston…we have a problem.”
This has been an ongoing
This has been an ongoing struggle for years and I personally have been looking for answers to these same questions. What I have found to be some what helpfull was having a top notch certified or certifiable crew lead. Someone who cares, not only about the company he is working for and there resources but more importandly cares about the residence he is working on. This attitude can be passed onto his workers and make it known right from the beggining that only quality work will be accepted.
In the background I come from the crew lead was the most experienced and knowledgable person on the crew. The only thing that earned him or her was to do the bulk of the work. Today i think we should try and go in the other direction. The lead is there to supervise and to teach the crew on what they are doing, how to do it and what the goals of the job may be.He is also the QC for the crew and the job.He may want to come up with a way to incentivise his crew.Of course this means that the lead needs to be paid enough so he can share, this sharing can be lunck, breakfast a 10$ gift card anything to show HIS or HERS crew that he appreciates their hard work.
I understand this issue all to well but I do think the crew lead is a big part of the solution
Joe Ilacqua
I mostly emphatically agree
I mostly emphatically agree with Mark that building performance must be financially competitive on it’s own merits in order to be profitable, or even sustainable, in the long term. I think one of the keys to overcoming this issue is the education of the homeowner and home builder. When they understand that BP professionals are as valuable as architects (most of the time) and interior designers (all of the time) it will become commonplace to include us in the quiver of contractors. And when raters are able to provide their services with short payback periods they will receive referrals time after time.
Education and efficient process flows – those are the current goals of our company.
Mark, when I refereed to a
Mark, when I refereed to a better system I was referring to the sort of control that the HVAC industry could and should do to police themselves (along with other industries responsible for the need for the retrofit).
You say, “Every building requires a building permit and inspections, right?”. The answer is no, you’re not right. There are still several states in the US that have no minimum state mandated building code.
Better system? Yea, we need to take the one we have and police it. That alone would begin to create a “better mouse trap”.
In part, we shoot ourselves
In part, we shoot ourselves in the foot.
First, we don’t come back and test our work later to prove its worth. This needs to happen 6 months to 1 year later.
Second, we allow our clients to pick and choose items off the proposal as a menu. When they object to our proposal, we need to provide new solution. We won’t build a house with a partial blueprint. Why do we try to improve one that way?
Third, we fail to recognize there is a strong learning curve. It takes most people months to learn enough about what we do before we can do the audit. Then, we overwhelm them with our improvement report. It takes people willing to put in the time a while to comprehend what what we’re trying to do. My sister found a video to give my clients between the audit and report presentation.
Fourth, we forget we’re a team. For example, HVAC companies don’t usually want to do air sealing and insulation, so any solution that that doesn’t include part of the HVAC system is uninteresting to them. Rather than refer, the opportunity is dropped.
Finally, we don’t model the current situation and show the impact of various solutions. HERS modeling is horrible for doing this. I’m learning how to use Right-J to do this. It has a lot more value than selling HVAC systems.
Finally, our reports don’t reach our customers. I’ve seen really short ones that communicate nothing substantial to anyone to information overload. I’m getting my customers to help me figure out how to present to them.
I do know our blogs help! I know being a building consultant for life helps. I know videos help. My report formats have changed for the better. However, I’m not there yet!
The biggest thing I had to overcome is to realize I’m a trusted consultant coordinating team members and not just a home inspector.
When I “graduated”
When I “graduated” from my 4 day training and 3 tag along visits I knew very little about what improvements to recommend, let alone how to actually perform the work properly. After 2 years of trial and error, there is still quite a bit of trial with less error. If there had been additional training offered (required) that covered the how-to’s of various improvement work, I would have signed up immediately.
Good luck new BP grads!
So why hasn’t someone come up
So why hasn’t someone come up with a rigorous qualification program for Energy Pros? LEED has the commercial building area tied up with all sorts of qualifications and the U.S. GBC has built a nice little non-profit business out of that. Why can’t there be some stamp that energy raters get to show they truly are experts?
Wow! There are a lot of good
Wow! There are a lot of good comments here, and I couldn’t get in and respond to each one as they came in, so let me just make a few comments based on my experience. I don’t know what the ultimate answer is either, but we’ve hit on a lot of the problems here.
As Jason mentioned, new people in this industry, at least in the Southeast, where he and I are, don’t have much opportunity to go through any kind of apprenticeship. I went out and just jumped in, doing assessments, fixing houses, testing in, and testing out. It was hard because I ran into a lot of different materials and construction methods. I found that achieving the results I thought I should be able to deliver was a lot harder than I thought it’d be.
Turns out, houses are pretty complex creatures that don’t always respond the way we’d like. Good results are possible, and I got better after my first few projects. It takes understanding the fundamentals and having an eye for detail. I think the key is probably having highly trained, experienced, and motivated crew leaders, as Joe said above.
Sam, I don’t agree that ‘HERS
Sam, I don’t agree that ‘HERS modeling is horrible.’ Why do you say that? What aspect of it do you think Right-J does a better job with?
Chris, there is such a ‘stamp
Chris, there is such a ‘stamp’ for energy raters. Actually there are two: certified HERS rater and certified BPI Building Analyst. There are ancillary certifications as well (HESP, CHERS, Envelope Professional…). It’s definitely not easy for someone to figure out if they’re not familiar with the organizations and certifications that exist, nor to disentangle the fundamental certifications (BPI & HERS) from the green building cert’s.
Or am I misinterpreting your question?
Allison,
Allison,
I think that answered it. As you know, my website is focused on the homeowner. So let me rephrase my question: “What is the rating stamp that homeowners should ask their energy professional if they have, so the homeowner knows they are getting an expert in home energy who will do an expert job?”
This is wonderful . . . we’ve
This is wonderful . . . we’ve got a sincere and important discussion going here. Thanks for making it possible, Allison. Here are a few notes:
1) Sam: If HERS modeling and ratings are inaccurate or otherwise of poor quality the responsibility falls squarely on the HERS Provider. It is the Provider’s responsibility to check, QA, and certify the ratings. Some raters do excellent work despite having a Provider who fails to deliver the mentoring, support, and oversight that all Raters need and should have, but they are rare exceptions.
2) A lot of certifications are like medals on the breast of a general for some obscure South American country: they look good, but they don’t mean much.
3) Understanding good building performance means being dedicated to learning it. Turn off the freaking TV and study the articles on BuildingScience.com until you know what’s in them. Reread Krigger and the EEBA guide for your climate. Read Home Energy, join Home Energy Pros, subscribe to GreenEnergyAdvisor and other newsletters, ask questions, learn from the mistakes of others.
Isaac Newton transformed man’s understanding of the universe in the 17th century, and he tells us how he did it: “If I have seen further, it is by standing on the shoulders of giants.”
Sometimes we have to stand on the shoulders of shorter people,but then we are not Isaac Newton.
Getting a certification from BPI or as a HERS rater is like going from a tricycle to a little bike with training wheels. You’re not ready for the Tour de France.
If somebody said it was going to be easy it sure wasn’t me.
HERS Modeling. I can write a
HERS Modeling. I can write a whole blog post or three on what is disagreeable with doing HERS modeling.
To put it in perspective, I believe the model, when complete may be okay. I don’t know because I’m still working out why heat loads are about 10 kBtuh apart between a Manual J & HERS heat load. I’ll find out, now that I can model in both.
First, starting with a set of plans and site specific plans, it takes me 12 hours to model a house. If there are are any changes to the structure after that, it takes a lot of time to ensure all the pieces are accounted for. It takes time to make a model you can change without having to recalculate everything.
Right Draw allows me to create a rapid model of the house. I can take the summary information to include in the HERS model and I’m done. REM/Rate does not have a drawing tool that propagates changes through it when the model is changed. Doing this saves a lot of time and provides reliable results I can defend to my QAD.
Second, REM/Rate has an immense costly overhead associated with it. First, I have to take a costly course that gets me about 1/2 way to what I need to know to model something more than a simple building. Then, I need to pay somebody to qualify it for me–every time it changes. To do them, I have to either go to a conference, get provider specific training, or retake the test. Never mind that the CEUS I took to learn to do the model better have been discarded by REM/Rate because they didn’t make the money on my training.
Third, from a practical matter, I would not do a HERS model on an existing house unless somebody wanted an energy mortgage. That whole process is flawed too because it what my customer thought they were getting through the marketing is vastly different than what they really get. Once I’m done with a model, I can’t really use it to help make decision. Sure, I can propose changes and provide dollar amounts. But there is nothing rapid about and there is no useful reporting of any sensitivity analysis.
Think about the difference between the data I have to include in either model. Most of it is identical. HERS keeps track of specific appliance energy data. So what? Once I pick it, I’m not changing it–thankfully!
I will do a Right-Draw Manual J block load on every house I do. Why? I can show the current load and changes when I do air sealing and insulation. I can show the impact on the HVAC equipment. I can even do several model of the ductwork! The HERS model doesn’t care whether I actually make the room air comfortable. However, Right-D does! Pictures and customer friendly documents are available with a push of my print button. None of this is available with a HERS model.
To make matters worse. Once I model a house, I can’t print anything until my QAD says I can. In the real world, I change the house as improvements mature. What I model in the beginning is not what I finish with. Because I have to pay every time I want to print something, I’ve given up trying to use REM/Rate to do anything meaningful for my client until we’re done. What good is that?
At the end of the project, I’m proud of my HERS model. Unfortunately it’s a useless tool during the improvement process. It’s great for modeling the beginning and the end, but to be avoided while doing the work!
Wisdom is knowledge applied.
Wisdom is knowledge applied. Hopefully when the DOE roles out their new Weatherization Training program and all workers are required to be credentialed to perform Weatherization on any Government contract the field of knowledgeable weatherization workers will vastly expand.