What Is the Best Way to Deal with Crawl Space Air?
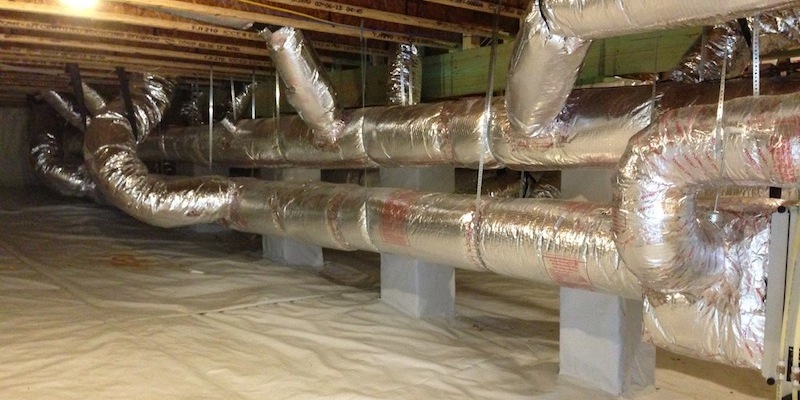
If you have a home with a crawl space—or are building or buying one—you have several options on what to do with that particular foundation type. Most crawl spaces are vented to the outdoors, but over the past decade, encapsulating the crawl space (as shown below) has gained favor among builders of green and energy efficient homes. It’s often seen as the best way to eliminate the moisture problems that often result from vented crawl spaces. But what do you do about the air down there?
Before we address that question, however, let me point out that encapsulated crawl spaces are great for humid climates, like the Southeastern US. In a dry climate, it may or not be worth the cost to encapsulate. So, as always, do what’s most suitable for your climate.
Basically, your options are to do one of the following:
- The tried and false method of venting the crawl space to the outdoors
- Putting a little bit of supply air from the HVAC system into the crawl space
- Using an exhaust fan to move air from the crawl space to outside
- Installing a dehumidifier
Let’s take a look at each of these methods.
1. Vent the crawl space to the outside
Do this in a humid climate, and you’re asking for trouble. The outside air that you bring into the crawl actually has more moisture in it than the crawl space air you’re venting to the outside much of the time. Although the psychrometric chart shows mathematically why it doesn’t work, a look into just about any vented crawl space in the Southeastern US proves that venting to the outside is often a disaster.
The photo above is from a house that was only a year or two old. Although the home builder had installed closed cell spray foam insulation in all the above-grade walls and the attic, he left the crawl space vented to the outside. The result was mold growing on the HVAC system.
Let’s just say this is your worst option unless you’re in a dry climate and quickly move on to the better choices.
Conclusion: This is your worst option in humid climates. It’s probably also worst for most climates if the HVAC systems and ductwork are located in the crawl space.
2. Supply air from the HVAC system
If you encapsulate the crawl space, adding a little bit of air from the HVAC system is probably the most common method used. If there’s already a duct system down there, it’s easy and inexpensive to do. The air from the system helps to dry out the crawl space air.
But it also puts the crawl space under a slight positive pressure and the house under a slight negative pressure. Is that a problem? Not according to Advanced Energy‘s Closed Crawl Spaces guide:
In Advanced Energy field tests, the small crawl space airflow causes a negligible pressure effect that is far exceeded by the effects of duct leakage, stack pressure or wind-induced pressures in the building.
How much supply air do you need to add to the crawl space? Advanced Energy recommends 1 cubic foot per minute (cfm) for each 30 square feet of crawl space floor area. The International Residential Code (IRC) recommends 1 cfm per 50 square feet:
Conditioned air supply sized to deliver at a rate equal to 1 cubic foot per minute (0.47 L/s) for each 50 square feet (4.7 m2) of under-floor area, including a return air pathway to the common area (such as a duct or transfer grille), and perimeter walls insulated
If you go this route, it may work well in the summer if the air conditioner is sized properly. If the system runs long enough, it can provide enough dry air to the crawl space to keep the relative humidity below 70%, where you want it.
In the swing seasons, however, and in homes with oversized air conditioners, this method may not work well. Another thing about this method that I’m not crazy about is that you’re conditioning the crawl space based on the conditions in the finished space above. The crawl space has its own conditions, though, and may or may not respond well to controls in another place.
Conclusion: Although it’s the most common method of treating the air in encapsulated crawl spaces, it may or may not work well.
3. Exhaust air to the outside
First, note that I’m not talking about the crazy idea to put large fans in the crawl space to exchange large quantities of air between the outdoors and the crawl. (Yes, companies really do promote this, and it’s a quick way to rot the wood in your crawl space.) I’m talking about a small exhaust fan, as described in the IRC. Here’s the language from the code:
Continuously operated mechanical exhaust ventilation at a rate equal to 1 cubic foot per minute (0.47 L/s) for each 50 square feet (4.7m2) of crawlspace floor area, including an air pathway to the common area (such as a duct or transfer grille), and perimeter walls insulated
So a 2000 square foot crawl space would need a 40 cfm exhaust fan. It’s pulling just a little bit of air from the crawl space. The problem is that you don’t really know where the makeup air for the crawl space is coming from. Yes, the code specifies a pathway for air to move into the crawl space from the house, but air doesn’t always follow those arrows in the diagrams. If the band joist isn’t sealed well, for example, it may pull a lot of the air from outdoors, which isn’t really what you want.
Conclusion: It could work but is probably less reliable than supply air from the HVAC system.
4. Install a dehumidifier
In this method, you use a standalone dehumidifier for the crawl space. (Again, we’re talking about encapsulated crawl spaces only; although some people try, you can’t dehumidify the whole outdoors.) It’s controlled by the conditions in the crawl space, not the house above, so this method will do the best job of keeping the crawl space dry.
Brad Brinke of The Crawlspace Company in Virginia Beach responded to my question about this topic on our Facebook page: “We have a very good track record with the dehumidifier here in Virginia. We install a humidistat and fan system to help the dehumidifier operate efficiently. We tried using supply air from the home and it did not work.” (See the full discussion here.)
If you want dry air in your crawl space, a dehumidifier is the way to go. Yes, they do have drawbacks. You have to buy additional equipment. They require maintenance. If the drain fails, you may have a bulk water problem in the crawl space.
If it’s a small crawl space, a standard dehumidifier that you can buy for $200 to $300 may be sufficient. For medium to large crawl spaces, however, it’s best to go with a more robust model, like the ones made by Therma-Stor. Their Santa Fe line is made for basements and crawl spaces. The photo above shows an older Santa Fe model made just for encapsulated crawl spaces.
Conclusion: Although more expensive, installing a dehumidifier is the best method for treating the air in an encapsulated crawl space.
Should you connect the crawl space to the house with a transfer grille?
Both of the quotes from the building code that I mentioned above include the following language:
…including a return air pathway to the common area (such as a duct or transfer grille)
What they’re saying is that if you pressurize the crawl space with supply air or depressurize it with an exhaust fan, they want the crawl space to be able to communicate with the house above to relieve the pressure. The easiest way to accomplish this is with a transfer grille right in the floor, as you see below.
Advanced Energy isn’t a fan of this method, instead recommending that the entire floor be air sealed to isolate the crawl space from the house. There are some good reasons for this. If, for example, the intent of the opening is for house air to move downward (as in the case of the exhaust fan), the stack effect may win out if the crawl space isn’t perfectly sealed to the outside.
Another potential problem is pollutants in the crawl space air migrating into the house. These could be soil gases such as radon or fumes from paints, pesticides, or fuel stored in the crawl space. Also, if the crawl space access door is left open, it may not be discovered for some time. Meanwhile, the house is directly connected to the outside through that transfer grille.
Is it ever OK to install a transfer grille? Sure. In the house where I took the photo above, there’s no access to the crawl space from outside, and the owner doesn’t store hazardous chemicals down there (unless you consider wine hazardous).
The bottom line
The best way to deal with the air in a crawl space is to encapsulate it and install a dehumidifier. Adding supply air from the HVAC system is tricky and may let the crawl space humidity go too high in spring and fall.
Now, go out there and turn those nasty crawl spaces into clean, dry mini-basements!
Allison A. Bailes III, PhD is a speaker, writer, building science consultant, and the founder of Energy Vanguard in Decatur, Georgia. He has a doctorate in physics and writes the Energy Vanguard Blog. He also has a book on building science coming out in the fall of 2022. You can follow him on Twitter at @EnergyVanguard.
Related Articles
3 Reasons Your Crawl Space Has High Humidity & Grows Stuff
The Medical Doctor, the HVAC Guy, & the Crawl Space
Beautiful Duct System in a Beautiful Crawl Space! Was I Dreaming?
External Resources
This Post Has 53 Comments
Comments are closed.
There are many terrific
There are many terrific articles, including yours, on encapsulating the crawl.. However there is an alternative, that is moving the pressure and thermal boundaries to the bottom of the floor joist, air sealing and leaving the venting (or increasing it). Of course with proper duct sealing/insulating if they exist there.. Have you spoken to this solution..?
Thanks..
Good article Allison.&
Good article Allison.
Reed, the only problem that we have with your approach down here in the “lowcounty” of South Carolina is that termite companies want to inspect all of the wood. They are dropping termite bonds left and right these days for improperly done crawlspaces where insulators are covering the stem walls all the way up to the subfloor, or even spray foaming the subfloor and covering down the band board. This promotes a great air seal, but hides a real problem. “Capping” the joists from below would work well, but it would hide a lot of the inspection ability and can create other issues with termite bonding of the home.
Thanks,
Jamie Kaye
Elm Energy Group
The cost of option #2, supply
The cost of option #2, supply air from the HVAC system, looks to be nearly zero to me (what is the cost of one hole?). The capital cost and the operating cost of option #3, dehumidifier, are significant. I submit that by doing *both*, you incur the dehumidifier operating cost less in the cooling season, and more in the mild spring and fall seasons, for lower overall cost than option #3 alone.
Allison,
Allison,
Having used all of the methods you enumerate, I agree 100% on your conclusions and recommendations. I suspect that future building scientists will scoff at our attempt to treat a crawl space like a regular room in the house. It is not.
I have seen the energy savings claims of 18% by “conditioning” the crawl space. I remain skeptical. I suspect that there are some missing data in the calculations. Do you have any opinions on these claims?
#1 After 30 years of moisture
#1 After 30 years of moisture/mold problem solving and 12 Summer Camps I understand dewpoint and crawlspace environments. But why did I (embarrassingly today) encapsulate my small crawlspace in 1967? To get rid of the damn chipmunks. When I encapsulated there was a musty smell and a light white dusting on the floor joists. Six months after encapsulation the space was bone dry with no musty smell. The crawlspace dewpoint was about 2°F higher than the room above. My crawlspace had no supply, return or exhaust air & no dehumidifier. Near-dewpoint equilibrium was apparently due to moisture diffusion though the hardwood floor and perhaps a little supply air duct leakage.
#2 The eastern part of Canada within 300 miles of the great lakes (and the U.S. below) has summertime dewpoint temperatures of 68°F +/- 3°F (not much different from Atlanta). I recall a Canadian code or design guide which appropriately said to close crawlspace vents in the summer unless you wanted to humidify the crawlspace.
#3 Providing cold supply air to the crawlspace will result in a crawlspace RH higher than that in the home. In some homes this could be near the mold proliferation RH!
#4 Perhaps it is time to research and test basic encapsulated crawlspaces (a) without supply/return/exhaust and (b) with only a transfer grille.
#5 If a dehumidifier is used it should be distant from bedrooms above because light sleepers often complain about the change in sound level as the dehumidifier cycles.
Dr. Bailes, you need to
Dr. Bailes, you need to escape your southern parochialism and visit places where hockey is played by real hockey players. Transfer grilles work just fine in such locations.
The point needs to be made that moisture has to be removed from the crawlspace. That can only be done with dilution with drier air or with a dehumidifier. With the former approach some type of air change is needed with the conditioned part of the house where dehumidification is occurring either via the operation of an air conditioned or via dilution ventilation with outside air when the outside air is drier than the inside air.
If your crawlspace is “clean” connecting it to the rest of the house is ok. If it is not clean then you should not do so. In trashed crawlspaces sucking on them with a continuous exhaust fan works well. In clean crawlspaces up north transfer grilles work just fine. In between and in the south a very small amount of return air works fine with a transfer grille as does a small amount of supply air with a separate fan that does not blow cold air from the HVAC system (that Mr. Gatley guy knows a few things about physics) but blows house air that is warmer and drier.
Allison,
Allison,
Hope you (or Joe L. if he is “listening”) can help answer a crawlspace question for me out in the cold dry region of Santa Fe, NM. Slabs are most common out here, but I’m helping to spec a home to be built at Santa Fe Community College that will be transferred to a home site. Because the floor system will be open-webbed trusses, getting insulation against the warm floor (and keeping it there) is problematic. The stem walls will be ICFs with an R-22 value.
I have suggested we have an unvented crawlspace with a sealed membrane on the dirt that is also sealed to the ICF stem walls to keep radon out of the envelope. The main reason for the unvented space is not to keep moisture out but to negate the need for insulation in the floor assembly. We are at 6000 HDD so cold dry air in the winter is more of an issue than moisture.
There will be plumbing runs and ductwork in the crawl space but no mechanical equipment. Access to the space will be a trap door from the home’s interior. The band joist will be sprayed foam.
Am I on the right track here?
Another great article,
Another great article, Allison. But I see a dehumidifier as a method-of-last-resort. After spending an extraordinary amount of effort trying to reduce consumption, I just can’t see the logic of that if there’s another method that can be effective.
This is one of those building science topics where smart people may disagree. Airing it out in forums like this is a great way to move toward best practice.
For the pros following this thread, here’s a link to a thread Allison started last year in the LinkedIn RESNET BPI group on HERS interpretation of diagnostic testing (ducts & envelope) in homes with closed crawls: http://linkd.in/10hYIDX (a must-read for HERS raters)
And here’s a more recent thread on ACH50 calculations and crawl space drying (http://linkd.in/103mcut). Lstiburek put me in my place for suggesting that Advanced Energy developed the concept of closing a crawlspace (but HE was wrong about NC BBQ).
Barry
Barry wrote:
> I have seen the energy savings claims of 18% by “conditioning” the crawl space. I remain skeptical. I suspect that there are some missing data in the calculations.
You should be skeptical. Energy savings claims are very much dependent on climate and circumstances, in particular, whether ducts are in the crawl. Also, there’s a trade-off between insulated walls vs. floor in colder climates, which is a nice segue to Kim’s situation. But if energy savings and first-cost is paramount, best to eliminate the crawl and either build a finished basement or slab-on-grade.
@Kim, you’ll also need to mechanical fasten and seal the membrane to the piers. In a cold climate and no mechanicals in the crawl, the floors may get a bit cool (due to influence of cooler ground). I have a project in eastern Long Island with radiant floors over a closed crawl, with AC ducts in the crawl. If the thermal envelope aligns with foundation wall rather than floor, the radiant system will lose too much heat to the crawl, increasing heating costs. They decided to insulate both walls and floor, but I advised some air exchange between crawl and house. Since the floor isn’t a pressure boundary, I suggested batts rather than foam (imperfect, but adequately reduces heat loss to the crawl). I’m also interested in what others have to say about this.
I think you have a good
I think you have a good approach. I would have a small 4 inch supply duct supply air to the crawlspace and have two transfer grilles connecting the crawlspace to the house. Our website has more information on this.
That Mr. Butler fellow also knows what he is talking about. Not sure about that turpentine stuff he puts on his pork though…..
Allison,
Allison,
Your customarily thoughtful and informative observations are always welcome.
I try to precede all my interweb comments with something positive. It has a lulling effect :-).
All seriousness aside, I encapsulated my CS here in semi-arid Carson City several years ago, and because the builder of our ’02 home had conveniently (and mysteriously, according to the HVAC contractor) specified a 4″ duct from the attic distribution system, a bit of ventilation air was easy to provide. I chose to add a return grill in the closet CS access hatch, after confirming that, with the hatch in place, no air (undetectable with wet finger 🙂 came down the 4″ supply.
Exterior vents were foam sealed and additional insulation was added to a few wall areas in need. The vapor barrier is probably not as continuous as it needs to be, but regular visits to the netherworld have revealed no condensation issues. Annual radon tests (free through the Agricultural Extension Office) have the been just below the threshold but at age 69, I will doubtless die from something beside lung cancer anyway.
Benefits include bare-foot comfortable hardwood floors, no more mice wintering over through the hole in the vent left by the cable guy (three hours clean-up with a shop vac), no more dirt in the CS blown in by our Washoe Zephyers and no annual fussing with vent dampers. Energy use changes have been undetectable on a purely anecdotal basis.
Totally DIY but without the supply duct, would have been a big deal. With the supply duct in place, I’d estimate a 4 hour job by a pro.
No actual engineering was involved in this project and any unintended negative consequences have been below the threshold of detection.
Best wishes.
“Let he that hath AC
“Let he that hath AC supply in his crawlspace cast the first supply duct.” 1 Fleshalonians 9:16
One thing I’ve noticed that is as consistent as the supply of fine Le Pergolet Tort is that of skin wettedness >25% for those exceptional followers that enjoy subterraneous twittifications at Summer Camp.
It may be that developing a strategy to process Allison’s profuse subterrestrial sweating may be one of the most important developments of 2013-14 for BSC.
Regardless, in our dry CA climate we have had very good results with installing a sealed ground source vapor barrier directly on the soil, sealed to the foundation walls, then sealing up all perimeter venting, and providing exhaust ventilation at code minimum .02 CFM/SF through a continuous duty crawlspace fan like this one: http://www.rewci.com/underaire-crawl-space-ventilator-one-fan.html
Reed D.:
Reed D.: Yes, I’ve heard of people doing that. I met a guy from New Jersey (or was it Delaware?) who’s been doing it and is working on marketing a whole system to do it that way. One issue you have to be careful with there is what happens when there’s a plumbing leak above that pressure boundary? If you use foamboard to at the bottom of the joists, you’ve got to have a drain in it somewhere, or maybe many somewheres.
Jamie K.: Good point. I know someone in Hilton Head who promotes this idea, too, but I don’t know if he’s still doing it. Maybe he’ll comment here and let us know.
M. Johnson: Yes, that hybrid approach would get you the best of both worlds. Then the DH would be down there when you need it during cool, rainy periods in summer, too (like we had most of this summer in Atlanta).
Barry W.: The 18% savings number you cite came from Advanced Energy’s Princeville study, which you can read about in this report (pdf).
Matthew R.: I don’t quite understand your system. How will a sub-poly ventilation system affect the air above the poly?
Don G.:
Don G.: “I understand dewpoint and crawlspace environments.” That’s a bit of an understatement for someone who wrote what may be the best book on psychrometrics. Your 5 points contain a lot of great points. About your home, though, I think maybe you got lucky. Not all homes get such a happy result without doing something with the air.
Dennis D.: Thanks!
Joseph L.: Indeed I do…escape my Southern parochialism, that is. In fact, that photo of the transfer grille was taken in New England. Perhaps you’ve seen it? Perhaps I should have just let you write the article because you said more clearly in two paragraphs what I tried to say in 30.
Kim S.: That Lstiburek fellow knows what he’s talking most of the time, although it did take him 58 years to learn how to pronounce his own name. Here’s a list of
conditioned crawl space articles on the Building Science Corp. website.
David B.: Thanks! Here are the clickable links to those other discussions:
Diagnostic testing (ducts & envelope) in homes with closed crawls (a must-read for HERS raters)
ACH50 calculations and crawl space drying
Steve W.:
Steve W.: “…undetectable with wet finger” Ah, it looks like you’re referencing Dr. Lstiburek’s famous “Look, lick, and squirt” test method. Be careful — I hear he’s going to start enforcing his patents.
Michael M.: And don’t forget this one: “Let he that hath never missed the last shuttle throw out the last ersatz apothegm.” 9 Apocryphals 3:12,ħ*ψ(t). As for the rest, I’ll just leave you with this:
…the clickable link for that crawlspace fan you mentioned.
>> "
>> “undetectable with wet finger”…”Dr. Lstiburek’s famous ‘Look, lick, and squirt’ test method”…”Be careful — he’s going to start enforcing his patents.”
Sounds to me like everyone here is guaranteed a wet willy, sooner or later… 😛
Allison,
Allison,
At my company we deal with many problems related to both sealed and vented crawlspaces in the United State and Canada. If done right a new home can be designed for a closed environment and can be very effective. But a retrofit can bring an entirely different set of problems.
Our systems try to take the advantages of both a vented space and a closed space and put them together.
Please feel free to contact me if I can help you with anything.
Steve Michael
ATMOX INC.
atmox.com
@Tom, not a good idea with an
@Tom, not a good idea with an ERV. A goodly percentage of the moisture from incoming airstream would be transferred to the exhaust air via the enthalpy media.
I sure would like to hear an
I sure would like to hear an explanation of what conditions are expected in say, Tom’s scenario. Humidity problems become awfully clear *after* someone explains them using the right principles of physics.
I have a general idea of dewpoints to expect from indoors air, and also from outdoors air in my region (hot-humid South). The dewpoint of ERV exhaust air is of interest to me, as well as the conditions we must avoid in crawl spaces. Are ERVs any better than 40% effective in transferring humidity from one air stream to another? I would love it if someone would explain using some details.
My first guess which is probably wrong: indoor air 60F dew point, outdoor air 70F, ERV exhaust maybe 64? Is that such a difference that blowing ERV exhaust into the crawl space would lead to harm?
Yo DAndre,
Yo DAndre,
“…and the complete air barrier sounds like the best solution over any kind of grille to the conditioned space.”
With a “complete air barrier in place”, how would you get any circulation in the CS? What am I missing?
As noted in my earlier post, I’m pushing (pulling? 🙂 air down a 4″ supply and back up through a grill in the access hatch. No inappropriate storage in the CS and regular Radon checks are nominal. I call it my “crawlment”.
Again, non-existant Northern Nevada humidity.
YMMV
Best wishes.
Allison,
Allison,
Could you elaborate on what you are warning against here:
“First, note that I’m not talking about the crazy idea to put large fans in the crawl space to exchange large quantities of air between the outdoors and the crawl. (Yes, companies really do promote this, and it’s a quick way to rot the wood in your crawl space.) ”
Are you talking about fans in the stem wall that end up bringing humid air into the CS?
Thanks for all the insights.
@Mark, unfortunately, ERV
@Mark, unfortunately, ERV manufacturers only publish total efficiency at summer conditions (sensible + latent), so there’s no way to know how much moisture is rejected in the opposing airstream.
Indoor dewpoint generally should not exceed mid-50’s, at least not for any length of time. But outdoor dew points are often in the mid-70’s in much of the country. So mid-60’s might be a fair assumption for exhaust stream, with AC picking up the excess moisture introduced in the fresh air stream.
The crawl is likely to be significantly cooler than the outside, so dumping air with 64F dewpoint into a crawl that’s 75F would create a relative humidity of 70%, which is high enough to grow mold. Also, if you use ERV to exhaust a bathroom during a shower, 60% of the interior moisture (using your example) would be pushed into the crawl. Shower steam may have a dew point in the 80F range!
Check out dew point calculator.
David, thanks for your
David, thanks for your response. I am searching for dewpoint data in my locale (27278) to see if I can further sort this out. I get Allison’s thinking, but I sure would like to find a solution other than a dehumidifier, with its energy load and other attendant hassles.
@Tom: I have done some
@Tom: I have done some research using Weather Underground website. For example using airport “KIGX” in Chapel Hill, you can see July dew point averaged 70F.
@David: Something has been nagging at me about indoor dew point. You said it “should be mid-50’s” which corresponds to 45% RH at 78F temperature. I believe lots of homes in Houston run at 78F but have higher RH. When the subject is preventing crawl space hazards, I submit one should not assume anything better than mediocre conditions. It will be the more pathological 20% or so of homes which show problems. So the question I see is what would be the indoor dew point in the worser part of the market, not the ones behaving well. I wish I knew all the stuff you know, and thanks for listening.
@Tom, you can look at
@Tom, you can look at historical dew point graphs at wunderground.com. Monthly view is best for that, although you can also set a custom range.
Last July, the peak dew point at nearest station was 76F: http://bit.ly/16IVuqq
In your previous post, I thought you were trying to further recover the lost sensible heat from the ERV. There’s obviously no way that’s not going to exacerbate the humidity issue.
If it were my home and the crawl was clean, I would do a “pretty good job” sealing the floor and install a very small transfer fan between house and crawl. I would control the fan with a humidistat set to about 50% in winter and about 65% in mid-summer (depending on peak crawl temperature and peak house RH). A dehumidifier may be necessary to dry out the crawl in the beginning, after construction wetting.
@Mark, I didn’t see your post
@Mark, I didn’t see your post when I posted my last comment. We were on the same page (literally).
Regarding dew point, I agree that many homes have higher humidity than desirable, but for purposes of my point (bad idea to dump ERV exhaust into closed crawl), that’s even worse.
In general, if stat is set to 78F or higher 24/7, there’s no problem with dew points into the low 60’s… you just want to keep the RH below 60%), but that’s going to make it more difficult to manage crawl moisture.
Anyone who recommends solutions for these types of problems needs to be proficient in psychrometrics. In fact, that goes for anyone involved in building science and especially mechanical design.
@Tom, I didn’t want to drag
@Tom, I didn’t want to drag this thread off-topic, but that’s more or less what I’ve specified on several projects with crawls… e.g., lower rate air transfer to crawl combined with supply-only ventilation (CFIS is BSC’s term for supply-only).
Although the CFM transferred to the crawl is likely to be lower than whole-house ventilation target, this strategy kills two birds with one stone. It takes advantage of the efficient latent capacity of the AC to address crawl moisture while making use of the positive pressure created by supply-only ventilation. However, I typically don’t use an air cycler since the crawl xfer fan accomplishes the same effect. The key is to adjust the butterfly damper in the fresh air duct so the crawl fan will pull its makeup air through the fresh air filter rather than leaks in the envelope. The extra moisture introduced between cycles will be dealt with when there’s a cooling call. Depending on the location and other factors, this isn’t usually a problem for an otherwise tight home with right sized equipment.
@Tom, I have read differently
@Tom, I have read differently. If this site will let me post a link, here is a 1999 paper by Lstiburek and Rudd, titled “Design Methodology and Economic Evaluation of Central-Fan-Integrated Supply”:
http://tinyurl.com/pjew8ou http://www.buildingscience.com/documents/reports/rr-9908-design-methodology-and-economic-evaluation-of-central-fan-integrated-supply-ventilation-systems
There is a marvelous table on page 2, predicting flow rates for various size ducts at various pressures (External Static Pressure in your AC plenum). You really want to measure your own ESP as it is very installation dependent, but that 6-inch duct woule flow approximately 100 cfm for a typical ESP.
The model used 25 ft of duct, vs. your 20 ft, so your airflow should model a bit higher. And the model used flex duct, so your hard pipe always flows more. But I can think of no reason other than religion, not to use flex for this project. Hope this helps.
@Tom, as you can see from the
@Tom, as you can see from the table on pg2 on the BSC doc Mark cited, CFM depends heavily on static at the top of the OA duct. And that depends heavily on return side static.
For example, I typically design to less than 0.1″ return side, so I’m not going to get close to 100 CFM through a 6″ OA duct.
I’m confused… why do you need an ERV if you have outside air tied to return plenum? Said differently, why do you need OA duct if you have an ERV?
As for your transfer fan CFM, North Carolina code requires 1 CFM per 50 ft2 of crawl area (not volume), but it’s impossible to say if that’s enough to satisfy peak humidity loads for a given crawl. As noted in my previous comment, I prefer to switch the fan based on RH demand, in which case there’s little downside to going a bit larger (than code) on the airflow. The code is a very very blunt instrument. In particular, running xfer fan 24/7 at an arbitrary flow rate will unnecessarily increase space conditioning loads.
Mark, thanks for your input.
Mark, thanks for your input. I will read that article.
David, thanks for your responses, too. The ERV is to provide fresh air but keep pressures balanced in the home. The remaining task is to dehumidify a closed crawl. I would prefer an option that does not require the energy and maintenance required for a dehumidifier. One way to do it to transfer conditioned air to the crawl, as you proposed. To end up slightly on the positive pressure side of balanced in the home, the additional supply and exhaust strategies have to be tuned (without going crazy overboard). I am looking for help in how to do that.
An RH-based controller on the exhaust/transfer fan makes good sense to me. So, how to do the supply -?
@Tom, in moderate climates
@Tom, in moderate climates like yours, I typically specify OA duct (CFIS) for fresh air. A recovery ventilator is overkill… the higher first-cost is really hard to justify. But that’s a converstion for another day.
But in your scenario, if you install ERV + crawl transfer fan, and you want to maintain positive pressure, you have two choices: Re-balance the house by reducing ERV exhaust flow (e.g., to offset the transfer fan). That could be accomplished with a motorized adjustable damper, energized by the humidistat. However, that would absolutely kill the recovery efficiency of the ERV.
The better option would be to do what you’re suggesting… install an OA vent on the HVAC. This requires an ECM blower and coordination between blower and crawl fan. However, in that case you don’t need the ERV. A simple control would allow the CFIS system to kill two birds with one stone.
@M.Johnson, ‘requires’ may be
@M.Johnson, ‘requires’ may be the wrong word, but a PSC blower will eat your lunch if you run it 24/7 or a substantial period bewteen heating and cooling cycles, as would be the case if you’re using an OA duct for ventilation. ECM (VS) blowers are not only much more efficient than PSC when operated at low static, but most have a fan-only mode, typically 50% of low stage fan on 2-stage systems. Of course, this also impacts sizing of OA duct.
The problem with CFIS is that it has to be designed, and we all know what that means. Studies have shown that these systems (also referred to as ‘supply only’) often fail to deliver the desired amount of fresh air. Likewise with recovery ventilators. Likewise with heating and cooling systems in general. Yet I digress…
Great write up, and perhaps I
Great write up, and perhaps I am missing something, but in this blog, “3 Reasons Your Crawl Space has High Humidity Grows Stuff
http://energyvanguard.com/blog-building-science-HERS-BPI/bid/38021/3-Reasons-Your-Crawl-Space-Has-High-Humidity-Grows-Stuff
You say that the dehumidifier are not a solution at all which I tend to agree with as it attacks symptoms not causes.
Thanks for the clarification on this.
Todd
Hi Allison and others,&
Hi Allison and others,
I have a crawlspace in Hayden Lake Idaho that I love some comments on. It is new construction lakefront house and we just finished drywall. I realized recently that i did not add vents to the crawl space during the siding process and now have significant moisture and mold on many of the 2×6 studs and the plywood on the lake side of the crawlspace is dripping wet. We haven’t had rain or moisture in ages so i’m assuming this is humidity from the lake coming in through the left open crawl space door. The lot is very steep so the crawl space is as tall as 6 ft on the lake side and 2 ft on the uphill side. I currently have fiberglass insulation in the joists above. The concrete foundation wall extends out of the ground 2 ft in most cases before transitioning to 2×6 studs.
how do i dry this area out? fans and dehumidifier after installing a vapor barrier on the ground? Should I add vents at this point?
Would you recommend encapsulation? plus dehumidifer up here?
I have just been quoted $11
I have just been quoted $11,200 to encapsulate my 1400 (that actually being the size of my house) crawlspace in Eugene, Oregon. It is currently vented and my problems have been standing water, rodent and cat entry with resulting nastiness, fallen insulation from moisture as well as animal damage (this is a very wet, rainy valley we live in.) This includes a strong vapor barrier mounted on floor and wall, blocking vents, a humidifier and excellently-rated sump pump, plus debris removal. No replacement insulation. Is this a good price?
I also have a more conservative bid to use gravel with sump pump, leave the venting , redirect water to the sump pump (which the above bid would also do) and replace the vapor barrier that is there with similar, cheaper material for $4,900.
Are both bids in line for what they propose, and is encapsulating far superior if I plan to live in the house for about 5 more years? I have been advised by my heat/air company I need to do something, that I am getting poor heat/air efficiency and I know it is a problem down there, I’ve seen pictures and there are some odors in my home.
i need to dry my vented crawl
i need to dry my vented crawl space in NC. How will this work? Place 40 ft drainage pipe with holes across center floor of dirt crawl space , attach this to duct line to attic space with an inline 90 cfm silent exhaust fan at the other end of attic, run a 6 in. duct through corner of closet from attic back to crawl to circulate dry attic air and close the foundation vents. Any comments are welcome.
@Todd, that’s an interesting
@Todd, that’s an interesting idea. Assuming the attic is vented, the attic air is by definition no drier than outside air (e.g., roughly the same dew point). It has a lower RH simply because it’s been heated by the roof.
Drawing warm air from attic into crawl would likewise raise the RH in the crawl You could do the same with a space heater, but you’re using the roof as a solar collector as it were.
This should help, but whether it’s enough to actually “dry” your crawl depends on how wet it is, and the sources for that moisture.
The best strategy is always source control. If the source is roof or site drainage, your strategy will likely fail. But the the source is mostly due to venting your crawl with outside air, then using attic air to raise the temperature may work.
Built new home 4 yrs. ago no
Built new home 4 yrs. ago no problem for 2 yrs. then duck sweating started. It’s vented per state rules has 6 mil visqueen over lapped and taped crawl space on a slope. Inspector says not my fault home owner says it is ! only sweat’s in hot summer of course. Will duck fans solve problem ? Need answers fast to avoid law suit.
Bud: No,
Bud: No, duct fans will not solve your problem. You’ve got two choices: (i) You can either reduce the humidity in your crawl space by removing the sources and then doing something about the air in the crawl space. (ii) Or you can make sure your ducts are sealed and insulated really well, with the outer jacket sealed as well.
You didn’t say where your home is, but I’m assuming you’re in a humid climate. If you’re in not in a humid climate, you can still have this type of problem but it’s less likely and probably won’t last as long.
@Bud, I’ll be a bit more
@Bud, I’ll be a bit more direct that Allison… ANY exposed metal on the supply side (plenum, fittings, ducts, and boots) WILL sweat in vented crawls anywhere other than the desert southwest.
Moreover, if insulation jacket is not completely sealed at every end and seam, moist air will make its way to the cold ducts and condense, and water will collect inside the insulation jacket, making a real mess.
This is basic stuff your mechanical contractor should know. The International Mechanical Code requires ducts to be protected from condensation (Section 603.12), which means supply side components must be fully insulated and all seams in outer jacket sealed (604.11).
I have a slightly different
I have a slightly different issue….We had our basement encapsulated in the fall and made it through winter no issues. Now since Spring we are smelling this bad smell. It is making me sick I believe. We live in GA. I have tried air cleaner, odor remover etc. with no luck. Basement is dry and at 40 percent humidity so dry. I am hoping the smell eventually dissipates but so far it is strong and we smell it in the living space. A subtle yet bad smell. What to do??? I spent a lot on the encap. Didn’t anticipate this bad chemical-cat urine-odd smell. We have a sante fe dehu running at about 40-45% humidity. In the crawl is a gas water heater and our HVAC. Ducts have been cleaned and HVAC serviced. Still the cat urine type odor is strong even in living space. Some folks told me it is the vapor barrier out gassing. I don’t know what to do but need help! Thanks Jeff
Jeff,
Jeff,
That I am afraid is a common sealed problem. It is most likely the bacteria under the liner. You are welcome to contact me to discuss it.
Steve
704-248-2858
@Jeff, was spray foam
@Jeff, was spray foam insulation used to insulate your walls or rim bands? Cat urine odor can occur if foam is improperly mixed or cured.
Also, unrelated to the odor problem, is your gas water heater sealed combustion (typically two PVC pipes)? It’s a very bad idea to have an atmospheric water heater in a closed crawl or basement. Although it’s not prohibited by code if you have big vents (2 required, one high, one low), but that would sorta defeat the purpose of encapsulating the crawl.
BTW, it’s unnecessary to keep your basement at 40-45%. There’s no benefit (other than for your utility’s shareholders) in keeping your house or basement that dry. As long as a crawl or unfinished basement remains below 60% or so, your building will be happy. 50% to 55% is a good maximum to shoot for in living space.
Hello,
Hello,
I have just bought a house with some crawl space issues. It’s for the most part dry outside of extremely heavy rains. It does have plastic down with gravel. It’s not overly moldy all the floor joist look great. Although it does have a Strong crawl space smell. hvac there is some trunk line that that is not insulated and does sweat. I’m in southern ohio. Also they added two supply ducts to the garage. When open the pressure obviously goes negative in the house and unleashes the crawl space smell the the house. I was planning on encapsulating the crawl. Adding a perimeter drain. Sealing and insulating duct. Insulating crawl walls. My next thought was to add a 6 inch supply and 6 inch return to the crawl. Controlling these with dampers and a Humidistat. My thought that running the return air through a filter UV light and over an evaporator coil would help with air quality over a transfer vent to the house? When the crawl was positve with pressure. The house currently has a furnace with with ecm motor that should compensate for change in duct pressure. (Carrier Infinity with 2 stage AC) any thoughts or insight would be great.
@Matt, your situation raises
@Matt, your situation raises several questions and is too specific to get into details in a forum like this. Feel free to contact me privately if you’re interested in professional guidance.
Musty crawlspace odor:&
Musty crawlspace odor:
I have a 100 year old house in NYC. I have a front crawlspace built with hollow building blocks and dirt floor,adjoining regular basement built with poured concrete, and a back crawlspace made adjoining basement with building blocks and dirt floor. The joists run from front crawl through basement to back crawl, so the crawls breathe into the basement. As spring and summer arrive i get musty smell that lingers until the fall. Once heating season arrives the smell starts. These have been my attempts to fix the problem. Easy Breathe fans (similar to wave or humidex) in each crawl space to remove musty air. 12 mil vapor barriers on the floor of each crawl space (but not tightly against the building block walls). Dehumidifier in basement and fans into each crawl space and then easy breate fans in both crawl spaces to expel musty air.
Possible solutions: Extend vapor barriers on crawl spaces floorsto within 2 inches of sill plates, but use polyurethane caulk to ensure the vapor barrier is tightly against wall and is not allowed to breathe into crawl space. Essentially trap the musty air under vapor barrier. 2. close off the air between crawls and basement. Not easy as each gap space is 8 inches by 23 feet.
I can’t fit crawl space dehumidifiers into crawl space but I could purchase a heavy duty dehumidifier that I could hang from basement ceiling and vent directly into crawl space. I could add crawl space humidity detectors into each crawl space to indicate the humidity and try to keep that at 50% or below. I could possibly remove the fiberglass insulation int the crawl space ceiling but prefer not to bother. Not sure how to insulate the rim joists as floors above crawls are cold in winter. I don’t thing I need french drains in crawls. The soil can be damp but I have never seen puddles of water.
I would love to hear replies from people who have had success. Thanks for listening and to any constructive advice.
@Kevin, vented crawl spaces
@Kevin, vented crawl spaces should be banned in the southeast. I’m from Charlotte, and I’ve never seen one that didn’t have problems. Slab-on-grade and basement foundations are much more efficient than a vented crawl, and are less costly than an encapsulated crawl.
Since you already have a crawl space, you should definitely encapsulate. But I would hold off on the DH. It’s not required by code.
If you address roof and site drainage issues, and the encapsulation is done properly, you’re unlikely to need mechanical dehumidification. You can always add one later.
Camille, I’m sure you read
Camille, I’m sure you read the threads here that this seems to be a problem for some of us. Our basement was also relatively dry but we had a pipe leak and it caused some mold. We overreacted with the encap and a dehu and ended up with a cat pee smell 6 mos later. Still have it. Think it’s the organic earth gases of some kind. But not going away. We may try a radon fan as that seems to be an option. A neighbor is trying this as he had identical issue. Please post what you end up doing as many of us are still searching for a cure. I simply added a vent fan to pull some air through. It helps a lot but the smell does go away. It just gets more vented out. I’d like it to go away. Thanks. Jeff
Note that soil gas mitigation
Note that soil gas mitigation solutions (i.g., fan-induced negative pressure below the liner) will not work very well unless the liner is continuous and sealed to walls and piers. I suspect if that were the case, the strong odor would not be seeping into the crawl space proper in the first place.
Before crawl was closed, the vents allowed soil gasses to escape. When the crawl is closed, it must be sealed properly, otherwise you end up with an unsealed closed crawl, which is a bad thing indeed.
Thanks David. Our builder is
Thanks David. Our builder is recommending putting in a Fan in the enclosed crawl to vent the bad air to the outside and have the outside air recirculate back in. Won’t this bring moisture into the crawl? He is also trying to see if he can use some type of foil instead of plastic. Other option would be to replace the plastic to see if it is a bad batch or not. or just remove plastic altogether which means we don’t have benefit of encapsulated crawl. It is just so strange that other homes in the neighborhood do not have this issue. Do you know of a specialist that could assist us with this as I am at a lose.
We just completed a 1,600
We just completed a 1,600 foot “pretty good house” in NW Oregon. We opted for a conditioned crawl space and use our Lifebreatth ECM-155 HRV to provide continuous ventilation at the IRC specified rate of 32 CFM. We monitor the RH and temperature of the crawl and it has been consistently 3-4 degrees cooler than the living space this winter. The humidity now tracks perfectly with the living space which is maintained at 50% by the HRV. Air quality in the house is excellent, we could not be happier with this system.
My 2,400 sq. ft. brick ranch
My 2,400 sq. ft. brick ranch house was built in southern Indiana in 2000. It has a crawl space that is 4 to 6 blocks high. It had the typical foundation vents. I closed vents in the winter and opened them in the summer. My living space near front door developed a bit of a musty odor only in 2011, mainly only noticeable in warmer weather. After a few inspections, no mold was found and the contractors have all appeared puzzled by the smell. After much research, I ended up closing the crawl vents year around, used foam board on inside to better seal them, installed new 10 mil vapor barrier and taped all seams. I went up the block walls about a foot and taped to block moisture. My block walls are all covered with blue board. I added a ventilation system, basically a radon system beneath the vapor barrier, and it pulls air 24/7 out one of the foundation vents. I also installed a dehumidifier in the crawl. While my crawl is staying pretty dry, I am still smelling that slight musty odor in my entryway to the right of my door especially. Thus, no help from the improvements. I have also noticed that my humidity in house goes as high as 59% now, depending on the weather. Any suggestions regarding odor or humidity? Thanks
The radon mitigation fan
The radon mitigation fan seems like a good idea.
I think that is the way I will go. Install 4 concrete block
plenum by laying the blocks on the side so cavities face the
4 crawl space walls. Fill with crushed stone. Then encapsulate
with a quality 20 mil barrier. If vapor pressure builds from organic
decomposition then I will have a place to tap into with the radon
mitigation system. The thinking is the fan thru the room would create
negative pressure under the barrier and pull air thru the soil to help
dry it out. Sure there will be rain see if the system can be timed not to
turn on during and immediately after rain. Just in case the vapor barrier
is not enough the plenum is there cheaply to tap into just in cast.