Where Should the Air Barrier Be Located?
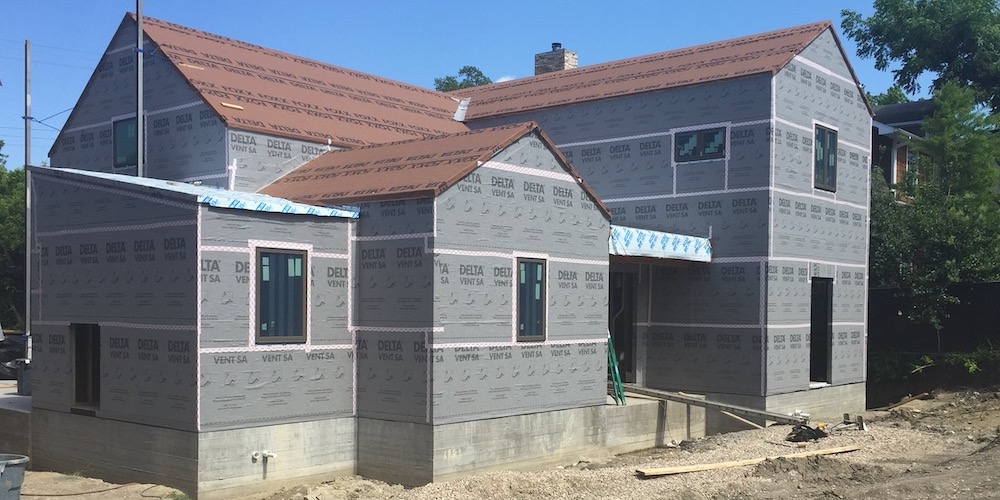
Where to put the air barrier may seem obvious, but this question has many dimensions…literally. Let’s look at the question of air barrier location from three perspectives. First, building assemblies are three-dimensional. The air barrier can go on the inside, outside, or in between. Second, the type and location of insulation makes a difference. Third, the air barrier can include or exclude buffer spaces, like a crawl space or attic. Which way should you go?
Inside, outside, or in-between
Most houses in North America are built with framing lumber that creates frames for the floors, walls, and ceilings. The building assemblies aren’t solid pieces of a single material, as a concrete wall is, but have an outside, an inside, and interstitial spaces in between.
The outer surface has sheathing, control layers, and cladding. The inside has the inner surface, with drywall, and perhaps a vapor retarder. The in-between part has wood framing and insulation-filled cavities. This kind of structure creates interstitial spaces that air leaking through the enclosure has to pass through to enter or leave the house. Double-stud walls have even more complex structures with the possibility of another layer between the two sets of studs. (See end of next section.)
“Buildings are complex three-dimensional air flow networks driven by complex air pressure relationships.” ~ Joe Lstiburek
These three-dimensional building assemblies mean that air can leak in at one location, travel through the interstitial spaces, and come out somewhere entirely different. During a blower door test, for example, you can feel air coming in through switches and outlets even when they’re on interior walls.
The interstitial space the air traveled through to get to the switch or outlet was the empty wall cavity. The place where the air came in might have been a wiring penetration at the top of the wall. That unconditioned attic air then travels several feet before entering the living space.
Think about the complexity of the structure of a framed house. A hole in one part allows air to get in. That air can move through a floor, wall, or ceiling, looking for a hole or crack that lets it get into the house. The distance could be a few centimeters, or it could be 10 meters (33 feet). The air keeps going, though, pulled by a pressure difference. It’s like ants getting into a house through the basement, traveling through interstitial spaces, and coming out in the kitchen, drawn by the crumbs they find there.
Outside is usually best
Now that you understand this kind of air leakage, you probably can guess the best place to put the air barrier for most buildings. It’s on the outside of the structure. Keep all unconditioned air out of the interstitial spaces. That solves most problems associated with air leakage. (The one that it doesn’t solve is moist, indoor air getting into wall cavities and condensing on the back side of cold, exterior sheathing. For that, the best solution is exterior insulation. Barring that, an interior air barrier and maybe a vapor retarder will do the job.)
Interior air barriers used to be a thing. Building scientist Joe Lstiburek even wrote a book on the airtight drywall approach in the mid-1980s. Air barriers on the interior side of the structure certainly can keep unconditioned air out of the house, but they’re not ideal.
One big drawback with interior air barriers is the potential for moisture and mold on the backside of drywall in humid climates. In an air-conditioned house, the drywall will be cool in summer. Without an exterior air barrier, humid, outdoor air can get into a wall cavity, find that cool drywall, and get the drywall wet enough to damage it or grow mold.
Another problem with interior air barriers is that they’re not tamper-proof. When someone makes extra holes trying to hang a picture or doesn’t seal the gap around the new thermostat, they’ve compromised the air barrier. When it’s a choice between the inside and outside of the structure, the outside is the better choice for the location of the air barrier.
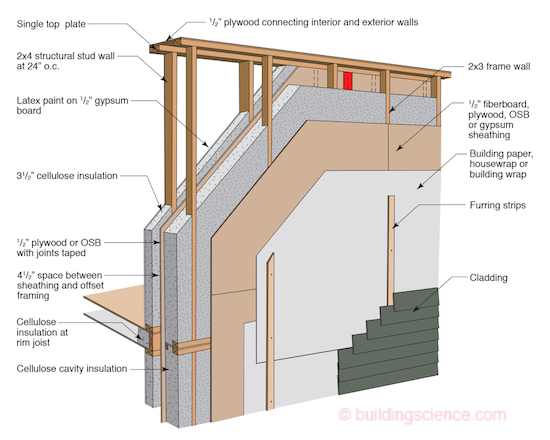
But there’s another option, too. Some superinsulated walls—like Joe Lstiburek’s ideal double-stud wall shown above—are really thick. Often, the air barrier goes somewhere in the middle of such a wall. That’s a really good place to put the air barrier because it’s protected from damage from both sides.
Where’s the insulation?
The second perspective of air barrier location has to do with its relation to the thermal control layer (i.e., insulation). For insulation to do its job of limiting the flow of heat, it needs to be free of air flow. The most commonly used insulation in homes is fiberglass, which is air permeable. When air flows through fiberglass or any other air-permeable insulation, it loses some of its ability to resist heat flow.
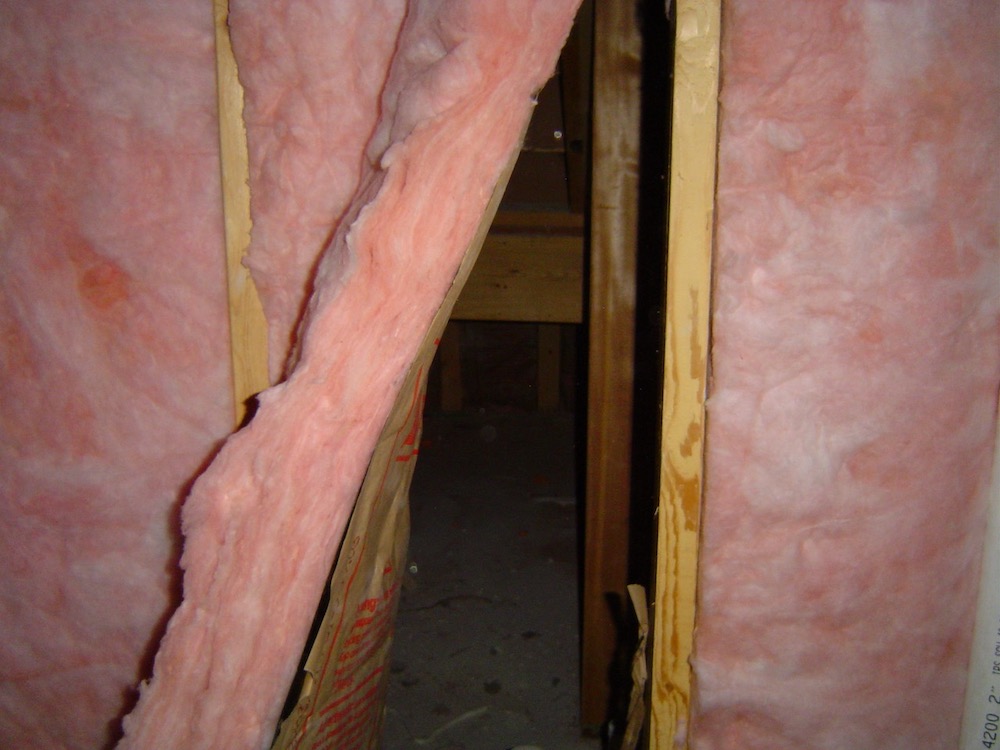
The implication here is that the air barrier needs to be right next to the insulation. You can’t have an effective building enclosure, for example, if you put fiberglass batts in a stud wall with no air barrier, as shown above. The same is true when your air barrier is at the subfloor over a vented crawl space, and the insulation is on foundation walls that have also contain vents allowing the free movement of air between outdoors and the crawl space. The air barrier needs to be aligned with the insulation. Air impermeable insulation materials have this alignment built in because the insulation is also the air barrier.
What about buffer spaces?
The third perspective of this question is the decision about whether buffer spaces should be included or excluded. The air barrier, recall, needs to be at the boundary between conditioned and unconditioned space. In complex buildings, it’s sometimes difficult to see exactly where that boundary is…or should be. We know, for indoor air quality reasons, a house needs a robust air barrier separating a garage from the living space. Basements, however, are often included, and that’s generally the best choice because of how difficult it is to isolate the basement from the living space above it.
To find the best place to put the air barrier with buffer spaces, you need to evaluate the pros and cons of each choice. How will including or excluding the buffer space indoor air quality? How easy will it be to do the air sealing? Which will be easier to insulate? Crawl spaces and basements are usually better kept inside the building enclosure. Attics can go either way, although it’s easier and less expensive to put the air barrier at the attic floor.
In the end, you want a house to have the best possible air barrier it can have. It should be protected from damage, aligned with the insulation, and exclude buffer spaces you don’t want inside the building enclosure. And then you do a blower door test to find out how airtight the house is.
Allison Bailes of Atlanta, Georgia, is a speaker, writer, building science consultant, and the founder of Energy Vanguard. He has a PhD in physics and writes the Energy Vanguard Blog. He is also writing a book on building science. You can follow him on Twitter at @EnergyVanguard.
Related Articles
Joe Lstiburek’s Ideal Double-Stud Wall Design
I Blew a Gasket — Air Leakage at Electrical Switches and Outlets
An Incomplete Building Envelope Doesn’t Work
NOTE: Comments are moderated. Your comment will not appear below until approved.
This Post Has 19 Comments
Comments are closed.
Allow me to preface this by saying we’re in a pretty low latent load area (Kitsap Peninsula, WA state). We generally have the air barrier at the drywall plane and work with aerobarrier on that.
However, we’re doing a case study project wherein we’ve changed the pressure boundary to the exterior. I’ve done a series of blower door tests with the latest one being yesterday. We started at 9.34 ach50 with minimal attention paid to the details, and the final pre-sheetrock blower door number was 7.75. Note that we didn’t follow all IECC protocols as we are only going for general results.
Yesterday we got 2.3, post drywall installation and finishing. Again, we didn’t follow all of the protocols of the IECC as this isn’t our final test. For this case study, we used spray foam in the walls, at the roofline, and at the underside of the floor (it’s way more complicated, but who wants to read all of the minutae?).
We’re a spec builder, so I’ve been trying to not devote an incredible amount of time to getting a low number. To get back to our area, we are a heating climate although ac is becoming more important. Due to the relatively low delta Ts and relatively low latent heat most of the year, the cost/benefit/risk exposure has tilted to the pressure boundary at the subfloor, drywall walls and ceilings. Note that we typically have vented crawlspaces and roofs (I know, that’s anathema to some).
Anyway, figured I’d share my two cents.
Bryan, I like your approach. Yes, climate matters, of course. I’m always leery of relying on drywall, though, because it’s so easily damaged. A plumber comes in to fix the drain behind the washer, for example, and the hole in the drywall doesn’t get repaired until years later. All that Aerobarrier material sealing the bottom plates and penetrations was just made irrelevant. If you do Aerobarrier while the walls are still open, not only is the air barrier likely to stay intact longer, but also you can use a less expensive insulation.
I lived in Seattle for a few years so I know the climate (although I don’t think we had any 90° F days back then, much less 106° F or whatever ungodly temperature it was there earlier this summer). Outdoor air leaking into the wall won’t cause moisture problems there, but it can diminish the effectiveness of air permeable insulation. With spray foam, you air barrier is actually the whole inside of the wall, though.
Roger that. We use Huber Zip System on the exterior, so there’s that factor. The only thought I might share about the idea of the damage created at drywall with a repair is that generally this will only affect a single “cell” or “compartment” or “stud bay” of the outside wall system. I view it like watertight compartments or hull divisions in a ship. They should be sealed from each other, so that if there is a puncture, the whole hull (building shell) shell isn’t negated.
Obviously, the analogy isn’t perfect as each stud bay isn’t necessarily totally sealed from adjacent bays. And the following numbers aren’t perfect, but with a somewhat made up average number of stud bays of say, 100 in a house (square plan, 4 fifty foot long walls with 24 inch o.c. stud spacing), one or two repairs wouldn’t grossly impair the house’s airtightness.
Thank you for your posts, I’m thankful you’re in the industry.
Good point, Bryan. There’s definitely resistance to air flow from one stud bay to another, but in the case of air permeable insulation, it’s not hard to find lateral wiring penetrations and gaps around studs. I know you’re using spray foam, at least on some of your houses, so that resistance is much higher there.
If you haven’t seen it, here’s an article I wrote about a bathroom remodel I did five years ago. The sheathing was Celotex, which created some interesting air flow pathways.
Air Flow Pathways in a Leaky Bathroom Wall
Hi Bryan, just curious what IECC version your locality is on…? Aren’t those blower door ACH numbers going to fail code requirement?
This particular home is vested in the 2015 WSEC (a stricter version of the IECC). The way the Washington code works is that there is a menu of energy credits that have to be selected which causes the home to be more energy efficient than following the code only. The base code requires 5 ach50, but the choice can be made to select energy credits based off of a tighter envelope and ventilation solutions/efficiency.
Where the 2018 code gets challenging is the decision to go with 8.5 feet x square footage as the cubic volume. No more does one get an easier blower door by a large double height wall or similar volume input.
In fact, I’ve been tracking this metric (the code cubic volume vs. actual cubic volume), and the 5 results so far are below. If the code credit decision of 3.0 ach50 was used, it would pass via the 2015 code but fail via the 2018 code.
Actual CV Code CV Difference
ACH50 ACH50
11.7 9.34 2.36
11 8.78 2.22
10.8 8.63 2.17
9.7 7.75 1.95
3.16 2.5 0.66
Wow that’s an interesting twist on the base code! Levels the playing field in some respects…
Is it necessary to disable or somehow immobilize the whole-house ERV while running the blower door test?
Aron, yes, anything that moves air between indoors and outdoors needs to be turned off during a blower door test.
Excellent post – again! Your point that interior walls must also be considered is right on point. Adjacent spaces where a lot of moisture is generated (like residential commercial kitchens, bathrooms, steam rooms, walk-in freezers, cold rooms, basements used for crafts or shops, laundries, hair washing stations, … un- or under-conditioned/ventilated spaces …) any of these can create an inadvertent ‘exterior’ condition.
Now add another of my favorite complexi-fiers: wallpaper. Most have permeability ratings consistent with air barriers. We’ve seen some things.
Monica, as your comment makes clear, the air barrier is inextricably tied to moisture control. Controlling air flow is the best way to control water vapor.
Allison – I think Joe sums it up regarding the complexity of air flow, moisture flow, and thermal flow through out building envelope. For me the air barrier is too complex to boil it down to one plane or spot on the house. I think we need to think about the building thermal envelope as an assembly and the air barrier system in the same way. Therefore we should concentrate on both the interior and exterior air barrier systems. Drywall would be a primary air barrier on the inside and sheathing on the outside. Where we don’t have continuity we add supplemental air barrier systems. This is really what the EnergyStar thermal checklist and IECC Table R402.4.1.1 are getting at.
Belts and suspenders, to better ensure that those interstitial spaces are protected from air flow, moisture flow, and heat flow and we get better control and predictability from our assemblies defining the building thermal envelope.
My 2 cents – Thanks for bringing this up.
Robby, yes, air sealing both the drywall and exterior sheathing on walls is the best way to go to keep all wall cavities airtight. As I mentioned above, though, drywall makes a flimsy air barrier because of the number of holes it develops over time. The airtightness remains good if the exterior sheathing is sealed, although it, too, gets holes punched in it that don’t get sealed sometimes.
I am interested in reader opinions on the best air barrier design for the lower portion of an exterior wall of the second story of a house that extends below the roof (the upper portion is lap siding over house wrap). In my case, the attic is vented/un-conditioned.
For example, would you use sealed OSB, drywall over house wrap or a sheathing like Georgia Pacific DensGlass?
I think placing the air barrier at the exterior makes more sense. You can align the air and water barriers. When the air barrier is at the outsurface you also keep bugs out.
The air barrier will be better protected. It doesnt take many small leaks to have a proportionally big impact on a tight structure. An easily comprised barrier could turn into swiss cheese in a couple of decades. We should think long term durability.
Matt Risinger has a good video on blower door testing of a house that was well air sealed but they wanted to take it to the next level.
Great post. Speaking as a dry climate homeowner doing retrofit, only so much can be done to improve the outside air barrier after the fact, mostly in the attic and around doors/windows. This makes me think that there is no harm in then also trying to seal the interior as much as practical. Why not seal all electrical penetrations/outlets/switches, openings behind cabinets, medicine cabinets, around baseboards, canlight trims, pipes, and any other place where the gypsum was compromised? The house itself could have a stack effect in its interior or when the various forced air units/fans run could pull air around the rooms/floors including via interstitial gaps.
I have noticed another area seemingly glossed over are the various fan exhaust dampers. Those can add up too.
I have a cabin in Tennessee. I don’t have drywall interior walls by rather wood planking, with fiberglass insulation. Would I be better off with an air barrier inside and outside, with water barrier on the outside?
A single great air barrier is better than two good air barriers. And once you have one great one you don’t need a second. I’d do it on the outside.
Looking to build a house on a lake in Central Alabama soon. I’m also interested in an answer. to the question M Jolie asked above.