Guest Post: The Fatal Flaw in Advanced Framing, Part 1
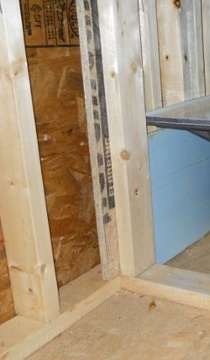
A few weeks ago Allison made a couple of quips that could be construed as critical of Advanced Framing methods, also often referred to optimistically as Optimum Value Engineering (OVE). I myself am generally critical of Advanced Framing, so perhaps I was just reading into Allison’s comments what I wanted to hear. So I messaged him “You ought to do a whole article expanding on the criticism of Advanced Framing,” and he replied “Ok, you ought to write it for me.” So here I am.
A few weeks ago Allison made a couple of quips that could be construed as critical of Advanced Framing methods, also often referred to optimistically as Optimum Value Engineering (OVE). I myself am generally critical of Advanced Framing, so perhaps I was just reading into Allison’s comments what I wanted to hear. So I messaged him “You ought to do a whole article expanding on the criticism of Advanced Framing,” and he replied “Ok, you ought to write it for me.” So here I am.
My issues with Advanced Framing are not with the details, or at least only with a small part of the details, and are more with representation of the whole package. So in this piece I am going to dwell more on the context, and less on the details. I’ll spend a little time talking about what I see is problematic, and more time talking about the fallout of the problems and how it undermines what there is good and useful to be taken away from this.
Basics of Advanced Framing
Advanced Framing is well known among green building advocates and professionals engaged in energy matters of building houses. I’m not going to explain it in detail because there are many good resources online. If it’s new to you, or you’ve heard of it but don’t know the details, here are a few solid resources. Green Building Advisor has a good overview in the Energy Nerd blog. You can also go to ground zero at the DOE’s page on Advanced House Framing. In the green building frenzy, there have even been entire how-to books published on the subject.
Let’s get the brief lesson over with already so we can get on to the important ideas. Advanced Framing is a variation of the Western Platform Framing model, developed during the 1960s primarily as a technique to reduce the amount of lumber used in framing, and hence the cost. More recently it’s been taken up by green building advocates as a way to improve the energy performance of wall assemblies. It’s telling that this was not the original intention, and that while it does do a little bit of this, it does not do it exceptionally well. The main mechanism here for improving performance is reducing thermal bridges by simply reducing the amount of wood in the wall, and hence the bridges from the exterior to the interior.
Common-sense Advanced Framing methods
Advanced Framing sets out to do this with several common-sense modifications to standard framing practices, and one very impractical modification. First the list of what is common sense:
- Framing on wider centers such as 24″, which increases the amount of insulation in the wall. This helps a little bit. And it does save you studs.
- Two stud corners which reduce studs again, and allow you to get insulation into the corners.
- Single stud jambs which prevent the bulking up of jack studs and cripple studs at window openings, which again reduces the number of studs and associated thermal bridging.
- Right-sized insulated headers including no headers in non-bearing walls. This gets less play but helps to keep extra wood out of the wall and reduce thermal bridging.
- Eliminating studs at intersections with interior partitions. Perhaps this is the most minor, but also clearly useful. (Photo at top shows this.)
These are all sensible techniques, easy to do for any home builder, whether they think they are pursuing better performance, or just trying to save a few dollars on lumber. It’s something we should see being done everywhere, after all these ideas have been kicking around for 50 years. But it is not, and even in the current climate where we now have a small community of green builders zealous about performance and sustainability, the vastly larger housing industry ignores these techniques, things that could legitimately save them money and earn them more profits.
The I-can’t-believe-anyone-does-this Advanced Framing method
So why does the housing industry ignore what could be a license to print money, albeit not a great deal of money, but I don’t recall this industry ever shying away from fractional gains – I’m talking to you 7/16″ sheathing. It’s because of one additional modification to standard practices, the one I feel is problematic:
Single top plate
Wow, brilliant! We cut the thermal bridging of the top plate in half there and save a pile of studs! Ok, let’s high-five all around before we read the fine print on this deal. You see, it brings along a bit of baggage. To eliminate that one 2-by from your top plate, you’re going to have to line up all your framing on a 24″ grid.
OK, thanks, bye.
Can we re-engineer for the single top plate and grid?
Wait a minute there before you run out the exit. Did you just say you want me to line up all my framing on a 24″ grid? As in every window location has to fall into that grid? And my windows have to be 24″ wide or 48″ wide or they are going to need an off-grid jamb stud? The last time I looked, my front door is not 24″ wide, or 48″ wide for that matter. And things that make big holes in my floor, like stairs? Well, they’re rarely 4ft wide and even less so 24″ wide.
Ok, ok, this isn’t rocket science, and I’m a grown up. I can design a house on a 24″ grid, and it will all be easy as pie. My housing industry is working from existing house designs that are going to require at least some re-engineering to make this work. Maybe I’m a small builder working with only 20 or 30 of them myself, but let’s take a peek out on the Internet. What do you know?! There are something like 100,000 house designs to update. That’s only doing a couple of thousand plans per year for the past 50 years. Sure we can do that, sharpen up our pencils and get right on it, but only if you share some of what you’ve been smoking.
Pardon my snark if it chafes you. Yes, I’m exaggerating the scale of re-engineering here. The point is that this one recommendation of Advanced Framing brings with it so much baggage that the trouble to adopt it greatly outweighs the benefit. The proof is in the numbers. Advanced Framing has a track record of a spectacular Failure to Launch, in that after 50 years, it has only recently won the support of a tiny segment of a special interest within the housing industry. As far as the industry goes Advanced Framing has already come, failed, and gone. And no amount of trying on the part of those interested in better performance will change that.
Stay tuned for part 2 tomorrow!
About the author
Gregory La Vardera is an architect in practice, and a building scientist by training. Outside of his local practice he is focused on opening up niche markets in housing, and is interested in the development of broadly adoptable strategies for high performance building including off-site manufacturing of houses. You can read his blog for more info about the Swedish Platform Framing method and other topics.
Related Articles
A Huge Heat Loss Flaw – A Lesson in Energy Efficient Design
This Post Has 18 Comments
Comments are closed.
Brilliant! Thank you.&
Brilliant! Thank you.
Add the reality of framers that generally are unable, or unwilling, to follow a framing plan in the first place. Are most even capable of aligning the framing in that kind of precision?
A challenge at best.
the sweedish method is
the sweedish method is interesting but the critique of advanced framing seems limited to the top plate. Doing all of the rest and keeping the double top plate seems like the easy answer. Still a lot of benefit and with some exterior foam the disadvantage shrinks.
Nice start. I look forward to
Nice start. I look forward to part II. I am also a proponent of advanced framing, mostly right-sizing headers and an open corner for insulation. I also like the reduced lumber use as it speaks to my inner cheapness. I do not see 24″ OC as a problem; simple cad (or a wall panel plant) can easily design for alignment, and the single top plate? meh. a little thermal bridge and a tiny bit of wood. Keep in mind that alignment is an issue to some extent, code-wise, even with a double top plate on 2×4 walls. 2 stud corners or open 3 stud corners get my vote for smartest idea ever in energy efficient framing.
Every energy seminar that I
Every energy seminar that I have attended focuses upon mitigating the inherent flaws in building energy efficient structures with stick framing. This is the classic “putting lipstick on the old bulldog”. There are several alternative building technologies available now. If we really want to get serious about building energy efficient homes, we need to move away from this form of construction. SIPs, ICF, and Superior Walls pre-cast insulated concrete panels are three examples of extremely energy efficient technologies readily available. All of these can virtually eliminate air infiltration and ex-filtration through their wall systems.
Geoff yes, framers can do it
Geoff yes, framers can do it successfully & there are quite a few good ones out there that do it everyday. With that this method isn’t feasible in many areas with seismic or wind requirements.
I got to say as I hit the midpoint I was simply just shaking my head at some of the absurdity – I see no issues with… The only issue is… & then I see the reason in the author’s bio – Swedish framing.
Well Gregory & anyone considering using OVE / advanced framing – try to remember that the whole house is a system and it impacts everyone working on it & then living in it later. If you do want to consider some of the issues – http://bit.ly/CSB-OVE
As we approach the 200 year
As we approach the 200 year anniversary of this technology, I think the big joke is that people are still doing stick framing at all. US DOE tells us that AVERAGE thermal wicking of stick framing is about 25%. So you have 25% of the house that is about R4. Another 15-20% of the home is windows & doors, so we are at 40-45% of the home that is about R4. Are you kidding me? It starts to not matter whatever you put for insulation in the walls, you are fighting a losing battle if almost half of the home is R4. And Advanced Framing improves this ratio very little as the author notes above.
It seems to me the biggest
It seems to me the biggest problem is the “this is how we’ve always done it” mentality. Take that with the misconceptions most framers have about how much is needed to make an adequately stable structure and you have your reason for the Advanced Framing failure you’re talking about.
There seem to be a lot of good ideas for building better homes that builders simply ignore because they just want to do what they are comfortable with instead of trying something new. Can you blame them? These days everyone has that fear in the back of their mind that something will go wrong and get blamed on their new technique. For most the risk of failure outweighs the cost benefit.
Calling what Greg described
Calling what Greg described as advanced framing is like calling the Model “T” an advanced mode of transportation, which I will agree it is compared to the horse & buggy.
The only major gain I see with the advanced framing he describes is switching to 2x6s (R-6) 24″ O.C. from 2x4s (R-4) 16″ O.C. And, the major gain with that is due more to R-11 (3-1/2″) fiberglass being replaced with R-19 (6″) fiberglass – – R-23 Roxul today. In my opinion, the rest of the thermal break improvements that he describes are “minimal” and not worth the effort to retrain carpenters. It took years for Maine carpenters to accept that 2×6 24″ O.C. was stronger than 2×4 16″ O.C. and many 2×6 homes were built 16″ O.C. and some still are being built that way today.
While 2×6 (24″ O.C.) construction was advanced 34 years ago when I was the first to build with such construction in my municipality, Maine adopted that as a state construction requirement around 20 years ago. Yes, I was ahead of my time 34 years ago, but 32 years ago I was already experimenting with double-wall construction which really provides for some highly significant thermal breaks. I also have 32 years of developing economical methods of building double-walls and increasing their thermal break properties.
I will look forward to Greg’s The Fatal Flaw in Advanced Framing Part 2. Perhaps I will learn something. Perhaps he and others following this discussion will have the opportunity to learn something from what I will have to share.
I think some of you are
I think some of you are missing the point; I doubt highly that Greg is advocating a 2×4 wood sheathed wall as an energy efficient structure in and of itself, just the minor energy benefit gained from some of the techniques. Double framed walls are great, but only one is structural, and certainly neither need to be 2×6, unless it is a 3 story structure. SIPs and ICF’s and the such are great, but from a cost standpoint, still not where the market at large can embrace them. These techniques are largely adaptable to any jobsite with a little education and effort. SIPS and ICF’s? not so much.
From a purely structural
From a purely structural perspective, the vertical load path uses the double top plate both for rafter ties and for the 3″x3″ staggered nail pattern to “sew” the wall together using the structural OSB or plywood sheathing. If you eliminate that second top plate, you will have to supplement the top connection with extensive metal strapping over the top of the rafters and then downward onto the stud faces. All of this for very little reduction in thermal coupling from plates. The number one challenge (IMHO) is stopping drafts and convection. Housewraps perform miserably with this as they are do not address the very top of the wall and joint between foundations and exterior sidings (brick veneers are much better here as they bridge that connection). Wind blows up under the siding and up into the wall cavities from here. The only way to truly seal a stick frame structure is with spray foam (again IMHO). When you really solve the whole energy problem with stick framing and add in that cost, alternatives become much more competitive. Then add in the benefit of a much stronger structure and the decision becomes much easier. This is all about education and changing an entrenched mindset.
So they call it advanced
So they call it advanced framing now?! Ha! We call it “rural” or “ghetto.” I’m kidding (no I’m not).
Seriously, if we’re talking about building techniques and looking for general consensus, we’ve come to the wrong place (I don’t mean Energy Vanguard). The world of building is too spread out for a one-size-fits-all.
Depending on what you’re building and who you’re building for will dictate your technique(s). If you’re looking to save the world then maybe advanced framing is the first step in the right direction. If you’re looking to save some cash on a spec house, well…whatever…more than likely you’re cutting corners elsewhere too and are likely building a piece of crap.
I’ve been milling my own lumber recently so I generally try to “cut corners” (yep) and reduce the amount of framing material I use. I like to use a 4×4 top plate with a half lap for partitions. It means less milling without sacrificing the strength.
If you’re truly worried thermal bridging at the second top plate, use a 2×3 and pack the rest with foam. If you’re that worried about the amount of lumber being used, start looking into the natural building world instead.
I consider myself to be a sort of hybrid builder. I cherry pick from all the different worlds. Conventional, natural, and alternative. It’s liberating when you’re not beholden to the rigidity of one possible accreditation or some sort of snazzy certification. It’s like voting your conscience instead of your party line…the results are always custom and unique.
Most of what I see in Advanced Framing resembles good old-fashioned common sense building practices. But let’s be clear…if you want a 36” window, pop in a header and call it day.
I like the drywall clips instead of the triple stud. I’ll have to try that some time when I’m not using lath & clay plaster.
Tom, agreed on the difficulty
Tom, agreed on the difficulty of air sealing, but I have gotten great results using Zip and liquid applied air barriers. If you can get your framer to caulk the top and bottom plate prior to sheathing, and use Zip and tape joints and wrap window openings, air sealing gets a lot easier.
A good piece and getting
A good piece and getting framers to adapt is a challenge. Raised Heel trusses at 24o.c. compared to conventional framing takes a huge amount of lumber out. for non load bearing interior walls why not use single plates with a longer stud or 2×3 stud walls (yes it requires changes to door frames). Longer length OSB panels eliminate blocking and reduce air leakage big time.
Let’s skip all the mumbo
Let’s skip all the mumbo-jumbo and blaze into the future of advanced framing: TRIPLE TOP PLATES. Bam. Done.
The problem with relying on
The problem with relying on spray foam for air sealing is that it is simply not the panacea that the manufacturers make it out to be. #1 – spray foam can not/should not be applied on cool studs. It will initially appear to stick and then peel away (so they always try to get the sheetrock up quickly) creating many voids & air leaks. We see this on about 1/2 the homes we look at. #2 – spray foam is often installed with air gaps between the foam & the sheet rock – “You only need a couple of inches because it is soooo good!” they say – but this is simply not true. You need to fill the cavity ENTIRELY to eliminate air gaps that will form convective loops & reduce R values. There are much better systems than stick & spray foam.
Charles,
Charles,
Not sure is your concerns are climate related or not. I spray closed cell foam under all roof decks and seal attics completely. I do this for structural as well as insulating reasons. I have not run across your cold stud issues and am not sure who “they” are when you refer to installing sheetrock quickly. As sheetrock typically goes up after insulation has been installed, that would be normal. As for convective loops, I have a problem with your assessment. Air movement with porous fiberglass batts certainly can reduce effect R values, but with closed cell foam that does not pass air or moisture, I doubt that air moving across the surface reduces the R any more than air moving across the sheetrock face. And yes, when you take all aspects of draft stopping, waterproofing, and increased structural strength, closed-cell foam could actually be the panacea they claim it to be.
The headline seems out of
The headline seems out of touch with the content. You provide a list of ‘common sense’ items and then one problematic issue around the top plate. So do all the ‘common sense’ items and use a double top plate!
Interesting topic. If
Interesting topic. If builders did calking plus added ridged foam board with taped seams to the exterior sheathing, would this also help the insulation facts mentioned in the above posting.