Thermal Comfort: Everyone Wants It but Few Know the ASHRAE Standard
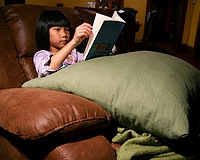
GUEST POST: As the Affordable Comfort conference kicks off today, it’s appropriate to take a look at what comfort is and how we construct buildings to have the best shot at getting it. Robert Bean is an engineer in Calgary who’s full of knowledge and wisdom on the topics of building science and HVAC, especially radiant heating. In addition to having all kinds of credentials and honors, he’s the editor of a great website called Healthy Heating, which you really should check out. In this guest post for the Energy Vanguard Blog, he discusses the ASHRAE standard on thermal comfort. Pay attention, because he makes a statement toward the end that, I believe, could lead to a great shift in our thinking about buildings.
Let me start by suggesting that one would think that an industry with its roots grounded in thermal comfort, could roll the definition of thermal comfort right off its tongue like an old Frank Sinatra classic. I mean this should not be difficult to do right? It seems almost obvious that someone who sells comfort equipment or designs HVAC systems for comfort or repairs buildings to be more comfortable should not have to think about what it takes to be comfortable right?
Unfortunately, if you assembled a thousand people from the professions of HVAC contracting, energy auditing, construction, engineering, interior design, architectural, and manufacturing in an exam hall and asked them only one question, that being to list the 10 key elements of an industry thermal comfort standard, approximately 30 individuals would pass. How do I know that? Because I’ve been asking that question in classes for over a decade and typically only 3% get it right and of these only half of them own a copy of ANSI/ASHRAE Standard 55 Thermal Environmental Conditions for Human Occupancy.
The purpose statement from this standard is, “to specify the combinations of indoor thermal environmental factors and personal factors that will produce thermal environmental conditions acceptable to a majority of the occupants within the space.” This standard is as equally resourceful as other ASHRAE standards and was first published 1966 – that would be almost 37 years before ANSI/ASHRAE Standard 62.2 (Ventilation and Acceptable Indoor Air Quality in Low-Rise Residential Buildings) came unto its own.
So let me take this moment to ask a few basic questions: Do you provide products or services related to thermal comfort? If so, could you right now explain ten key elements of thermal comfort? If you do promote thermal comfort, do you own a copy of ASHRAE Standard 55? If not, why not? I’m always intrigued by the answers I get. Most people don’t even know the document exists.
Along this line of questioning, how many consumers and their service providers believe comfort is defined by a numerical thermostat setting? If so, why do we have color-coded temperature controls in cars and on plumbing fixtures? Is comfort provided by high efficiency furnaces? If so why do people still complain about discomfort with the newest of appliances, especially in origami homes constructed essentially of glass? Is indoor air quality a requirement of thermal comfort or thermal comfort a requirement of indoor air quality? If so, can you explain all the thermal comfort complaints in leaky homes or how it is that you can sit back in your granddad’s La-Z-Boy™, tipping back your favorite brew, feeling all warm and cozy inside whilst inhaling radon gas, VOCs, or carbon monoxide?
The latter of these questions are definitively rhetorical and stated only to point out that neither air quality nor thermal comfort serve as proxies for each other. In fact, ASHRAE 62.2 states the standard does not address thermal comfort, referring users to ASHRAE Standard 55. Likewise, ASHRAE Standard 55 states that the standard does not address indoor air quality.
These questions should get you to start thinking about what thermal comfort really is. Now here’s mind-blowing part: According to indoor environmental ergonomic definitions, thermal comfort is (wait for it) a “condition of mind.” That’s right – it’s in your head and your client’s head and because all heads are not alike (unless you’re in the club of medicinal marijuana licensees), thermal comfort is and always will be a subjective perception.
Ultimately one of the difficulties in discussing thermal comfort is that this definition of “condition of mind” sits, “at the crossroads of physics, physiology, psychology, culture, and climate (Solomon, 2011);” and as I like to point out, it does so amongst a competitive industry driven by public relations, marketing, and sales teams all offering products and services related to a term that it doesn’t really understand nor can it accurately define.
In the space allotted I’ve not gone into the exhaustive details of thermal comfort but I have provided in the reference section below numerous free resources for you to study at your leisure, including a link where one can purchase the ASHRAE standard; in a nutshell the ten elements for consideration when addressing thermal comfort are shown in the accompanying table.
Most are familiar with “dry bulb temperature,” that being what 99.99% of all thermostats measure and readers of the Energy Vanguard Blog should now be familiar with “mean radiant temperature” from Allison’s infamous article, Naked People Need Building Science, but the others are equally imperative to understand when establishing conditions for thermal comfort. When all are considered, it points out why the typical thermostat is a poor “thermal ambassador” to an HVAC system since most fail to perceive what the occupants perceive.
As I wind down this post, I want to point out one of the principles that indoor climate engineers understand full well – there exists an intimate relationship between building performance and that “condition of mind” and ultimately HVAC must start with the choice in architectural systems where energy consumption and system complexity is inversely proportionate to the performance of the enclosure. As David Butler pointed out in his excellent guest post, the enclosure should do the bulk of the thermal comfort work.
In support of this principle, I have stated on several occasions that if building codes dropped the reference to controlling air temperatures and switched the requirements to controlling mean radiant temperature, building performance specifications would have to change overnight. Bad buildings have low MRT’s in winter and high MRT’s in summer; this contributes to large differences in the vertical air temperature; creates excessive drafts and increased radiant asymmetry. Bad buildings also have uncomfortable floor temperatures and are challenged to maintain reasonable levels of humidity.
I believe once you read and digest the content below (linked for convenience), you will be motivated to purchase the ASHRAE standard and embrace its messaging as it relates to improving building enclosures and reducing energy demands for conditioning people…because at the end of the day people don’t feel the heat loss or heat gain of the building, they feel the heat loss and heat gain within their bodies and this will effect a “condition of mind”, that being our individual perceptions of thermal comfort.
Copyright © Robert Bean, R.E.T., P.L.(Eng.)
The views and opinions expressed in this post are strictly those of the author and do not necessarily reflect the views of The American Society of Heating, Refrigerating and Air Conditioning Engineers (ASHRAE).
Photo by stevendepolo from flickr.com, used under a Creative Commons license.
This Post Has 19 Comments
Comments are closed.
Very true. We have
Very true. We have technologies such as variable speed blowers and humidity sensing thermostats but they are rarely implemented correctly. HVAC contractors seem to be stuck on “400CFM per ton of cooling” regardless of SHR. Thermostats/humidistats should be able to dynamically set the CFM/ton to any value between coil freeze up and max blower speed to achieve COMFORT. If humidity in the space is 70% run the blower @ 200CFM per ton, the high latent load will prevent freeze up. If humidity is 35% run the blower @ 600CFM per ton, no latent removal is needed.
Having return and supply registers at different heights helps a lot in mixed climates. Low returns help suck cold air off the floor while high supply registers help break up the heat collected at the ceiling in summer.
Manual D comes to mind also, lets size ductwork so all rooms have about the same temperatures w/o the need for zoning. While we’re at it bring all the ductwork into conditioned space instead of hot attics/cold crawlspaces.
Lets get equipment sized right, stop making the thermostat the “bar” on design days, and making other comfort factors more priority.
It could be said that the
It could be said that the thermal envelope enclosure determines the comfort level of a home. The HVAC system simply maintains comfort which has already been predetermined. Although, a 3200 degree fire and 130 degree air can cover up a multitude of defects.
This is a great post and a
This is a great post and a long time coming. Years ago I learned that ASHRAE states that the number one influencer of in-home comfort is RADIANT ENERGY. Not conduction, not convection, RADIANT (and ironically radiant floor heating doesn’t even touch the meat of the problem). Everyone knows what it’s like to be on the cool north-side of a home and yes this is a very subjective condition. But how does it get that way and why does it vary so much from room to room? Actually conduction has a lot to do with radiant energy in a home – it’s still the same energy, just in a converted form. BY LAW (code), a typical stick-built home’s building envelope is 23-25% wooden structure – the exoskeleton of the wood frame. This wood has an R value of approx 1 per inch. Therefore most homes are approx 25% R4-R6 (call it R5) depending upon stud & sheathing thickness. Think of the fact that a single 9ft stud has MORE surface area as a one square foot window. How many stud “windows” do you have in your home (and don’t forget headers, etc)? It matters little what you put in-between the studs compared to the thermal wicking of the studs themselves. And what are the studs typically directly connected to? The THERMAL MASS OF SHEETROCK. So you’ve got this highway of flowing energy – remember approx 25% of the building envelope – transmitting the outside thermal environment to the thermal mass of sheetrock. Actuall it doesn’t have much thermal mass but it does CONDUCT thermal energy across it’s surface to a high degree – bypassing insulation – and this then is RADIATED throughout the room. Remember how the sheetrock is always cool to the touch in that north room? This is why radiant energy is the number one influencer of indoor comfort. Nevermind the 15-20% of a building envelope that is windows and doors – so approx 40- 45% of your stick-built home is in the neighborhood of R5. We have long believed that it is inherently energy inefficient to build homes using 2×4 or 2×6 construction – and darn tough to make comfortable.
What a great article Robert!
What a great article Robert!
Comfort is so dynamic and that should not be forsaken, but seems that it often is due to its overwhelming lack of understanding. Until now I have thought only airflow, MRT, humidity and sensible temperature were the components that affect comfort, but reading your article lets me see that delving into each of those components deeper is where the answers and solutions will be found. The wild card is the “mind”.
I am encouraged to continue reading (as I always do) and I do not own the ASHRAE Standard 55, but have already purchased one after reading this article. We have a world of opportunity to make occupants more comfortable while also saving energy, but using the holistic approach seems the only, or at least the best way to get there. Most of the HVAC industry seems to not want to fight the tide that is rising but I HOPE they will, or be left behind as some begin to embrace the documents and information that is readily available and use it to make these homes better and help people find comfort.
Your statement of people not recognizing the heat loss/heat gain of buildings, but of their “they feel the heat loss and heat gain within their bodies” only is POWERFUL! Finding that balance of the building and the people should be our goal and I feel ignited! Thanks again for this great post!
Good work. Putting a link to
Good work. Putting a link to this post on my HVAC courses.
Other things to consider are
Other things to consider are how HVAC contractors are “hired”. The typical doesn’t think about HVAC unless it’s hot/cold in the house or their power bills are $300+ per month. In the 1st case they could care less about efficient design, they just want to be warm/cool NOW at the lowest possible initial cost. Add to this when a system breaks sometimes homeowners will wait until the hottest day of the summer to call the HVAC contractor and get it fixed. The HVAC contractor is already working 10-12 hour days trying to keep up, probably doesn’t have 1/2 a day to do a complete energy audit/manual J etc. He’s making his money in the “busy season” to cover for fall/spring when it’s slow.
Good article! ASHRAE (which
Good article! ASHRAE (which by the way no longer stands for anything but is rather their official name instead of an acronym)55 and 62 should be the most dog-eared reference docs in any in this industry’s arsenal. Along with a psychrometric chart of course!
I would encourage everyone who hasnt got one and read it word for word to do so in order to gain a better understanding of the specific definitions of comfort, the “occupied zone” – ankle to shoulder of a sedentary standing adult, and what percentage of occupants are realistically expected to feel “comfortable” within the purvey of what the standard qualifies. These are very specific criteria for those of us that engage in significant expert testimony, forensic diagnostics and troubleshooting.
I also suggest everyone become intimately familiar with how to conduct ADPI. Air Diffusion Performance Indexing as well as the measurement methodology and standards of NEBB and AABC.
Get out from behind that infrared camera and learn what is going on in that “uncomfortable” space!
Thanks for the kudos Robert!
Thanks for the kudos Robert! I failed to mention in my recent article that that was the most comfortable home I’ve every lived in. To Charles’ point, no doubt the insulated headers and insulated sheathing had a lot to do with that. I also controlled MRT by disallowing any direct solar gain in summer, and minimized the impact of air movement by careful register placement, and in winter, I slowed down the already low system airflow, which was less than 0.30 cfm/ft2.
Bob wrote:
“If humidity in the space is 70% run the blower @ 200CFM per ton, the high latent load will prevent freeze up.”
Not true. First, reducing cfm/ton does not create a high latent load, or even increase the latent load. In fact, it slowly reduces the latent load as more mositure is removed. I think what you meant is running a low cfm/ton increases latent capacity. Second, slowing the blower to 200 CFM/ton is a sure way to freeze up the coil, or cause the system to default to operating on the low-limit switch. I sure hope you’re not an HVAC contractor!
you also wrote:
“…lets size ductwork so all rooms have about the same temperatures w/o the need for zoning.”
Sorry, but it doesn’t work like that. The design CFM for a given room is often very different from winter to summer, especially in multistory homes. Moreover, the room-to-room load balance changes throughout the day, and from night to day based on the sun. You can improve temperature performance of a non-zoned system far more with good design (overhangs, building shell, orientation of comfort-sensitive rooms), than by sizing ducts according to Manual D. I’m just sayin…
A study was done to see what
A study was done to see what systems were actually delivering with small/poor designed duct systems and they found most systems weren’t even doing 300CFM per ton. Static pressures were measured at 1.2″ and higher, even though blowers are only designed for 0.5″. Perhaps 200CFM/ton is an low end, but the point is CFM per ton shouldn’t be “locked” @ 400CFM/ton regardless of latent load. ICM has manufactured a variable speed control that is supposed to do all of this automatically, not sure how it works in the real world.
http://www.icmcontrols.com/Comfort-Control-Center-field-programmable-motor-speed-controller-115-VAC-model-Prodview.html
Duct design in Oklahoma is awful for the most part. Rooms that are hot in summer AND cold it winter aren’t uncommon. No allowance is made for number of exterior wall or distance from air handler. Ducts are sized by sqft of the room!! With 2 floors you need some sort of zoning or 2 systems to get even temps. I’ve never seen a 2 story house with even temps that wasn’t zoned or had 2 systems.
Of course designing the building correctly helps a lot, pity it’s rarely done in practice. Lots of West facing windows seem to be the worst offender around here…
Danny G: well said…(3200
Danny G: well said…(3200/130 there’s that exergy thing – powerful stuff).
Charles: thanks for the comments and I agree, for more on thermal bridging see
Jamie K: Thank you for your kind words and enthusiasm…hope everyone catches what you have – gotta like be ignited!
Christopher C: awesome…two best places to learn stuff…being the student and being the teacher…it’s a symbiotic relationship.
Bob: yep…along the same lines industry needs to consider that perhaps it needs to help consumers clearly understand that HVAC effects the health of the indoor environment and by association their health; their personal cash flow by consumption of utilities connnected to HVAC appliances; and through the regulation of temperature and humidity the preservation of personal assets…taking off my technical hat and putting on my PR and marketing hat I say HVAC is an undersold consumer product.
Matthew C: Thanks and yes…dog eared and coffee stained.
David B: My pleasure – your article was a great read – something everyone needs to study.
Bob, duct design &
Bob, duct design & installation quality *is* awful for the most part, which creates its own set of issues. On that point, you’re preachin’ to the choir.
We have an incredible mountain range a few miles SW of town (Huachuca range) and I bet you can guess which way most folks orient their homes when given a choice, and which direction most of the glass faces!
Also, I couldn’t agree more with your point re: fallacy of designing to 400 CFM per ton. With most air handlers and furnaces, it only takes a humidity sensing thermostat (with DH out) and an $8 relay to reduce fan speed on RH call. Variable speed models typically don’t require the extra relay.
Here in the SW, we can get away with 500 CFM/ton or higher, although the additional sensible capacity and efficiency gain will be lost as you push a blower up its power curve. I’ve never been able to find an economic rationale for more than 550. Once the coil is dry, you’re just burning blower energy.
What I’d like to see is a blower that could be programmed to operate just beyond dry coil when RH is well below the high limit, as is often the case here.
Agreed, there is no point to
Agreed, there is no point to increasing blower speed on an already dry coil. Perhaps a system like the ICM humidity controller uses to keep coil temp constant regardless of latent load would work best. I don’t see why it would be difficult to implement a RA and Coil temp sensor to maintain a constant differential, especially if you have a VS blower to begin with.
I have actually done the $8 relay trick on my own system, except I used an $10 “delay on make” ICM102 set to 7 minutes instead of a $150 thermostat that has humidity control. I’m not sure why this strategy can’t be implemented OEM on PSC systems, it’s an extra relay and delay IC.
I’m sure the $150 thermidistat would provide better control, and I’ve even considered using a standard humidistat instead of the timer. The delay timer works well, but I’m probably giving up some efficiency when latent loads are low.
For those who want to pursue
For those who want to pursue the measurement of comfort metrics for comparison against ISO and ASHRAE Standards and for identifying thermal comfort problems, the link below will take you to one provider of field instrumentation…maybe you can now add this to your blower doors and thermographic cameras [;@).
http://lumasenseinc.com/EN/products/thermal-comfort/innova-1221/
For studies in thermal comfort in the automobile industry search out http://www.mtnw-usa.com/thermalsystems/products/custom/thermal-manikin-adam.php and then ask why we don’t have such a tool for use in residential research work.
With the Manikin PC2 software
With the Manikin PC2 software, we can have a complete thermal comfort monitoring system…
http://bit.ly/Hfx2By
I need a couple of these to deploy in client homes – one on the sofa and the other on a cot beside the bed. Add a sub-load energy monitoring system and weather logger and I’d be all over my client’s comfort issues like white on rice! Or a bad rash.
Ok now that’s funny! Ya just
Ok now that’s funny! Ya just about snapped the stitches holding my abdomen together. Definitely a haha ouch moment!
Looking to build a house with
Looking to build a house with 5750 sq ft for 1st floor and basement, and 3200 sq ft for 2nd floor. The house is 89′ long (67′ excluding the garage). How many Heating/ac zones should the house be equipped with?
@Harry, there’s no way to say
@Harry, there’s no way to say without seeing the plans, but depending on climate zone and envelope specs, you might be able to get by with as few as 2 equipment zones (unlikely) or as many as 4. Either way, the ideal number of damper controlled zones within each equipment zone is very much specific to the particulars of the home. Also keep in mind that smaller systems (3 tons or less) are more efficient than 4 and 5 ton models.
You should hire an independent mechanical designer to specify your equipment. On a home that size, the stakes are too big to leave this critical detail to the hvac contractor, in which case you’re likely to spend up to 5 figures more than necessary for the wrong type of equipment, too much capacity, and end up sacrificing comfort and efficiency on top of all that. I see it all the time.
It’s not a simple
It’s not a simple answer, I can’t speak for others but my evaluations for zoning include:
Room use: rooms separated out or consolidated based on grooming, socializing, resting, storage, personal spaces such as hobby rooms or home offices etc.
Potential magnitude for heat loss and heat gains: rooms separated out or consolidated based on solar exposures, window to wall ratios, choices in external and internal shading, lighting, and appliances other equipment heat sources.
Surface treatments: rooms separated out or consolidated based on chemical, optical and thermal properties of the various surfaces. Important for evaluating source control for IAQ and in the case of radiant systems important for emissivity in heating and absorptivity in cooling systems.
Orientation to North: rooms separated out or consolidated based on similar solar loading and shading.
Proximity to Similar Spaces (see room use): separated out or consolidated based on similar functions typically; bedrooms, bathrooms/powder rooms, kitchen/dining/nook, family/living rooms, basements, garages, hobby rooms, home theater etc.
Architectural Layout: separated out or consolidated based on geometry such as height, shape, changes in planes (l shape versus rectangular etc.)
Impact from home theater equipment, lighting, fireplaces: separated out or consolidated based on contributions to internal heat gains.
A lot of the above is filtered out when budgets have been established for the enclosure, interior finishes and choice HVAC systems.
In general, the higher the performance of the enclosure, the more consistent characteristics of finishes, the greater the use of low VOC materials the less zones are required and the simpler the HVAC system will become.
So if there were a simple answer to the question it would be, “it all depends”.
…and what David said…
…and what David said…