A BTU Is A BTU…Or Is It?
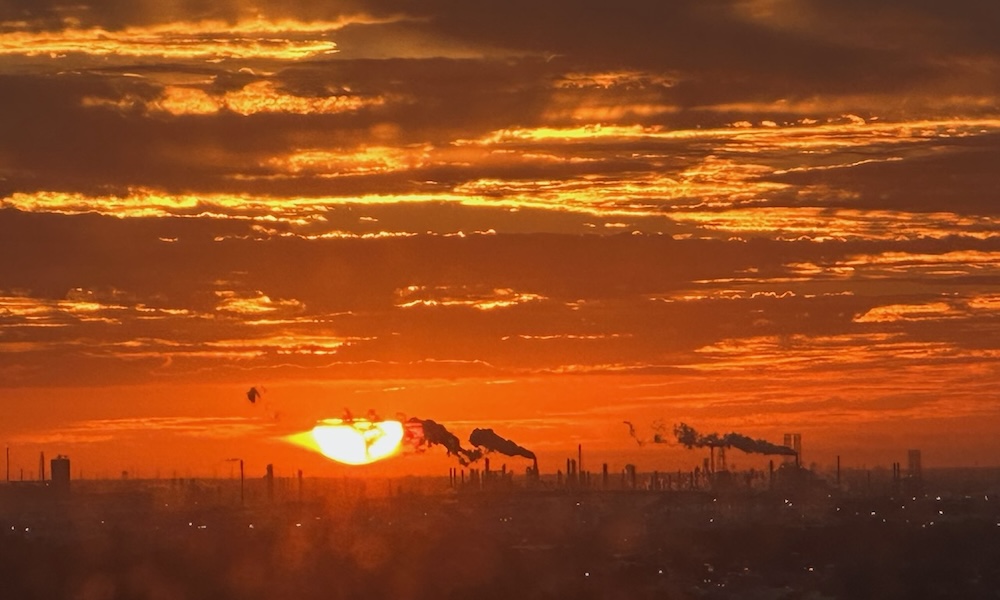
Since we’re on the topic of energy, let’s extend last week’s discussion of electric resistance heat efficiency. I’ve sometimes told people that “a BTU is a BTU.” (For the rest of the world, the conversion is simple: “A joule is a joule.”) But is that true? And what would make it not true?
Energy for heating
When I say “A BTU is a BTU,” it’s a reaction. It comes out when I hear someone say, “Oh, a heat pump just won’t heat as well as furnace.” Or sometimes it’s when they say, “You can’t heat an existing home with heat pumps.”
But the thing about heating is that it doesn’t matter where the heat comes from. If you need 6,000 BTU per hour to heat your house, it doesn’t matter whether those 6,000 BTUs come from a furnace, heat pump, woodstove, baseboard heaters, or cats.
One reason some people doubt that heat pumps are up to the task is that they confuse temperature with heat. Temperature is definitely related to heat, but they’re not the same thing. As I wrote in an article about heat pump supply air temperature, you can get just as much heat from 100 °F (38 °C) air as you can from 140 °F (60 °C) air. You just need more air if it’s being delivered at a lower temperature.
So in that sense, yeah, a BTU is a BTU and a joule is a joule.
Thermal comfort
Now, where that statement starts to break down is when you assume that delivering heat gives you the the right air temperature for comfort. Paraphrasing the great Robert Bean here, heat pumps and furnaces provide warmth. They can heat a space, but they don’t deliver thermal comfort. That, dear reader, is a more complex issue.
Comfort isn’t just about getting the right air temperature. First of all, comfort is subjective. It varies from person to person. Even for a single person, it varies from time to time. And air temperature is only one of six major factors that affect comfort as spelled out in ASHRAE’s thermal comfort standard. They are:
- Metabolic rate
- Clothing insulation
- Air temperature
- Radiant temperature
- Air speed
- Humidity
You may have the “perfect temperature” in your home and still be uncomfortable. Stand next to those big single pane windows on a sunny summer day and you may feel too hot even if the house is at 68 °F (20 °C).
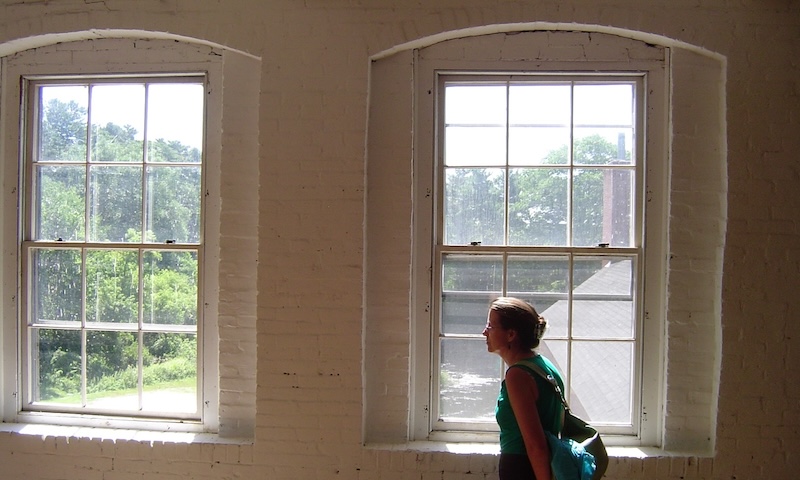
Or sit next to an uninsulated wall when it’s really cold outdoors, and you may feel a chill even with the furnace blasting. As it turns out, the temperature of the surfaces surrounding you is more important than the air temperature.

If you really want to be comfortable in your home, you need to start with the building enclosure. Make it airtight. Insulate it well. Design the locations and sizes of the windows and put overhangs above them.
In terms of thermal comfort then, a BTU is NOT a BTU. The BTUs you feel from the enclosure are more important than the ones from your heating or cooling system. That’s because most of the heat exchange between our bodies and the environment is due to radiant heat.
Indoor air quality
Your indoor air quality also may depend on the source of your heat. Using an unvented gas fireplace or space heater means all the exhaust gases from the combustion get dumped into your indoor air. At a minimum, those exhaust gases will contain water vapor and carbon dioxide. In reality, though, you’ll also get some oxides of nitrogen, soot, and, if you’re unlucky, carbon monoxide.
But it’s not all about space heating. A natural draft water heater inside the home is easily backdrafted. If it does backdraft, the exhaust gases don’t go up the flue. They spill into the indoor air. And when that happens, carbon monoxide likely gets into your air—and your lungs and your bloodstream.
Cooking with gas? Those BTUs and joules produce more indoor air pollutants than cooking with electricity. The research keeps reinforcing that conclusion.
Source energy
See last week’s article for a more complete definition of source energy, but the short version is that it’s all the energy used in delivering energy to your home. The gas, electricity, propane, and other fuels you use come at a cost. And it’s not just in dollars.
Electricity, for example, comes from burning coal or gas, running nuclear power plants, and increasingly, from wind and solar. When it comes from burning stuff, there’s a thermal penalty. The electricity we receive has only about a third of the energy that was in the fuel. That’s just thermodynamics, and there’s not a lot we can do to improve that. See my article on rejected energy.
Gas, too, has losses. There’s energy used to drill for it and deliver it through pressurized pipelines. And there are leaks in those pipelines. Gas isn’t as clean as we’ve been led to believe.
In this case too, then, a BTU is not a BTU, nor a joule a joule. Where the heat comes from matters. As I’ve said here many times over the past five years, though, electricity from the grid is getting cleaner all the time.
Thinking
I realize this is a rabbit hole that a lot of people choose not to explore. But if this kind of discussion interests you, I hope it helps clarify your thinking about energy, indoor environmental quality, comfort, and other big picture issues.
The sum and substance here is: When given a chance, choose your BTUs wisely.
Allison A. Bailes III, PhD is a speaker, writer, building science consultant, and the founder of Energy Vanguard in Decatur, Georgia. He has a doctorate in physics and is the author of a bestselling book on building science. He also writes the Energy Vanguard Blog. For more updates, you can follow Allison on LinkedIn and subscribe to Energy Vanguard’s weekly newsletter and YouTube channel.
Related Articles
Is Heat Pump Supply Air Too Cold for Heating?
The Meaning of Rejected Energy
Comments are welcome and moderated. Your comment will appear below after approval. To control spam, we close comments after one year.
A side note: It’s aggravating to find HVAC trades using the term “btu” when they “btu/h” (a rate). Worse yet: “btuh”. It has infected other areas, e.g. the nonsensical definitions commonly given for EER.
Bob: You’re speaking my language now! I HATE “btuh” most of all, but it’s also frustrating to see and hear “BTU” for “BTU/hr” and “feet” for “square feet.” It’s part of the jargon disease. You take a shortcut that insiders understand but outsiders are confused by.
But Allison, you want me to talk to my concrete guy “how many cubic yards?” He’ll respond, “you mean how many yards?”
Btw, is it my browser, or the Captcha feature is fooling around with me. It asks me to re-certify that I am not a robot every 30 seconds, while I am typing the reply… Busses, crosswalks, and motorbikes.
A domesticated cat weighs roughly 10 lbs on average which gives us 37.1 Btu/hr or 10.9 W. These figures would be doubled if the cat in question is undergoing moderate activity. (probably AHSRAE data)
Andrew: Is that 37.1 BTU/hr sensible, latent, or total heat output of a 10 pound cat?
For others interested in this topic, Manual J assumes 230 BTU/hr sensible heat for each person in a house and 200 BTU/hr latent heat. See my article on occupant loads for more:
Understanding Manual J Occupant Loads
https://www.energyvanguard.com/blog/understanding-manual-j-occupant-loads
Regarding radiant heat, this cannot be overemphasized in building a home. My current “pretty good home” is very comfortable at 64-66 in the winter and going near a wall or window or door does not change my comfort enough to notice. However, I can go into less insulated homes and buildings and feel a definite chill even though the room temperature is higher than at home.
There has been some discussion in the BS arena about using PV panels instead of insulation to mitigate heating and cooling needs, and I think there needs to be some minimum insulation and air sealing standards if, for nothing else, comfort.
Norman: I also had experience with that level of comfort in the house I built in 2001. We could keep the thermostat set at 18 °C (64 °F)* and be perfectly comfortable. The airtightness and well insulated walls made of structural insulated panels kept the mean radiant temperature much higher than in my current 1961 house, where we often set the t-stat to 72 °F (22 °C).
Thank you, Allison, this topic never gets old. Air temperature is only one of six major factors!
If we spent 2 days in school discussing this article in 5th grade, and then again in 10th grade, maybe, just maybe, we would all live more comfortably and healthier.
Paul: I like that idea! Yes, we should definitely be teaching this kind of stuff to kids in school.
Thanks Allison,
Don’t forget that a BTu in doesn’t equal a BTU out. A 75000 BTU water heater that’s 66% efficient only delivers 50000 BTUs to the water. Similarly for a furnace, right?
Tom
Tom: That’s another good point!
Great article Allison. Really like the way you break it all down to the energy needed to make you home warm and get that energy to you home. The better the enclosure is insulated, the more comfort the occupants have and less energy is needed/wasted.
Thanks, Eric!
Regarding making houses and buildings more and more airtight and efficient, 15 states are now suing HUD to fight the government’s energy efficiency standards.
The 2021 IECC’s requirements have caused a lot of issues for the builders in the six states that have adopted the code. It appears most of the other 44 states don’t want anything to do with it.
I draw up houses in Northern NJ (NJ is one of the 6 states) and the prescribed code is R-60 in the ceiling, R-30 walls, R-19 in the basement, and R-30 in the floors. And then there are sneaky additional upgrade credits, that can add another 5% of insulation. The big upgrade in R value requirement has caused most builders to switch from batt insulation to spray foam.
One of my builders just spent $50K in spray foam. It costs about 4 times what fiberglass costs. Add in the upgrade in R requirement since the previous code and the insulation costs are now up 5 fold. Plus, the review process has lengthened an extra 2 months with all of the extra required calculations and professionals involved. The builders have to sit on the properties longer before breaking ground.
I’ve performed well over 100 ResCheck calculations and it appears the extra costs for professionals, insulation, more complicated mechanical systems will never be offset by savings in energy.
Another big issue is spray foam is combustible. After watching these L.A. fires who wants to live in a combustible plastic house? The fire underwriters used to write our building codes decades ago, but they got pushed out by lobbyists. If they someday write our codes again, spray foam foam boards may get outlawed.
But another issue is new housing is becoming far too expensive for the average American.
Karl, there is a lot in your comment. How are Rescheck calculations directly dictating construction cost? Builder education is the culprit. Lack of it, and/or unwillingness to learn.
To clarify:
R-60 in ceilings is easily achieved with a bit extra blown-in. 2021 IRC actually allows R-49 if it’s continuous (N1102.2.1), and other exceptions, like R30 in vaulted if no more than 500sqft or 20% (N1102.2.2). Where is the big deal?
2021 IRC requires walls to be either: R30, R20/5, R13/10, R0/20 (where the second number is continuous insulation). This does not have to be spray foam.
Floors: R30 (starting with zone 5) isn’t anything that ground shattering, is it? Pack the 2×10 floor joists with R30 batts and you’re done.
The minor (from the overall) extra cost is in planning, a bit more insulation, extra 2×4 lumber if you insist on R30 batts or blown-in insulation in walls, otherwise R5 rigid foam, and some extra labor, but less than 5% of total cost, give or take. And it reduces your HVAC systems. And it exponentially improves the home ownership experience for people.
NAHB and states have lobbied against and complained about every single step forward in the way we build. You mention fire and codes and lobbyists. OK, what happened to single-family sprinkler requirement introduced in IRC around 2010? Most state codes succumbed to NAHB lobby and removed it. Because of $700 extra cost per house (at the time).
I’ve been bombarded by ads that address 4. The heat pump or furnace is a convection air heater. The “radiator” is generally 80-90% convector and 10-20% radiator. Radiant flooring companies claim that they offer about 70% radiant heat. Some infrared panel heaters claim to be 99% efficient at warming you. Is the cost of such systems in climates where we already need forced air cooling the only reason they aren’t regularly found in southeastern homes? The only other disadvantage I can name is the directional nature of radiant heaters. I can stand outside at 50 F on a sunny day and still be comfortable.
Stacy, to your question about cost being in the way of dual systems in the SE: yes.
And you kind of answered your other comments with the 50F sunny day example. You can be comfortable outside, because you’re standing in the sun with no wind: mostly radiant.
Btw, forgot to mention, there seems to be a possible good alternative to continuous foam board.
There’s a company out in Pittsburgh that created a 1/4″ thick house wrap, Insultex, that has an R-6 value. I called out there today and the tech guy said the product gets the significant R value because the encapsulated bubbles are vacuums (no air).
It appears I can get one of my jobs to work with mineral wool and with an R-6 continuous insulation. But I have to get the building official to okay it.
Karl, the 1.5mm (that’s what the product spec is) thick house wrap with R-6? Snake oil. I hope you don’t fall for it.
Yep, Insultex is most likely a scam. There is no way they could put a vacuum in those bubbles, let alone maintain it. The Federal Trade Commission has pointed out their false claims:
https://www.ftc.gov/news-events/news/press-releases/2016/11/ftc-charges-purported-insulated-house-wrap-marketer-making-false-claims
If it sounds too good to be true, it probably is.
I did some additional research and found out that the FTC false claim charges against Insultex were thrown out in court. I still don’t believe their claim of R6 based on my knowledge of fundamental heat transfer. Even if you can contain the vacuum bubbles, you still have to block radiation through the bubbles and conduction through the walls of the material that is containing the bubbles.
Roy, yeah, 1mm of bubbles + 0.5mm of fibrous layer does not provide R-6, not on this planet. It’s unfortunate that FTC botched their case.
The manufacturer says it’s “translucent”, “water vapor barrier”, “moisture vapor-protective but breathable”, “no air-gap required”, all on the same website. No perm rating is given. I could not find an ICC-ES report.
Paul,
Regardless whether this product works or not, the overall energy savings on houses for the upgrade from the 2015 IECC to the 2021 IECC is neglible. NJ skipped the adoption of the 2018 and 2012 codes.
Builders didn’t have to use continuous insulation (or spray foam) for the 2015 code, but for 2021 they do. The energy savings for the 2021 code don’t come close to offsetting the extra costs of installing the upgrades, plus the extra design fees and inspections.
My own house (2,300 s.f.) meets the 2015, though I built it in 1996. NJ had a special geothermal rebate package back then for geothermal which I opted for and had some upgrades they required. I plugged in my house data into ResCheck for both 2015 and 2021 and though I meet the 2015 requirement, I fail 2021 by 13%. I would save 13% of energy costs if my house was set up 2021. My annual electricity for heat and a/c is about $1,500. 13% of $1,500 is $195. R-5 zip board for my house (lets say I was building it today) would cost me about $6,000. Plus there’s the cost of the required make-up air, extra costs for extra ceiling insulation, and probably extra costs for installing windows and siding over the foam board. Plus there’s an enhancement you have to choose for new houses for the 2021 code. My builders typically choose the 5% extra insulation- keep in mind that 5% applies to all assemblies which include windows.
The 2024 code gets really bizarre-(ResCheck already has the software for it). It has 10 required enhancements on top of the prescribed insulation and U-value for windows. ResCheck lists 48 possible enhancements- some for insulation, some for air tightness, HVAC, hot water heaters, and misc. You can fulfill 7 enhancements by upgrading the insulation assemblies by 30%. Once again that includes windows.
I plugged my house data into this and the 30% of extra insulation plus increased efficiency of the windows (probably triple pane) would save me another 2% of energy costs each year or just a mere $30. It appears all of these extra enhancements will create work for MEPs and other lobbying groups. It’s way out of control and the American people won’t be able to afford new houses.
Karl, my advice, if you insist on using “Insultex”, treat it as a WRB only, but only after verifying a reliable perm rating with the manufacturer.
Regarding Rescheck, it’s a very simplistic tool used for permitting compliance. It may also give you a very rough overall picture of your thermal performance, but it’s not a simulation tool by any stretch. For example, it misses air infiltration completely (other than having a constant for it). Relating differences in Rescheck UA scores to energy savings for one house vs. another is really like saying that this apple is 50g lighter than that orange and therefore is less healthy for you.
Btw, Zip R sheathing comes in R-3 and R-6 (also R-9 and R-12, but they give my P.E. headaches because of the amount of separation), and foam board is on the interior side of sheathing, so your door and window installation is more or less unchanged.
Making houses tighter and adding make up air mechanisms is ultimately to our advantage: health and comfort. How much is your health insurance premium these days?
New home affordability has a single digit per cent (<5%) correlation with builder energy improvement expenditures (a short-term cost factor), and anywhere between 30-50%+ correlation with market factors (exuberance, location, perception, etc), and the rest is fixed cost. Karl, nice try, but energy improvements are not the affordability busters.
Regarding MEP groups lobbying for more work, interesting, but not very logical. Builders, like myself, want good, but reasonable MEP subs and equipment, why would they lobby themselves out of work? They have enough headaches dealing with new refrigerants, for example. Not that change isn't necessary. You change, or you're left behind. The only thing constant is that a BTU is a BTU. (my feeble attempt at bringing this conversation back to the context of Allison's post)
In my experience, there is a learning/improving/enhancing/embracing way of growing in construction, and there is resisting/insisting/blaming/complaining way of "existing" in construction. I've seen both. Ultimately homes are our castles however small or modest. Throughout the modern era they've been known to keep us safe, but also to make us sick. It's crystal clear to me which way contributes to which outcome, and I am very grateful for Allison providing a platform where the former rather than the latter is shining.
Hey Stacy…it’s unfortunate to be on the receiving end of BS… if any floor heating vendor says they can get 70% radiant off their floors I’d be happy to take them to task. I am one of the co-authors of the ASHRAE handbook chapters that address radiant heating and cooling and there is nothing in these chapters that support what they’re claiming …what we do state is that any surface that contributes 50% or more of its heat via radiation is considered a radiant surface. There are empirical heat transfer coefficient which tell the practitioner how much energy is delivered via radiation and how much is via convection. Those heat transfer coefficient are dependent on the orientation of the panel and whether they’re in the heating or cooling mode. For floor heating systems it’s about a 50-50 split.
Robert,
I’m not sure what Stacy is referring to but my 40 years of extensive empirical research and experimentation, have taught me that the actual instantaneous output of radiant “panels” is a complex interplay of a number factors. This isn’t saying much, but still intuitively more difficult for many to understand than hot air blowing out of a hole in floor.
The 50/50 rule of thumb for radiant floors rings true but even it ignores the necessary direct contact of the occupants with the floor which may comprise the larger fraction of the comfort provided regardless of the thermal condition of the space otherwise.
The output of a radiant ceiling in a heating mode is typically greater that 50% radiation in that the convective component is curtailed by the orientation. In cooling, however, the convective component is recovered and the output by radiation will be balanced by the output from convection.
How the panel is loaded also makes a significant difference in a panels response. A radiant panel in front of glass receiving solar gains, for example, will have high radiant fractions of the output in both heating and cooling applications.
We might size a radiant panel for indoor heating to provide ~ 25 btu/ft2. If we take the same radiant panel area outside and dump snow on it and send it through a couple of phase changes it can put up >125 btu/ft2. (the design of the “panel” accommodates the increased flow necessary)
Hey Dale,
Re: I’m not sure what Stacy is referring
Her statement…”Radiant flooring companies claim that they offer about 70% radiant heat.”
Re: “complex interplay of a number factors.”
Yes, and these are also discussed in various chapters of the ASHRAE Handbooks.
Re; “difficult for many to understand than hot air blowing out of a hole in floor.”
Yes, which is unfortunate. Understanding electromagnetic energy, radiant energy transfer, and conversion to and from heat is missing in many practitioners’ skill sets. Those with the knowledge operate at a different level of understanding, especially regarding thermal comfort.
Re: The 50/50 rule of thumb for radiant floors
The rule is frequently used in dialogues to expedite the conversation. More precision is afforded through the formulas and graphs published in the ASHRAE Handbooks. As mentioned above, discussing it with others who have yet to understand is akin to putting 10 gallons of water in a 5-gallon jug. It requires those raised on air-only systems to empty a bias to make room for one of the greatest foundations of energy transfer.
Re: ignores the necessary direct contact of the occupants with the floor
Yes, but readers should know it is not by error or omission. The heat transfer coefficients for designing the system ignore the occupant deliberately, addressing only the exchange between the conditioned and unconditioned surfaces. Conduction kicks in when people are introduced and depends on the footwear and contact coefficient of the flooring type. Including the occupant would be to treat it as a migrating heat source of variable output; frankly, that becomes an academic exercise IMNSHO [:@).
Re: which may comprise the larger fraction of the comfort
It would be circumstantial. ASHRAE 55 requires analysis of floor temperatures when occupants have less than 1.3 met rates (reading) and 0.7 clo values (lounge wear). So yes, there will be times when conduction will be a local factor that could dominate the general factors. Thus, the reason why people at 72F/22C complain about cold floors when they’re lightly clothed and just hanging around the house – literally chillin’.
Q. How many practitioners do this evaluation?
A. less than 1.5%.
Re: The output of a radiant ceiling in a heating mode is typically greater
Yes. That is why I stated it depends on the mode and orientation of the panel. Radiant dominates (i.e. >75%) in the ceiling heating and floor cooling modes due to the partial disabling of convection. But does not approach 70% in the floor heating, which is what Stacy has been told.
Re: A radiant panel in front of glass receiving solar gains, for example, will have high radiant fractions
Yes, due to both the short and long-wave electromagnetic energy. This is why, in cooling, the thermal-optical properties of interior finishes should be strategically optimized for absorption/conduction rather than reflection. I’ll say it again for the general audience…the interior designer is our friend in HVAC…never ignore their influence on IEQ and energy efficiency.
Also, all of this ignores the operational or dynamic characteristics of how different btu delivery methods vary.
Forced air systems working by filling a room with hot air and spend their entire operating time accelerating the air to reach a lost air temperature set point. Once this setting is achieved, they turn off. Because there is very little thermal mass in the air, heat is lost quickly and the acceleration cycle repeats. Such an air system spends all of it’s time “catching up”.
A radiant floor necessarily heats the mass of the flooring system before heat, aka kinetically agitated atoms and molecules, can be moved into the air or other surrounding surfaces. Introducing this capacitance profoundly changes the instantaneous load that the equipment and the room sees and acts to lengthen the duration of the heat delivery on and off cycles as the building is being heated and not just the air in the building.
Most of the operational time is spent at a steady state condition and very little time is spent accelerating as the mass of the building itself is not allowed to go cold. The actual air temperature becomes almost superfluous to comfort.
Well said Dale…”Most of the operational time is spent at a steady state condition and very little time is spent accelerating as the mass of the building itself is not allowed to go cold. The actual air temperature becomes almost superfluous to comfort.”
and unlike f/a where the motive air temperature is driven at the air handlers exchanger…sans solar gains… with radiant the air temperature will never exceed the temperature of the heated surface…we’re talking 10F max… with F/A the differential between the supply air and MRT could be at best 20F and at worst over 60F… this difference defines the nearly zero stratification with radiant vs almost guaranteed stratification with F/A… caveats on high performance enclosures and buildings in warmer climates….
To translate all this, comfort comes from a building and its enclosure that is capable of maintaining a Mean Radiant Temperature without moving much air, to the desperation of many HVAC mechanics who want to throw their systems at the problem.
I would not discount air’s volumetric heat capacity as “very little” just yet. Take a room 10mx10mx3m with interior walls covered in sheetrock. The volumetric heat capacity of 1/2″ sheetrock in this room is about 2,230 kJ/m3 K. The air in this room has a volumetric heat capacity of about 360 kJ/m3 K, a little over 6x less than the sheetrock, but not negligible.
Yes, you are right about the sheet rock adding some mass. However, in an air system, the sheet rock is not directly heated, and typically sit below room air temperature; making their actual contribution to the thermal time constant of the room negligible.
A radiant floor can also thermally invoke those surfaces by radiation, in way that simply holding the air temperature in a room constant cannot.
This is how radiant floors offset the heat loss from windows or from any surface colder to the floor. No medium for heat transfer is needed and heat is transferred between surfaces at a rate relative to the 4th power of the temperature difference.
Dale, my point wasn’t as much about sheetrock adding mass, although it does and for a typical light frame house sheetrock is the first to participate in majority of heat transfer (all modes). It was that air’s participation in this game isn’t negligible.
I understand and would love radiant heat everywhere. I would prefer those radiant BTUs vs forced air BTUs (in keeping with the blog’s theme). Anywhere between zones 2-5 it’s not that easy, however. Not in retrofits, and not in new construction. I don’t like it, but I need to choose my battles on the path to optimal housing, and we’ve had enough resistance over the last 30+ years in making envelopes better performing.
Radiant floors aren’t without considerations. Homes are messy. A living room isn’t necessarily a perfect lab box, an isolated physical system. There is a rug on the floor. There is a couch or two and a coffee table. Suddenly the radiant floor isn’t invoking all the cold surfaces in the way we wanted it to invoke.
Radiant systems, in my view, make the most sense with a great external envelope, where conduction is slow, air leaks effectively non-existent, and thus a slow response is just fine. Envelope is where I want to improve our housing first. That has proven to not be as simple as we thought. And there is plenty to talk about radiant gains or losses around the envelope if you’re itching to plug in that 4th power of ΔT.
Hello Paul,
Thank you for the on point comments.
However…with respect,
– I’m speaking of what is now popularly known as “Thermally Active Building Surfaces”.
In this sense, any solid surface that is not thermally “active” represents a potential thermal liability. In a F/A system, only the air is thermally active and it is only superficially and temporarily “active”.
Since air is a fluid and not a solid, any heat in it is subject to the vagaries of convective heat transfer including mixing, stratification etc. Heat that is in the air is very poorly coupled to the other room surfaces, furnishings or furniture. In a F/A heating system all surface temperatures are below the air temperature, especially at the floor.
By way of contrast, an “thermally active” surface is directly heated or cooled and doesn’t participate in the envelope losses even if it’s part of the envelope as in ceilings and floors. We calculate gains and back-losses from a radiant floor but the floor does not contribute to net losses from the envelope as it does in a F/A system.
Heating these otherwise solid “surfaces” directly does invoke their mass and if that mass is as large an area of as the floor, then we have profoundly affected the thermal constant or rate of gain and decay of thermal comfort in an otherwise lightweight and thermally inactive envelope. Also, the heated floor does heat rugs, furniture etc. in a way that cannot be done by periodically blowing hot air at them. Whether parts of the room are shaded from the floor or not is somewhat unimportant to Mean Radiant Temperature.
-To be overly concerned with the speed of “response” is to miss the point which is that there is no need to “respond” rapidly to some internal change in comfort because there is no rapid change in comfort…or thermostat settings for that matter.
With reset water temperature control heat can be delivered at the same rate that it is being lost by circulating water at the “Goldilocks Temperature”
At this is heat delivery rate air temperatures don’t drift off thermostat set-point.
Keep up rather than catch up.
Thank you.
“Goldilocks temperature”: 78 for me in the summer, 74 for my kids, which to me feels like close to freezing.
We’ve been hearing about radiant cooling for a couple of decades now, at least. Not that easy to do here in the SE. What I’ve been planning to do for a while now is to visit the Kendida building on GaTech’s campus. I’ll wait for a day in the 90’s with dew point hovering around 70.
Paul and Dale,
If you’re interested, CBE maintains a database of radiant-cooled buildings from around the world including TAB’s…
Paul, ASHRAE’s Headquarters in Atlanta are radiant-cooled…you can read about the building here:
Good discussion,
RB
Those interested should check out AirFloor systems.
https://www.airfloor.com/
I actually installed this very system in Bozeman in the late ’80’s. I’m amazed they are still around! Robert should like this.
The Airfloor is a 1 ft2 sheet metal concrete form that is shaped in such a way as to provide `3.5″ arched openings in the 4 sides. The corners are turned down in such a way as to allow the concrete poured over the top to form structural pillars at each corner. The 1 ft2 forms are assembled on top of a 2″ subslab.
The system is designed to allow warm or cooled air to circulate through the concrete floor.
In the system we did, we put wire mesh on top of the airfloor forms and wired polybutylene tubing to it. We heated the slab hydronically and used the the airfloor to distribute ventilation in a large slab on grade super/duper insulated building.
https://www.airfloor.com/
Robert, thank you.
Dale, why go into all the trouble and expense installing the slab airflow grid system you described with hydronic heat on top? Pushing ventilation air through all that? Also, sorry about the PB tubing…
I would like my ventilation air to be delivered quickly, through known conduits that are as inert and as short as possible, as opposed to a random path on top of an unfinished sub-slab where cracks, particle accumulation, moisture, rust, possible soil gases, insects, and mold may interfere.
The floor system you reference triggers several questions: how do you ensure that the slab air channels stay dry, mold-free, don’t rust, don’t introduce soil gases? How do you handle the slab perimeter zone in a cold or hot climate? We wanted to escape from forced air and yet here it is. How would you ever clean or replace this system?
Sorry, but the idea and execution in the case of Airfloor seems to me like another enterprise focused more on finding new ways of selling old bulk materials (steel, concrete) than on delivering a solution that doesn’t make the building occupants sick under the right circumstances. After reviewing the guides and white papers posted on the site my snake oil indicator started to jitter.
Hello Paul,
Your attitude is typical of an HVAC industry that historically doesn’t even recognize the need to ventilate buildings at all. I did this project before there were such things as HRV’s and ERV’s.
Even today, Mickey Mouse* methods are employed by those who should know better to avoid putting dedicated ventilation systems into buildings and ventilating to standard.
I originally used the Airfloor system in a couple of passive solar greenhouse we built, as a means of capturing solar gains. The tubing is there for backup hydronic heat.
Though Polybutylene doesn’t have an oxygen barrier, I have not had any problems with the few systems that we still have in the field, we switched to PEX with 02 barriers as soon as Tomas Lenman brought it into country.
The problems that PB tubing had with fresh water systems was in the poly-acetal fittings that were subject to chlorine in the drinking water. We used brass fittings in closed loop heating systems….very different thing.
My Company designs hydronic heating and ventilation systems and distributes hardware. I did this project decades ago now but it’s still there operating.
If you have issues with the AirFloor company or the TABS concept I suggest you take them up with ASHRAE and the AirFloor people who appear to be quite successful with the concept and the LEEDs certified product. I doubt very much that anyone is trying to deceive you.
My only goal here is continuing education; for myself and others.
Unfortunately as Robert said above, education regarding radiant heating/cooling systems “requires those raised on air-only systems to empty a bias to make room for one of the greatest foundations of energy transfer”.
T’was always thus.
*No offense to Mickey
Thanks for the article Allison. Yes, people confuse temperature with heat and with energy. One of the confusing things about radiant heating and cooling is that the panels actually work at surface temperatures just above or just below “room temperature”.
How do I hire Vanguard to help with some design work?
Dale
ResCheck calculations give builders flexibility. More often than not, there will be assemblies that I can’t meet the prescribed code, so ResCheck allows me to shortchange insulation in some assemblies if I upgrade elsewhere.
Regarding that R-30 you mentioned for sloping rafters- that can only work if I upgrade the rafters to 2″x 12″s unless I opt away from batt insulation. Batt insulation in rafters require air baffles per code. And if you cram in R-30 with an air baffle in a 2″x 10″ rafter, you’ll lose R value.
As for the R-60 that you suggest blowing in insulation on top, that won’t work in our market. People want plywood flooring in their attics, and most houses I draw up have “finished” habitable attics. The concealed spaces behind the half walls are usually where the ductwork is installed.
As for this R-5 continuous insulation foam board, most builders don’t like it for either the siding overhangs the foundation by a couple of inches or they lose space by setting the walls in. Applying siding and installing windows become a problem. Window flanges get nailed through the foam board as does the siding- not a good application. I realize the salespeople say it’s not a problem, but they’re salespeople.
Googling per square foot prices for residential sprinklers and I find “$1.35 to $2.50.” With the average new house size around 2,350 s.f., you’ll be paying $3K to $5K.
Btw, here’s a link to IECC adoption per state.
https://www.energycodes.gov/state-portal
It appears 8 states have adopted the 2021 code.
Karl, R-30c works just fine in 2×10 rafters. Look it up! (Include the letter “c” in the spec when searching.) It’s a higher density version of the R-30 batt, only 8 1/4″ deep, so no need for 2x12s. R-30c has been around for 30 years, maybe longer. Similarly, R-38c batts for 2x12s.
OK, but earlier you said your builders were spending $50k in spray foam per house to comply. Now you are saying you’ve been wiggling out a compromise using the UA alternative with Rescheck. Which one is it?
About adding R-5 rigid foam board. It’s one-inch thick, not two. There are plenty of details out there on how to incorporate it into your outside envelope. Setting exterior walls in by 1 inch, or the foundation wall out by 1 inch isn’t the end of the world, right?
About sprinkler systems: multipurpose (using the home’s cold water supply lines) in new construction will cost less than $1 per sq.ft. today, but your plumber needs to be certified. There are sprinkler heads with pex fittings on them. So pass the $2-3k on to the buyer, and they will recoup it in the first 4-5 years on their home insurance.
Paul,
Regarding using “Insultex” as a insulation, I’ll leave the decision to my builders.
ResCheck is a guide and it’s based on the IECC. It may not be 100% accurate, but what is? Even Simpson Strongtie is still building wind tunnels to test their products. Their capacity numbers on their products aren’t necessarily 100% spot on.
Your PE is certifying buildings with the zip board on the inside of sheathing??? There are approximately 30 pages in the code devoted to wall bracing and it’s doubtful most building officials would accept this application. The sheathing is what gives walls’ their bracing strength.
Making houses more air-tight may add to comfort if designed, installed, and maintained properly but does not add to health advantage. Fresh air is usually best unless you live in smoky/ smoky areas. That’s funny- I was at a LEED seminar and the presenter tested carbon dioxide in front of us and it was 1,000 ppm to his surprise- it was in a newer government building.
“Energy improvements are not the affordability busters”. Everything adds up and energy improvements do add into lack of affordability. Btw, why don’t people have a choice? If you want all of these extra bells and whistles for your own house, go for it, knock yourself out.
“You change, or your left behind.” Exactly. 15 states are suing HUD, pushing back against the 2021 IECC requirements. Most states, builders, and other professionals are unaware of the requirements. As more find out there will be even more push back. There’s an ICC committee of 7 that meet in KC and they have to deal with constant lobbying pressure.
And once again, why aren’t people being given a choice?
Karl, Rescheck is a compliance verification tool, not an energy modeling tool.
Zip R sheathing is a version of Zip System structural sheathing with attached polyisocyanurate rigid foam board on the interior side. You can become familiar with it here: https://www.huberwood.com/uploads/documents/technical/Installation-Manual-ZIP-System-R-sheathing-Wall.pdf (see page 6 for general description)
The 1000ppm CO2 level that the LEED presenter tested in front of the seminar audience you attended was the result of the audience being there.
About ICC code development process, here is a simple illustration that might affect what you know: https://www.iccsafe.org/wp-content/uploads/ICC-CDP-By-the-Numbers-2019.pdf
As always there is a balance point on insulation, once you exceed that there is a distinct diminished return on investment, where additional insulation makes little sense in additional cost/benefit whether its greenhouse gas reduction used during lifespan of building, or the energy expended to accomplish the extra insulation (governing bodies are not very good at math, they just like jumping on bandwagons). There is an interesting study done by UC Davis/Western cooling Efficiency center, that talks about various home systems and the greenhouse gas reduction. Google “analysis of greenhouse gas emissions from residential heating technologies in the USA”. I opted to not go with geothermal for my new system install because I live too far south in the USA, and I would end up “heat soaking my geothermal field” and have to replace my entire system in less than 10 years (and unless you have the land to relocate an entire geothermal field your sunk). The geothermal system is also subject to a balance point that requires that the btuh injected into the geothermal field during the course of a year, is equal to the btuh extracted during the course of the year, in colder climates this can be offset by cheap auxiliary heat systems, in hotter climates you may need an expensive cooling tower. Bear in mind that the heat injected to the geothermal field in the summer is about 25% more than the homes yearly cooling load, and the heat extracted from the geothermal field is about 25% less than the homes heating yearly heating load, due to compressor heat input plus the pump power btuh input.
Yes, that’s a nice way to put it Paul…it could also be said that radiant is a marathon solution, f/a is a sprinting solution…a proverbial thermal manifestation of the tortoise and hare parable…except the under the hood of the tortoise is a 4th power supercharger with instantaneous characteristics [:@)
Thank you for the recognition Robert, your input helps me sound less crazy.
Regarding input by direct conduction comprising the larger fraction of the comfort.
You said “It would be circumstantial. ASHRAE 55 requires analysis of floor temperatures when occupants have less than 1.3 met rates (reading) and 0.7 clo values (lounge wear)”
I think several things,
-those circumstances would likely prevail anytime your feet are on the floor, 😉
but also in any real lived in home; but less so in a commercial situation.
– If the floor is warm then occupants will gravitate to it and the floor itself can remain un-insulated. Hardwood and tile and other easily cleanable surfaces become desirable and welcoming, instead of cold and unforgiving. Probably all bathroom tile or stone floors especially in hotel rooms should be made warm by law.
If the floor is cold it becomes a net liability regardless of the air temperature. Cold floors will get insulated by foam backed carpeting + 1/4″ of dead dust mites so the occupant doesn’t feel the floor through their bunny slippers.
You also said, “f/a where the motive air temperature is driven at the air handlers exchanger…sans solar gains… with radiant the air temperature will never exceed the temperature of the heated surface…we’re talking 10F max… with F/A the differential between the supply air and MRT could be at best 20F and at worst over 60F… this difference defines the nearly zero stratification with radiant vs almost guaranteed stratification with F/A… caveats on high performance enclosures and buildings in warmer climates….”
Yes, it’s easy to imagine and probably to demonstrate how hot a ceiling might get under an attic with a roof receiving high solar gains. Even though the attic is insulated, that is just a matter of rate. What is the resultant temperature of ceiling surface and how does that contribute to the “cool” load. And if the reason for the load and the loss of comfort is high MRT, how does blowing cold air around help?
We might imagine how a water laden ceiling held just below desired room temperature might provide all the comfort one needs without blowing any air around at all.
What I posted below is apparently a foreword to an abstract or a book
THERMALLY ACTIVE SURFACES IN ARCHITECTURE: 2008
RFP & 2009 UPJOHN RESEARCH GRANTS
https://www.brikbase.org/sites/default/files/aiab092630.pdf
by
Kiel Moe
Northeastern University
School of Architecture
I’m posting it here as it describes TABS building and HVAC design using radiant heating and cooling and DOAS systems.
This quote below is expresses it well.
2009 Upjohn Research Grants have significantly accelerated the research and production of the first book manuscript on the topic of Thermally Active Surfaces in Architecture. The intent of this book is to document the basis and efficacy of heating, cooling, and building with thermally active surfaces. In this transformation of energy and building practices, the thermal conditioning of a building is decoupled from the ventilation system by using the mass of the building itself as the thermal system; a paradigm of water, rather than air, as the primary medium of heat channeling and transfer. This method of heat transfer is physiologically and thermodynamically optimal. It also reinvests the fabric of the building itself with a more a poignant role: the structure is also the primary mechanical system. As the basis of energy and construction strategies, it yields a cascading set of advantages for the building design and construction industry: radically lower energy consumption, more durable buildings, more healthy buildings, and more integrated building systems and design teams (Figure1). An important aspect of thermally active surfaces is that they are low-tech yet high performance and are thus equally applicable in the developed and developing worlds. As such, thermally active surfaces are central to multiple aspects of sustainability.