A Simple, Inexpensive Way to Better Airtightness
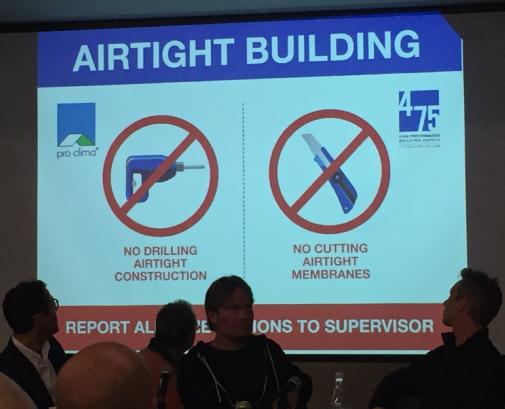
Airtightness. It’s one of the key components of a house that’s built well. We know that it’s a myth that houses need to breathe. We know it’s one of the surest ways to reduce energy bills. We know it’s a starting point for achieving good indoor air quality. Yet it can be difficult to achieve when you’re building a new home.
Airtightness. It’s one of the key components of a house that’s built well. We know that it’s a myth that houses need to breathe. We know it’s one of the surest ways to reduce energy bills. We know it’s a starting point for achieving good indoor air quality. Yet it can be difficult to achieve when you’re building a new home.
Why? Because a lot of different trades come in and do their jobs. All of them wear blinders. “Hey, I’m just the plumber. I don’t deal with that energy stuff.” Substitute painter, framer, insulator, electrician, cable guy, and all of the other trades for plumber in that sentence, and you start to realize how difficult it can be to get everyone on board.
But what if you could get them them all — or even a significant number — to pause a minute before they drill a hole or cut a membrane that might be part of the air barrier? How could you do that?
Last night I attended the Passivhaus Maine panel discussion in Portland. The topic was making Passive House affordable, and I saw something simple and inexpensive and elegant that’s working for some builders. Diane Schless of Horizon Maine showed the sign below and said she’s seeing it on some of the jobsite where she’s called in to do the verification work as a PHIUS+ rater.
Put enough of them around a jobsite and people working there will start to think whenever they pick up a drill or a saw or a box knife. Is it OK to cut here? Or is this part of the no-cut zone?
Have you seen anything like this in use? Have you tried it? Has it worked? I don’t have any data, but Diane said it’s helping on the jobs she’s been involved with. What do you say?
Link to the sign image at 475: Airtight Building Sign
Related Articles
The One Thing I’d Love to See Building Enclosure Workers Do
Structural Insulated Panels — An Easier Way to Build an Airtight Home
I Blew a Gasket — Air Leakage at Electrical Switches and Outlets
NOTE: Comments are moderated. Your comment will not appear below until approved.
This Post Has 16 Comments
Comments are closed.
Great idea, Allison. Need a
Great idea, Allison. Need a source for the signs. Pass them around to builders that I work with.
Paul, I just added a link to
Paul, I just added a link to the sign image file at the 475 website. You’ll find it at the bottom of the article.
Hello I am currently working
Hello I am currently working at a big house and we are trying to figure out which insulation is best open cell in the roof rafters we were told by someone that will create moisture between the roof tiles and the foam insulation and eventually the plywood with roth what do you think about that? thank you
Elias, I wrote about this
Elias, I wrote about this topic last year. See my article:
Will Open-Cell Spray Foam Insulation Really Rot Your Roof?
http://energyvanguard.com/blog-building-science-HERS-BPI/bid/75042/Will-Open-Cell-Spray-Foam-Insulation-Really-Rot-Your-Roof
A picture is worth a 1000
A picture is worth a 1000 words, that slide posted at job sites would help, but won’t cut it! Many people do not read, but do what they are use to, or taught. most need hands on training. I can not believe how many remodeled homes have exposed Kraft paper, with printed warnings! “WARNING do not leave exposed flammable”
You’re absolutely right,
You’re absolutely right, Dennis. Posting these signs and that’s all likely wouldn’t get you very far. You’d have to make sure that everyone who comes to the jobsite understands the goals of the project and then follow that up with enforcement. Once you get that far, then the signs take on a life of their own. When a worker comes to a new site and sees one, they’ll say, “Oh, it’s another one of those houses.” They might groan, but they’ll do it if they know it’s expected.
Being more of a construction
Being more of a construction oriented guy I like your article but it falls a little short. I was expecting more. It’s fine to put a sign that says “No drilling” but you still have to drill holes. Pipes and wires don’t magically make their way through materials. Holes are a part of building a house. The key (and where I wish your article would have gone) is how those holes are handled. We have a rule. You make the hole – You patch the hole. Yes, you do have to train the trades and get them to understand what they are doing and how it affects the big picture.
All great points, Dave. Holes
All great points, Dave. Holes do need to be drilled, and the way I read the signs—and the way I’d use them were I a builder—is that no holes get drilled or cut unless and until there’s a plan in place for how to deal with them. This also goes back to the design phase because far too many homes get holes cut through the building enclosure even after the cladding is installed, thus compromising the rain control layer (drainage plane).
I’ve been a proponent of the trades owning their holes for a long time, but this takes it to the next level. They only own the hole after they know how it’s supposed to be detailed.
Thanks for the comment, Dave!
Has anyone come up with a
Has anyone come up with a code approved way of getting rid of plumbing vents? I saw a program where they were using a one way air valve to vent the plumbing of an island kitchen sink.
I hate poking holes through the roof for plumbing vents.
Sean, I believe you are
Sean, I believe you are talking about an air admittance valve or Studor Vent. Here’s a link to images: https://www.google.com/search?q=studor+vent&tbm=isch&tbo=u&source=univ&sa=X&ved=0CFUQsARqFQoTCKS0jYzwjckCFYYyiAodAwkNYA&biw=900&bih=417&dpr=1.5
I’ve installed these in kitchen islands too. Be sure to check with your local building department because some jurisdictions do not allow these.
Or, you could spray foam to
Or, you could spray foam to perfectly seal and insulate after everyone’s done drilling and cutting. This topic reminds us that a house or building is a series of systems (framing, plumbing, electrical, etc.) and most air leakage occurs where systems come together. Perhaps someday, we’ll 3-D print our homes, but until then spray foam is the best material to air seal and insulate high performance homes and buildings.
Mac, you are absolutely right
Mac, you are absolutely right, in my opinion, about spray foam and air sealing. What I have found in my inspections are holes in the sheathing that allow the foam to touch the back of the house wrap, sometimes distending it. A big 6 x 6 hole punched through the gable for the crane straps has often been filled with spray foam. I don’t think that the foam should be backed only by house wrap for drainage plane requirements. The house may be air-tight, but over time the house wrap alone may fail, abrading against the edges of the roughly punched hole, allowing moisture to be in touch with the foam. Not a good scenario, but I don’t have statistics to prove it (yet). Today’s framers might not agree with me, but we never did that “back in the day”. Pure laziness.
Mac, Walt, Allison – we also
Mac, Walt, Allison – we also encourage builders to consider airtight gaskets and tape as an alternative to foam: https://foursevenfive.com/product-category/air-sealing-system/duct-pipe-airsealing/. Pro Clima’s Tescon Vana is aged tested to 100 years, so it helps reduce the risk of failure and moisture issues. https://foursevenfive.com/what-we-mean-by-permanently-airtight/
Some more on penetration airsealing from our Question of the Week series, including a video of a walkthrough by Habitat Humanity of Washington DC, showing how they like to take care of penetrations: https://foursevenfive.com/question-of-the-week-aug-28-2015/
Allison, I’d like some signs
Allison, I’d like some signs just to start conversations with! “Could this ever happen? What would it take before a sign like this had a real effect?” But sadly I note the link is broken as of 20:20 EST on 13 Nov 2015.
Allison, thanks for the post
Allison, thanks for the post and link.
Signs work well in most projects. Unfortunately our website did go down last night, it should be back up soon, we are working on it.
I’ve owned an 1100 SF Bedford
I’ve owned an 1100 SF Bedford stone ranch w/full unfinished basement,built in the late 50’s, for 15 years. Its currently very energy efficienct, but it can definitely be improved.I have a few questions if someone has the time or inclination to be of assistance. Any comments are greatly appreciated!
1. I replaced all of the aluminum windows w/triple pane vinyl. How often should those be recalled? I don’t know how to determine this.
2. The breaker box is not original to the home, but the house desparately needs rewiring so I’ll be replacing that also. The existing wires have been spliced and taped to create outlets over the years. There are for three-pronged outlets in the home; all others are two pronged and installed upside down(?). Would this job be best handled by a master electrician? If so, does anyone have a cost estimate? I’m in Louisville, KY.
3. I covered the external attic fan while I was stapling 8 mm plastic sheeting over a leaky area in my roof. Last year I covered its internal vents with a flexible ~1/8″ baffle. I’m planning to do so again this year. Since I rarely use the fan, would it be logical to remove it when the roof is repaired?
4. Last and most important question. The walls are plaster, with a 7′ ceiling. I’m sure that’s part of the reason for its energy efficiency, but I’d prefer to rip out the ceilings and have them vaulted in each room for aesthetic reasons (and resale!) Would this be worth the cost? I would insulate with R38 batt and then use a rigid insulation, perhaps the Superior Walls mentioned earlier for ease of finish. Is this cost-effective, or would I not recoup the funds? (Yes, I just want an opinion.) I’m hoping to add skylights and solar paneling also, since my house faces south.