You Don’t Need a Load Calculation
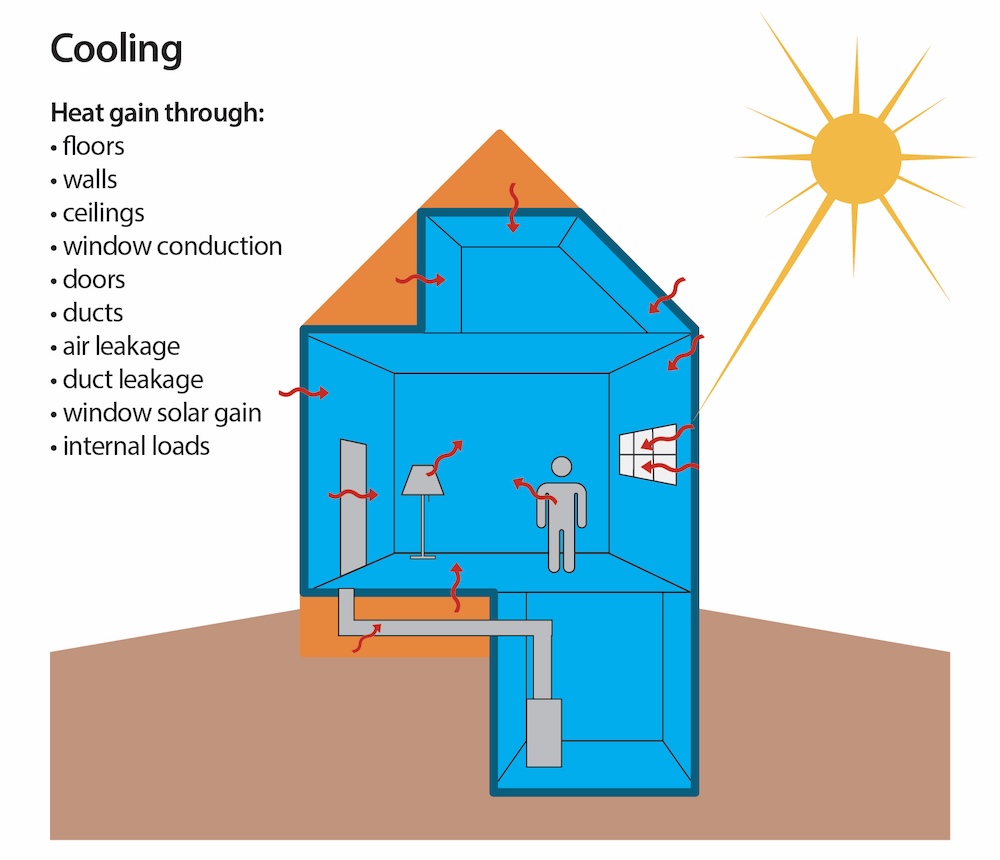
Yeah, I’m talking about a heating and cooling load calculation. Or in HVAC-speak, an ACCA Manual J. It’s a way of calculating how much heating and cooling a house needs. The calculations use the details about the house to determine how much heat leaks out of your house in winter and how much heat the house gains in summer. And yeah, I’m really saying you don’t need them…in certain situations.
“Ah, I knew there was a catch,” you may be thinking. And you’re right. But here’s the thing. You definitely want a properly sized heating and cooling system. And in the majority of cases, you can get that without doing an actual load calculation.
When can you skip the load calc?
Before I get into how to determine your heating and cooling loads without a load calc, let’s discuss the primary factors that matter. The first line dividing the houses that need an actual load calculation and those that can do it another way is age. If the new HVAC system is going into a new construction house, you need a real load calculation. If you’re replacing a system in an existing home, you may be able do it another way.
Then we hit the second hurdle to get over before making the call to skip the load calc. The current system still has to be doing about as well as it ever has at heating and cooling the house. If it’s in decline and struggling to keep up, like my air conditioner was in 2009, a load calculation is still your best bet.
Finally, there’s one more reason you should stick with a real load calc. If you’re doing other work that might change the heating and cooling loads, you probably need a load calc. But if you do the other work first and then go through at least one heating and one cooling season, you should be able to skip the load calc. That other work could be adding onto the house, modifying the duct system, or insulating and air sealing the house.
The method
So how do you determine the size of your new furnace, air conditioner, or heat pump without a load calculation? If you’ve gone through the list above and the house meets all the criteria, you simply measure time and temperature. Here’s how:
- Find the 1 percent (cooling) and 99 percent (heating) design temperatures for your location. An easy place to find them for the US is in this document from the ENERGY STAR new homes program (pdf). Here’s a screenshot showing the design temperatures for Fulton County, Georgia, where Atlanta is.
Design temperature example from ENERGY STAR new homes program - To check your air conditioner in Atlanta, for example, find a day when the temperature gets up is 92 °F (33 °C). Then, while the temperature is at 92 °F, measure how many minutes per hour your AC runs. But keep measuring even after the temperature starts dropping. There’s usually some thermal lag in buildings, so your peak cooling load probably won’t happen until after the outdoors has started to cool down. For heating, do the same thing with your 99 percent design temperature.
- Convert the minutes per hour to a decimal. If the AC ran 24 minutes per hour, that would 0.4 hour per hour.
- Find the capacity of your heating or cooling system. Nominal capacity will work for this. Let’s say it’s 3 tons, or 36,000 BTU per hour.
- Multiply the decimal runtime by the air conditioner capacity. In this case, you’d get 14,400 BTU per hour, or 1.2 tons. (The conversion comes from 12,000 BTU/hr = 1 ton of capacity.) In this case you definitely wouldn’t have to replace a 3 ton AC with another 3 ton AC. A 1.5 ton system should work fine if you’ve measured runtime correctly.
A heating example
We have a client in Savannah, Georgia who wants to electrify her 80 year old home. She has a furnace and air conditioner and used the method above for her heating system. The heating design temperature for Savannah is 29 °F (-2 °C). This winter she had some periods with a temperature that low. She also had some weather where it got down to 24 °F (-4 °C), and the runtime wasn’t much different.
The runtime she measured for design conditions was 25 minutes per hour, or 0.42 hour per hour. The furnace has a nominal rated output capacity of 89,000 BTU/hour. Using this method, then, she was actually heating her house with about 37,000 BTU/hr.
Is that an accurate number? It’s probably close enough. Here’s why. The actual capacity of the furnace is almost certainly not higher than the nominal capacity. It could be lower, though. But lower furnace capacity only means that the 37,000 BTU/hr number is too high. If the furnace only produces 80,000 BTU/hr, for example, she’s heating her home with only 34,000 BTU/hr.
4 ways to measure runtime
1. Use a stopwatch. This one’s time consuming and maybe uncomfortable if you have to sit outside and listen to the outdoor unit in the heat. But it’s straightforward and you don’t have to buy anything new.
2. Get the data from a thermostat. Some thermostats measure runtime and give you access to the data. If you have an Ecobee thermostat,* look there first.
3. Get the data from an electricity monitor. There are a bunch of these on the market now. I have the Emporia Vue and love it.
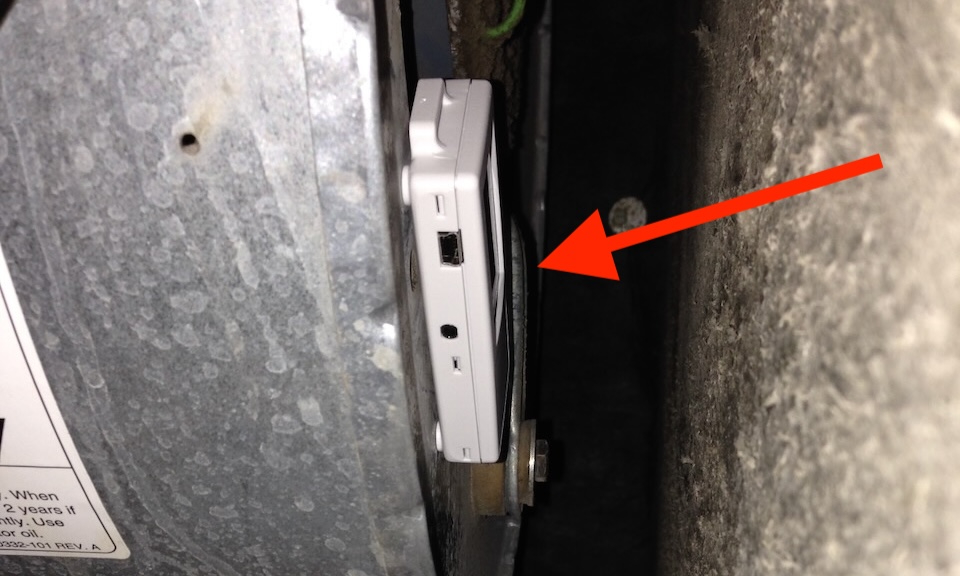
4. Install a motor runtime data logger. This is how I first did it with my air conditioner in the condo I used to to live in, and it’s how our Savannah client did it. You just attach the logger close enough to the blower motor in your air handler, and it can give you minute-by-minute data showing whether the motor is on or off. The photo above shows one attached to the side of a furnace blower. (See the article about my runtime data logger measurements to learn more about his method.)
Can you skip the load calc?
Actual data is usually a better way to go when you can get it. We know that ACCA Manual J results in inflated heating and cooling loads. That’s not a terrible thing when it’s done correctly. Modeled results are better than the old rules of thumb that consider only the conditioned floor area.
But with existing homes that meet the criteria I listed above, you may be able to come up with a more appropriately sized heating and cooling system to replace the old one. Sometimes, it’s MUCH more appropriately sized. It’s not uncommon for homes to have double the heating and cooling capacity they really need.
At the beginning of the article, I said that the majority of homes could benefit from not doing a load calculation. That’s because way more air conditioners, furnaces, and heat pumps are sold to replace systems in existing homes. New construction is a small fraction of the total.
Currently, the majority of the majority that could benefit from this method don’t get a load calculation or use this method. The HVAC contractor usually installs the same size system that’s already there. Sometimes they even put in a bigger system.
If you have an existing home with a working heating and cooling system, get your runtime data before it’s too late.
Allison A. Bailes III, PhD is a speaker, writer, building science consultant, and the founder of Energy Vanguard in Decatur, Georgia. He has a doctorate in physics and is the author of a bestselling book on building science. He also writes the Energy Vanguard Blog. For more updates, you can follow Allison on LinkedIn and subscribe to Energy Vanguard’s weekly newsletter and YouTube channel.
Related Articles
My Big Fat Oversized Air Conditioner
3 Reasons Your 3 Ton Air Conditioner Isn’t Really 3 Tons
How to Determine the Size of Your Central Air Conditioner
* This is an Amazon Associate link. You pay the same price you would pay normally, but Energy Vanguard may make a small commission if you buy after using the link.
Comments are welcome and moderated. Your comment will appear below after approval. To control spam, we close comments after one year.
It’s nice that every homeowner can do this. When trying to do a load calculation, one must know the airtightness of the house, which requires a blower door. Who has one of those just lying around? If the windows are old, how do you know how much solar heat gain you’re actually getting? Even if they were added after the government said they had to label the SHGC, how do you know they’re still performing according to the stated specifications? How do you know that the insulation is still properly performing after some mice have visited your house? What temperature does the manual saying you’re going to heat/cool your house to? What temperature does the occupant actually set it to?
Stacy: Those are all good points. Regarding the blower door test, it may not matter that much anyway. I was just emailing someone who has a client they did a Manual J for before doing a blower door test. When they did it with 7 ACH50, they got 3.0 tons for the cooling load in Phoenix, Arizona. When they dropped it to 5 ACH50, they got 2.9 tons. Going down to 3 ACH50 dropped it to 2.8 tons. Do you think they really needed a blower door test? Probably not.
Re blower door test:( Speaking, cautiously, from SW VA here). We’ve found that blower door tests are important if there have been changes to the building enclosure for climate zones that are more humid and/or have higher heating loads, and to do an accurate load calculation. When a home project begins with an energy audit and work is done in the best order (typically building enclosure improvements first and then heating / cooling system replacement), the new load calc is definitely more accurate and can be a great deal lower. But there are at least three more reasons to complete a blower door test after air sealing and insulating: (1) blower door testing documents to the client how much tighter the home is; (2) for QA and verification of an air sealing and insulation job before and during blower door testing, infrared thermography will pick up any ‘missed’ air sealing and insulation so the company who installed it can address it before the owner pays them; (3) for ventilation. Ventilation fight club aside, most homes below .35 ACHn (usually corresponding to ~<6 ACH50) technically require mechanical ventilation. New homes require it by code – in VA we also require <5 ACH50. Ignoring ventilation for existing building retrofits can inadvertently create new indoor air quality issues, and a missed opportunity to address ventilation systems at the point of HVAC replacement. Everything is connected.
Allison, but aren’t we ignoring the latent loads in different locations? In Phoenix, the cooling latent load fraction of total cooling load will be completely opposite of what Atlanta is, for example in Atlanta latent cooling might be 70% of the total, and in Phoenix it might be as low as 10%. Going from 7 ACH50 to 3 might not make much difference in Phoenix, but it sure will in Atlanta, or am I missing something?
To clarify the above: speaking about infiltration cooling and heating loads.
You can use degree day data and energy consumption over a longer period
“Performance-based heat load calculations”. That’s my term for calculating a heat load with runtime data or gas usage.
It’s more accurate than Manual J,F280, or HOT2000 because it’s based in real-world performance.
So, I agree with the spirit of the article—but the real conclusion is “don’t waste your time on heat load estimates when you can get real data.”
It’s amazing how much fudge is built in to Manual J, using real world data shows this
Drew: Did you read this article as having a conclusion different from what you stated?
The method you described *is* a heat load calculation. So the recommendation is “you don’t need to do a heat load calculation, do a heat load calculation instead!”
I support anything that gets contractors doing heat loads, although I prefer gas usage because it’s much easier to get gas bills than thermostat data.
Drew: I think most people understand the term “load calculation” to apply to the standard way of calculating loads. In the US, that’s ACCA Manual J, which I pointed out in the second sentence. And although there’s a little bit of arithmetic in the method I described, it’s really a measurement of the heating and cooling loads, not modeling.
Semantics aside, we both agree that measuring actual performance is a better way to size heating and cooling systems than standard load calculations. Gas usage is great for heating with gas. For heating with electricity or for cooling, you need another way.
This is interesting and much better than my “square foot ÷ throw a dart based on previous builds” method.
Totally off topic and perhaps grist for another installment of BS: My home has a Mitsubishi hyperheat four-zone-through-a-branch-box system.
If the inverter compressor has a range of 2 to 4 tons, but only one head running and is calling for one ton, what happens to the excess 1 ton produced by the compressor?
Allison, if I understand the math correctly, is there an assumption that the hvac should be running constantly?
Scott: Yes, the HVAC design ideally results in a system that runs continuously at maximum capacity at the design conditions.
I have a friend that used to have his own HVAC company(retired now) and it was a common question to ask the homeowner how long the system ran a day before it failed.
I do have an issue with design temps though. They are extremely generic for many locations as there aren’t anywhere near enough testing locations. I’m in TX and the numbers for the DFW area are not even close for where the majority of the population lives. The population doesn’t live at the airports where the temps are cooler in the summer and often warmer in the winter. This is easily verified by looking at temp data over the region. The numbers used for design temps are what I call Chamber of Commerce temps as they show nicer temps to get people to live here…
I had my own weather station for years and data logged until the laptop it was on had a HDD failure. Over the 8 years of logging and averaging numbers it was interesting how much higher the 1% numbers were and the 99% was higher as well.
The temps in our area vary extremely over short distances in just say the DFW area. Go from one side to the other and the temps vary quite a bit as well as the rainfall etc. There is a reason that on the map there is a line right down the middle of Arlington splitting the area in 2 as it’s brown to the west and green to the east as yes the rainfall and temps are than different which is easily backed up by historical weather data which is ignored by those coming up with overly generic design temps. It doesn’t vary as much as the microclimates did in Hawaii but it’s still a big difference to take into account.
It’s such a problem that a few smaller citys have figured this out and adjusted their design temp requirements in city code to reflect actual local conditions.
The lesson is don’t take the data at face value do a little research and verify those numbers are right in your case.
But you can only do this by waiting for one of those 1% / 99% days – which don’t happen that often.
Like Robert Obrien suggested above, degree day data and energy consumption can be measured at any time in the appropriate season. Maybe harder to separate out cooling energy consumption without equipment, but for anyone who uses gas or propane, measuring energy consumption for heating is relatively straightforward – and without needing any equipment.
Does it matter how many degrees you turn the thermostat down/up?
Blake: Yes, the thermostat setpoint does matter. Our client in Savannah sets hers at 65 °F, but she should still put in a system that will work at 70 °F. We had already done a Manual J for her, so we used it to find the difference between those two setpoints. The result was about 10,000 BTU/hr. Like all MJ results, that would be inflated somewhat. Even if it’s not, though, she still can get by with a 4 ton heat pump.
you just opened a can of worms, or the pandora’s box to be more dramatic, in a global warming scenario, all this fails; ducts lose heat or gain heat, if you replace that system with a ductless anything, your approach goes to hell.
Also remember that the majority of the systems need heating, too, and the rules are totally different. In most cases, more heating is needed than cooling, and the outside temperature is never the same year after year. You need a load calculation using the latest data available. Thirty-year averages don’t work anymore, and floor area has nothing to do with the heating or cooling load.
your advice is confusing and opens the door for the uneducated contractor or homeowner to make the biggest mistake possible, fail to heat a house in the winter; cold kills, heat kills, are you ready to take that responsibility?
What would you suggest for the homeowner who sets back their thermostat to a reasonable temperature and may or may not sell their home during the lifetime of a new HVAC system? Size it to accommodate their typical usage or size it for standard indoor design temps?
John: Good question. If they’re certain they’re not going to sell before the equipment starts petering out, they could size it for their needs. But as people grow older, they like warmer temperatures, especially after the age of 85 or so. Another option would be to get multi-stage or variable capacity equipment and size it to the standard design conditions.
I did many run time tests before I did my own manual “manual J”. I also found a Carrier dealer willing to perform a manual J for me for free. All three calcs said that a 3 ton ac would be more than enough for my 2100 sq ft house built in 1987 with upgraded windows and sealed baseboards and outlets. But in spite of all that I could not find one installer willing to guarantee their installation unless I installed a 4 ton system. And my trunk line was only 16″ diameter so was not really designed for 1600 cfm that a 4 ton needs. Luckily I opted for a 5 stage Carrier, variable speed 98% pulse modulated furnace. Even on the most extreme day I’ve ever experienced in San Diego of 110F, 3 stages were more than enough. And 1000 cfm was more than adequate for heating. I did upgrade that trunk line to 18″ along with many other upgrades to keep the static pressure around 0.35″ max (It was 1.5″ after they installed my system). The formerly noisy system is now very quiet but I tend to think it might have been more efficient had they installed a 3 ton system in the first place. I’ll never know I guess. I did convince a neighbor to insist on a 3 ton with the same company and similar floor plan (they have a two stage) and they have never had one complaint since. Having at least a 2 stage unit along with variable speed air handler at least overcomes oversizing to some degree. Even the largest and most popular companies in San Diego still refuse to do or believe a Manual J.
With heat pumps it is important to choose your winter design day data carefully to include a storm day with heavy wind loads.
Certainly one should not rely on a summer design day alone if downsizing was the result in a heat pump calculation.
I believe a dual fuel system with a summer design day size backed up with a gas furnace will provide the lowest operating costs and best heating reliability that can be easily powered in winter during a power fail.
It’s a sneaky way to tell the old Manual J, “move over clumsy grandpa!”
But aren’t we missing indoor design temperatures (cooling or heating)?
Also, I’d choose my outdoor design temperature day wisely. If you are in Atlanta, I’d choose a nice sticky 92 °F with dew point close to 70 °F, not some “dry” outlier with DP at 62 °F, for example. And if you’re in Chicago, I’d go with a good 10-15mph wind and clouds with its heating outdoor design temperature of -3 °F, not a calm and sunny -3 °F kind of day.
And then the timing: do you measure your run time in the morning, when the system is trying to recover from the nightly setback in the winter? Do you have kids running in and out of the house all day on your measurement day? Suddenly, the simple method can turn into a not so simple result.
Technology Connections, a nice geeky YouTuber, went into doing these practical calculations. He also found that it was easy to do via simple electric space heaters.
https://youtu.be/DTsQjiPlksA?si=QWsen45liQoQuiFM&t=1774
Good article, Allison! I like the way you presented the concept in its simplest form.
We did a bit of research for NYSERDA using a similar method in 1990-91. We called it the Measured Performance Rating (MPR) method and used it to evaluate incremental weatherization improvements in one cold night. The largest confounding variable was the heating load lags due to thermal mass; hence we now use a longer time period to help normalize for this.
https://www.osti.gov/biblio/5278952
https://iifiir.org/en/fridoc/measured-performance-rating-method-for-weatherized-homes-13268
Today we use 1 to 4 winter months of HDD from http://www.DegreeDays.net and utility bill data to get a reasonable Energy Factor (BTU/sq.f.t/HDD).
Heating Load = EF x (base temp – design temp) x floor area/24
So, a 2,000 sq. ft. house with an EF of 6.1 in a 6°F design temp location could use a 2-1/2-ton furnace that runs 100% of the time at design temp. A 3-ton heating system would have a 100% runtime at -5°F. Thermal mass and a tight home will easily maintain comfort during nighttime dips to -15°F or more.
So, replace that 7-ton furnace, not with a Manual J 4-ton, but with a 3-ton heating system.
Fortunately, Science and Engineering do not care what you believe; you are so wrong, it is almost scary that other people may have the same beliefs. Hopefully, you are not a contractor or similar.
Eduardo: Science and engineering are methods developed by humans to understand and manipulate our world. They don’t have beliefs. I’ll come back when I have more time later and address your first comment. Based on your tone, though, I’m not sure it’ll make much difference to you. But many others read this blog and the comments, too, so it can help them if not you.
Been thinking about it and I think I have figured out the reason for oversizing in some places and under sizing in others.
Like I mentioned earlier design temps are wildly inaccurate for many places as the test sites are too far from where people actually live. But when every climate is using a blanket 99% and 1% rule and applying it to all of them the same.. There is your answer to the sizing problem.
Locations like us have a design temp of 99* Which I found my notes of my weather station data and our summer temp should be 103* from actual local data. Now think about using those numbers in GA when you go over your 1% temp it’s by what a degree or two for an hour or so in a day. While here even if you used a design temp of 103* we will be over that temp in the summer for weeks on end and not by 1-2* for an hour or two but our temps will be 105*-115* for hours of the day. What others call a heat wave we call summer and it lasts for months.
So the calc thinks you will barely skim over that temp rarely in many locations but ones like us we will soar well past it for 6 hours of the day for weeks at a time.
It will be 90* by 9am and still in the mid 90s at midnight so even when it drops below design temp the units will run for hours and never recover by the next morning because they are removing all the heat in the structure. Not to mention that the ground and everything around the house outside is heat soaked. Houses are brick here and that brick is also radiating heat into the house all night.
The calcs are very well done but they need to work at tuning them to varying locations instead of using a blanket 1% and 99% without taking into consideration how far over and under those design temps are common in different locations.
Homer Simpson described it very well “One size fits all my butt”
Now what I would suggest thinking about… In locations like ours that don’t work well with the 1% numbers I would say go ahead and follow it and install the system as the calcs say. However to make up for that lack of capacity you can install a small minisplit in say the living room or master bedroom (for better sleep). This unit would only need to kick on to supplement the main unit and since the main unit is running constantly it will spread that air around the whole house. Course there is the other side where you may run it more often as they are generally more efficient than ducted systems.
WOW, this one has grown some legs Mr. Allison. Good Google Juice!
I’d rule underperformance before grabbing my stopwatch. Check all the typical culprits…
– Filter Check
– Coil Inspection
– Refrigerant Check
– Compressor Vibe: Listen/feel for odd noises or weak performance.
– Airflow Test: Check supply vents…older homes = notorious duct leakage.
Otherwise, a tuned-up system at 100% runtime with comfort points to a good match – agrees with your math – again!
I started using “empirical heat loss calculation”. I also like “demonstrated heat loss” based on the “demonstrated electrical load calculation” that the Ontario Electrical Safety Authority is allowing. https://esasafe.com/assets/files/esasafe/pdf/Electrical_Safety_Products/Bulletins/8-3-15.pdf
For a gas furnace heat output, I would suggest at least multiplying the efficiency such as 96% or 80% times the nameplate input efficiency to get the output btu/hr for a little more accuracy.
Bruce: Thanks for pointing that you need to use output capacity of a furnace. When people talk about furnace capacity, it’s usually the input capacity they’re referring to. The nameplates usually state both input and output capacity, but if you find one without output capacity, just multiply by the efficiency in decimal form.
I thought I had put the word “output” in the Savannah example, but I hadn’t. I just added it, though.
Great Idea, makes a lot of sense. Good luck getting a permit in Canada for it. Up here they only accept calcs. It’s ironic, though not surprising, that the single biggest unmovable impediment to de-carbonizing my heating, is regulation. And I live in a lefty country, an even more lefty province and a lefty town. I’ve never been a small government type of guy, but this has opened my eyes to the cost regulation can have on innovation.
Hi Kevin,
We’re are you located? I know of a service organization that can do an F280 for a decarbonization project retrofit quickly and at a very reasonable cost.
North Van. If you post a search term I’ll look it up.