3 Easy Advanced Framing Techniques
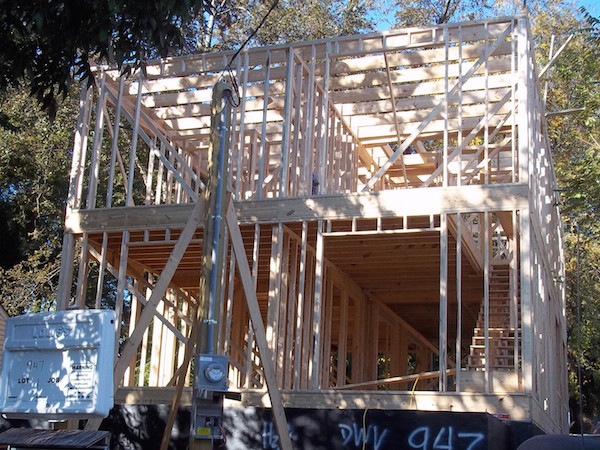
Most new homes in North America are built with sticks. The early home builders used bigger pieces of wood — timbers — and when the smaller dimensional lumber that we use so much today hit the market, they scoffingly referred to those new-fangled little woody things as sticks. So now our home construction industry is staffed with people who do stick building and the home you live is most likely stick-built. And sadly, many of the techniques used to build many of those homes are the same used before we started insulating them.
Before insulation became widespread, it didn’t matter if you put extra wood in your walls. In fact, many builders still think more wood is better. But when your insulation goes into the cavities between framing members, every extra bit of wood means less insulation. That means more heat loss in winter and more heat gain in summer. (Putting all the insulation on the outside is better, but that’s more expensive and not likely to happen on a wide scale in the residential market.)
The good news is there are some simple ways to improve the framing that allow more insulation without compromising the structural stability of the home. Here are three I think ought to be used on every stick-built home.
Ladder T-walls
This one is a no-brainer. When an interior wall intersects an exterior wall, the standard practice is to use three studs to complete the T-wall. The photo below shows what that looks like.
The oriented strand board (OSB) sheathing on the exterior side of the wall will be covered with insulation. The space where those two studs are in the exterior wall, however won’t get any insulation. There’s no way to get it there.
The solution is the ladder T-wall. The diagram below (from the US Department of Energy; click image to download pdf) shows what it looks like.
Rather than vertical studs, you take some of your scrap wood and run it across horizontally. You put the wide side against the T-wall stud so you have space in the back to insulate that cavity. It’s beautiful! You save wood and get a better-insulated house, too. Here’s what it looks like in real life:
The photo above is from the North Central Georgia Habitat for Humanity affiliate. We work with them and are always impressed with their ability to implement stuff like this.
Of course, there are variations of advanced framing at T-walls. Here’s one that a client of ours used a few years ago:
It’s got 1-by deadwood for drywall and what is essentially fireblocking through the cavity.
California corners & 2-stud corners
This is similar to the T-wall problem. The standard practice uses three studs and blocks off the corner so you can’t insulate it. Here’s what it looks like:
The advanced framing alternative is to use three studs but leaves an opening to get insulation back into the corner, like this:
It’s usually called a California corner here in the Southeast. I’m not sure what it’s called in California. Maybe just a corner?
That DOE factsheet I mentioned above also shows how to do a 2-stud corner. Here’s the diagram:
It uses less wood and gives you more space for insulation. Check out the factsheet for more details on that.
Insulated headers
Headers abound in stick-built homes. They carry the load when you can’t put in studs at the regular spacing, as is the case where you have doors and windows. They’re often made with two pieces of bigger wood, like 2x10s, but they have a gap. In a 2×4 wall, two 2x10s on edge are 3″ thick. The wall is 3.5″ thick. In a typical home, that extra half inch is wasted. In a 2×6 wall, you’re wasting 2.5″.
The natural solution here is to throw some insulation in the gap. You can do it easily with rigid foam board. If you don’t like foam, you can use mineral wool or something else. Just get some insulation in there. Otherwise, you’ve got a thermal bridge that wastes your heating and cooling dollars and could create other problems, like making your mean radiant temperature uncomfortably cold in winter or hot in summer.
The image above (from the same US Dept. of Energy document on advanced framing as the ladder T-wall image) illustrates how it works.
Too easy not to use
These three advanced framing techniques for walls in stick-built homes are too easy not to use. The only reason they’re not already used on every stick-built house is inertia. “We’ve been doing it this way for 30 years and it’s never been a problem.” If you’re a builder and worried about trying something new, check out Matt Risinger’s video about standard framing versus advanced framing.
The exterior walls in a typical house are 25% framing. Wood has an R-value of about 1 per inch. Most insulation is close to 4 per inch. Using these advanced framing techniques will reduce the amount of wood in those walls and increase the insulation.
It’s time to get over the inertia. These things are easy, easy, easy. Your house won’t fall down. Instead, your house will be better.
Related Articles
A Sword through the Ribs of the Building Envelope
Naked People Need Building Science
The Layers and Pathways of Heat Flow in Buildings
Image credits: All photos by Energy Vanguard. Advanced framing diagrams from a US Department of Energy Technology Fact Sheet titled Advanced Wall Framing.
NOTE: Comments are moderated. Your comment will not appear below until approved.
This Post Has 20 Comments
Comments are closed.
We were using muzzle loading
We were using muzzle loading rifles (like the model 1841 Mississippi Rifle) to fight our wars when stud frame construction and balloon framing was taking this country into a new realm of building technology. Good for us, right? Well, it’s almost 200 years later – the Army now looks to the M4 rifle, one of the most advanced pieces of weapons hardware on the battlefield – and people are still stud framing houses? Come on, people. There are newer, better ways of doing this. I hear builders complaining about the price of stud frame lumber going through the roof because of the recently announced tariffs on Canadian lumber – so maybe that will help people change. They say it is human nature that people don’t change unless there is pain (isn’t that obvious because of the evolution of weaponry over the years?), and certainly money can apply that pain pressure. Our preference is to educate the public and let the consumer apply the pressure on the builder. I think far too many builders are complacent and comfortable – must be nice to be so comfortable. Change is coming, no doubt about that. We just completed the first 3rd party engineering study (within the University of North Carolina system) on the strength of stick framed corners (apparently it’s never been done that we could find) – many different ways of doing it but no one’s ever looked at how it affects the strength of the overall structure, comparing one method to another. More to come on that. It is the ‘paradox of stud frame construction’ – the tendency to have less framing for more energy efficiency (but less strength) – to having more framing for a stronger structure (but less energy efficiency). Must be frustrating….
I look forward to hearing
I look forward to hearing more about the results of your stick-framed corner study, Charles. Be sure to let me know when you have something available.
Charles, your comment alludes
Charles, your comment alludes to a “newer, better way” that might replace stud framing. What are you referring to? Or am I misunderstanding your comment?
Is there any reason not to
Is there any reason not to put the 1/2″ foam to outside or inside of the header?
Sam, the ideal place for the
Sam, the ideal place for the insulation would be on the exterior side of the header. That would keep the header warmer in winter and cooler in summer, protecting it from the changes that happen with changing weather. I don’t think I’ve ever seen one done that way but don’t know of a reason why it couldn’t be. I have seen them insulated in the middle and on the inside.
Good to know, I have placed
Good to know, I have placed foam in all three locations, in, out and middle and like outside best for the reason you mentioned but have never seen a drawing/detail depicting it that way.
Foam placement is dependent
Foam placement is dependent on what you might be doing – placing it inside can interfere with drape placement, outside with trim or awning’s (though if you use plywood that point is moot). Ideal placement is also on outside for me though I have done inside.
FYI Allison that is a three stud corner you have pictured, a two stud corner does not have that one long one to catch drywall & instead people rely on drywall clips. http://thehtrc.com/2012/common-sense-ove-framing – shoot I need to find the picture of the 2.5 corner I have that a builder does
Thanks, Sean. Yeah, I
Thanks, Sean. Yeah, I realized after another commenter pointed it out that I was calling that a 2-stud corner when it’s really a 3-stud California corner. I had just been reading the DOE factsheet (which Southface helped put together and you probably got a copy of in your HERS binder) and they discuss the 2-stud corner there. I don’t know if I’ve ever actually seen a 2-stud corner in the wild. Mostly I see the California corners. I’ve updated the article to show both 2-stud and 3-stud corners.
With the foam or mineral wool
With the foam or mineral wool in the center, the load is transferred equally through the headers to the stud. If the headers are to one side to make room for insulation on the outside, then the load is not evenly transferred to the stud. You might observe a stud bowing out after several years of off-balance load.
Great ideas! Keep them coming
Great ideas! Keep them coming. Your stats on 25% of framing is eye opening.
I do have an issue/improvement with the first T-intersection detail. I believe if you put in enough 2×4 blocking to make for a decent drywall corner you will also be significantly compromising the insulation in a 2×4 wall. A better technique I have used for some time is one 2×4 in the center for partition wall stability and scabbing on a 5 1/2″ OSB rips on top and bottom of the joining partition stud to receive the drywall. This way you minimize the compression of the insulation, get perfect drywall support and enough stability for the joining wall.
Jim, yes, there are certainly
Jim, yes, there are certainly ways to improve upon the T-wall besides the ladder style I showed above. I’ve seen some similar to what you’re describing. All can work well and all are better than the typical uninsulated T-wall.
I’d like to see a drawing of
I’d like to see a drawing of what you’re describing. I’m not comprehending how the OSB rips are mounted. You can email me at option917@gmail.com if you’d like to respond with a drawing. Thanks.
Bo, I added a couple of
Bo, I added a couple of photos to the article. One is the ladder T-wall illustrated in the DOE diagram. The other is what I said I’d seen before.
The photo of the humongous
The photo of the humongous header over a 3-foot opening is a glaring mistake. Part of advanced framing is using right-sized headers. People are too lazy to do the calculations, but we should be insisting that they do.
Bo, that’s a good catch.
Bo, that’s a good catch. Putting in headers that are the correct size can reduce the framing factor, too. And so can eliminating headers altogether when they’re not needed. I once wrote about this for a case involving a header in an interior wall:
Common Sense – The Best Green Building Skill in the World
http://energyvanguard.com/blog/36859/Common-Sense-The-Best-Green-Building-Skill-in-the-World
I see that all the time.
Interesting to see these
Interesting to see these techniques described as “advanced” framing. Everything I’ve ever read describes ladder framing at interior wall to exterior wall intersections, 2 stud corners (there’s actually 3, but the point is that there are no cold corners), and insulated headers as “intermediate” framing. “Advanced” framing utilizes the same techniques but typically moves the on center framing up to 24″ and calls for single top plates (which is very hard to pull off unless you can align the roof truss loads to sit perfectly on top of your wall studs). Could the difference be regional (I work in the Pacific Northwest), tied to the prevalence of 2×4 vs 2×6 framing (the norm in the PNW) or both? Curious…
I agree, Ryan. In the Pacific
I agree, Ryan. In the Pacific Northwest, these things are intermediate, or perhaps even more basic. Here in the Southeast, this is definitely “advanced” framing. See that article I wrote right before this one and take a look at the joists running across the top of the wall separating the garage and the living space. That same house had all the standard T-walls and cold corners. I don’t think this is just a problem in the Southeast, though. Maybe some of the Midwesterners and others reading this will chime in and let us know what they see.
Advanced framing isn’t very
Advanced framing isn’t very common in high wind areas (Midwest, Texas, etc). Builders are afraid that 2×6 24″oc framing will get blown down unlike 2×6 or 2×4 on 16″oc or so I’ve read from Texas builders that have engineering degrees and “30 yrs” experience. Then there’s the obligatory “You can’t hang anything on your walls” or “you’ll put your hand on the wall and punch right through the drywall”.
There is alot of competing
There is alot of competing info out there, and difficult to obtain objective data vs. just opinions. I’m trying to understand if all things being equal, is a 2×6 wall at 24″ oc with advanced framing techniques weaker, stronger or the same as a 2×4 wall at 16″ oc with the same advanced framing techniques? In other words, do these techniques disproportionately affect the integrity of a 2×6 wall?
I’m also interested in learning about the regional differences in these techniques. One builder told me 2×6 @ 24″ OC advanced framing cannot be used in climate zones 1-4, and referenced page 6 of this APA document: http://www.apawood.org/data/sharedfiles/documents/m400.pdf
Another way to interpret that document is that in climate zone 1-4 it is possible to meet the Energy Star requirement with 2×6 @ 16″ oc using advanced framing, but the 16″ is the minimum spacing, and you can increase the spacing to higher than 16″ and thereby increase the efficiency…
Cal there is a term used
Cal there is a term used which is “it depends” which applies to a lot of stuff we do. Lets start with the easy one first though – the builder is flat out wrong, 2×6 @ 24 OC can be used everywhere though in seismic areas it might require other measures to help meet the engineering requirements. Strength wise it is a wash though you get the benefit of being able to add more insulation into the bay though that isn’t where I would really want it
You want objective data – first you need to spell out the requirements in full & then send to an engineer to crunch the numbers. Huh, well before people started to sexy up the name to get more mainstream attraction it was called OVE – Optimized Value Engineering. Now there are certain components that don’t require it, like swapping from 2×4 @16 to 2×6 @24, using 3 stud corner, ladders, etc… but others need a good layer of understanding (single top plate) & depending on your area an engineers stamp of approval