Guest Post: The Fatal Flaw in Advanced Framing, Part 2
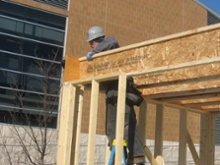
The tragedy of this is that in the effort to sell Advanced Framing as a whole package, presenting it as an alternative to Western Platform Framing, the sensible housing industry has thrown out the very easy and productive suggestions from the first list along with the bathwater that is the ill-conceived proposal of the grid dependent single top plate. By putting these all together and regarding this as a whole package, we are all complicit in the marginalization of what could be some very useful practices to increase efficiency in framing.
The tragedy of this is that in the effort to sell Advanced Framing as a whole package, presenting it as an alternative to Western Platform Framing, the sensible housing industry has thrown out the very easy and productive suggestions from the first list along with the bathwater that is the ill-conceived proposal of the grid dependent single top plate. By putting these all together and regarding this as a whole package, we are all complicit in the marginalization of what could be some very useful practices to increase efficiency in framing.
Rather, what we should do is what the housing industry has done all along. That is, jettison the notion of the grid and the single top-plate, and “re-brand” this as Advanced Framing Details. Get the industry adopting the useful practices from the first list. Rather than confound home builders with re-engineering their catalog of house designs let’s just hand them some common sense measures to save lumber and make small but useful advances in performance. More profit, more green. Win, win.
Reducing thermal bridging is the key
Now I hate giving up that single top plate as much as the next person, but the reality of this is the single top plate of Advanced Framing is not doing that much for performance. While Advanced Framing reduces thermal bridges incrementally it retains the basic structure of Western Platform Framing and all its inherent performance weaknesses. Notably the rim-joist space is unchanged, and this remains a difficult place to insulate and air seal.
Research will show that anybody in a significant heating climate shooting for high performance is already taking much more significant measures that eclipse the benefit of a single top plate. Reducing the number of thermal bridges is always good, but no wall assembly that is serious about high performance will be without some feature that interrupts thermal bridges with insulation.
Some common examples include:
- Exterior insulation. A layer of continuous insulation outside your studs will provide a thermal break for all the framing and goes much further to improve performance than eliminating one plate member.
-
Double stud wall framing. Another common strategy for introducing a thermal break to a wall and reaching high insulation values. It’s simple, easy to understand
and execute. However it is not winning on reducing lumber, nor labor for that matter, but it gets real results in performance.
- Structural Insulated Panels (SIPs). Among systems that are stud framing alternatives, SIPs are perhaps the simplest in concept and common enough to be a commodity. Strictly speaking, however, SIPs have been around for many years, and the moment for them to rise and replace the stud wall has likely passed. A continuous core of foam makes for no thermal bridges.
Is Swedish platform framing the answer?
But none of these is truly the replacement for Western Platform Framing that Advanced Framing claimed to be. I do think one will emerge, however. My bet is on wall systems derived from standards developed in Scandinavia, which by the way is the only example of a mature housing market that has moved completely to high performance wall systems. I’ve studied them, and presented a new framing model based on their techniques: Swedish Platform Framing.
This is a natural evolution of Western Platform Framing, modified to:
Improve thermal performance by overcoming the inherent weak points of the Western Platform method, and lend itself to off-site fabrication, which will inevitably be where volume home building shifts in the future.
No more to say on that in this piece. If Allison will have me, I’ll come back to write more about that at some future date.
Advanced Framing is done!
To close, I just want to say that I don’t blame Advanced Framing for these issues. It was not conceived with energy performance in mind. It’s up to us to own up to its limitations and to acknowledge what it does and does not do well.
If you are a fan of Advanced Framing, including the grid and the single plate, if you are training people to do it, or incorporating it into your own work, more power to you. It takes design discipline to work with its limits and extra know-how to build it correctly. You should be boastful about those skills.
If you are in a mild climate Advanced Framing may be enough to reach better than average performance levels. But we have to be realistic about Advanced Framing when working in more demanding climates. It simply does not deliver much performance for the effort of working to the grid in order to eliminate one plate. Selling it as a big improvement, and promising it as a significant green feature is just ingenuous, bordering on greenwashing.
We must do better and be brave enough to call out people that promote it as such. Finally we have to be realistic with our expectations for what the industry will adopt. When history is telling us clearly that something will not fly, it’s up to us to accept that fact and look for more workable solutions. We only harm our own credibility and influence by promoting a technique that the wider housing industry has already rejected.
So Advanced Framing? Fifty years. It’s been done. It’s done. Get over it. Long live Advanced Framing Details.
About the author
Gregory La Vardera is an architect in practice, and a building scientist by training. Outside of his local practice he is focused on opening up niche markets in housing, and is interested in the development of broadly adoptable strategies for high performance building including off-site manufacturing of houses. You can read his blog for more info about the Swedish Platform Framing method and other topics.
Related Articles
Common Sense – The Best Green Building Skill in the World
Structural Insulated Panels — An Easier Way to Build an Airtight Home
Green Curmudgeons, Architects, and Outlawing Batt Insulation
Photo at top of single top plate framing courtesy of Ohio State University Solar Decathlon
This Post Has 4 Comments
Comments are closed.
For the heat loss of a
For the heat loss of a typical structure how much could be saved by changing framing practices?
The only thing wrong with the
The only thing wrong with the single top plate is it isn’t how it was done in Swedish Framing… sheesh what a crock
Allison you would have done better writing about your issues with OVE, assuming you do have some.
http://bit.ly/CSB-OVE
I waited for the second
I waited for the second article before commenting, so pardon me if I mention things in first article in this post.
First I’d like to say that OVE is a good savings, but a hard sell to builders. (yep you knew that didn’t you?) I’ve found it works better for owner/builders..which isn’t burning up the market palce anytime soon.
Depending upon what is used for insulation, the raised heel is something I’d leave in, if conventional insulation on attic floor is being used.
Saving $$ on lumber costs is always a good idea IMO as long as strength & performance doesn’t suffer.
I’ve seen quite a few OVE builds in my rural area. The site usually has quite a few folks stopping to say wtf y’all doin? As it is not the common wall construction.
With things like my favorite…SIPS and ICF around I see why posters are asking why revisit OVE.
Not everyone can afford the upcharge of SIPS/ICF..thus OVE fills that void. If we put our foam sheathing on the exterior of the OVE walls, insulate conventionally and use ADA(air tight drywall approach) we have built a thermally broken, air tight wall. (as long as sole plates are sealed to slab, and foam board is taped).
And saved quite a bit of $$ in the process.
I’ve always thought there was a place for OVE in the market, and would like to see more of it.
more OVE less waste $$ in foam insulating walls. we can build walls tight.
save the foam for the errors
it covers by installing it on the roofline.
take out designer/architect mistake of putting ducts in attic, cover builder errors..thermal bypasses IC recessed lights..and hvac error of not mastic sealing the ducts.
I enjoyed the article as I seek ways to solve problems and not just throw $$ at them.
People need to realize that building/owning a house is a dream for most of us. Affordable options like OVE should be maximized, so that the dream becomes reality for more people..not less.
SIPS & ICF have their place..but so does OVE.
Thanks for the articles.
My company has used advanced
My company has used advanced framing for the past five years. While it’s not perfect, it’s a big improvement over the traditional 16″ OC 2×4 framing that we used before. No, our openings don’t land at the 24″ OC layout, but neither do the openings in 16″ OC frames. It’s about progression, and fewer studs and plates with thicker cavity insulation is an advancement over where we were, and where the vast majority of our competitors still are.
As for redesign, the Swedish model would require similar revision to the same 100,000 plans as OVE, with a larger learning curve for designers, framers and inspectors, not to mention the revision to the codes. While converting to Swedish framing may be worth it, getting builders to adopt these changes will be no less difficult than convincing us to advance frame. I do appreciate the introduction to this framing technique, and I hope to see it on the ground here in the U.S. in the future.